We can see plastic bottles everywhere in the world. Its material is durable and at the same time, non-biodegradable. Therefore, the issue of recycling plastic bottles is rising as an effective solution for a sustainable lifestyle. Let's see how many stages are included in the life cycle of a plastic bottle and understand the importance of recycling this item. Follow up for more!
1. What Are They Made Of?
All plastics are not the same, and the one often used for plastic bottles is PET. PET or polyethylene terephthalate is made from natural gas or crude oil. This oil is exploited by large-scale extraction processes, including drilling, mining, or fracking.
The reasons why PET is the main component of a plastic water bottle are its lightweight, strength, and durability. Yet, at the same time, its chemical bonds are hard to break, making them non-biodegradable and requiring 450 years to decompose. Once these chemicals are freely released into the environment, they can badly affect human life and wildlife.
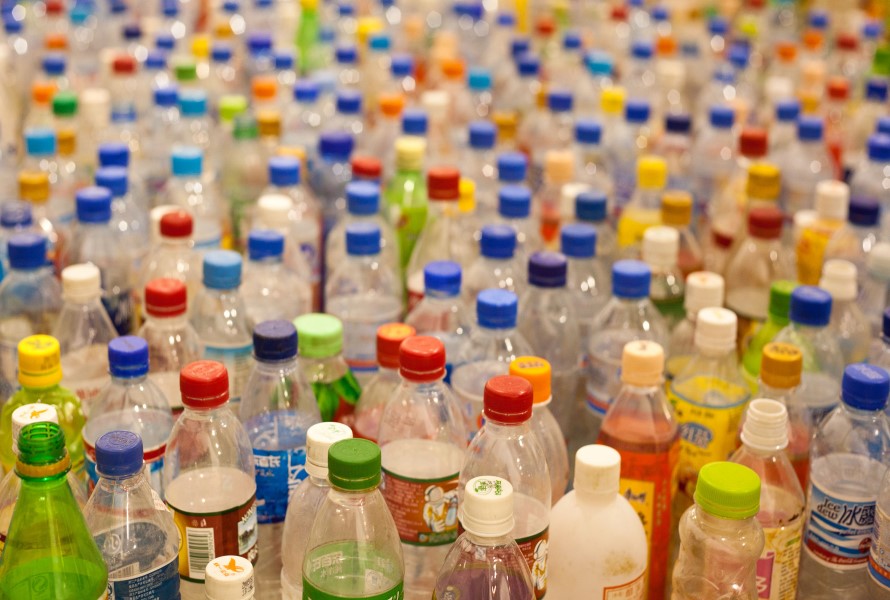
2. What Is The Life Cycle Of A Plastic Bottle?
The life cycle of a plastic water bottle consists of 3 stages: manufacturing, distribution, and disposal.
2.1. Manufacturing
Natural gas or crude oil is extracted from the earth and moved to the refinery for processing to make refined oil. This oil is then shipped to the plastic factory.
At the factory, chemical processes are conducted. Both natural gas and crude oil contain hydrocarbons. When they are under high pressure and high temperatures, they can turn into smaller units (called monomers). These monomers then will go through the process of polymerization or polycondensation, depending on the intended purpose of use.
The oil turned into plastic will be shaped into bottles and transferred to the bottled water brands for filling and packaging.
2.2. Distribution
The bottled water manufacturers will distribute their products to their agencies or stores and wait for the customers to consume them.
2.3. Disposal
The disposal stage will have two scenarios. After consuming, customers may throw the bottles in the trash can or even litter them somewhere. This scenario will end up with a landfill and negatively affect the environment as the items will take a very long time to decompose.
The second situation is the bottles are sorted for recycling. Polyethylene terephthalate is type-1 plastic, indicating it's easy to recycle. The recycling process includes sorting, melting, and reforming or remanufacturing into other products, such as single-use water bottles, clothing, and upholstery. Items made from recycled Polyethylene terephthalate will be marked rPET, rePET, or rPETE.
However, note that the material is only able to be recycled a maximum of 3 times.
3. What Makes Recycling Difficult?
There are two main reasons making the process difficult to do.
First, it's the lack of infrastructure. The infrastructure of the city or region may not be enough for recycling plastics. In addition, the waste collection services are not developed. Thus, consumers need to spend a lot of time and effort to collect and sort by themself, making the process inconvenient.
Secondly, a lack of education about the downside of plastic bottles can affect their decision to after-use plastic bottles. People don't really understand the importance of recyclability, reusability, and safety, thus leading to ignorance.
4. Why Should We Recycle Plastic Bottles?
41. To Save Energy And Natural Resources
Making new raw materials always takes more energy than recycling. Plus, recycling will reduce the exploitation of natural resources and create less emissions to the environment.
4.2. Reduce Landfills
Since less plastics are thrown away, they take up less space in landfills. Thus, cutting down the amount of trash is necessary.
4.3. Way To Protect Wildlife
Littering plastic bottles into the sea will lead to polluted marine waters. Plus, underwater creatures will be affected by digesting these indigestible products. It's terribly harmful to the health of both small fish and big mammals. It also may have a bad influence on people who consume these fish.
4.4. Create More Job Opportunities
Recycling can increase job opportunities as it requires people to work at recycling centers to collect and sort the plastic for the process.
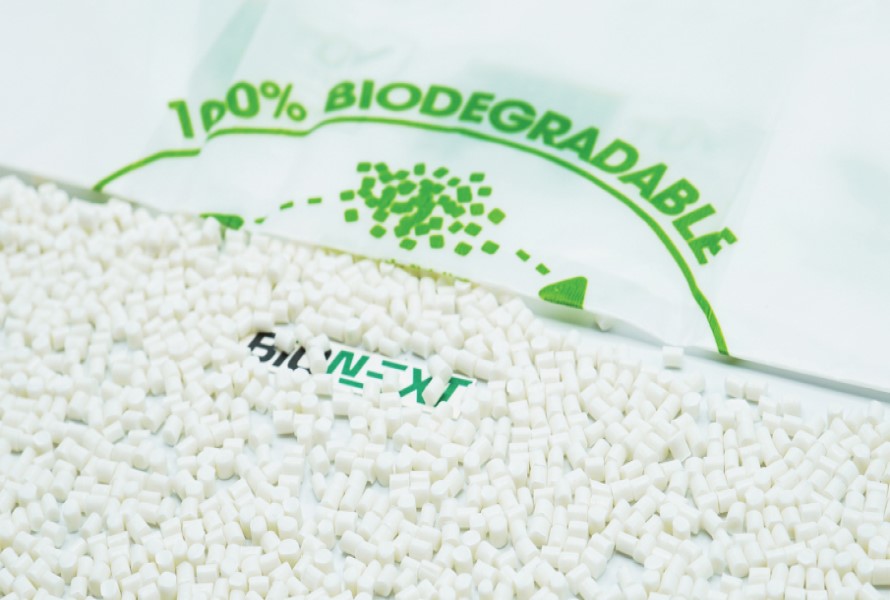
5. EuroPlas - Manufacture of Green Materials
EuroPlas is the world's No. 1 filler masterbatch manufacturer, providing customers with unique plastic raw material solutions to help their factories optimize production costs and improve their competitiveness in the market. Moreover, we understand the importance of eco-friendly materials to contribute to the green world and encourage sustainable lifestyles. Therefore, we've created a series of biodegradable products used in different industries to help reduce the bad effects of plastics on the environment.
5.1. Bioplastic compound
Bioplastic compounds have many advantages. Unlike conventional petrochemical-based plastics, which are made from costly petroleum or natural gas, bioplastic compound is produced from renewable biomass sources, including polylactic acid (PLA) and Polyhydroxyalkanoate (PHA), plants and vegetables (corn, palm oil, potatoes), or fossil fuels like aliphatic-aromatic co-polyester (PBAT).
Using biodegradable and compostable compounds means you'll be less dependent on fossil fuels. Its life cycle assessment shows that it can decrease the carbon footprint in the manufacturing process. Furthermore, the bioplastic compound has better mechanical properties than unprocessed plastics, fewer toxins, and decomposes faster.
The material is widely used in different industrial sectors such as electronics, automotive & transport, household appliances, construction, fibers, and especially food packaging.
Acknowledging this fact, EuroPlas has introduced the Bioplastic compound, a green material solution with outstanding mechanical properties that enables end-products to be biodegradable within 12 months. We ensure your final products will meet all strict quality control criteria. With our bioplastic compound, you can have a full function in one material, which can be tailor-made based on your end-product requirements.
5.2. Bio filler
EuroPlas has more than 16 years of experience in providing sustainable solutions for the plastic industry. Bio filler (including BioMates 01, BioMates 02, and BioMates 03) is another cost-effective material solution for bioplastic end-products. It's a popular choice in the international market, including Europe and the USA. Our biodegradable materials not only save your production cost for bioplastic end-products but also improve their properties such as gloss, stiffness, etc. They can also act as anti-block and slipping agents in blown film, making them ideal for different applications.