Liquid Crystal Polymer (LCP) is a type of aromatic thermoplastic with a unique molecular structure, exhibiting excellent mechanical and electrical properties. It possesses high strength, high rigidity, heat resistance, good electrical insulation, and chemical resistance. As a result, LCP finds widespread use in various industries. This article will delve into the uses, properties, manufacturing processes, and applications of Liquid Crystal Polymer (LCP) in plastic production.
1. What is Liquid Crystal Polymer?
Liquid Crystal Polymer (LCP) is a type of partially crystalline aromatic polyester based on 4-hydroxybenzoic acid and related monomers. LCP is an aromatic thermoplastic with a distinctive molecular structure, comprising large, rigid molecules arranged in an ordered fashion during the melt phase to form a liquid crystal structure.
The molecular structure of Liquid Crystal Polymer (LCP) is characterized by large, rigid, rod-like molecules arranged in a specific order. These molecules often contain aromatic groups, such as phenyl or biphenyl. These aromatic groups create strong Van der Waals interactions between molecules, leading to an ordered arrangement.
LCP plastic is produced by copolymerizing polypropylene with one or more types of copolymers. The most common copolymers used in LCP plastic include ethylene-propylene-diene monomer (EPDM), ethylene-propylene (EP), and polypropylene-ethylene-propylene-diene monomer (PPEPDM).
.jpg)
What is Liquid Crystal Polymer?
2. How is Liquid Crystal Polymer produced?
Liquid Crystal Polymer (LCP) is an aromatic thermoplastic, manufactured through two primary methods:
Copolymerization polymerization method
This method involves using aromatic monomers, such as biphenyl-4,4'-dicarboxylic acid (BPDA), and aliphatic monomers, like 4,4'-diaminodiphenylether (DAPD), to create the polymer. The monomers are mixed and copolymerized using acid or base catalysts.
The polymerization process takes place in a heated reaction vessel. As the temperature rises, the monomers react to form polymer chains. These polymer chains are oriented in a specific direction, imparting the liquid crystal properties to LCP.
Hybrid polymerization method
This method utilizes an aromatic monomer, like BPDA, and an aliphatic monomer, such as 4,4'-dihydroxydiphenylether (DHP), to produce the polymer. The monomers are mixed and react with each other using acid or base catalysts.
The reaction occurs in a heated reaction vessel. As the temperature increases, the monomers react to form a covalent bond between polymer chains. This covalent bond enhances the strength and heat resistance of LCP.
After polymerization or copolymerization, LCP is cooled and ground into powder. The LCP powder is then used to manufacture products through injection molding, blow molding, or fiber drawing.
The properties of LCP depend on the chemical structure of the monomers used. Aromatic monomers provide LCP with high heat resistance and strength, while aliphatic monomers contribute to good flowability and ease of processing.
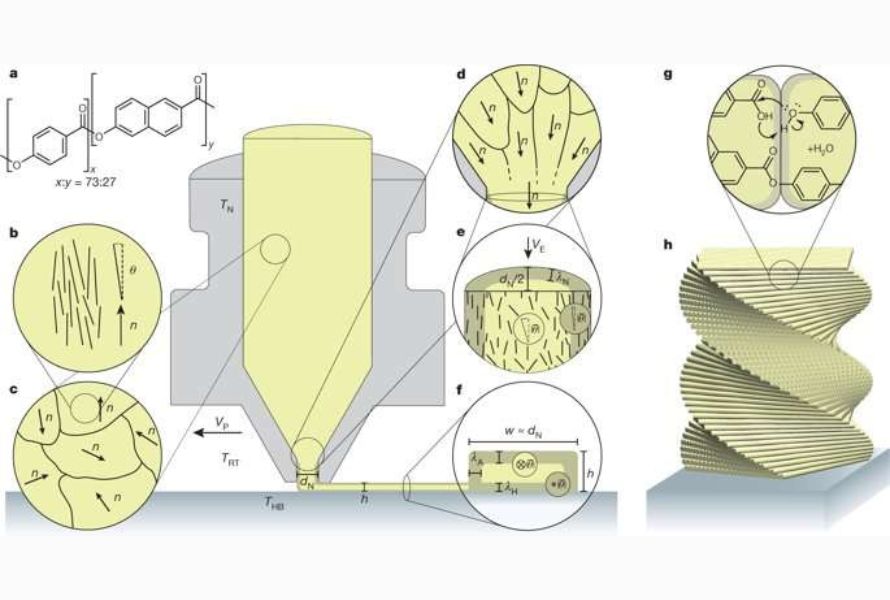
How is Liquid Crystal Polymer produced?
3. What are the properties of LCP?
Liquid Crystal Polymer (LCP) is a material with excellent mechanical, electrical, and thermal properties. The key characteristics of LCP include:
- High heat resistance: LCP exhibits high heat resistance, with a glass transition temperature (Tg) ranging from 200 to 350°C. This makes LCP an ideal choice for applications requiring high-temperature resistance, such as in the electronics, aerospace, and automotive industries.
- High mechanical strength: LCP has high tensile strength, compression strength, and rigidity. This makes LCP a suitable choice for applications demanding high mechanical strength, such as electronic components and load-bearing parts.
- High electrical strength: LCP has high electrical strength, with low dielectric constant (εr) and low dielectric loss. This makes LCP a good choice for electronic applications, including electronic components and conductive parts.
- Good flowability: LCP has good flowability, facilitating easy processing through methods like injection molding and blow molding.
- High flame resistance: LCP has high flame resistance, characterized by a high Limiting Oxygen Index (LOI). This makes LCP a suitable choice for applications requiring high flame resistance, such as in the automotive and aerospace industries.
- High chemical resistance: LCP exhibits high chemical resistance, capable of withstanding various types of chemicals. This makes LCP a good choice for applications requiring high chemical resistance, such as in the energy and chemical industries.
- High wear resistance: LCP has high wear resistance, making it a suitable choice for applications requiring resistance to wear and tear, such as in the automotive and aerospace industries.
.jpg)
What are the properties of LCP?
4. What are the disadvantages of Liquid Crystal Polymer?
- High cost: LCP is an expensive plastic, especially when compared to conventional thermoplastics like ABS, PC, or PET. This is due to the complex production process of LCP, which requires the use of high-quality materials.
- Difficult processing: LCP has high viscosity and is prone to degradation during processing, necessitating the use of specialized machinery and equipment. This can increase production costs and make the processing of LCP more challenging.
- High dielectric constant: The dielectric constant (DK) is a crucial parameter in electronic applications. A high dielectric constant can lead to power losses, reducing the efficiency of electronic devices. Although LCP has a lower dielectric constant compared to typical thermoplastics, it may still not meet all the requirements of high-end electronic applications.
- Susceptibility to environmental factors: LCP can be affected by high temperatures, moisture, and ultraviolet radiation. This can lead to a deterioration of the mechanical and electrical properties of LCP over time.
.jpg)
What are the disadvantages of Liquid Crystal Polymer
5. Liquid Crystal Polymer (LCP) in plastic manufacturing
Liquid Crystal Polymer (LCP) boasts high strength, high rigidity, heat resistance, excellent electrical insulation, and chemical resistance. Consequently, LCP finds extensive use across various industries, including:
- Electronics and telecommunications: LCP is utilized in electronic and telecommunication applications that demand high strength, high rigidity, and resistance to high temperatures. Examples include circuit boards, computer casings, LCD screens, and smartphones.
- Automotive: LCP is employed in automotive applications requiring high durability, stiffness, and resistance to high temperatures. Examples include drivetrain components, suspension parts, and exterior components.
- Aerospace: LCP is used in aerospace applications that require high durability, stiffness, and resistance to high temperatures. Examples include aircraft components, missiles, and satellites.
- Industrial: LCP is applied in industrial applications requiring high durability, stiffness, and resistance to high temperatures. Examples include electrical devices, machinery, and manufacturing equipment.
In plastic manufacturing, LCP plastic is specifically used in the following components:
- Load-bearing parts: LCP plastic exhibits tensile strength over 10 times that of conventional polypropylene, making it ideal for creating significantly stronger load-bearing parts. Typical applications include aircraft frames, automotive components, and industrial machinery parts.
- Heat-resistant parts: LCP plastic can withstand temperatures up to 200°C, considerably higher than many other plastic types. Common applications include heat-resistant components in the oil and gas industry and the electrical sector.
- Corrosion-resistant parts: LCP plastic demonstrates superior corrosion resistance compared to other plastics. Typical applications include corrosion-resistant parts in the chemical and food industries.
- Optical and electronic components: LCP plastic has high transparency and good electrical conductivity. Typical applications include optical components, electronic parts, and medical device components.
.jpg)
Liquid Crystal Polymer (LCP) in plastic manufacturing
6. Frequently asked questions
6.1. Does LCP affect human health?
During the production process, raw LCP materials involve the use of hazardous chemicals, but once completed, LCP becomes similar to other polymers. However, there are still some impacts of LCP on human health:
- Prolonged exposure to LCP may worsen symptoms and lead to allergic skin reactions, eye inflammation, or respiratory issues.
- Research on the health effects of LCP is ongoing. Based on existing studies, it suggests that LCP may pose some health risks to humans, particularly those exposed in the workplace environment.
6.2. What is the difference between LCP and Nylon?
LCP and Nylon are two types of thermoplastics with various applications in different fields. However, they differ fundamentally in structure, properties, and applications.
LCP is an aromatic thermoplastic polyester, while Nylon is a polyamide. Both plastics have a chain-like molecular structure, but LCP has a straighter molecular structure, while Nylon has a more twisted structure.
LCP has a melting temperature ranging from 340 to 400°C, significantly higher than Nylon (190 to 260°C). LCP also exhibits better impact resistance and wear resistance compared to Nylon. However, Nylon has higher tensile strength, better wear resistance, and greater flexibility than LCP.
6.3. What is the difference between LCP and Thermoplastics?
LCP is an aromatic thermoplastic polyester, while thermoplastics are polymers that can be melted and molded into various shapes when heated. Both have long-chain molecular structures, but LCP has a straighter structure, while thermoplastics have a twisted or branched structure.
LCP has a melting temperature ranging from 340 to 400°C, with the ability to resist various chemicals, including acids, bases, and solvents, much better than most other thermoplastics. LCP also exhibits better impact resistance and wear resistance compared to most other thermoplastics.
7. Conclusion
With outstanding properties such as flexibility, durability, and recyclability, LCP not only improves manufacturing performance but also contributes positively to environmental protection. Liquid Crystal Polymer is a material with many potential applications in various industries. LCP plastic is often used in applications requiring high durability, such as load-bearing parts in machinery, electronic devices, and automobiles.