Have you ever been bothered by the unpleasant odor of newly purchased plastic products? The new plastic smell is a common issue in the plastics manufacturing industry, directly impacting product quality and user experience. Not only is it unpleasant, but it also poses potential health risks. So how can we get rid of it? This article explores effective methods to deodorize plastic during production, giving you a better understanding of the process and safe cleaning practices.
1. Causes of Odors in New Plastics
The characteristic odor of new plastic products is a prevalent issue in the plastics manufacturing industry. Not only is it unpleasant to consumers, but it also poses potential health risks. What are the underlying causes of this phenomenon?
A primary factor is the thermal decomposition of additives. During the heating and molding process, additives such as stabilizers, plasticizers, and antioxidants can decompose, releasing volatile organic compounds (VOCs). These VOCs are responsible for the distinctive smell of new plastics.
Additionally, incomplete polymerization can contribute to the unpleasant odor. When monomers do not fully bond during the manufacturing process, free radicals may remain. These free radicals can easily volatilize at room temperature, causing the unpleasant smell.
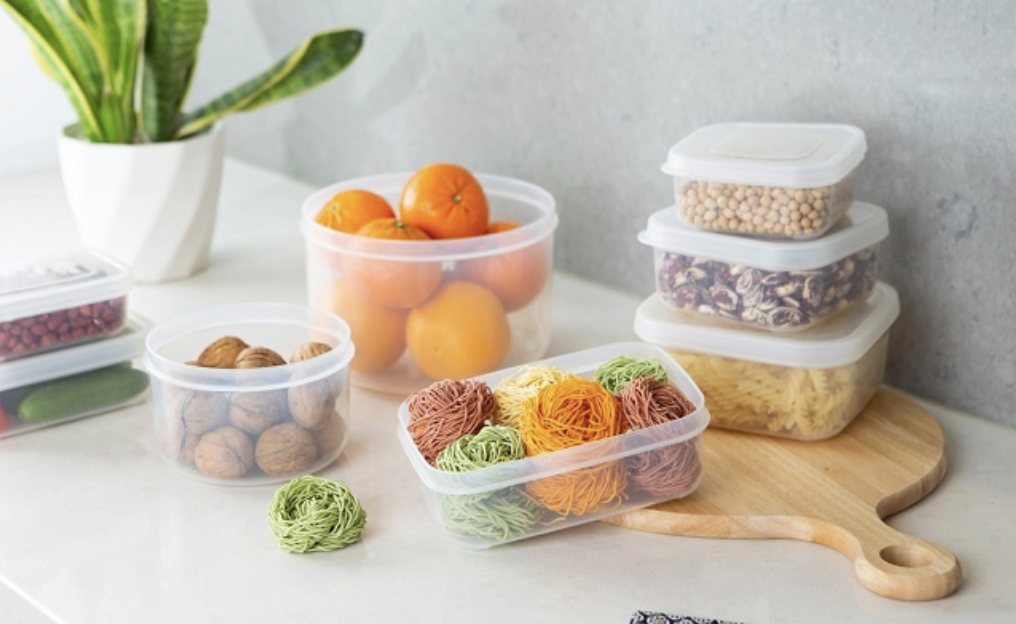
Other contributing factors include the accumulation of contaminants and oils from the manufacturing process. Machinery and molds may leave behind residues of lubricants or other substances, imparting an undesirable odor to the finished product.
Furthermore, the manufacturing environment can significantly impact the odor. High temperatures, humidity, and poor ventilation can accelerate the release of odor-causing compounds. In enclosed spaces, these odors can accumulate and become more concentrated.
Finally, the quality of raw materials plays a crucial role. Recycled plastics or low-quality resins may contain impurities that contribute to the unpleasant odor.
In conclusion, the odor of new plastics can negatively impact both consumer experience and product reputation. A thorough understanding of the root causes is essential for developing effective odor reduction strategies. By identifying and addressing each contributing factor, manufacturers can significantly improve product quality and consumer satisfaction.
2. How to Get Rid of That New Plastics Smell
The unpleasant odor associated with new plastic products is a common issue in the plastics manufacturing industry. This odor can negatively impact consumer satisfaction and product quality. Several effective methods can be employed to eliminate plastic odors during the manufacturing process:
2.1. Use of Odor-Eliminating Additives
One of the most effective methods for reducing plastic odors is the incorporation of specialized odor-eliminating additives. These additives are introduced during the plastic compounding process, minimizing odors from the initial stages of production.
- Select an additive compatible with the specific type of plastic being used.
- Adhere to the manufacturer's recommended mixing ratios.
- Ensure that the additive does not compromise the final product's performance.
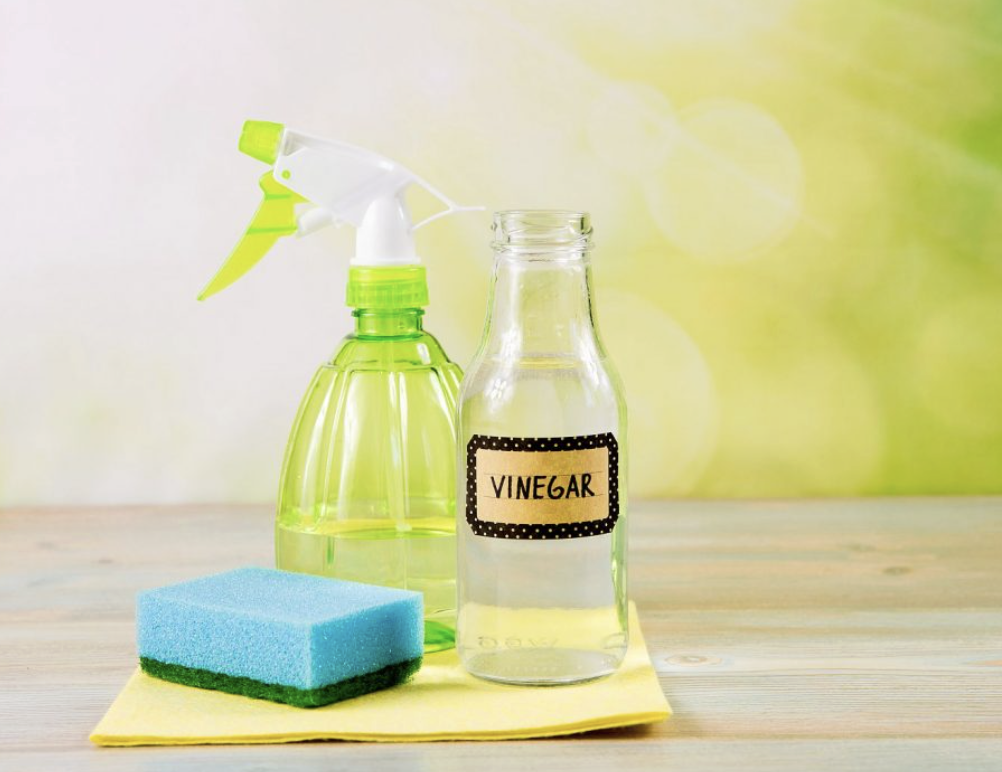
2.2. Optimization of the Heating Process
Uneven or excessive heating is a common cause of plastic odors. To mitigate this issue:
- Strictly control the temperature throughout the manufacturing process.
- Utilize modern heating equipment capable of precise temperature regulation.
- Avoid overheating, as this can degrade product quality in addition to causing odors.
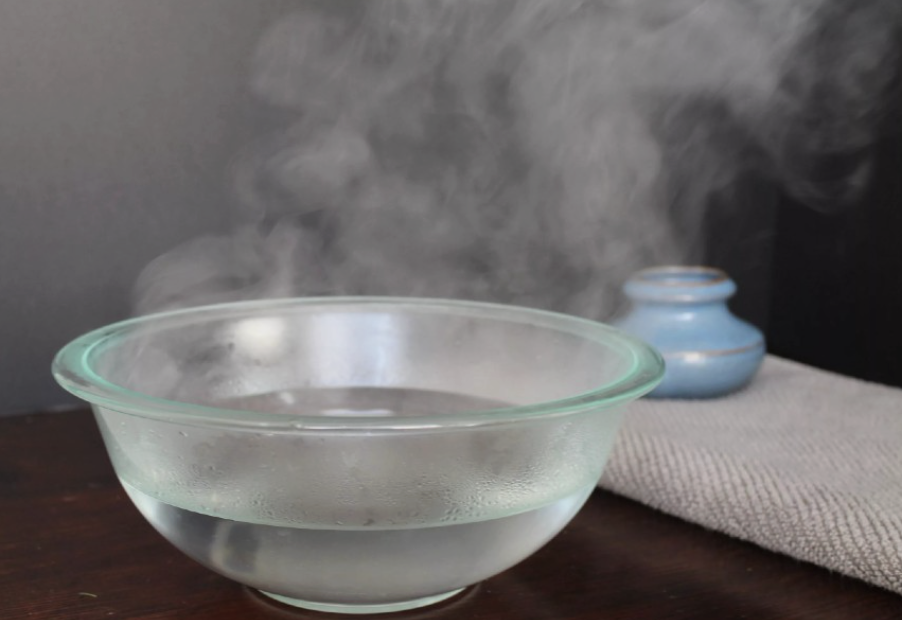
2.3. Ventilation and Filtration Systems
To remove volatile organic compounds (VOCs), the primary cause of plastic odors, effective ventilation and filtration systems are essential:
- Install industrial ventilation and filtration systems in the production area.
- Employ activated carbon filters to absorb odor-causing compounds.
- Regularly maintain and replace filters to ensure optimal performance.
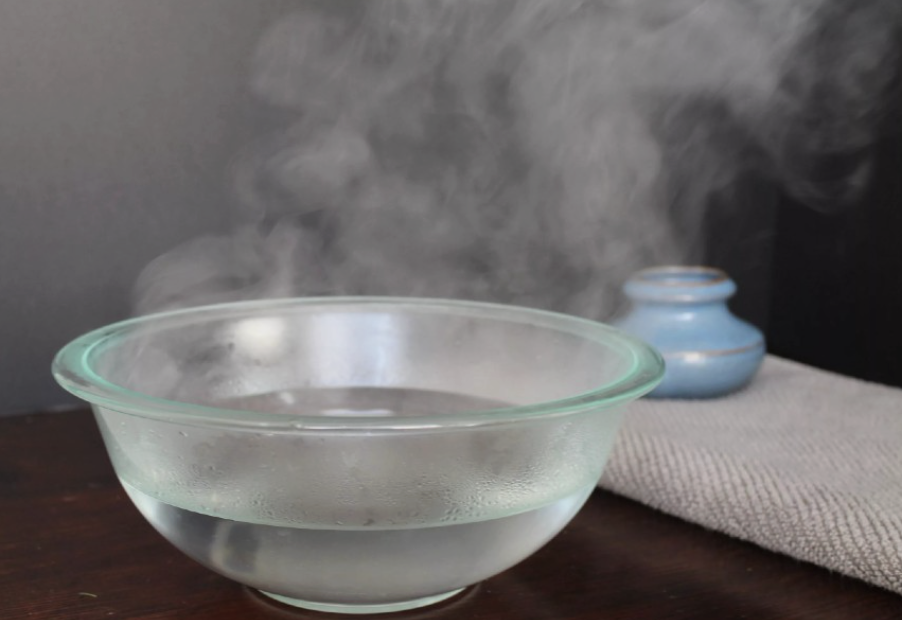
2.4. Post-Production Treatment
In addition to in-process methods, post-production treatments can be applied:
- Ozone chambers: Expose products to ozone to break down odor-causing compounds.
- Aeration: Allow products to air out in a well-ventilated area to facilitate the evaporation of volatile compounds.
- Washing: For certain plastics, washing with a warm water solution containing vinegar or baking soda can help eliminate odors.
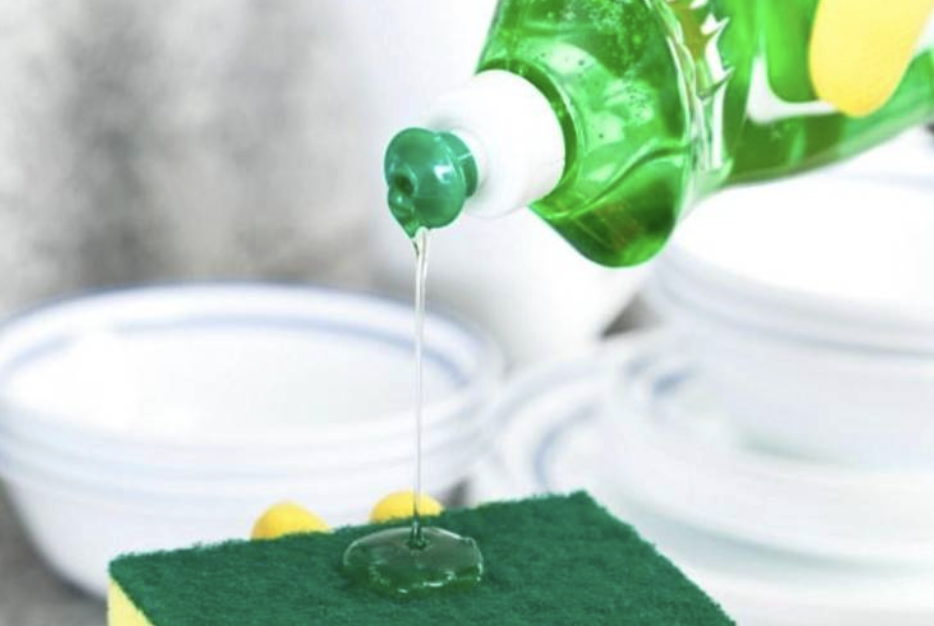
2.5. Research and Development of New Plastic Formulations
Investing in research to develop new plastic formulations can significantly reduce odors:
- Experiment with biodegradable plastics.
- Develop low-odor polymer compounds.
- Optimize the ratio of ingredients in plastic formulations to minimize odors.
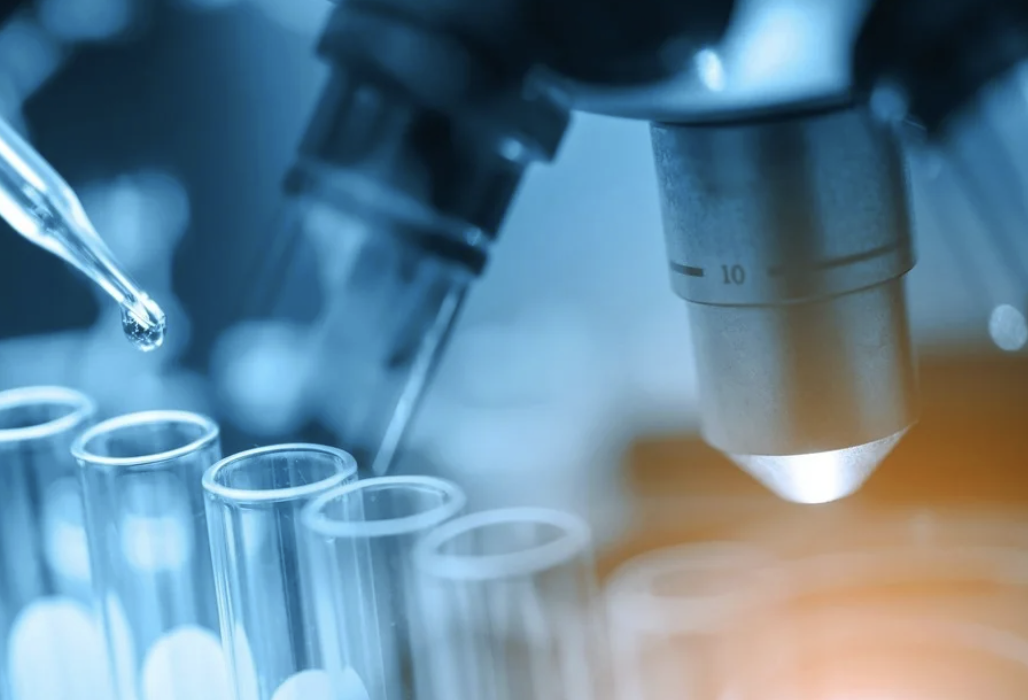
By implementing a combination of these methods, manufacturers can effectively address the issue of plastic odors, enhance product quality, and improve customer satisfaction.
3. Advanced Technologies for Odor Reduction in Plastics
In recent years, several advanced technologies have been developed to effectively address the issue of plastic odors. Some notable technologies include:
3.1. Cold Plasma Technology
Cold plasma is an innovative surface treatment method capable of rapidly and effectively eliminating plastic odors.
- Principle: Low-temperature plasma is used to decompose odor-causing molecules on the plastic surface.
- Advantages: Does not damage material structure, is environmentally friendly, and can be applied to various types of plastics.
- Applications: Particularly effective for complex-shaped or small-sized plastic products.
3.2. Silver Nanoparticle Technology
Silver nanoparticles not only possess antimicrobial properties but also exhibit effective odor-eliminating capabilities.
- Mechanism: Silver nanoparticles are integrated into the polymer structure of plastics, facilitating the decomposition of odor-causing organic compounds.
- Efficacy: Provides long-lasting odor control, even after product use.
- Applications: Suitable for medical, household, and electronic products made of plastic.
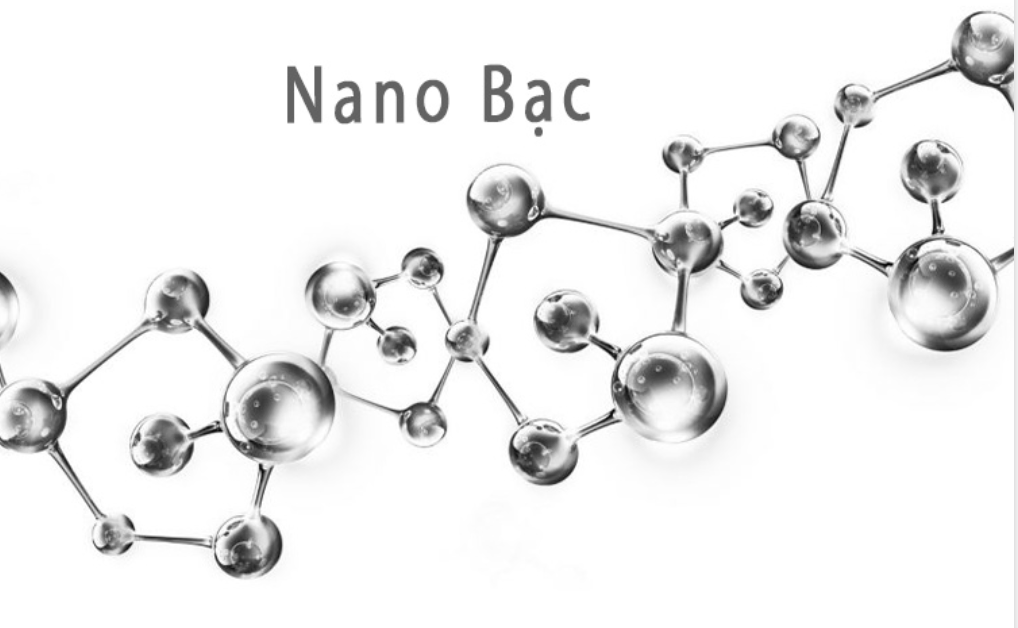
3.3. TiO2 Photocatalysis
This technology utilizes titanium dioxide (TiO2) in conjunction with UV light to eliminate odors.
- Principle: When exposed to UV light, TiO2 generates free radicals that can decompose odor-causing organic compounds.
- Advantages: Highly effective, generates no toxic waste, and can be integrated into existing manufacturing processes.
- Challenges: Requires a stable UV light source to maintain odor removal efficiency.
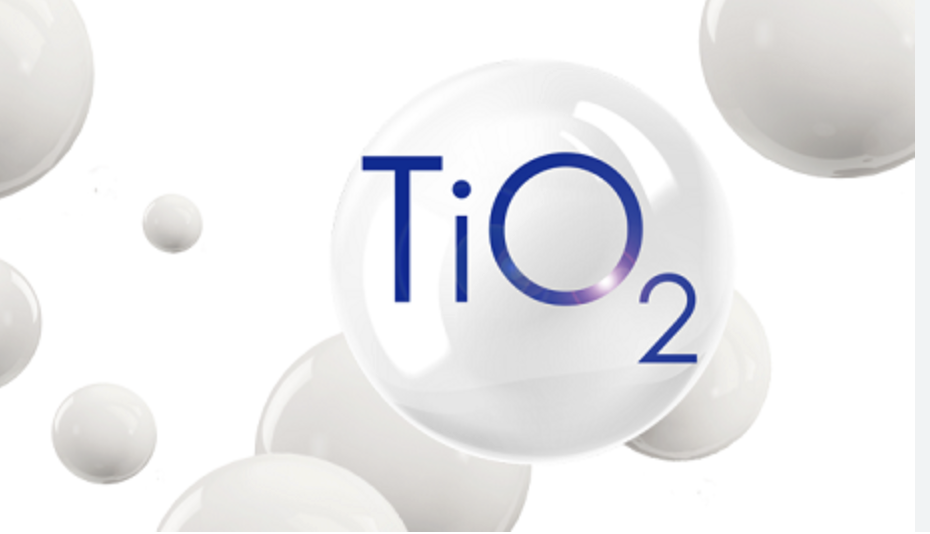
3.4. Microbial Technology
Specific microorganisms are employed to decompose odor-causing compounds.
- Process: Microorganisms are cultivated and applied in post-production treatment processes.
- Advantages: A natural, environmentally friendly method that can address odors at a molecular level.
- Limitations: Requires strict control of environmental conditions to ensure optimal microbial activity.
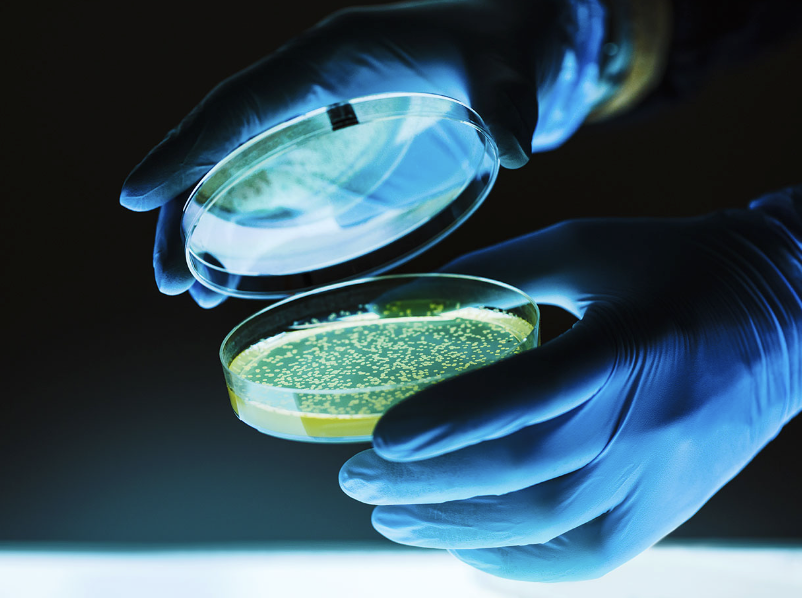
3.5. Ultrasonic Technology
Ultrasonic waves are used to break down the bonds of odor-causing molecules.
- Mechanism: Ultrasonic waves generate microbubbles in the treatment solution, which collapse and release energy that disrupts the structure of odor-causing molecules.
- Advantages: Rapid treatment and can be applied to a large number of products.
- Applications: Effective for medium-sized and small plastic products.
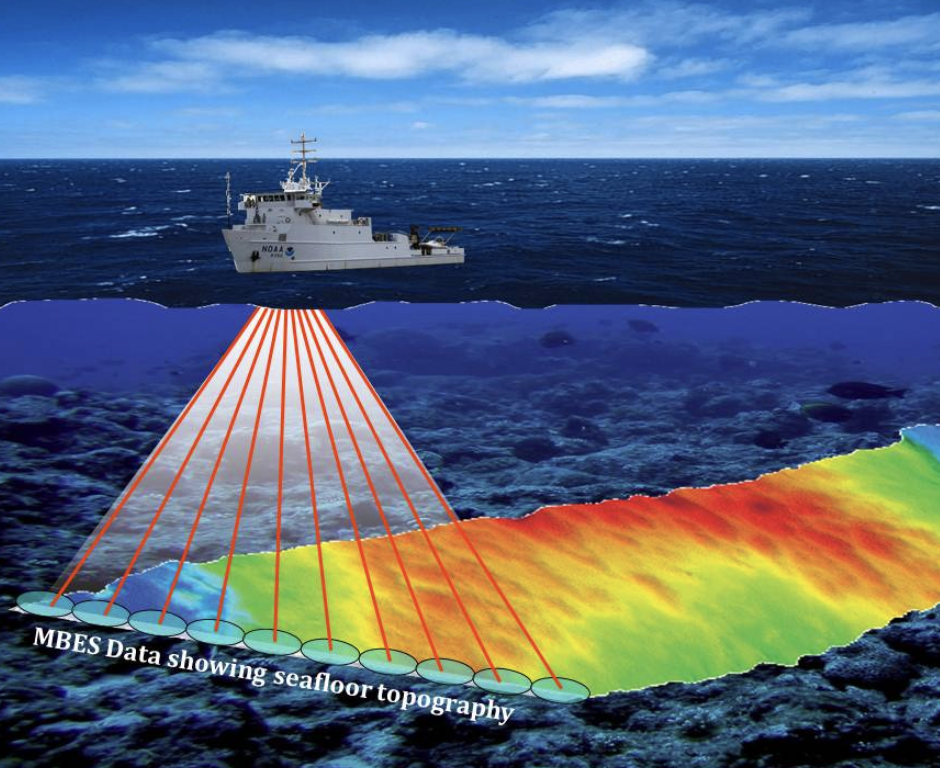
The implementation of these advanced technologies not only enhances the effectiveness of odor removal but also contributes to improved product quality and increased competitiveness within the plastics industry. However, selecting the appropriate technology depends on factors such as product characteristics, production scale, and investment capabilities.
4. Conclusion
Developing effective methods to eliminate plastic odors is crucial in today's plastics manufacturing industry. By combining traditional methods such as additive incorporation and process optimization with advanced technologies like cold plasma, silver nanoparticles, and photocatalysis, manufacturers can comprehensively address the issue of plastic odors. This not only enhances product quality but also meets the growing demands of consumers and environmental regulations. Investing in research, development, and implementation of tailored solutions for each product line can enhance a company's competitiveness and contribute to the sustainable development of the plastics industry.
5. About EuroPlas
With a diverse range of high-quality filler masterbatch products, EuroPlas is committed to providing comprehensive solutions to meet the demands of the plastics industry. EuroPlas not only offers premium products but also strives for a sustainable future. Our filler masterbatch solutions minimize environmental impact and meet sustainability standards.
For detailed and accurate advice, please fill out the contact form on our website. With our extensive experience and dedicated team of experts, EuroPlas is committed to providing optimal solutions tailored to your specific project.