Nylon 4 6 is a unique polyamide known for its exceptional strength and durability. This versatile material is utilized across various industries due to its impressive performance characteristics. In this article, we will explore an overview of Nylon 4 6, its properties, and its diverse applications. Additionally, we will compare it to other Nylon types to highlight its distinct advantages.
1. Overview Of Nylon 4 6
Nylon 4 6, also known as PA46 or Polyamide 46, is a high-heat-resistant polyamide renowned for its exceptional thermal stability and mechanical properties. This aliphatic polyamide is synthesized through the polycondensation of 1,4-diaminobutane and adipic acid, resulting in a material that boasts a higher melting point than both Nylon 6 and Nylon 66.
Due to its ability to withstand high loads and stresses in aggressive environments, Nylon 4/6 is particularly well-suited for automotive applications. It is commonly utilized in critical components such as engine and transmission systems, engine management, air intake, braking, and cooling systems. Its excellent creep resistance, toughness, and wear characteristics make it a preferred choice for manufacturers seeking reliable performance in high-temperature settings. Overall, Nylon 4/6 represents a significant advancement in polyamide technology, providing robust solutions across various industrial sectors.

2. Properties Of Nylon 4 6
Nylon 4 6 stands out with its exceptional performance characteristics, distinguishing it from other engineering thermoplastics, as follows:
- High Melting Temperature: Approximately 295 °C, enabling use in high-temperature applications.
- Increased Crystallinity: Around 70%, contributing to enhanced material performance and stability.
Fast Crystallization Rate: Results in improved processing efficiency and mechanical properties.
- Unreinforced: Heat distortion temperature of 190 °C.
- Glass fiber-reinforced: Can withstand up to 290 °C.
- Enhanced Wear Resistance: Outperforms competing polyamides like Nylon 6 and Nylon 66.
- Excellent Friction Behavior: Ideal for applications requiring low friction and wear.
- High Rigidity: Provides structural integrity under stress.
- Moisture Absorption: Effective in environments where humidity is a factor.
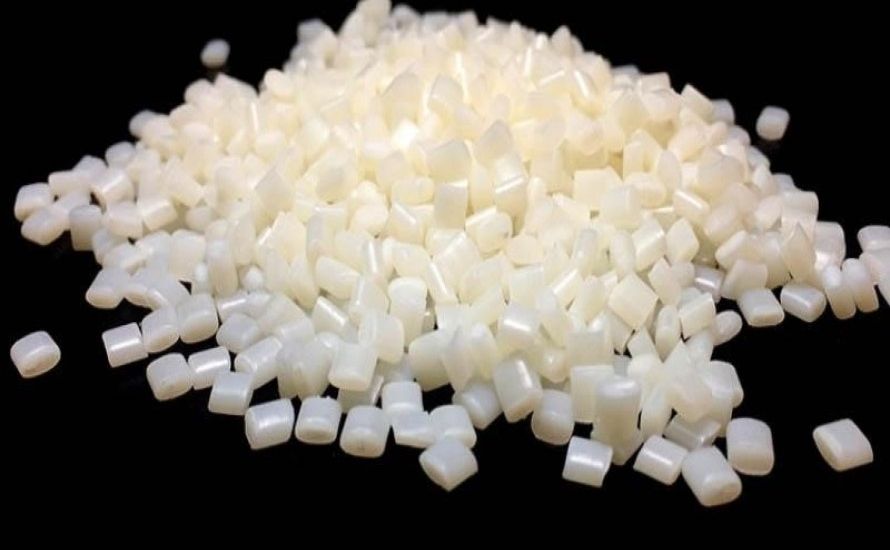
Read more: What is nylon? All about its properties and common uses
3. Applications Of Nylon 4 6 Across Industries
Nylon 4 6's versatility and superior performance make it an ideal choice for these applications, ensuring durability and efficiency in various demanding environments. Here are some key applications:
Automotive and Transportation:
- Chain Tensioners: Ensures optimal tension in timing chains, enhancing engine performance.
- Engine Covers: Provides high heat resistance and structural integrity, protecting engine components.
- Oil Filter Parts: Offers durability and chemical resistance for reliable filtration.
- Signaling Lamp Bases: Delivers excellent thermal stability for automotive lighting systems.
- Thrust Washers: Reduces friction in moving parts, extending component life.
- Gear-Shift Forks: Ensures precise gear engagement, improving vehicle performance.
- Speedometer Gear Wheels: Provides accurate speed readings with high dimensional stability.
- Fuel Distributors: Ensures efficient fuel delivery in automotive engines.
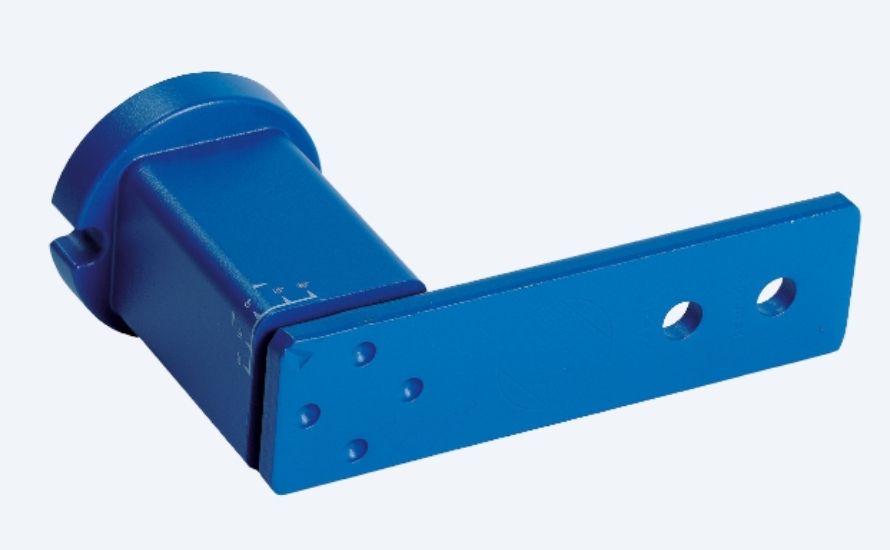
Electrical & Electronics:
- Surface-Mount Devices: Used in compact electronic circuits for reliable performance.
- Connectors: Offers excellent insulation properties and mechanical strength for electrical connections.
- End Laminates: Provides structural support in various electronic assemblies.
- Brush Holders in Electric Motors: Ensures reliable contact and performance in motor applications.
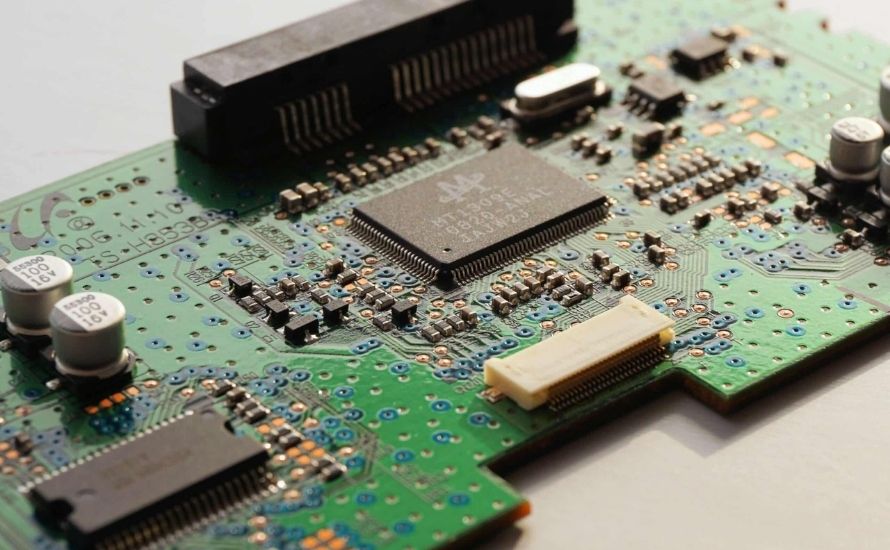
Appliances:
- Safety Controls: Utilized in appliances such as kettles and ovens, where high thermal resistance is crucial for safety and reliability.
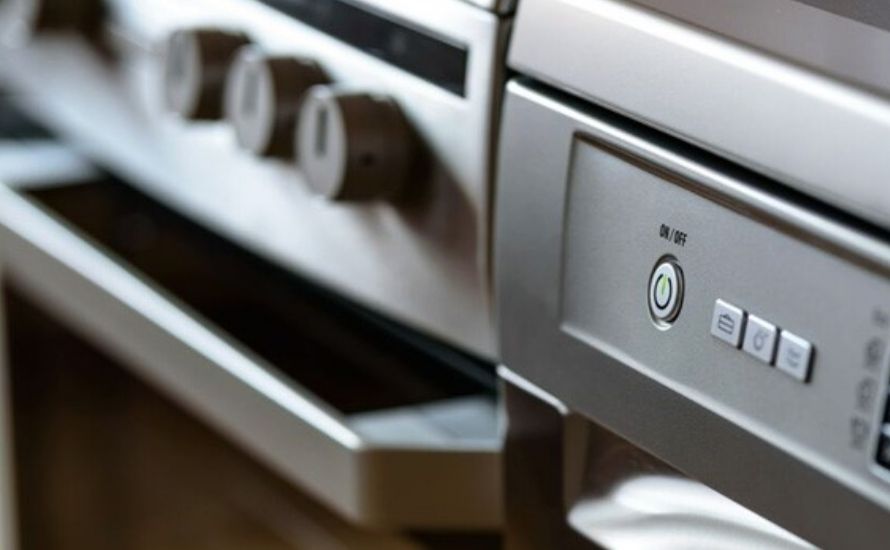
4. Comparing To Other Nylons
This section provides a concise comparison of Nylon 4 6 with other Nylon types, highlighting their unique properties and applications to help inform material selection.
Property/Type |
Nylon 4 6 |
Nylon 6 |
Nylon 6/6 |
Nylon 6/10 |
Nylon 6/12 |
Nylon 11 |
Nylon 12 |
Tensile Strength |
Exceptional |
High |
Excellent |
High |
Moderate |
Good |
Outstanding |
Melting Point |
-265°C |
220 -225°C |
High |
High |
Moderate |
Moderate |
Moderate |
Chemical Resistance |
Excellent |
Good |
Good |
Excellent |
Excellent |
Excellent |
Excellent |
Moisture Absorption |
Low |
Moderate |
Moderate |
Low |
Low |
Low |
Low |
Impact Resistance |
Reasonable |
Good |
Excellent |
Good |
Moderate |
Excellent |
Outstanding |
Flexibility |
Moderate |
Moderate |
Moderate |
Good |
Good |
Good |
Good |
UV Resistance |
Moderate |
Low |
Low |
Low |
Low |
Good |
Good |
Applications |
Automotive, Electrical, Industrial |
Textitle, Automotive, Consumer Goods |
Automotive, Electrical, Textitle |
Automotive, Electrical, Industrial |
Automotive, Medical, Industrial |
Automotive, Medical, Sporting |
Automotive, Consumer Goods, Industrial
|
5. Conclusion
In conclusion, Nylon 4 6 stands out as a robust and versatile material, ideal for a wide range of industrial applications due to its exceptional properties. Its unique combination of strength, thermal stability, and chemical resistance makes it a preferred choice in sectors like automotive and electrical manufacturing. By understanding its benefits and comparing it with other Nylon types, businesses can make informed material selections that enhance product performance and durability. Embracing Nylon 4/6 can lead to improved efficiency and success in various applications.
6. About EuroPlas’ PA Products
EuroPlas offers advanced PA6 and PA66 blend compounds, expertly formulated to combine the strengths of both polyamide types. PA6 provides ease of processing and cost-effectiveness, while PA66 enhances temperature resistance, stiffness, and abrasion resistance. This blend incorporates elastomers and impact strength modifiers, resulting in a resilient material with exceptional mechanical properties.
Commonly utilized in the automotive and motorcycle industries, our PA6, PA66 blend compounds are ideal for applications such as roller bearings, carburetors, exhaust gas control valves, and fuel tank lids. With 15 years of industry expertise, EuroPlas understands the challenges businesses face in sourcing reliable raw materials. Our PA6, PA66 blend compounds ensure the production of precise, durable, and high-performance final products.
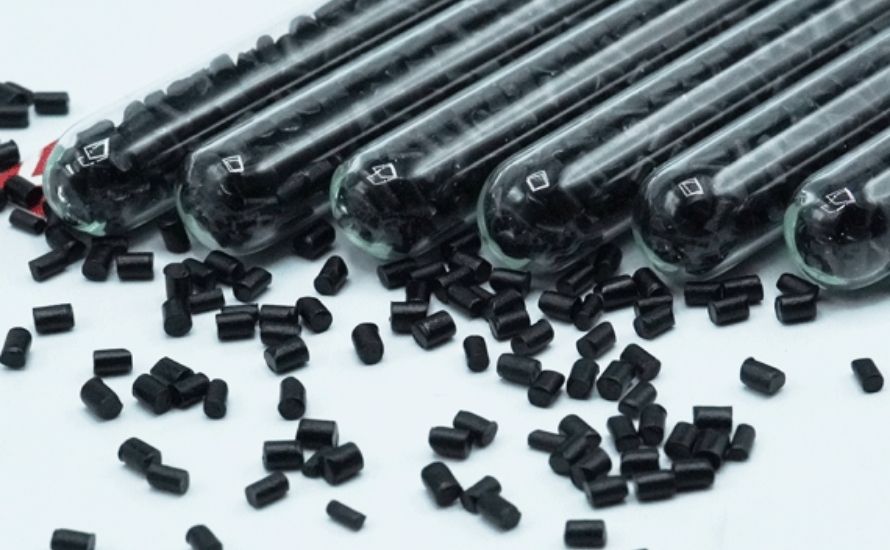
Ready to elevate your production with our premium PA6, PA66 blend compounds? Discover how EuroPlas can meet your material needs and enhance your product performance.
Contact us today to learn more about our offerings and how we can partner for your success!