PA 12, also known as Nylon 12, is a versatile engineering plastic known for its exceptional properties and wide-ranging applications. With its high tensile strength, durability, chemical resistance, and thermal stability, PA 12 has become a preferred choice in industries such as automotives, industrial manufacturing, oil and gas, electrical and electronics, and more. In this blog, we will delve into the definition of PA 12, explore its key features, and discuss its common uses across different sectors. Whether you're curious about the properties of PA 12 or looking to identify potential applications, this article will provide valuable insights into the world of this reliable and versatile engineering plastic.
1. What is PA 12?
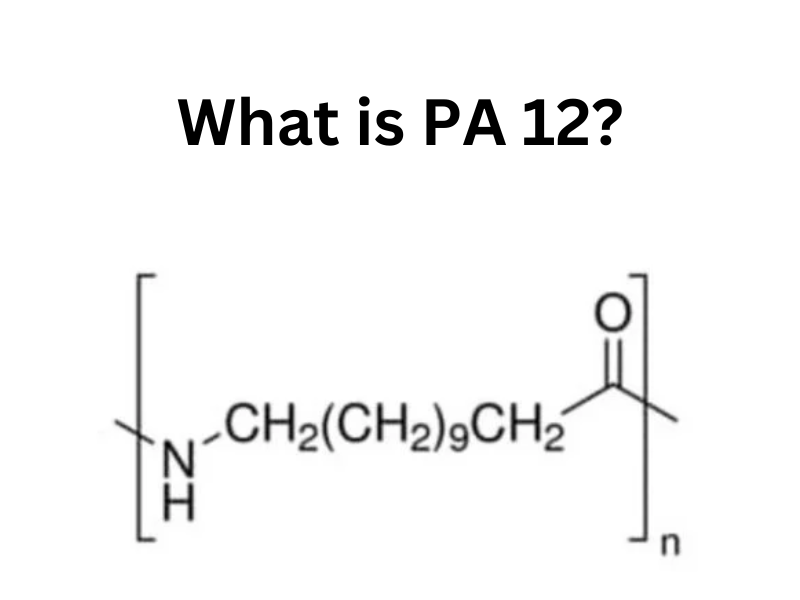
PA 12
PA 12, also referred to as polyamide 12 or Nylon12, is a thermoplastic polymer that belongs to the family of polyamides. It is known for its unique chemical composition, which gives it distinctive properties and makes it suitable for a wide range of applications.
PA 12 is composed of repeating units of amide groups (-CO-NH-) connected by carbon atoms. This structure gives the material its strength, durability, and resistance to wear and tear. The presence of amide groups also imparts excellent thermal stability to PA 12, allowing it to withstand high temperatures without losing its mechanical properties.
The molecular structure of PA 12 contributes to its advantageous properties. The long chains of carbon atoms provide flexibility and toughness to the material, enabling it to withstand impact and deformation. Additionally, the amide groups offer strong intermolecular interactions, resulting in high tensile strength and resistance to chemicals.
PA 12 is synthesized through a polymerization process, where the monomers of Nylon12 are chemically bonded together to form long chains. This process can be controlled to achieve specific molecular weights and desired material properties.
Due to its unique composition, PA 12 exhibits favorable characteristics such as excellent dimensional stability, low moisture absorption, and good electrical insulation properties. These attributes make PA 12 a preferred choice for various industrial applications where strength, durability, and reliability are required.
Read more: What is nylon? All about its properties and common uses
2. PA 12 material properties
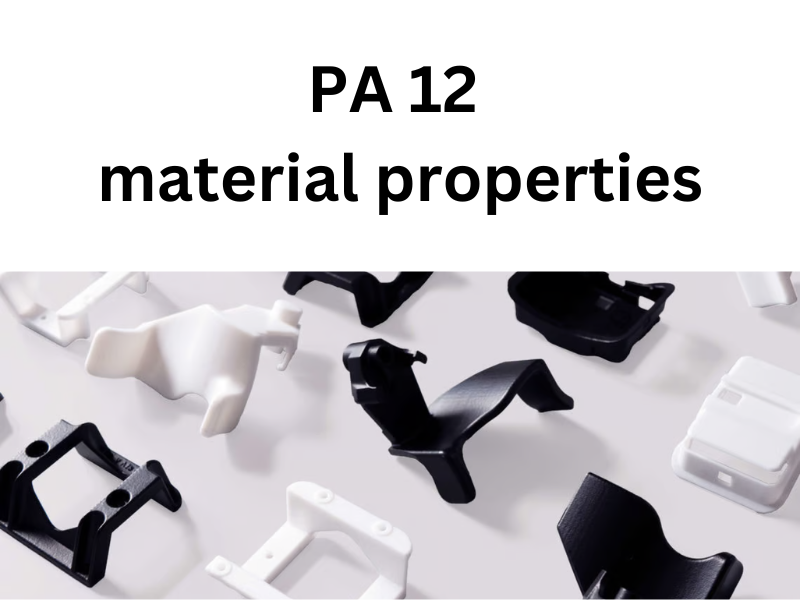
PA 12 material properties
PA 12 is a thermoplastic material that possesses a range of desirable properties. These properties make it a preferred choice for various industrial applications. Let's delve into the Nylon 12 material properties and understand why it is highly regarded.
- High Tensile Strength: PA 12 material exhibits exceptional tensile strength, making it ideal for applications that require robust and reliable materials.
- Excellent Durability and Toughness: PA 12, also referred to as Nylon 12, offers excellent durability and toughness, ensuring its ability to withstand harsh conditions and resist wear and tear.
- Impact Resistance: Nylon 12 material properties include notable impact resistance, allowing it to withstand sudden forces without cracking or breaking.
- Chemical Resistance: PA 12 Nylon demonstrates strong resistance to various chemicals, making it valuable in industries where exposure to solvents, oils, and fuels is common.
- Thermal Stability: PA 12 material exhibits remarkable thermal stability, maintaining its mechanical properties even at elevated temperatures. This property is advantageous in applications involving heat exposure.
- Low Moisture Absorption: Nylon 12, or PA 12, demonstrates low moisture absorption, resulting in enhanced dimensional stability and reliability in humid or wet environments.
- Dimensional Stability: The material properties of PA 12 Nylon ensure excellent dimensional stability, maintaining its shape and size over time, even under changing environmental conditions.
- Good Electrical Insulation Properties: PA 12 material possesses favorable electrical insulation properties, making it suitable for applications that require effective electrical insulation to prevent malfunctions or short circuits.
In summary, Polyamide 12 possesses a range of advantageous material properties that contribute to its versatility and suitability for various applications. Its strength, durability, chemical resistance, thermal stability, low moisture absorption, and electrical insulation properties make it a reliable choice for industries seeking a high-performance thermoplastic material.
3. Comparison of PA 12 with other polyamides
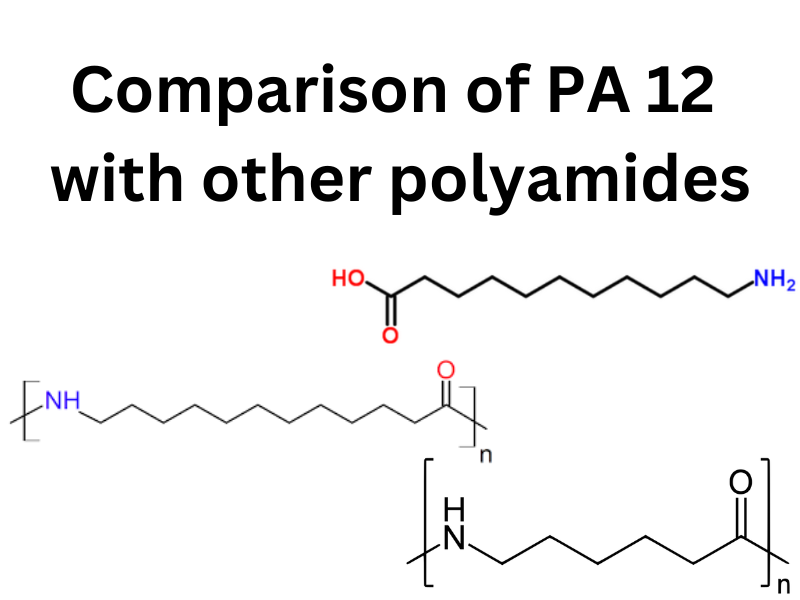
Comparison of PA with other polyamides
3.1 Nylon (PA) 12 vs Nylon (PA) 6
When considering the comparison between PA 12 and PA 6, commonly known as Nylon 12 and Nylon 6, respectively, several key factors come into play. Let's explore the differences and similarities between Nylon 12 vs Nylon 6.
Starting with the chemical structure, both PA 12 and PA 6 belong to the family of polyamides and share similar amide group (-CO-NH-) linkages. However, they differ in terms of their monomer composition and the number of carbon atoms in their repeating units.
PA 12 Nylon is derived from the monomer laurolactam, while Nylon 6, or PA 6, is synthesized from the monomer caprolactam. PA 12 has a higher number of carbon atoms in its repeating unit compared to PA 6. This variation in molecular structure leads to distinct material properties and performance characteristics.
In terms of mechanical properties, PA 12 generally exhibits higher tensile strength and impact resistance than PA 6. Nylon 12's enhanced toughness and durability make it suitable for applications that require robust materials capable of withstanding mechanical stress and impact forces.
Chemical resistance is another area where PA 12 and PA 6 differ. PA 12 demonstrates superior resistance to chemicals, solvents, oils, and fuels, making it highly suitable for applications in the automotive, chemical, and oil and gas industries. On the other hand, PA 6 offers good chemical resistance but may not perform as well as PA 12 in highly aggressive chemical environments.
Thermal stability is another factor to consider. PA12 Nylon exhibits better resistance to high temperatures than PA 6. It can retain its mechanical properties and dimensional stability even at elevated temperatures, making it suitable for applications involving heat exposure.
Regarding moisture absorption, PA 12 and PA 6 demonstrate similar characteristics. Both materials have low moisture absorption rates, leading to enhanced dimensional stability in humid or wet environments.
Overall, while both PA 12 and PA 6 share the advantages of polyamides such as good mechanical properties and chemical resistance, PA 12 offers improved strength, impact resistance, chemical resistance, and thermal stability compared to PA 6.
3.2 Nylon (PA) 11 vs Nylon (PA) 12
Comparing PA 11 and PA 12, also known as Nylon 11 and Nylon 12, respectively, reveals some distinct differences in their properties and applications. Let's explore the comparison between Nylon 11 vs Nylon 12.
Starting with the chemical structure, both PA 11 and PA 12 are polyamides, characterized by amide group (-CO-NH-) linkages. However, they differ in terms of their monomer composition and the number of carbon atoms in their repeating units.
Nylon 11 is derived from the monomer 11-aminoundecanoic acid, while Nylon 12 is synthesized from the monomer laurolactam. Nylon PA 12 has a higher number of carbon atoms in its repeating unit compared to PA 11, which impacts their material properties and applications.
In terms of mechanical properties, PA 12 generally exhibits higher tensile strength, impact resistance, and toughness than PA 11. Nylon 12's enhanced mechanical performance makes it suitable for applications requiring strength, durability, and resistance to impact and wear.
When it comes to chemical resistance, PA 12 and PA 11 offer similar characteristics. Both materials demonstrate good resistance to various chemicals, solvents, and oils, making them suitable for applications in the automotive, industrial, and oil and gas sectors.
Thermal stability is another aspect to consider. PA 12 exhibits better resistance to high temperatures than PA 11. It can withstand elevated temperatures while maintaining its mechanical properties, making it suitable for applications involving heat exposure.
In terms of moisture absorption, PA 11 and PA 12 exhibit similar properties. Both materials have low moisture absorption rates, resulting in enhanced dimensional stability in humid or wet environments.
Overall, while both PA 11 and PA 12 have advantages as polyamides, Nylon 12 offers improved mechanical properties, including higher tensile strength and impact resistance, compared to Nylon 11. Additionally, PA 12 demonstrates better thermal stability, making it a preferred choice for applications where high strength, durability, and resistance to heat and chemicals are essential.
4. Common applications of PA 12
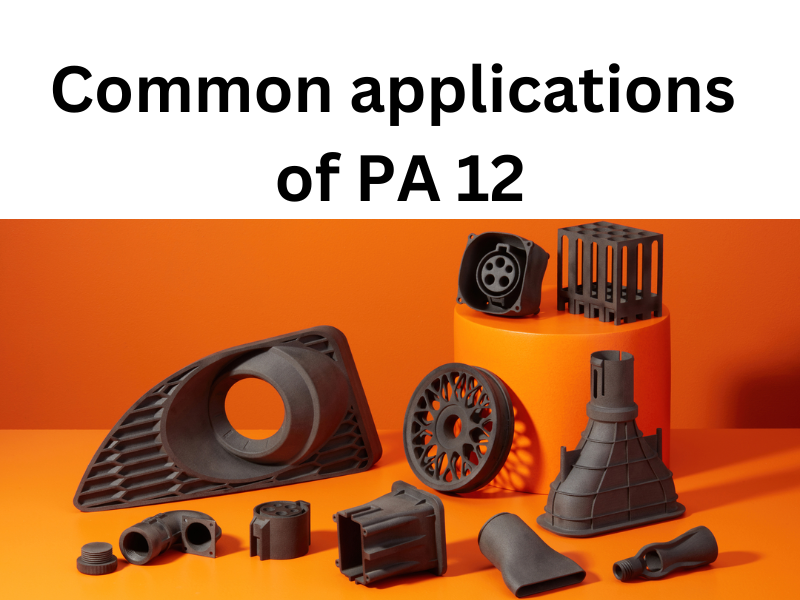
Common applications of PA 12
Polyamide 12 finds wide-ranging applications across various industries due to its advantageous material properties. Let's explore some of the common applications where Nylon PA 12 demonstrates its versatility and reliability.
- Automotive Industry: PA 12 is extensively used in the automotive sector for various applications. Its high strength, durability, and chemical resistance make it suitable for components such as fuel lines, brake tubing, and cable sheathing. Additionally, PA 12's low moisture absorption and dimensional stability ensure its performance in demanding automotive environments.
- Industrial Manufacturing: PA 12 finds widespread use in industrial manufacturing processes. Its excellent mechanical properties, including high tensile strength and impact resistance, make it ideal for applications such as gears, bearings, bushings, and conveyor components. PA 12's chemical resistance also allows its utilization in chemical processing equipment and pump parts.
- Oil and Gas Industry: PA 12's exceptional chemical resistance and durability make it well-suited for applications in the oil and gas sector. It is commonly used for flexible pipes, tubing, and connectors in offshore and onshore operations. PA 12's resistance to chemicals and hydrocarbons enables it to withstand harsh environments and maintain reliable performance.
- Electrical and Electronics: PA 12's good electrical insulation properties make it suitable for electrical and electronic applications. It is used in cable insulation, connectors, and wire harnesses where reliable electrical insulation is essential. PA 12's properties help prevent electrical malfunctions and ensure the safety and efficiency of electrical systems.
- PA 12 3D printing: PA 12 has gained popularity in the field of 3D printing. Its compatibility with various 3D printing technologies, such as selective laser sintering (SLS), allows for the creation of intricate and functional parts with high accuracy and mechanical strength. PA 12's ability to retain its properties at elevated temperatures makes it a preferred choice for 3D printing applications.
- Consumer Goods: PA 12 is utilized in the production of consumer goods due to its versatility and reliability. It can be found in items such as sporting goods, tool handles, and protective cases. PA 12's mechanical properties and chemical resistance contribute to the durability and long lifespan of consumer products.
In summary, polyamide 12, exhibits a wide range of applications across industries. Its utilization in the automotives, industrial manufacturing, oil and gas, electrical and electronics, 3D printing, and consumer goods sectors highlights its versatility and performance. The material properties of PA 12, including strength, durability, chemical resistance, and electrical insulation, contribute to its reliability and make it an excellent choice for various applications.
PA engineering plastic compound
At EuroPlas, we take pride in being a leading masterbatch manufacturer in Vietnam, specializing in the production of high-quality PA (polyamide) engineering plastic compounds. Our expertise and commitment to delivering exceptional products have positioned us as a trusted partner for various industries seeking reliable plastic solutions.
As an established player in the market, our focus is on producing top-quality PA engineering plastic compounds that meet the stringent standards of our customers. We understand the importance of reliable materials in the manufacturing process, and that's why we prioritize the production of high-performance compounds that consistently meet and exceed industry requirements.
EuroPlas' PA engineering plastic compounds are developed using state-of-the-art manufacturing technologies and processes. Our dedicated team of experts ensures that every batch of our compounds undergoes rigorous quality control procedures to guarantee consistency and reliability. We adhere to strict manufacturing protocols and implement advanced testing methods to ensure that our products consistently meet the desired specifications.
With a deep understanding of the diverse needs of different industries, our PA engineering plastic compounds are tailored to specific applications, providing optimal performance and durability. Whether you require compounds for automotive components, electrical and electronic parts, industrial equipment, or consumer goods, EuroPlas has the expertise to meet your requirements.
We pride ourselves on our customer-centric approach, striving to build long-term partnerships based on trust, reliability, and outstanding customer service. Our dedicated team of professionals is always ready to provide technical support, guidance, and customized solutions to meet your unique project needs.
If you are looking for high-quality PA engineering plastic compounds, EuroPlas is here to be your trusted partner. Contact us today to discuss your specific requirements, and let our team assist you in finding the perfect solution for your application.