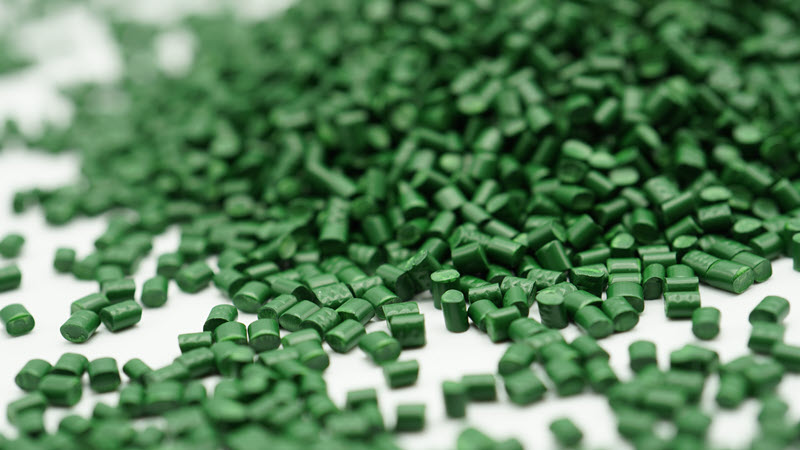
The importance of plastic to humanity is undisputed. Due to its light weight, ease of processing, low cost and outstanding features, plastic is used to manufacture many objects for human life.
However, plastic is also a double-edged sword, and you must have heard negative information about plastic all over the media. People are starting to tend to avoid plastic and look for more eco-friendly alternatives. One of them is bioplastic, which has exploded in popularity in recent years.
In this article, we will not reiterate the advantages or disadvantages of bioplastics, but instead let's dive into interesting facts and concepts about this material.
Related:
- Products made from recycled plastic bottles - 6 examples
- 25+ facts about recycling plastic bags
- What is American Milkman Model and how it could save the recycling industry?
- Potato starch bioplastic pros and cons - Top secret may surprise you
- Create a bioplastic business plan in 4 steps
1. Not all bioplastics are biodegradable
First of all, it is necessary to distinguish the concept of bioplastic and biodegradable plastic. As we all know, traditional plastics are made from petroleum, while bioplastics are made entirely (or partly) from polymers of biological origin.
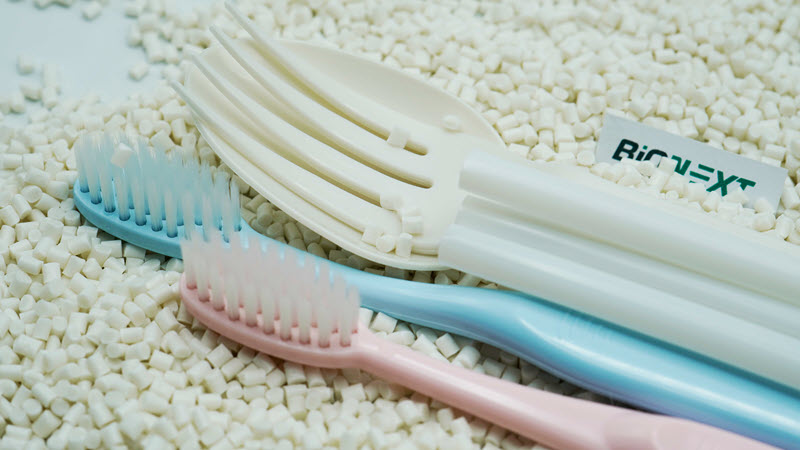
The term "bioplastic" can be understood in three cases:
- Bio-based plastic: Plastics are made entirely (or partly) from biological substances. For example, many of the plastic bottles we use every day are made from PET. This plastic is synthesized from fossil fuel sources and some plants such as sugar cane or corn starch. This is obviously bioplastic, but it won't be biodegradable.
- Biodegradable plastic: Plastic is completely biodegradable by microorganisms within a certain period of time.
- Biodegradable bioplastic: This is a plastic derived from plant-based materials and at the same time has the ability to biodegrade within a certain period of time.
So keep in mind that not all bioplastics are biodegradable and vice versa. When selecting the materials for the finished product, make sure the supplier is giving you the right plastic for the intended use.
2. Types of degradability
2.1. OXO biodegradable bioplastic
First of all, we need to distinguish the concept of decay and biodegradation. Conventional fossil-derived plastics, when released into the environment, can only break down into smaller pieces, called microplastics. And OXO plastic works in a way that can decompose, but not biodegrade.
OXO is a plastic derived from fossil materials (eg PE, PP, ...) mixed with metal additives (OXO additives), making the structure easy to break and decay. In addition, to serve product marketing purposes, manufacturers also mix fossil-derived plastics (about 70%) with biological materials (starch, bark, ...) to advertise their products as if it made from bioplastic that can be biodegradable. However, in fact, these products are OXO plastics, they can only decompose into microplastics but not completely biodegrade.
Although microplastics are only small pieces, the molecular weight of microplastics is still too high to biodegrade, so they persist in the environment and cause negative effects.
2.2. Photo-biodegradable bioplastic
As the name implies, photo-degradable bioplastic is a type of plastic that can biodegrade when exposed to sunlight. The composition of photo-degradable bioplastics includes fossil-based plastics such as PP, PE, PET... and some additives that act as catalysts.
The degradation process of photo-degradable bioplastics consists of two steps:
- Decomposes into microplastics when exposed to sunlight
- Active catalysts weaken the polymer chains that lead to the biodegradation process.
Depending on the desired level of biodegradation, manufacturers will add different catalyst ratios for photo-degradable bioplastics.
2.3. Hydro-biodegradable bioplastic
Hydro-biodegradable bioplastic is a type of plastic that biodegrades when it meets water and CO2. The biodegradation time of Hydro-biodegradable bioplastics is generally shorter than that of OXO-biodegradable plastics.
The composition of hydro-biodegradable bioplastics includes petroleum-based plastics, biomaterials, or a blend of the two.
3. Common materials to make biodegradable plastic
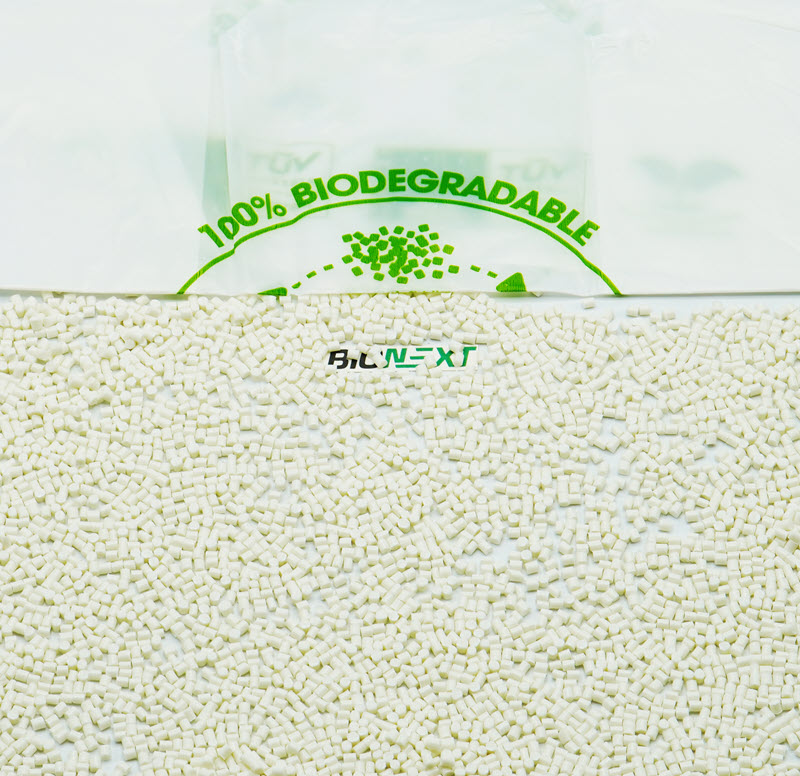
The types of materials used to create bioplastics include:
- PBAT (polybutylene adipate terephthalate)
- PBST (polybutylene succinate terephthalate)
- PLA (Polylactic acid)
- PBS (Polybutylene succinate)
- PCL (Polycaprolactone)
- PHA (Polyhyroxyalkanoate)
- TPS (Thermoplastic Starch)
Out of them, PLA and PBAT are the two most popular materials. We will learn about these two components shortly.
3.1. PLA
PLA or Polylactide (also known as Polylactic Acid, Lactic acid polymer) is a versatile commercial biodegradable thermoplastic based on lactic acid. Lactic acid monomers can be produced from 100% renewable resources, like corn and sugarbeets.
Polylactide has been able to replace conventional petroleum-based thermoplastics, thanks to the excellent combination of properties it possesses.
It is one of the most promising biopolymers used today and has a large number of applications such as the healthcare and medical industry, packaging, automotive applications, etc.
As compared to other biopolymers, PLA exhibits several benefits such as:
- Eco-friendly – It is renewably sourced, biodegradable, recyclable, and compostable
- Biocompatible – It is non-toxic
- Processability – It has better thermal processability compared to poly(hydroxyl alkanoate) (PHA), poly(ethylene glycol) (PEG) and poly(γ-caprolactone) (PCL)
Polylactides break down into nontoxic products during degradation and being biodegradable and biocompatible, reduce the amount of plastic waste.
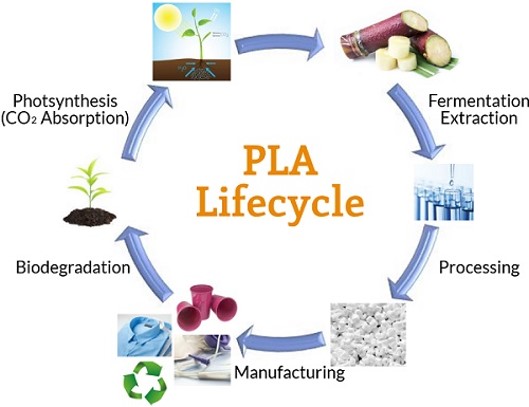
Most of the commercial L-PLA products are semi-crystalline polymers with a high melting point of ca. 180°C and their glass transition temperature in the range of 55 – 60°C, as it is desirable that PLA should have some crystalline content to benefit the quality of the finished product.
- PLA is a high-strength and high-modulus thermoplastic with a good appearance
- It has high stiffness and strength, comparable to polystyrene (PS) at room temperature
- Less energy is required in its production when compared to other plastics and has better thermal processing
However, there are still some disadvantages associated with the polymer:
- Its glass transition temperature is low (Tg ~ 55°C)
- Its poor ductility, low impact strength, and brittleness limit its use as compared to other thermoplastics such as ABS
- It has a low crystallization rate and processing results mainly in amorphous products
- As compared to PET (aromatic polyester), PLA is much more susceptible to chemical and biological hydrolysis
- It is thermally unstable and has poor gas barrier performance
- It has low flexibility and requires long mold cycles
- It is relatively hydrophobic
- It has a slow degradation rate
3.2. PBAT
PBAT (short for polybutylene adipate terephthalate) is a biodegradable random copolymer, specifically a copolyester of adipic acid, 1,4-butanediol, and terephthalic acid (from dimethyl terephthalate). PBAT is produced by many different manufacturers and may be known by the brand names ecoflex®, Wango, Ecoworld, Eastar Bio, and Origo-Bi. It is also called poly(butylene adipate-co-terephthalate) and sometimes poly butyrate-adipate-terephthalate(a misnomer) or even just "poly butyrate"
PBAT is classified as a random copolymer due to its random structure. This also means that it cannot crystallize to any significant degree due to the absence of any kind of structural order.
This leads to several physical properties:
- Wide melting point
- Low elastic modulus and stiffness
- High flexibility and toughness.
The flexibility and toughness of this polymer make it ideal for blending with another biodegradable polymer that is strong and rigid for bottle production.
4.Biodegradable plastic BiONext - the solution to optimize costs and improve the efficiency of finished products
BiONext is a biodegradable plastic product of EurPlas derived from environmentally friendly materials such as corn starch, potatoes, cassava, etc. This is an abundant source of raw materials in Vietnam and can be regenerated all year round.
Products made from BiONext will be biodegradable quickly through the composting process. The result of the decomposition process will produce water, carbon dioxide, and hummus. Currently, BiONext develops 3 main lines targeting three areas:
- BiONext 400 and 500 are raw materials for blowing biofilm, flexible packaging, with sufficient toughness and biodegradability.
- BiONext 152 targets the injection molding product segment to create biodegradable dental cups, spoons, forks, or toothpicks.
- BiOEXT125 is designed for the extrusion industry that produces biodegradable straws.
For more information and samples, please
contact EuroPlas’s consultant team today!