.jpg)
When it comes to plastic materials, polyvinyl chloride vs vinyl are two concepts that are often confused with each other. However, PVC is just one type of vinyl, and there are several other vinyl-based polymers with different properties and applications. Understanding the differences between these types of vinyl can be important when selecting the right material for your specific application. In this article, we will compare polyvinyl chloride vs vinyl, various types of vinyl, and discuss their unique properties and applications.
1. Is vinyl and PVC the same?
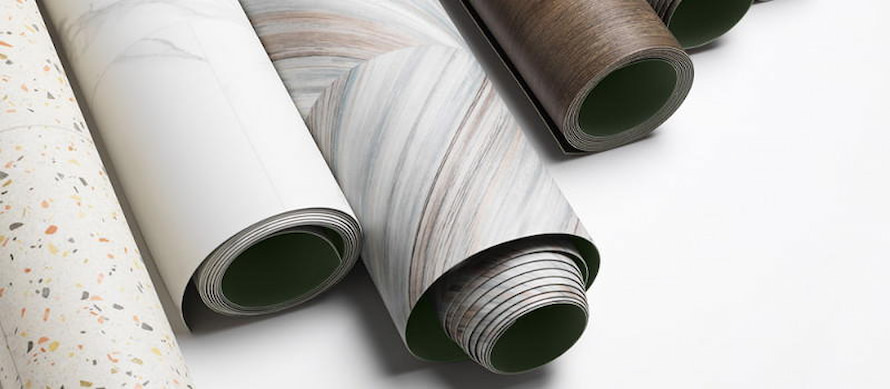
Polyvinyl Chloride (PVC) is a type of vinyl polymer that is made by polymerizing vinyl chloride monomers. It is a synthetic plastic polymer that is widely used in various applications, such as construction materials, electrical insulation, packaging, and medical devices. PVC is known for its versatility, durability, and cost-effectiveness.
In chemistry, however, the term “vinyl’ actually has a broader meaning, encompassing a range of different thermoplastic chemical compounds derived from ethylene and containing the vinyl group (-CH=CH2) in their chemical structure. The vinyl group is a double bond between two carbon atoms that gives vinyl polymers their unique properties. In addition to PVC, “vinyls” materials also include
- Ethylene vinyl acetate (EVA), which is a component of adhesives, films, and wire coatings.
- Polyethylene vinyl acetate (PEVA) is a copolymer of polyethylene and EVA used in shower curtains and body bags.
- Polyvinyl acetate (PVA), is typically found in paints and adhesives like white glue.
Polyvinyl butyral (PVB), is used in safety glass films.
What differentiates PVC from other vinyl is the addition of a chlorine molecule (the chloride “C” in PVC and PVDC). Much of the environmental health issues with PVC are caused by chlorine, including the production of dioxin, a highly carcinogenic compound, during both PVC production and disposal.
Therefore, PVC is a type of vinyl polymer, but not all vinyl polymers are PVC.
2. Other than PVC, are there any types of vinyl?
When it comes to vinyl, most people might immediately think of Polyvinyl Chloride (PVC) since it is one of the most widely used and known types of vinyl. However, as mentioned above, PVC is not the only type of vinyl polymer that exists. In fact, there are many other types of vinyl with unique properties and applications that make them suitable for different uses. In this part, we will explore other types of vinyl, highlighting their features and applications.
2.1. Polyvinylidene chloride
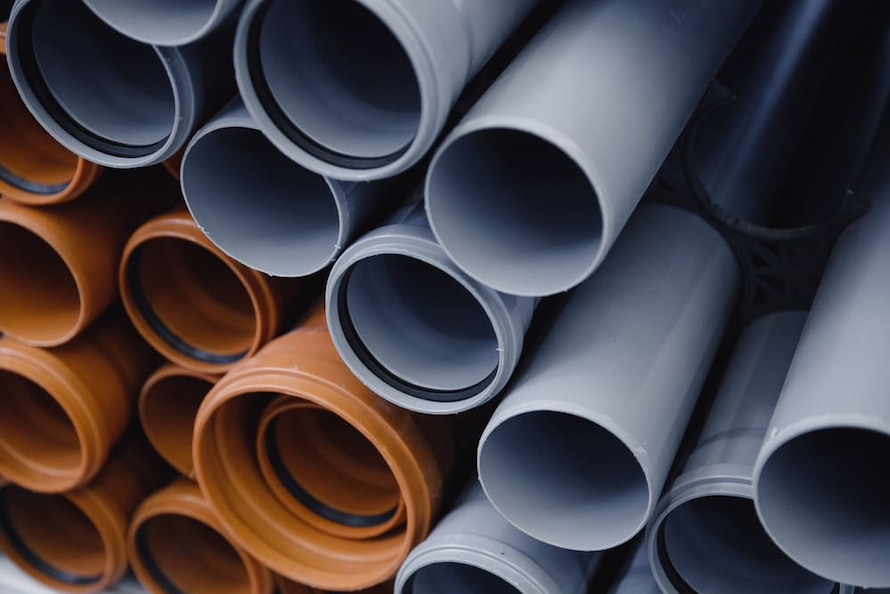
Definition: Polyvinylidene chloride, or polyvinylidene dichloride (PVDC), is a homopolymer of vinylidene chloride. PVDC is formed by polymerizing vinylidene chloride monomers, which results in a polymer with a high degree of crystallinity and good thermal stability.
Chemical formula: (C2H2Cl2)n, where n is the number of repeating units in the polymer chain.
Melting point: The melting point of Polyvinylidene Chloride (PVDC) is relatively high compared to other vinyl polymers, ranging from 190°C to 230°C (374°F to 446°F).
Properties: PVDC has several characteristics that make it unique and valuable for various applications.
- Barrier Properties: PVDC can prevent the penetration of gases, including oxygen, nitrogen, and carbon dioxide, as well as water vapor and aromas. This is due to its highly crystalline structure, which creates a dense and tightly packed barrier that blocks the movement of molecules through the material.
- Chemical Resistance: PVDC is highly resistant to a wide range of chemicals, including acids, alkalis, and organic solvents.
- Thermal Stability: PVDC has a high melting point of around 200°C, so it can withstand high temperatures without losing its mechanical properties.
- Weatherability: PVDC is highly resistant to ultraviolet radiation and weathering so it can maintain its appearance and mechanical properties even in harsh environmental conditions.
- Electrical Properties: PVDC is an excellent electrical insulator, with a low dielectric constant and low loss tangent.
- Easily Processing: PVDC is easy to process using a variety of methods, including extrusion, injection molding, and blow molding. Therefore, this material is a popular choice for manufacturing a wide range of products.
Application:
- Coating on paper, aluminum foil, or plastic films
- Packaging for pharmaceuticals, medical devices, and industrial chemicals.
- Electrical Insulation for wires and cables...
- Coating on textiles to provide protection against water, oils, and stains. It is also commonly used in the manufacturing of outdoor clothing and upholstery fabrics.
2.2. Polyvinyl acetate
.jpg)
Definition: Polyvinyl acetate (PVAc) is a synthetic polymer that is produced by the polymerization of vinyl acetate monomers. It is a white, odorless, and water-soluble thermoplastic polymer.
Chemical formula: The chemical formula for polyvinyl acetate is (C4H6O2)n, where n represents the degree of polymerization.
Melting point: The melting point of PVAc varies depending on the degree of polymerization. Typically, PVA has a melting point range between 160-210°C.
Properties:
- Solubility: PVAc is highly soluble in water, which makes it the proper material for water-based adhesives, coatings, and emulsions. It dissolves readily in cold water, forming a clear, colorless solution.
- Transparency: PVAc is a transparent polymer and its transparency can be improved by increasing the degree of polymerization or by adding plasticizers.
- Flexibility: PVAc can be easily molded into various shapes. It is also highly elastic, meaning it can be stretched and then return to its original shape.
- Low toxicity: PVAc is non-toxic and safe to handle so it is used in cosmetic products such as hair gels and nail polish, where safety is a key consideration.
- UV resistance: PVAc has good resistance to UV light and can withstand prolonged exposure to sunlight without yellowing or degrading.
Applications:
- Adhesives in woodworking, paper, and packaging, and textiles
- Coating in paper and textiles industries,
- Sizing agent to improve the stiffness of fabrics during weaving.
- Used in the production of emulsions, which are widely used in industries such as paints, coatings, and adhesives. PVAc emulsions are used as a binder in water-based coatings and adhesives.
- Used in shrink wrap and cling wrap thanks to its transparency and adhesive properties.
- Inggredient of hair gels, nail polish, and mascara due to its good adhesive properties and low toxicity.
2.3. Polyvinyl alcohol
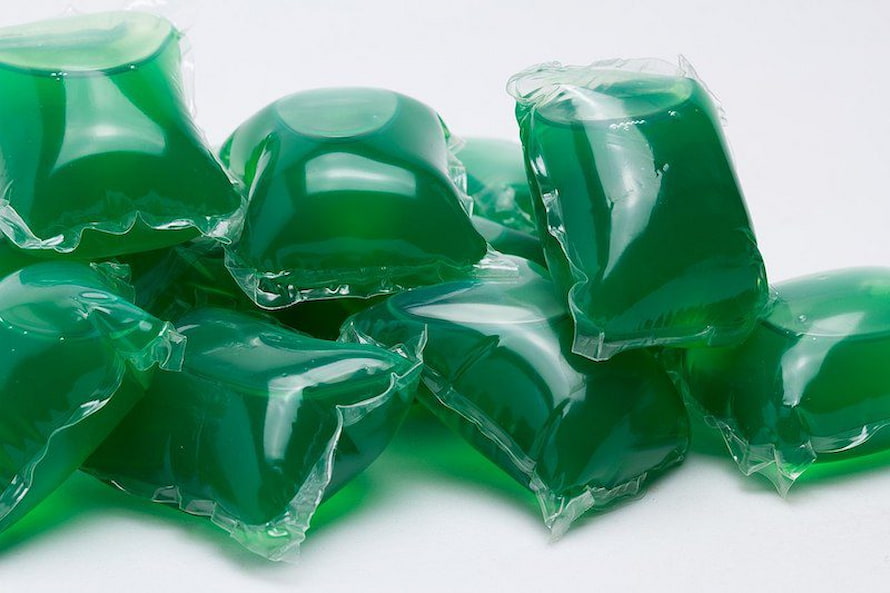
Definition: Polyvinyl alcohol (PVA) is a synthetic water-soluble polymer that is derived from the polymerization of vinyl acetate and subsequent hydrolysis of the resulting polymer. It is a versatile polymer that finds applications in a wide range of industries due to its unique properties.
Chemical formula: PVA is a polymer made up of repeating units of vinyl alcohol monomers. The chemical formula of PVA is (C2H4O)n, where n represents the degree of polymerization. The degree of polymerization can vary widely, ranging from 100 to 5000, depending on the desired properties of the final product.
Melting point: PVA typically does not have a distinct melting point, but rather begins to decompose at around 200°C (392°F). The decomposition temperature of PVA can be increased by incorporating crosslinking agents into the polymer structure.
Properties:
- Water solubility: PVA is highly soluble in water. It can be dissolved in some organic solvents, including alcohols, glycols, and glycerol.
- Film-forming ability: PVA can form a thin, transparent film when it is dissolved in water or other solvents and then dried. These films have good tensile strength and flexibility and are commonly used in packaging applications.
- Barrier properties: PVA films have good barrier properties against gasses and aromas. They can also act as a barrier against moisture and water.
- Biodegradability: PVA is biodegradable, meaning it can be broken down by microorganisms into simpler compounds.
- Chemical resistance: PVA is resistant to most organic solvents, oils, and greases, hence becoming preferred in applications where chemical resistance is required
- Thermal stability: PVA is relatively stable at room temperature, but begins to decompose at around 200°C. Its thermal stability can be improved by incorporating crosslinking agents into the polymer structure.
Applications:
- Used in the medical industry as a wound dressing and as a drug delivery system due to its biocompatibility and water solubility.
- Adhesives, caulks, and sealants are common household repair products that contain PVA.
- Used to improve the distribution of active chemicals in a variety of skincare products, such as moisturizers and cleansers. Also, it has a binding effect on hair color and peel-off masks, and it strengthens the adhesion of tight-grip cosmetics.
- Used to make a variety of biomedical products, including surgical threads, contact lenses, wound dressing, and artificial organs.
In short, while PVC is the most well-known and widely used type of vinyl, it is not the only one. In fact, each type of vinyl has its own unique properties and applications. By understanding the differences between polyvinyl chloride vs vinyl as well as various types of vinyl, we can make more informed decisions on our material selection.