Polypropylene (PP) woven bags are widely used for packing a variety of products, ranging from food items to industrial goods. These bags are made through a series of steps, starting with the preparation of raw materials and ending with printing and packing. The process is efficient and cost-effective, making PP woven bags a popular choice for packaging. In this blog, we will take a closer look at what PP woven bags are as well as each step involved in the PP woven bags manufacturing process.
Related:
- PP compound manufacturer - Ttop 10 world class companies
- HD, PP raffia troubleshooting
- Benefits of using PP calcium carbonate filler in PP woven
- 6 polypropylene compounds for automotive applications
I. PP woven bags
1. Defintion:
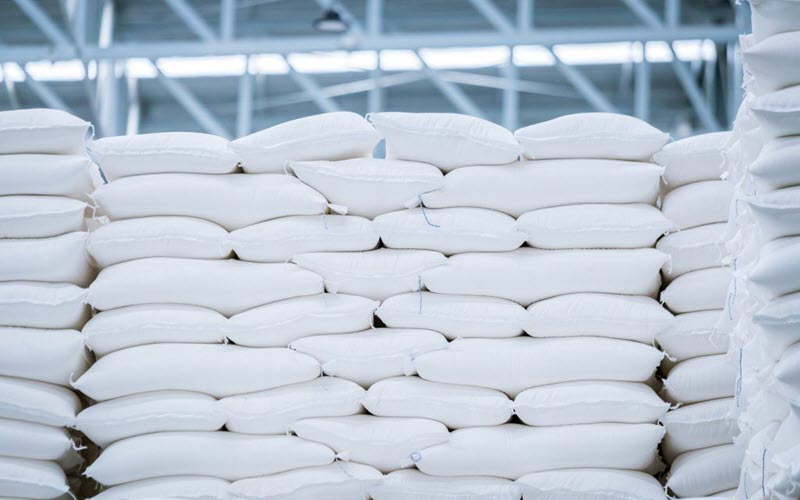
PP woven bags, also known as polypropylene woven bags, are a type of flexible packaging material made from woven fabric of polypropylene. The material is lightweight, durable, and flexible, making it an ideal choice for a wide range of aPPlications, including storage and transportation of food, agricultural products, chemicals, and other consumer goods. The bags can be customized to meet the specific requirements of each customer, including size, shape, color, and print.
2. Difference between PP woven bags and PP non-woven bags
PP woven bags and PP non-woven bags are two types of packaging materials made from polypropylene, a commonly used plastic material. While both types of bags have similar properties and aPPlications, there are some key differences between them:
- Manufacturing process: PP woven bags are made by weaving together polypropylene fibers to form a fabric. This process creates a tight interlocking weave that provides excellent strength and durability. The woven structure also helps to prevent moisture from penetrating the bag, making it ideal for storing and transporting heavy items and products that are sensitive to moisture. On the other hand, PP non-woven bags are made by bonding polypropylene fibers together using heat, pressure, or chemicals. This process creates a softer and more flexible fabric that is not as strong as a woven fabric.
- Physical structure: PP woven bags have a tight, interlocking weave that provides excellent strength and durability. The tight weave also makes the bag more resistant to tearing, puncturing, and other types of physical damage. In contrast, PP non-woven bags have a softer and more flexible structure that is not as strong as woven bags.
- Properties: PP woven bags are strong, durable, and moisture-resistant, making them suitable for storing and transporting heavy items and products that are sensitive to moisture. They are also resistant to UV light, which helps to extend the life of the bag and the products it contains. PP non-woven bags, while not as strong as woven bags, have the advantage of being softer and more flexible, making them easier to handle and less likely to cause damage to the products they contain.
- Cost: While PP woven bags tend to be more expensive than PP non-woven bags, the added durability and versatility make them a good investment for many aPPlications. However, for aPPlications that do not require a strong and durable bag, PP non-woven bags can be a more cost-effective option.
3. Benefits:
PP woven bags offer several advantages over other packaging materials, including:
- High strength and durability: The woven fabric of polypropylene provides excellent resistance to wear and tear, ensuring that the contents of the bags are protected during handling and transportation.
- Moisture resistance: PP woven bags are designed to resist moisture, making them ideal for storing and transporting food, agricultural products, and other items that are sensitive to moisture.
- Low cost: Compared to other packaging materials, PP woven bags are relatively inexpensive, making them an affordable option for a wide range of aPPlications.
- Environmentally friendly: PP woven bags are recyclable, which helps to reduce waste and protect the environment.
- Lightweight: PP woven bags are lightweight, making them easy to handle and transport.
- Customizable: PP woven bags can be customized to meet the specific requirements of each customer, including size, shape, color, and print.
- Resistant to UV rays: PP woven bags are resistant to UV rays, making them suitable for outdoor use and reducing the risk of the contents of the bags being damaged by exposure to sunlight.
- Long shelf life: PP woven bags have a long shelf life, which makes them a cost-effective solution for businesses that need to store products for an extended period of time.
- Easy to handle: PP woven bags are easy to handle and transport, which makes them convenient for use in a variety of applications.
4.Applications
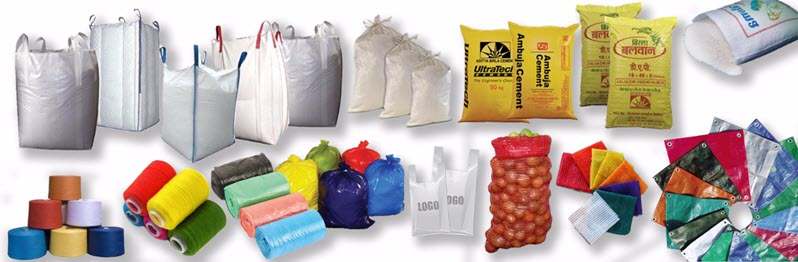
PP woven bags have a wide range of aPPlications in various industries, including:
- Agriculture: PP woven bags are used to store and transport various agricultural products, such as grain, feed, fertilizer, and seed.
- Food industry: These bags are ideal for packaging food products, as they are moisture-resistant and help to keep the food fresh for longer.
- Chemical industry: PP woven bags are used to store and transport chemicals, including hazardous materials, as they are strong and durable.
- Retail: PP woven bags are often used in retail stores for carrying items such as clothing, groceries, and other consumer goods.
- Industrial: The bags are used for storing and transporting industrial products, such as machinery parts, building materials, and other goods.
- Mining: PP woven bags are used in the mining industry for storing and transporting minerals and other materials.
- Recycling: These bags are ideal for use in the recycling industry, as they are recyclable and help to reduce waste.
Overall, PP woven bags offer a versatile, durable, and cost-effective solution for a wide range of aPPlications, making them an increasingly popular choice for businesses and consumers alike.
II. PP woven bags manufacturing process
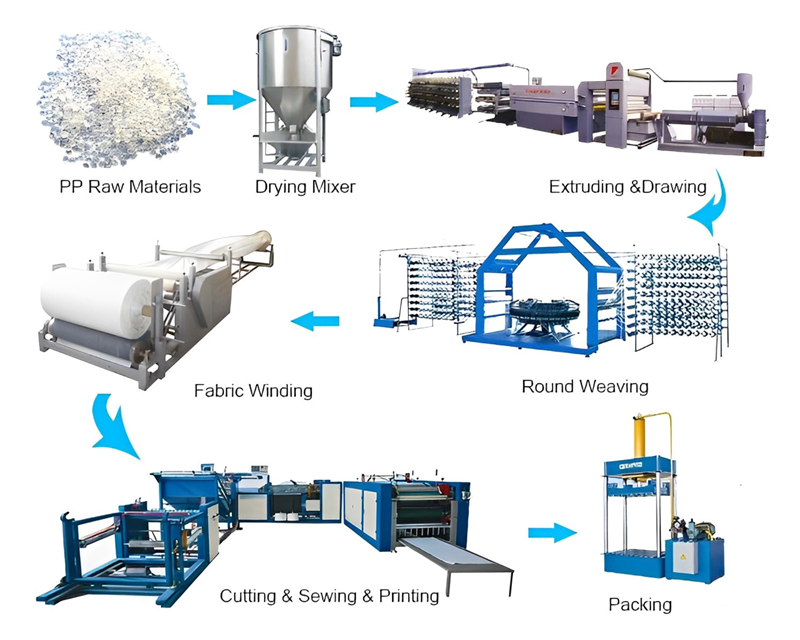
PP woven bags are a popular choice for packaging goods due to their strength, durability, and versatility. The PP woven bags manufacturing process is complex, and each step must be executed with care and precision to ensure the final product meets the highest quality standards.
1. Raw Material Preparation
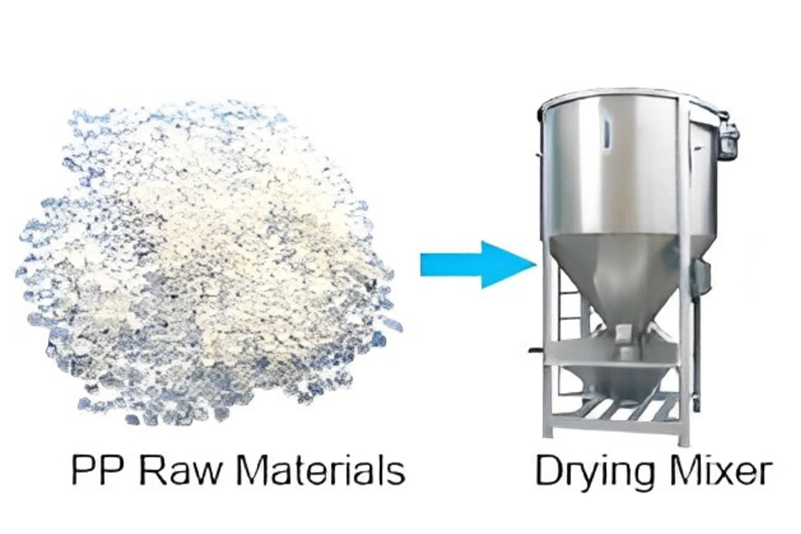
The production of PP woven bags starts with the preparation of the raw materials, which typically include high-quality polypropylene granules, color masterbatch, and other additives. The granules are melted and mixed together to form a homogenous mixture, which is then passed through an extruder to produce a continuous plastic film. The temperature, speed, and pressure of the extruder must be precisely controlled to ensure that the film is of the correct thickness and strength. The use of high-quality raw materials is essential for producing durable, strong bags that can withstand the weight of the contents and handling during transportation.
2. Extruding & Drawing
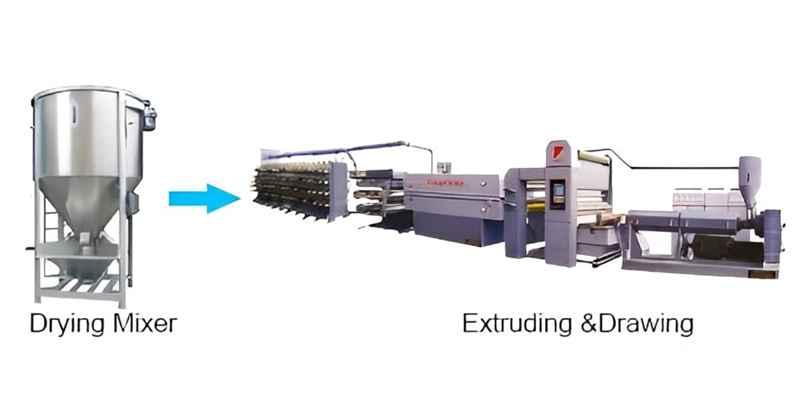
After the film has been produced, it is then extruded and drawn to increase its strength and stability. The film is extruded through a die, and the speed and pressure of the extruder are closely monitored to ensure that the film is of the correct thickness. The drawing process further increases the film's strength and stability, which is critical for ensuring the bags are strong enough to withstand the weight of the contents and handling during transportation.
3. Weaving
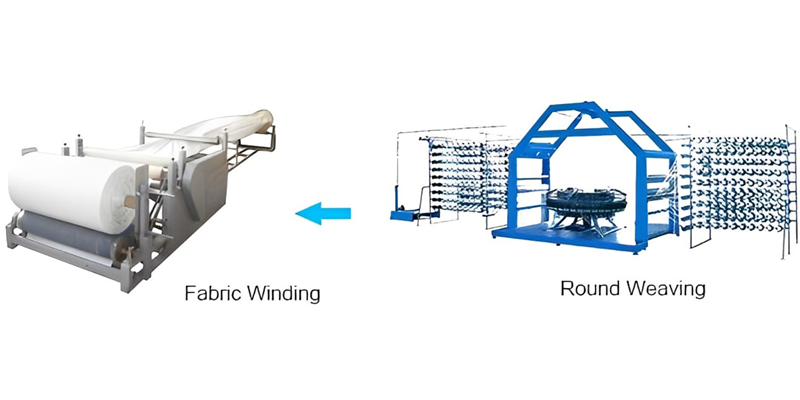
The next step is weaving the plastic film with a woven fabric, such as polypropylene, to create a laminated material. This process involves using high-speed weaving machines to interweave the film and fabric together, producing a strong and durable material suitable for making bags. The weaving process must be accurately controlled to ensure that the fabric and film are properly interwoven and that the final product is of the correct thickness and strength.
4. Winding
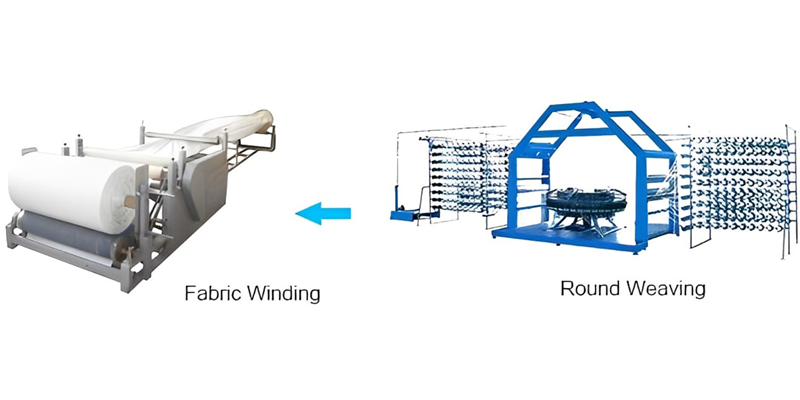
After the laminated material has been created, it is then wound onto a large spool for storage and protection. This step helps ensure that the material remains in good condition until it is needed for the next stage, and makes it easier to manage the material, reducing the risk of damage during transportation and storage.
5. Cutting & Sewing
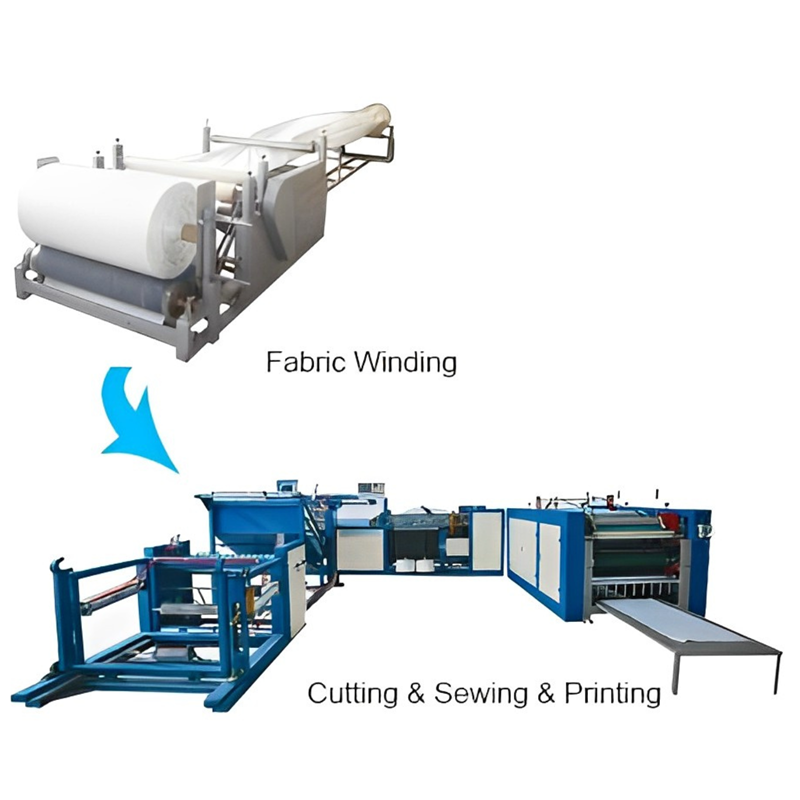
The laminated material is then cut into the desired size and shape, and the edges are sewn together to create the final bags. This step is usually performed using specialized cutting and sewing machines, which are equiPPed to handle heavy-duty materials and produce consistent results. The cutting and sewing process must be executed with care to ensure that the bags are of the correct size and shape, and that the seams are strong enough to withstand the weight of the contents and handling during transportation.
6. Printing
If desired, printing can be done on the bags using rotogravure or flexo printing methods. This printing can be done on one or both sides of the bags, and the customer chooses the design. Printing on the bags can include logos, branding, and other information that is useful for the customer or end-user. The printing process must be executed with care to ensure that the printing is of high quality, and that the colors are vibrant and accurate.
7. Inspection
The final bags are thoroughly inspected for any defects, ensuring that only high-quality products are sent to the customer. This step is critical in ensuring that the customer receives a product that meets their expectations and requirements, including the correct size, shape, color, and print, and is free of any defects or damages.
8. Packing
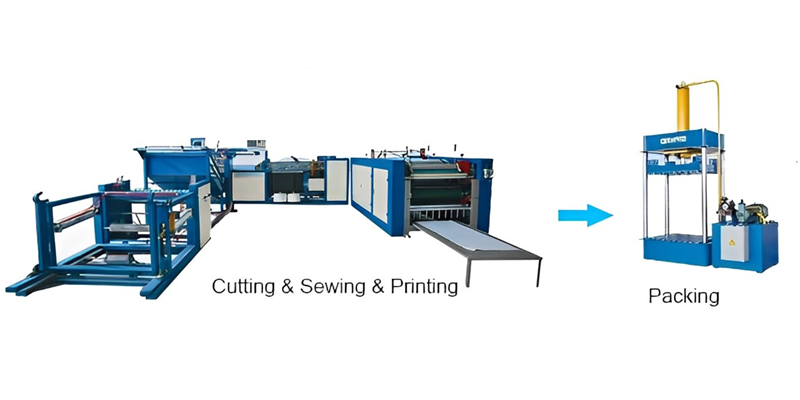
The final step is to carefully package the bags for shipment to the customer. The bags are packaged to ensure they reach the customer in perfect condition and minimize the risk of damage during transportation. The packaging process is critical in ensuring that the customer receives a high-quality product that meets their expectations and requirements.