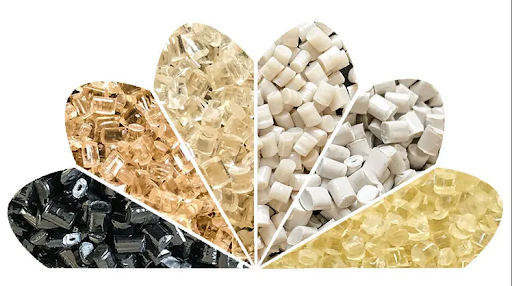
PPSU vs PSU both are reliable materials for a variety of industries
Overview, both PPSU vs PSU materials are reliable materials for a variety of industries from medical equipment, food and beverage industry and machinery equipment, etc. The main reason is thanks to its durability, flexibility and good heat resistance. However, each type of material also has unique characteristics that lead to it occupying different positions despite being in the same manufacturing industry. For example, PPSU plastic is preferred for products for pregnant women and infants while PSU plastic is suitable for implant applications. Right now, let's explore the separate aspects of PPSU vs PSU in this article to better understand the material properties and make a suitable choice for your upcoming project!
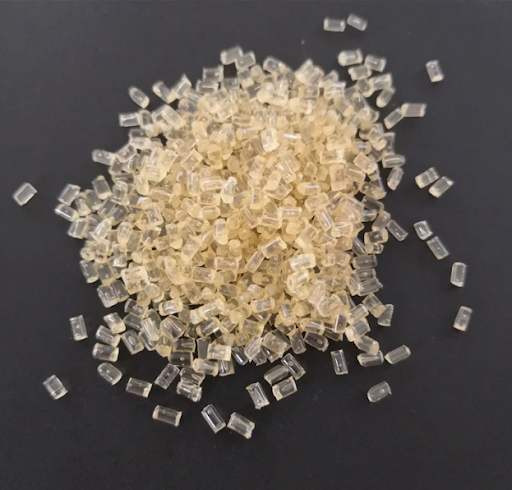
PPSU plastic is also known as Polyphenylsulfone
PPSU plastic is also known as Polyphenylsulfone. This type of material is considered the most advanced and safest on the material market today. PPSU plastic has been recognized by the US Food and Drug Safety Administration (FDA) as completely friendly to human health. In particular, PPSU plastic is confirmed to not contain BPA, so it is safe for consumers, especially infants and young children. Besides, PPSU plastic possesses a series of outstanding properties such as durability, light weight, hydrolysis resistance and good chemical resistance. The durability of PPSU plastic is also evaluated through two properties of impact resistance and heat resistance up to 150 - 180 degrees Celsius. This type of plastic is used in a variety of fields but is still a leading pioneer for products for newborns.
Read more: Polyphenylsulfone (PPSU): What is it?
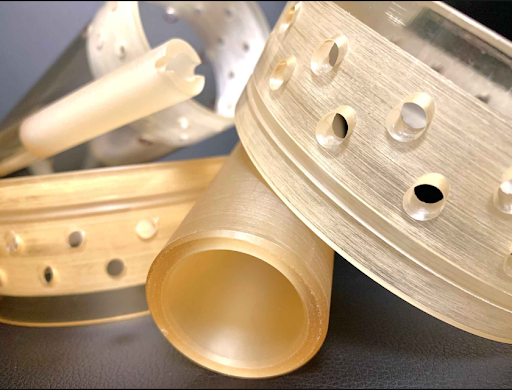
PSU plastic is also known as Polysulfone
PSU plastic, also known as Polysulfone, was invented by Union Carbide Corporation in the 1960s. To produce PSU plastic, people conduct a polymerization reaction between 4,4'-dichlorodiphenyl sulfone and bisphenol A. People proceed This process of heating the mixture results in a high-quality polymer. Polysulfone is separated from solution by adding an insoluble substance (e.g. water) leading to the precipitation of polysulfone as a powdery solid. Polysulfone continues to undergo final processing to create the shape of a material such as plastic pellets, plastic pellets or plastic films. In the early stages, this material was mainly used in the aerospace industry. Thanks to its outstanding properties, PSU plastic has gradually been widely used in many other manufacturing fields up to the present time.
Read more: What is Polysulfone? Definitions and applications
3. Properties comparison: PPSU vs PSU
3.1 Properties of PPSU plastic
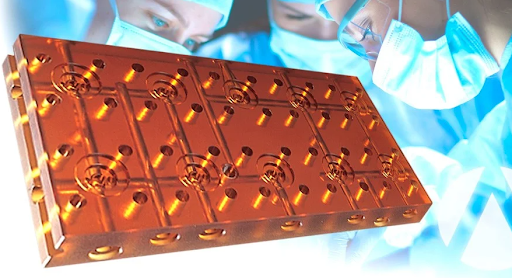
PPSU is very safety
As mentioned above, PPSU plastic has been recognized for its absolute safety by the US F.D.A. international organization. Unlike other materials, PPSU plastic does not release any harmful chemicals or compounds even when exposed to high temperature environments. Thanks to that, PPSU plastic is applied in the production of products for newborns and nursing mothers.
PPSU plastic is a material that will not easily crack or crumble. Thanks to its excellent hardness and flexibility, PPSU plastic gives the product impact resistance in cases of drops and strong impacts. Thanks to this feature, consumers can be completely assured about the product's longevity and save a large part of the cost of replacing new appliances.
-
Heat resistance and thermal conductivity
Heat resistance and thermal conductivity give PPSU plastic an advantage in the materials industry. When exposed to high temperature environments, PPSU plastic is not recorded to release any substances harmful to human health. We can easily see milk bottles made from PPSU plastic that can be put in a microwave to heat up. Besides, heating and cooling products contained in products made from PPSU plastic will also become easier thanks to its extremely good thermal conductivity.
One of the reasons why PPSU plastic is trusted even for newborns is largely thanks to this property. The situation of milk bottles, water bottles, and containers being dirty and smelly even after cleaning will no longer occur. Anti-fouling helps products made from PPSU plastic minimize unpleasant odors and bacteria accumulation from food particles stuck on the walls of the product.
The transparency of PPSU plastic is on par with glass material, giving the product a desirable aesthetic. In addition, PPSU plastic can easily create smooth product surfaces that limit scratches caused by external impacts. Thanks to that, products made from PPSU plastic possess transparency and durability even after long periods of us
3.2 Properties of PSU plastic
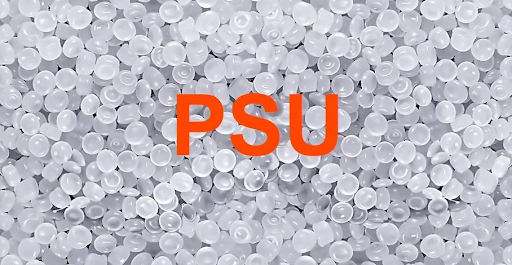
PSU plastic possesses the ability to heat resistance
-
High temperature resistance
The ability to withstand temperatures up to 180°C (356°F) for long-term use and 250°C (482°F) for short exposure times has helped PSU plastic be considered to possess the ability to heat resistance. Manufacturing industries such as aerospace, medical equipment, and automobiles have very effectively taken advantage of this characteristic of PSU plastic.
-
Chemical resistance and safety
PSU plastic has the ability to operate well in chemical environments such as bases, acids, oil solvents, etc. It is this characteristic that has helped PSU plastic occupy a position in the medical and pharmaceutical industry, chemical industry and food and beverage industry. In addition, PSU plastic is known to be safe for the human body, so it is also used in medical implants.
Applications that require high flexibility and durability, with little damage due to external impacts, should consider choosing PSU plastic. This material possesses ideal impact and abrasion resistance. Additionally, PSU plastic is quite lightweight providing an ideal weight for applications requiring weight savings.
PSU plastic has transparent properties that are very suitable for the production of items that require clear visibility such as medical equipment, containers for materials, chemicals, etc.
Thanks to these two characteristics of PSU plastic, they are becoming increasingly popular in applications that require fire safety and some electrical and electronic construction projects.
4. Application comparison: PPSU vs PSU
4.1 Application of PPSU plastic
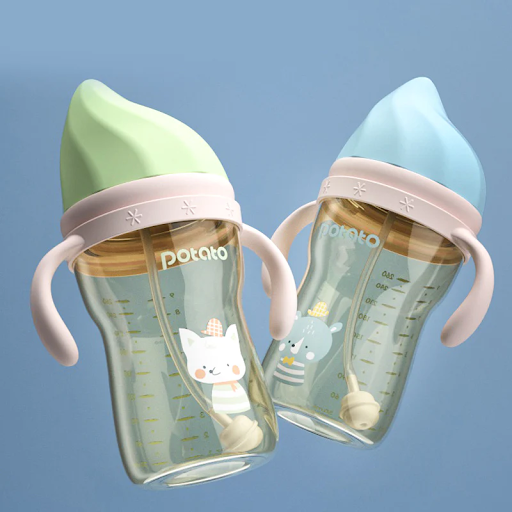
PPSU plastic is recognized as BPA-free
PPSU plastic is recognized as BPA-free, which is one of the top criteria for designs for babies. Milk bottles made from PPSU plastic are also noted to not release any toxic substances while storing milk for children, even when heating milk in a microwave. This is the ideal choice for a non-toxic, lead-free solution that is completely safe for babies when using milk bottles
PPSU plastic applications can be easily found in medical equipment such as surgical instruments, endoscopic equipment, pacemakers, dental trays, anesthesia equipment, containers and trays, etc. Items made from PPSU plastic are safe for human health and easy to clean thanks to their stain resistance.
You will easily find PPSU plastic in products around your home such as water bottles, microwaves, coffee filters and some items that require heat resistance and are safe for the user's health.
-
Departments in manufacturing industry
PPSU plastic is always the ideal choice for machine parts that require good temperature resistance, long life, electrical insulation and low wear.
PPSU plastic is favored in aircraft cabin interiors thanks to its low smoke-generating properties and low toxic emissions into the environment despite exposure to high temperatures.
Besides, the lightweight properties of PPSU plastic help save weight for the aircraft, thereby saving fuel. Not only that, PPSU plastic provides aircraft design with good flexibility and impact resistance, ensuring safety in harsh aviation environments.
4.2 Application of PSU plastic
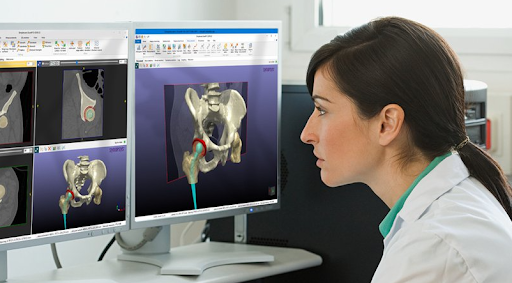
PSU plastic application for medical implant
Medical devices commonly made from PSU plastic include surgical instruments and diagnostic equipment, artificial joints, dental implants, pacemakers, dialysis equipment, test tubes, and tubes. centrifuge and Petri dish. The reason PSU plastics are trusted for medical use is because they have antibacterial properties and good biocompatibility, are transparent and safe for the human body.
-
Aerospace and automobile components
PSU plastic is quite hard and can withstand extreme temperatures to meet the requirements for aircraft or car engine design. In addition, with its lightweight, PSU plastic helps the device save most of the weight of the machine. Applications can be easily found such as bumpers, headlights, windows, interior panels, wiring insulation, turbochargers etc.
PSU plastic designs in the world of electronic components can include electrical connectors, semiconductor encapsulation, printed circuits, etc. PSU plastic helps components operate smoothly, resist heat and fire.
-
Food and beverage processing equipment
Equipment that can be named as transporters, packaging machines, mixers, etc. These are devices that require safety for human health and long machine life. In addition, PSU plastic is also used to make bottling machines, canning machines and beer barrels thanks to its remarkable chemical resistance.
PSU resin is an ideal material for the process of removing impurities such as bacteria, debris and heavy metals from water. Applications include urban, industrial and civil water treatment equipment.
5. Conclusion
In general, PPSU vs PSU plastics are ideal materials for applications that require durability and safety for human health. Currently, both PPSU and PSU plastics are widely used in a variety of industries. Choosing the right material requires manufacturers to consider the properties of each material and the requirements of the product being targeted. Read more useful articles from our EuroPlas today. EuroPlas is always proud to be a reliable companion for your upcoming project!