PVDF plastic, or polyvinylidene fluoride, is a high-performance polymer known for its strength, chemical resistance, and thermal stability. Essential in industries like electronics, pharmaceuticals, and construction, it withstands harsh environments while maintaining integrity. This article explores the definitions, properties, and diverse applications of PVDF plastic, underscoring its importance in modern manufacturing and innovation.
Read more: What is so special about PVDF material?
1. Definitions of PVDF Plastic
Polyvinylidene fluoride (PVDF), also known as polyvinylidene difluoride (PVF2), is a semi-crystalline thermoplastic fluoropolymer distinguished by its high purity and impressive service temperatures of up to 150°C. The polymer structure features alternating CH2 and CF2 groups, which contribute to its unique properties, including insolubility and exceptional electrical characteristics.
As the second most widely produced fluoropolymer after PTFE, PVDF is renowned for its outstanding combination of mechanical strength, chemical resistance, and processability. It is available commercially in various melt flow rates and can be enhanced with a range of additives to optimize processing and end-use performance. This versatility makes PVDF an indispensable material across diverse industrial applications.
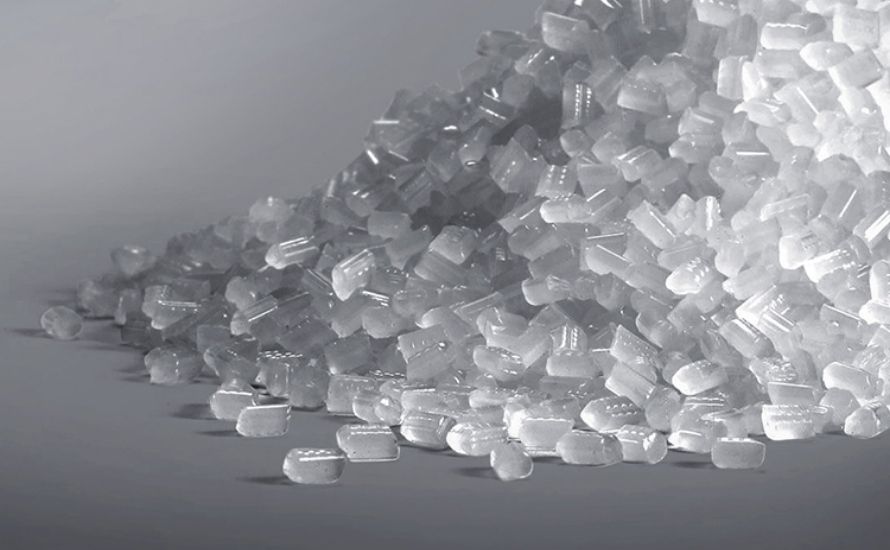
2. About PVDF Plastic’s Properties
PVDF is a highly versatile polymer, renowned for its exceptional properties that make it ideal for a wide range of applications. Below are some of the key properties that define PVDF:
Chemical Resistance: PVDF exhibits outstanding resistance to a broad spectrum of chemicals, acids, and solvents, making it an excellent choice for environments where exposure to corrosive substances is prevalent.
- Thermal Stability: With a high melting point and remarkable thermal stability, PVDF maintains its integrity and performance even at elevated temperatures, positioning it as a reliable material for high-temperature applications.
- Electrical Insulation: Known for its superior electrical insulation properties, PVDF is frequently employed in electrical and electronic applications that demand exceptional insulation performance.
- Mechanical Strength: PVDF Plastic boasts impressive mechanical strength and toughness, enabling it to endure significant mechanical stresses and impacts, thus making it suitable for applications requiring durable materials.
- UV Resistance: This polymer exhibits good resistance to ultraviolet (UV) radiation, rendering it suitable for outdoor applications where prolonged exposure to sunlight is a concern.
- Weather Resistance: PVDF is resilient against weathering effects, including rain, snow, and atmospheric pollutants, enhancing its suitability for outdoor environments.
- Low Density: With a relatively low density, PVDF is lightweight, a beneficial characteristic for applications where minimizing weight is crucial.
- Piezoelectricity: PVDF possesses piezoelectric properties, allowing it to generate an electric charge in response to mechanical stress. This feature is effectively utilized in sensors, actuators, and various electronic devices.
- Transparency: The polymer is transparent to certain wavelengths of radiation, particularly in the infrared spectrum, making it advantageous for specific optical applications.
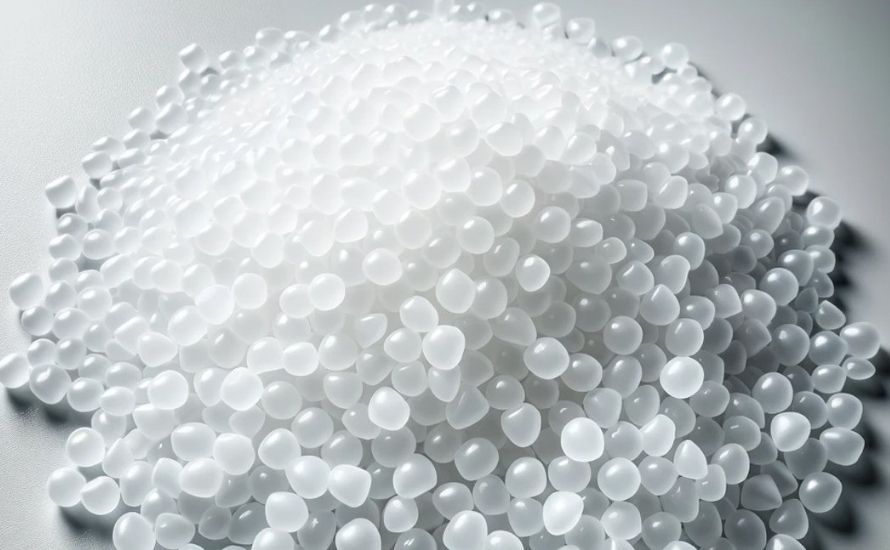
3. PVDF Plastic: Pros & Cons
Below, we explore the pros and cons of PVDF to provide a comprehensive understanding of its suitability for various applications.
3.1 Advantages
- Exceptional Tensile Strength: PVDF boasts the highest tensile strength among all processable fluorocarbons, making it an ideal choice for demanding applications requiring robust materials.
- Radiation Resistance: This polymer exhibits superior resistance to radiation compared to other fluorocarbons, enhancing its reliability in environments where exposure to radiation is a concern.
- Melt Processability: PVDF can be easily melt-processed, allowing for versatile manufacturing techniques and facilitating its use in a wide array of applications.
- Abrasion Resistance: The material demonstrates excellent abrasion resistance, ensuring durability and longevity in applications subject to wear and tear.
- Chemical Resistance: While not as chemically resistant as PTFE, PVDF still offers good general chemical resistance, making it suitable for various industrial environments.
- High Maximum Use Temperature: PVDF can withstand temperatures up to 150°C (300°F), making it suitable for high-temperature applications without compromising its structural integrity.
- Useful Piezoelectric Properties: The piezoelectric characteristics of PVDF allow it to generate an electric charge in response to mechanical stress, making it valuable in sensors and actuators.
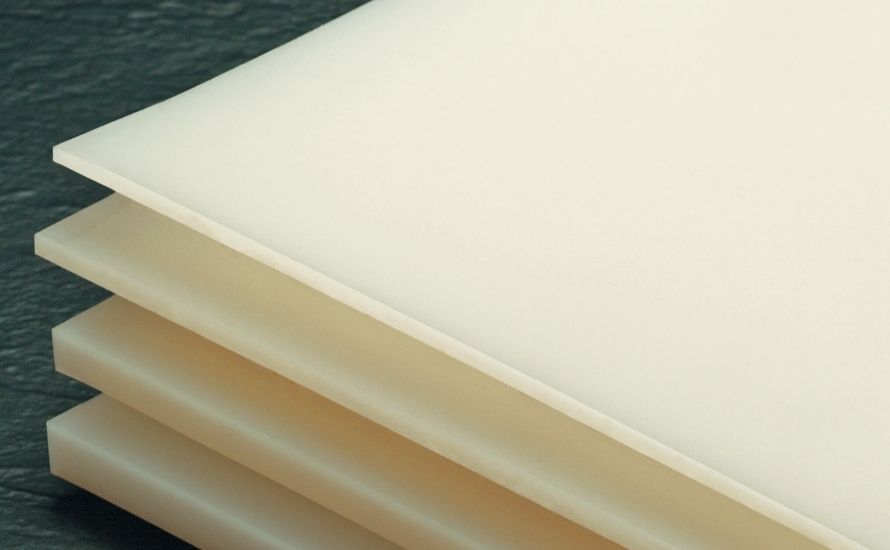
3.2 Disadvantages
- High Dissipation Factor: PVDF has a relatively high dissipation factor, which can lead to energy loss in certain applications, potentially limiting its effectiveness.
- Clean Processing Requirements: The processing machinery for PVDF must be exceptionally clean to avoid contamination, which can complicate manufacturing processes.
- Reinforcement Limitations: PVDF typically cannot be reinforced with glass fibers due to decomposition issues initiated by boron, restricting its enhancement options.
- Poor Resistance to Fuming Acids: The material exhibits inadequate resistance to fuming acids, which can limit its applicability in environments where such conditions are present.
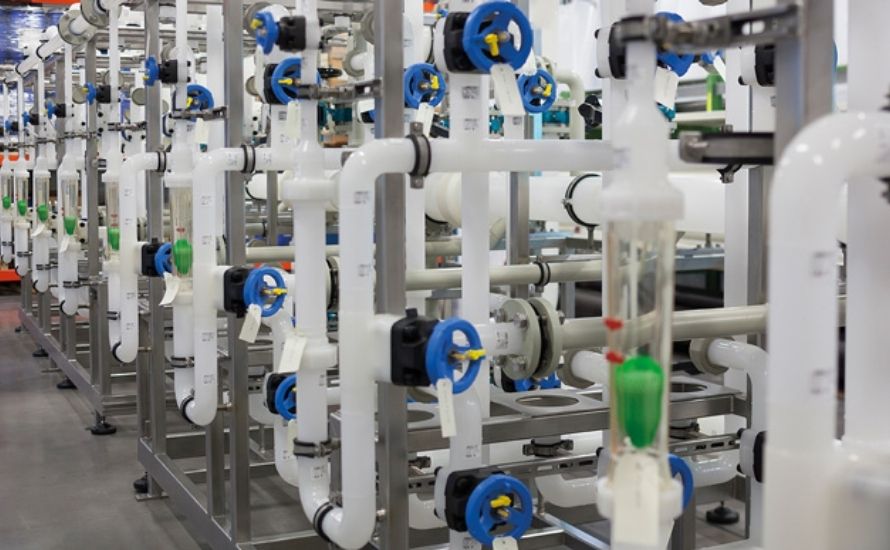
In conclusion, PVDF Plastic presents a compelling mix of advantages that make it a preferred choice in various industries, despite its limitations. Understanding these pros and cons is essential for making informed decisions when selecting materials for specific applications.
4. Applications Of PVDF Plastic
PVDF Plastic stands out as a highly adaptable polymer, renowned for its impressive characteristics that have led to its extensive implementation across numerous sectors. Below, we explore several significant applications where PVDF proves to be invaluable, showcasing its versatility and effectiveness in meeting industry demands.
- Chemical Processing Industry: Thanks to its superior chemical resistance, PVDF is the material of choice for manufacturing pipes, fittings, valves, tanks, and other equipment utilized in the chemical processing sector. It effectively withstands aggressive chemicals, ensuring long-term integrity and reliability in demanding environments.
- Electrical Industry: PVDF's excellent electrical insulation properties and high-temperature resistance make it indispensable in the electrical industry. It is widely employed for cable insulation, wire coatings, connectors, and encapsulation materials for circuit boards, where effective control of electrical conductivity is paramount.
- Water Treatment Systems: The chemical resistance and durability of PVDF under harsh environmental conditions render it ideal for water treatment systems. It is extensively used in pipes, filters, membranes, and other critical components. Notably, PVDF membranes are integral to reverse osmosis desalination plants, where they efficiently retain ions during the filtration process.
- Architectural Coatings: PVDF coatings are favored in architectural applications due to their exceptional weatherability and UV resistance. These coatings are applied to facades, cladding, roofing, and other external surfaces of buildings, providing long-lasting protection against corrosion, fading, and degradation.
- Medical Industry: In the medical field, PVDF is extensively utilized to manufacture vital components such as catheters, surgical instruments, implants, dialysis membranes, and drug delivery systems. Its biocompatibility and resilience to sterilization methods make it an ideal material for a wide range of medical devices.
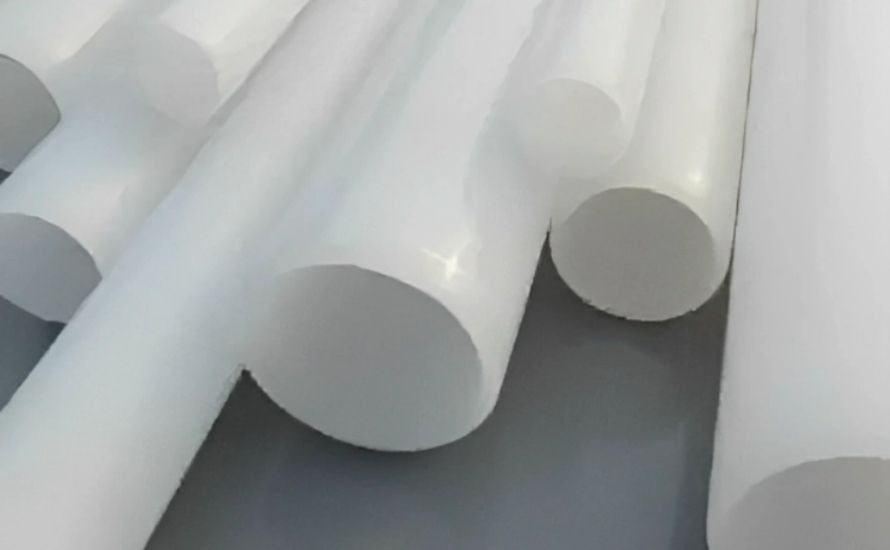
5. Conclusion
In conclusion, PVDF Plastic is a highly versatile polymer with a broad range of applications and significant advantages. Its exceptional properties - chemical resistance, thermal stability, mechanical strength, and UV resilience - make it essential across industries such as aerospace, automotive, electronics, and construction. PVDF's ability to endure harsh environments enhances operational efficiency and supports sustainable practices. With adaptable production methods, it offers customized solutions, solidifying its role as a key driver of innovation in modern engineering.
6. About EuroPlas
If you are looking for a reliable supplier of high-quality plastics, look no further than
EuroPlas. We take pride in offering top-notch products and cost-effective plastic materials, produced on advanced technology lines with modern equipment such as extrusion machines, blowing machines, and injection molding machines. Our standard measuring systems, including thermal deformation testers, impact resistance testers, and tensile strength testers, ensure that every product delivered to our customers meets the highest quality standards. Our diverse product range includes additives, bio fillers, and bioplastics, designed to meet the varied needs of your industry.
.jpg)
To explore how our innovative solutions can enhance your projects, don’t hesitate to contact us today. Connect with our team for a detailed discussion about our offerings, or dive into the latest insights on the plastics industry by visiting our blog. Let EuroPlas be your trusted partner in achieving excellence in every application!