Single-stage vs. Two-stage Blow Moulding: Choose Which One?
Blow moulding is a critical manufacturing process in producing hollow plastic parts and containers. With numerous applications in industries ranging from automotive to packaging, choosing the right blow moulding method is vital for efficiency and product quality. In this article, we will explore the two main types of blow moulding: single-stage and two-stage. We'll compare their processes, advantages, and disadvantages, and help you decide which method is best for your needs.
1. Definition of Single-stage and Two-stage Blow Moulding
Blow moulding can be categorized into two primary methods: single-stage and two-stage. Each method has distinct characteristics and applications:
Single-stage Blow Moulding: In single-stage blow moulding, the entire process from raw material to finished product occurs in a single, continuous operation. This method is often used for manufacturing smaller quantities of high-precision products.
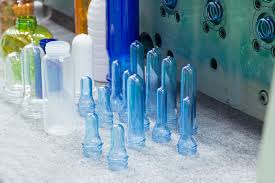
Definition of Single-stage.
Two-stage Blow Moulding: Two-stage blow moulding separates the process into two distinct stages. The first stage involves creating preforms or parisons, which are later reheated and blown into the final shape in the second stage. This method is commonly used for large-scale production of bottles and containers.
.jpg)
Definition of two-stage.
2. How Do Single-stage and Two-stage Blow Moulding Work?
Understanding the operational differences between these two methods is crucial:
Process Step |
Single-stage Blow Moulding |
Two-stage Blow Moulding |
Injection Moulding |
Plastic resin is heated and injected into a mould to form a preform or parison. |
Plastic resin is heated and injected into a mould to create preforms or parisons.
|
Blow Moulding |
The preform is immediately transferred to the blow moulding station where it is inflated to take the shape of the final product. |
Preforms are reheated to the optimal temperature for blow moulding. Blow Moulding: The reheated preforms are placed into blow moulds and inflated to form the final product. |
Cooling |
The moulded product is cooled and ejected from the mould. |
The finished product is cooled and removed from the mould. |
Storage (if applicable) |
Not applicable (immediate transition to blow moulding) |
The preforms are stored and can be transported to a different location for the second stage. |
3. Advantages and Disadvantages Of These Two Blow Moulding Ways
Here's a quick comparison of the advantages and disadvantages of single-stage and two-stage blow moulding:
Aspect |
Single-stage Blow Moulding |
Two-stage Blow Moulding |
Efficiency |
High, due to continuous process |
Moderate, due to separate stages |
Precision |
Excellent for high-precision products |
Good, but can vary |
Production Volume |
Suitable for small to medium batches |
Ideal for large-scale production |
Equipment Cost |
Higher initial investment |
Lower initial investment |
Flexibility |
Limited, best for specific product types |
High, adaptable for various product sizes |
Material Usage |
Efficient use of materials |
Can result in more material waste |
Turnaround Time |
Faster due to single operation |
Slower due to reheating and separate stages |
4. Which Blow Moulding Way Should You Choose?
Choosing the right blow moulding method depends on various factors such as production volume, product precision, and investment capacity:
Choose Single-stage Blow Moulding if:
- You require high-precision products.
- You have a smaller production volume.
- You prefer a faster production process with less material waste.
Choose Two-stage Blow Moulding if:
- You are producing large volumes of products, such as bottles or containers.
- You need flexibility in product size and design.
- You have a lower initial budget for equipment investment.
- Which blow moulding method should you choose?
Both methods have their unique advantages and are suitable for different manufacturing needs. Assessing your specific requirements will help you make an informed decision.
5. Conclusion
In the world of plastic manufacturing, choosing between single-stage and two-stage blow moulding is crucial for optimizing production efficiency and product quality. Single-stage blow moulding offers high precision and efficiency for smaller batches, while two-stage blow moulding is ideal for large-scale production with flexible design options. By understanding the differences and evaluating your specific needs, you can select the most suitable blow moulding method for your business.
6. About EuroPlas
EuroPlas is a leading provider of plastic additives, offering a wide range of products including odor absorbers, desiccants, flame retardants, anti-fog agents, anti-aging agents, processing aids, anti-static agents, UV stabilizers, and optical brighteners. Our experts at EuroPlas can help you select the right type and dosage of additives to meet your specific production requirements. Whether you choose single-stage or two-stage blow moulding, our additives can enhance the quality and performance of your final products. Contact EuroPlas today and visit our blog for the latest updates on plastics and advanced manufacturing solutions.