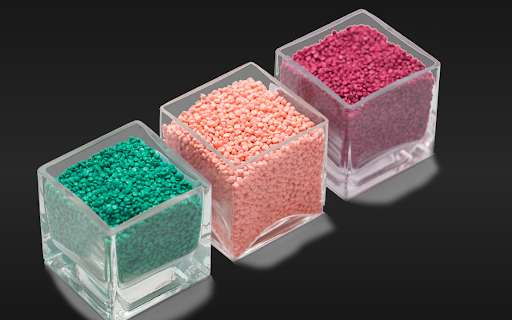
PP compounds hold an important position in manufacturing industries
Known for its many outstanding advantages, PP compounds plastic hold an important position in many manufacturing industries today. The demand for producing products from PP compounds is increasing from many fields such as automobiles, aerospace, civil water supply systems, resource exploitation systems, and even in the medical industry. Choosing a suitable production method for Polypropylene compounds is also one of the ways to optimize the economic efficiency of the business and avoid wasting resources. Among the countless methods of producing plastic products, extrusion is one of the bright candidates to create plastic products in general and PP compounds in particular. The following article will help you update more useful information in considering the extrusion process for your future PP compound plastic project.
1.1 Definition
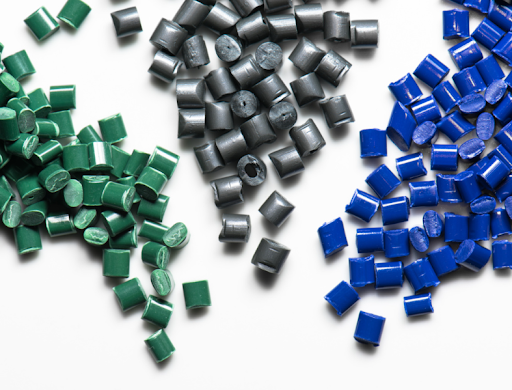
PP compound has become the top choice in automotive technology
Compound PP plastic (polypropylene) is understood as a technical plastic material that is combined from the base material (PP plastic) and appropriate enhancers or additives (carbon, glass beads, etc.) according to each formula to produce a new innovative material. Based on production needs, investors can process PP plastic compounds according to many different formulas to improve the inherent properties of PP plastic. Those properties can be mentioned as harder, more durable, better chemical resistance, better heat resistance, etc. depending on the additives added to the virgin PP substrate. Thanks to improved properties through blending, PP compound has become the top choice in manufacturing industries such as automotive technology, aerospace, water supply systems, road systems, and raw material pipeline.
Read more: 6 polypropylene compounds for automotive applications
1.2 Types of PP compound
There are many types of PP compounds on the market today. Depending on production needs, investors can choose PP compounds with appropriate features. Types of PP compounds can be listed as follows:
In this compound, Pp plastic beads will act as the substrate and carbon black will act as the reinforcing agent. This process helps increase the hardness, toughness, impact resistance and elasticity of the new material. In particular, in this PP compound, electrical conductivity will be significantly improved to reduce cases of static electricity in machines.
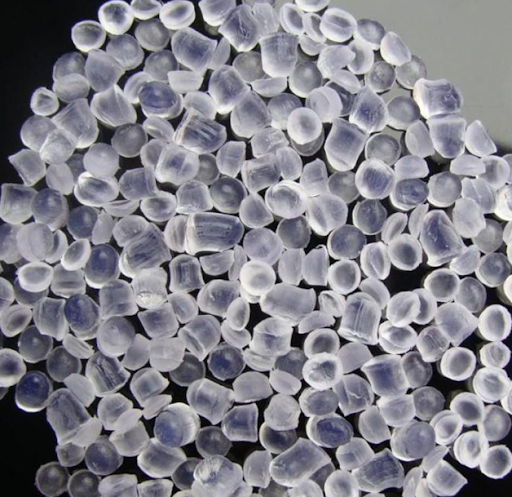
PP plastic will be mixed with glass fiber
In this substance, PP plastic will be mixed with glass fiber and some other additives to help balance the combination process. This is an extremely popular form in the materials industry. It helps PP compounds enhance some properties such as reducing shrinkage, increasing strength, resisting strong impacts from outside, and being more durable. This is a very popular material line in the extrusion process to shape products.
Glass fiber and glass beads are two easily confused concepts in PP compounds. In addition to glass fibers, glass beads are also used as reinforcement for PP plastic substrates. This combination gives the material significant improvements in thermal stability, mechanical stress, etc.
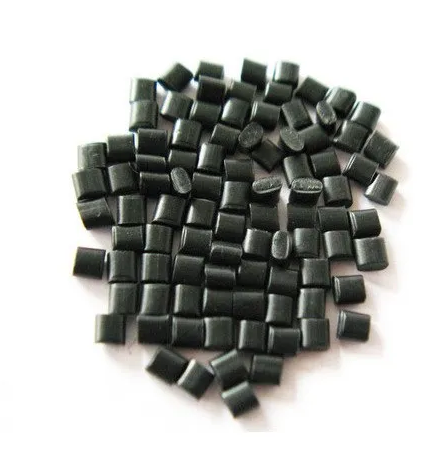
Talc powder will help PP plastic enhance the desired properties
Talc has always been one of the ideal ingredients to act as a plastic filler. Talc powder will help PP plastic enhance the desired properties (according to ratio and formula) at an extremely optimal cost. The outstanding features that talc powder can help PP plastic improve are conductivity, flexural modulus, hardness and durability. PP Talc compound is also very commonly used in many different manufacturing industries
In this compound, BaSO4 acts as a reinforcing agent, which helps PP plastic improve a series of outstanding features. Many manufacturing industries pay attention to PP BaSO4 because it has significantly reduced shrinkage, improved formability, increased product gloss and is super durable, better impact and chemical resistance.
-
PP flame retardant compound
This PP compound will be a combination of PP plastic and fire-resistant additives. One typical process is that the PP plastic substrate will be added with halogen-free additives to make the material less flammable and harder to burn. Besides, PP flame retardant compound also gives the product outstanding mechanical properties.
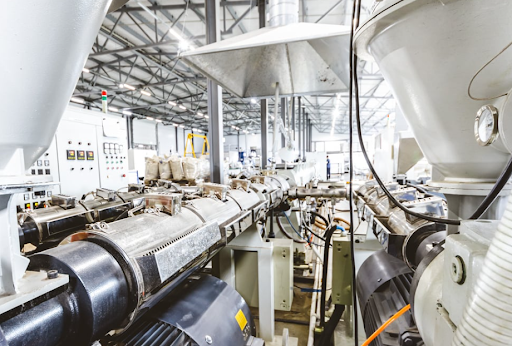
The extrusion process is one of the popular production methods
The extrusion process is one of the production methods that many investors are interested in thanks to the benefits that extrusion brings. This is a plastic processing process that involves high-pressure compression of plastic material by forcing the material through the mold hole of the machine. After being compressed through the mold hole, the material will form a new shape according to the design. This is one of the most popular manufacturing methods for long bar applications, tubes, and many other mass production processes. Among the many forms of extrusion, there are two most basic forms: hot extrusion and cold extrusion. Depending on the production plan, investors can choose the appropriate method.
Read more: Types of plastic extrusion and its manufacturing process
3. The extrusion process of Polypropylene compounds
PP composite materials have outstanding properties and can be fully adapted to the extrusion process to create finished products. The process of creating a product from PP compound by extrusion can be basically described as follows:
Step 1: Research ingredients
The main reason is because PP compound plastic has many different types and of course they also have different properties. Investors need to consider the goals for the upcoming product to choose a PP compound with corresponding properties.
Step 2: Proceed with the extrusion process
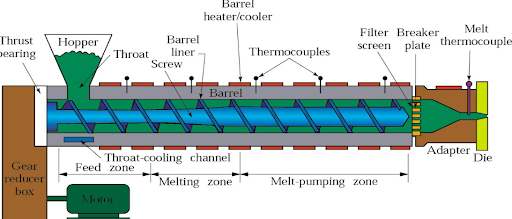
PP compound will be filtered through a barrier layer
-
The extrusion machine will be operated and closely observed throughout the production process. The PP compound will be poured into the material compartment of the extruder through the hopper. The material compartment will be the initial storage place, these PP plastic pellets will be ready for the shaping journey ahead.
-
In the current raw material chamber, PP plastic pellets will be heated at very high temperatures. This heating process will be carried out using the three heat intensity zones of the extruder until they melt.
-
At the well containing the molten material, the extrusion machine will continue to operate a continuously rotating shaft to push the molten plastic to the next part of the machine to prepare for the forming mold.
-
Before entering the mold, the molten PP compound will be filtered through a barrier layer. This step is intended to remove impurities contained in the original raw materials to avoid negative effects on the quality of the finished product. After passing through the filter membrane, the plastic material will be pushed into the pipeline to the mold part of the machine to be pressed into shape.
- The mold plays the role of shaping this liquid with high pressure and helps it stabilize to form the desired shape. Here, the liquid will fill the mold and create the designed shapes, even complex designs.
- After being pressed into the mold, the extruded product will be pushed to the cooling unit. Depending on the type of machine, this part can be a water nozzle or a cooling coil. After cooling, products made from PP compounds will be very hard and last forever in their newly extruded form.
Step 3: Evaluate the quality of finished products
To be able to bring PP compound products to consumers or apply them to construction projects, investors need to have an evaluation step to check product quality. This is an extremely important step because products made from PP compounds are often used for applications that require durability over time and certain safety. Defective, broken, cracked or unsatisfactory products need to be screened before application.
4. Benefits of the extrusion process of PP compound
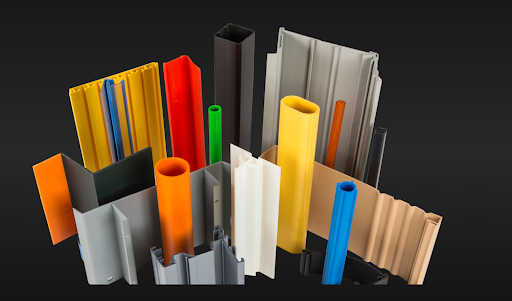
Extrusion process can produce products from PP compound in a short time
-
PP compound can adapt well to extrusion
The extrusion process is popular but also requires materials that can withstand harsh environments. PP compound plastic is one of the materials with high stability, good durability, and flexibility that can be completely adapted to the extrusion process. Some materials with low durability will break easily during the extrusion process, leading to the product not achieving the expected hardness.
-
Easily control product shape
PP compound material is known as one of the materials with excellent hardness. However, the extrusion process will help melt the material to create a shaping process that is many times easier. In addition, extrusion is also the ideal choice for designs with elaborate and complex details.
-
Produce a series of products from PP compound in a short time
The extrusion process takes place in a fairly quick cycle, saving much time for mass production of products. With a large production scale, investors can completely rest assured about the accuracy and uniformity of the molded products.
The investment cost for the extrusion machine is not too high, but the production efficiency is extremely large, helping to bring great economic benefits. PP composite materials that have cracks or defects can also be cut into small pieces, melted and then molded again. This helps make full use of materials and avoid waste.
5. Conclusion
In general, there are currently a series of optimal production methods, but extrusion is also an ideal solution for products made from PP compounds. Besides, PP compound plastic also adapts very well to the extrusion process thanks to its outstanding features. To make a decision for the upcoming extrusion method, you need to consider the unique characteristics of the above PP compound types. Find out more useful information from EuroPlas to optimize your project!