Bioplastic polymers are made from plants and other biological sources. They are used in 3D printing as a method of recycling waste by grinding undesired 3D prints and using a desktop extruder to turn them into filaments.
Bioplastic polymers can also be used to create biofilaments, which are made from sustainable energy sources like fats and vegetable oils. Since they're made from environmentally friendly material, these 3D filaments are less toxic and odorous than other filaments.
Read more: What are bioplastics made from? Materials to make bioplastics
1. Current Applications of Bioplastic Polymers in 3D Printing
Bioplastic polymers are used in 3D printing in many industries, including:
There are many eco-friendly furniture items, such as phone cases and vases, that are made from bioplastic polymers. It reduces the amount of plastic waste produced and appeals to users who are concerned about the environment.
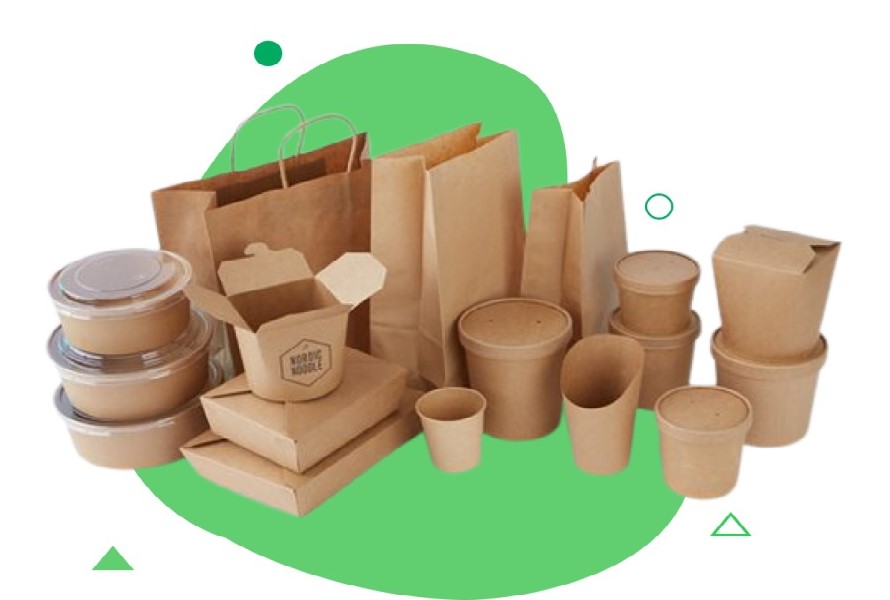
Environmentally friendly ones are gradually replacing traditional plastic food packaging. Nowadays, we can see many 3D-printed food containers and utensils available in the market.
Bioplastics such as PLA are used in medical applications for biodegradable implants and tissue engineering. Meanwhile, 3D-printed orthotics and prostheses are lightweight and reasonably priced and can be customized to fulfill patient requirements.
Many research studies and experiments have been done to create lightweight components made of bioplastic polymers. They are said to have the potential to reduce environmental impact and increase fuel economy.
Bioplastics are utilized to create sophisticated architectural features or lightweight, long-lasting construction materials for structural prototypes.
2. Technological Advancements Driving the Future of Bioplastic 3D Printing
Technological developments in bioplastics 3D printing provide a feasible way to address the drawbacks of petroleum-based materials, including environmental concerns and limited resources. Many eco-friendly ingredients, such as cellulose, starch, and lignin, are used in 3D printing.
Fused deposition modeling, direct ink writing, micro-extrusion 3D bioprinting, inkjet 3D printing, and 3D spinning are common additive manufacturing (AM) techniques used to manufacture biocomposites. These methods allow low-cost biomass resources to be used in the production of composite materials for a variety of sectors, including food, construction, pharmaceutical, and biomedical.
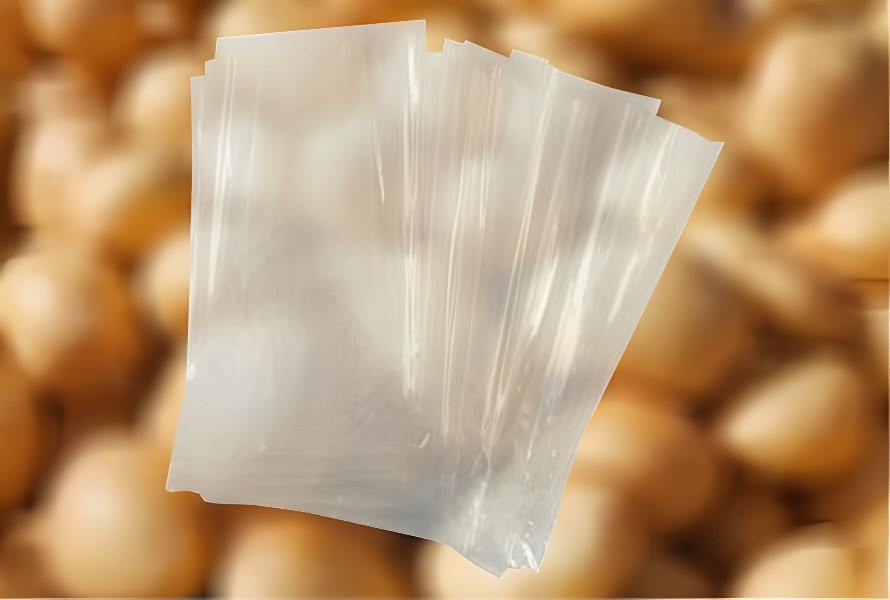
3 categories of 3D printing methods most frequently used for bioplastic polymers include:
- Material Extrusion Method: An extrudable substance is deposited via a nozzle (layer by layer). Common examples are FDM (fused deposition modeling), DIW (direct ink writing), and SLA (Stereolithography).
- 3D Spinning: Wet 3D spinning and 3D electrospinning methods are used to spin the polymer solution into layered filaments.
- Inkjet 3D Printing: Binder jetting is the method of depositing microscopic liquid droplets onto a substrate at a user-specified location by acoustic or thermal pressures.
3. Challenges and Limitations
Using bioplastic polymers in 3D printing faces can make it difficult to produce thin filaments for the material extrusion process. It's because of the die swell, a flaw that arises from the extrusion of viscous material via a tiny diameter extruder nozzle.
Besides, optimizing bioplastic formulations for 3D printing presents a challenge in minimizing defects such as low aggregation, poor mechanical characteristics, and component warpages. Yet, blends and composite formulas can reduce the possibility of flaws in 3D printed items by being tailored for certain processing methods and applications.
It's important to know that bioplastics are dissolved in potentially dangerous solvents such as tetrahydrofuran and chloroform during the 3D wet spinning process. Thus, investigating environmentally friendly solvents for 3D printing techniques is advised.
4. The Future Outlook Of Using Bioplastic Polymers In 3D Printing
Technological developments, strict plastic waste restrictions, and environmental consciousness are driving the growth of using bioplastic polymers in 3D printing. Market expansion is also being driven by corporate ecological initiatives and government incentives.
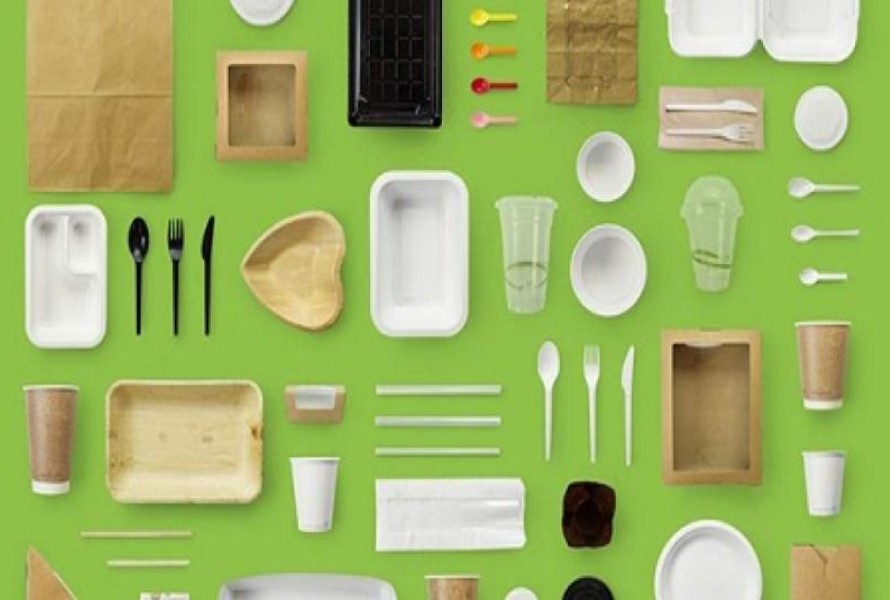
Biodegradable polymers, which provide a quicker and safer means to break down conventional plastics, are emerging as a possible solution to the plastic pollution problem. Technological advancements like polyhydroxyalkanoates (PHA) and polylactic acid (PLA) have made it possible to create solutions that are more effective and durable.
By addressing the drawbacks of previous biodegradable polymers, these materials open the door to more effective and long-lasting solutions. The trend towards sustainability is being driven by consumer demand for eco-friendly items as more and more people look for alternatives to traditional plastics.
Businesses are being forced to adopt more sustainable practices by this trend, which is having an impact on the market for biodegradable polymers. The market is changing to satisfy the rising demand for eco-friendly products and the growing environmental consciousness.
In the biodegradable polymer market, industry partnerships among enterprises, institutions, and governmental bodies are propelling innovation. These collaborations promote information exchange, resource sharing, and technological growth, which advances the development of biodegradable polymer solutions and paves the way for a sustainable future.
In summary, the market for biodegradable polymers is expected to expand in the future because of developing technologies, favorable laws, and growing consumer demand.
5. Conclusion
Due to the growing industrial demands, technical advancements, and environmental consciousness, bioplastic polymers have a bright future in 3D printing technology. These polymers have the potential to transform production processes and advance sustainable development. Businesses should not neglect this trend and should start investing in this futuristic material.
6. About EuroPlas' Bioplastics
Being the top manufacturer of filler masterbatch worldwide, EuroPlas is pleased to offer our clients innovative bioplastic solutions that help their companies save costs and gain competitive ability.
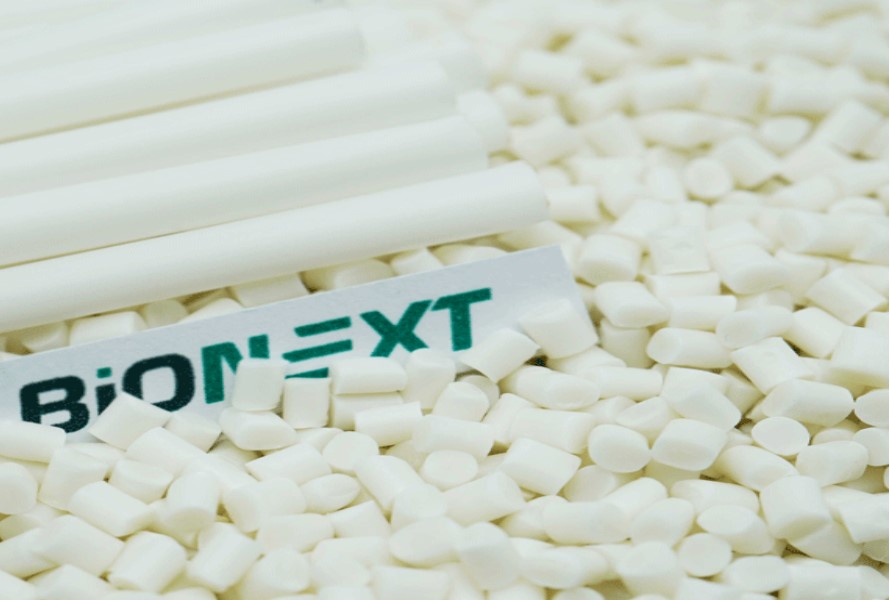
Our Bioplastic compound is a green material solution that enables end-products to be biodegradable within 12 months. It's made from renewable resources such as polylactic acid, PHA, and PHA. Our company always ensures strict control over our bioplastic production process.
Our product has:
- High elongation
- Great impact strength and hardness
- Easy machining properties
We also offer bio fillers, a cost-effective material solution for bioplastic end-products. Our BiOMates series are made from bioplastic, modified CaCO3 powder and dispersion aids with the following outstanding features:
- Full functions in one material
- Biodegradable within 12 months after use
- Tailor-made based on end-product requirements
If you're interested in our products, contact us now for more details!