Plastic materials with high wear resistance and durability are very popular in today's market. The main reason is because the demand for heavy industries is increasing. Customers place high demands on plastic materials. Therefore, please immediately refer to the article below to know the Top load-bearing and abrasion-resistant plastic materials with the most effective and sustainable quality over time.
1. List of Top impact-resistant and abrasion-resistant plastic materials
Plastic materials that are resistant to force and abrasion will minimize damage, will not deform and ensure quality after long periods of use.
Besides, these plastic materials also have other outstanding features such as: temperature resistant, waterproof, environmentally friendly and easy to combine with other materials.
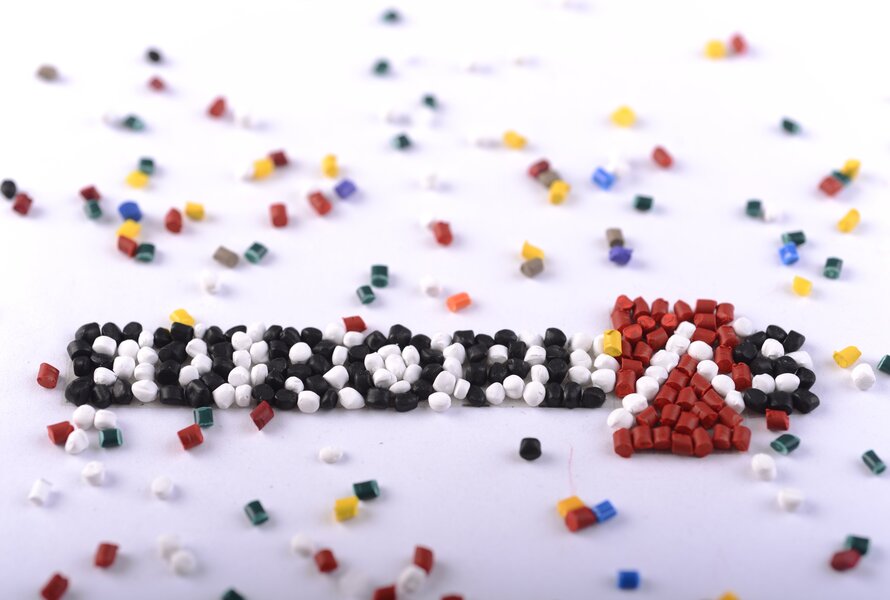
All types of plastic materials are resistant to impact and abrasion
High-durability plastic materials are commonly used in heavy industries and products that require long-term production.
Below is a list of the Top load-bearing and abrasion-resistant plastic materials.
1.1 PA6 bearing plastic material
PA6 plastic is also known as nylon 6 and called Polycaprolactam, they are classified as semi-crystalline Polyamide Polymers and have tight bonds between molecules in their chemical composition. PA6 plastic undergoes a ring-opening polymerization process.
In particular, the synthesis of nylon 6 involves the ring-opening polymerization of caprolactam, a molecule with 6 carbon atoms. Besides, the Amide bonds in PA6 plastic material will be arranged in the same direction, this is different from PA66 engineering plastic compound material and increases the surface durability of the material.
To prove the durability of PA6 bearing plastic material, we can look at the temperature they can withstand when converted into fiber. The average temperature is up to 533K in a non-reactive Nitrogen environment and lasts 4 - 5 hours.
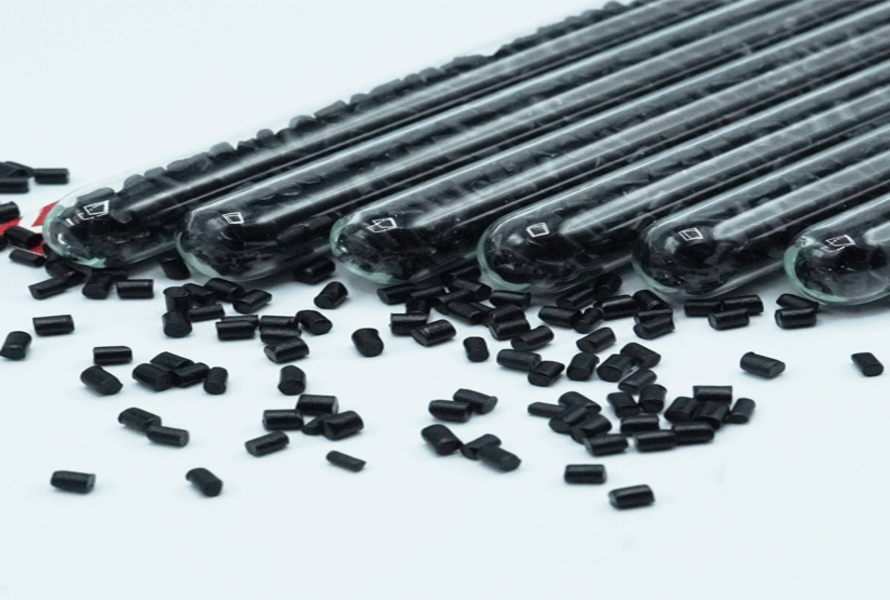
PA6 plastic sheet has stable thickness and bearing capacity
The abrasion resistance of PA6 plastic material is demonstrated by its resistance to foreign chemicals or strong acids or alkalis.
PA6 plastic material stands out with its abrasion resistance, high force tolerance and more stable mechanical properties than PA66 plastic. Furthermore, the heat resistance level of PA6 is up to nearly 300 degrees Celsius for many continuous hours, the density is quite dense from 1.13 to about 1.17 g/cm3.
Therefore, load-bearing PA6 plastic material is applied in the electrical & electronics industry, automobile & transportation industry, heavy industrial machinery & equipment as well as the medical field.
1.2 POM bearing plastic material
Acetal or Polyacetal is another name for the resistant plastic POM. Material product line with wide range of capabilities and durable mechanical properties.
The biggest advantage of POM material is its hardness and mechanical stability. They demonstrate this ability wonderfully even in temperatures as low as minus 30 degrees Celsius for long periods of time.
The density of wear-resistant POM plastic material is much higher than PA6 and other materials. The estimated index is from 1,420 to 1,450 g/cm3. Scientists have evaluated that: "The material with good mechanical performance, low friction index and the most durable size on the market is POM plastic."
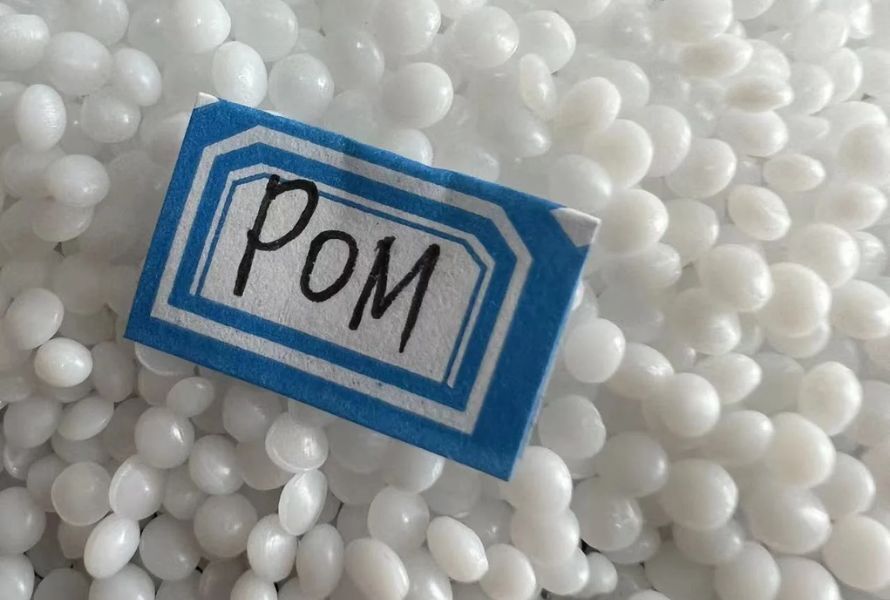
POM plastic pipes are abrasion resistant
70N/mm2 is an index to evaluate the tensile strength of plastic materials. The rate of elongation and destruction of POM plastic material reaches about 40%. Meanwhile, 100 degrees Celsius is the highest working temperature of the material and the lowest is about minus 50 degrees Celsius.
POM bearing plastic material also possesses similar characteristics to other materials such as: chemical resistance, water absorption, high temperature resistance, electrical insulation,...
POM anti-abrasion plastic is used in many industries such as:
- Automotive & Transportation: Products such as fuel systems, fuel valves, wheel axles or gear areas in engines.
- Industrial equipment: Products such as conveyor systems, motor shafts, gears, bearings.
- Electrical industry: Their insulating ability helps them be applied to products such as relay housings, circuit connectors, switches,...
- Sports: The field also needs plastic materials that are resistant to force and abrasion. POM is perfectly suited for the production of: bow and arrow parts, ski bindings, gear parts or bicycle mutes. These are products that require toughness, flexibility, low friction and extreme durability.
1.3 Abrasion-resistant plastic PVC
PVC plastic's official name is Polyvinyl Chloride. They are classified as thermoplastics and are formed from the polymerization of vinyl chloride (CH2=CHCl).
The material line is commonly used in the fields of medicine, packaging, construction materials or equipment & electronics. Besides, PVC plastic also stands out with its mechanical characteristics, variety of colors and sizes as well as high heat resistance. Moreover, PVC plastic is very difficult to deform when exposed to high levels of force from surrounding collisions.
The specific gravity of PVC plastic is approximately the same as POM anti-abrasion plastic, from 1.4 to about 1.5g.
In particular, if PVC resin is well combined with plastic additives, its specific gravity can be further increased. Next, PVC plastic is one of the plastic materials that can withstand the highest temperatures up to 1600 degrees Celsius. The molecular particles in the chemical structure of PVC plastic are relatively large from 50 - 150 microns and have very hardness. Good. Therefore, durability is the perfect point of this load-bearing material.
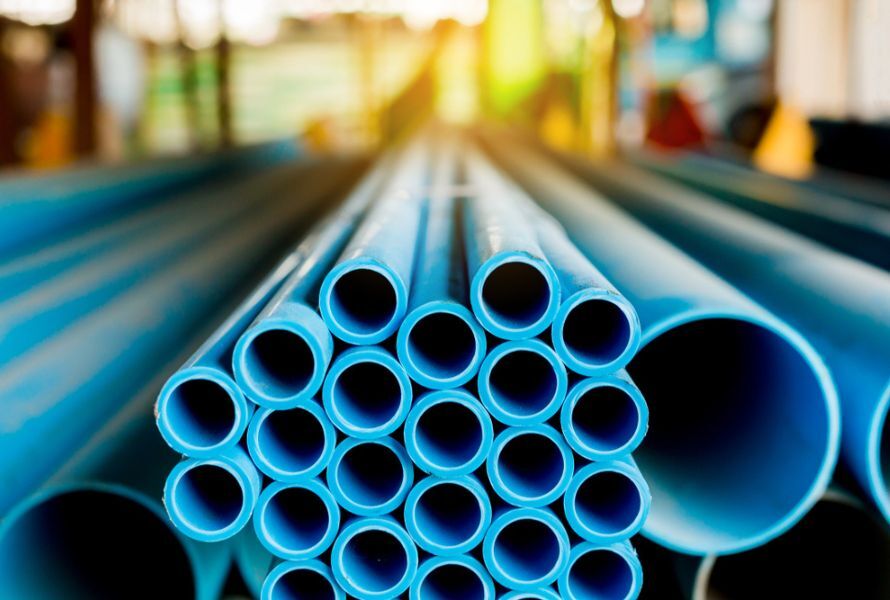
PVC plastic possesses stable physical properties
PVC is also classified into two different types including flexible PVC and rigid PVC. Each species has its own unique hardness but is still higher than other materials. If the hardness (psi) of flexible PVC is only from 1500 to 3600, the hardness of rigid PVC will range from 5000 to more than 8500. In particular, the compressive strength of PVC material reaches nearly 10,000 psi.
PVC abrasion-resistant plastic materials are used in a number of specific industries such as:
- Medical industry: PVC plastic materials are used to make respiratory tubes, intravenous bags, dialysis equipment, blood bags or catheters.
- Household industry: The flexibility and durability of PVC plastic help them be commonly used in manufacturing fiber optic cables, electrical wires, casings of metal products, and water pipes.
- Industrial art industry: PVC is used as wall cladding, partitions, shelves, tables or beds in the house. They are also designed into outdoor products such as event stands because of their UV resistance
- Sports industry: PVC is water resistant, flexible up to nearly 11,000 psi. Therefore, PVC abrasion-resistant plastic can be produced into jumping ropes, sports backpacks, and equipment for training and competition.
1.4 PEEK plastic material is resistant
PEEK bearing plastic material debuted on the market in late 1879 and was found by ICI Group in the United Kingdom. The chemical structure of PEEK resins is also quite special because they are made up of the connection of many Benzene rings through two main groups including: ether group (-O-) and ketone group (-C(=O)-) .
Currently, PEEK plastic is divided into 2 types on the market. These are PEEK plastic in tree form and PEEK plastic in sheet form. Their average size will range from 600x1000mm with a variety of colors.
PEEK plastic is considered by many manufacturers to be the highest quality plastic material on the market. The tensile strength and elastic modulus parameters of PEEK plastic are extremely impressive at 170MPa and 3.6 Gpa, respectively. Furthermore, the impact durability is calculated in units of Lzod j/m of PEEK plastic up to nearly 4000.
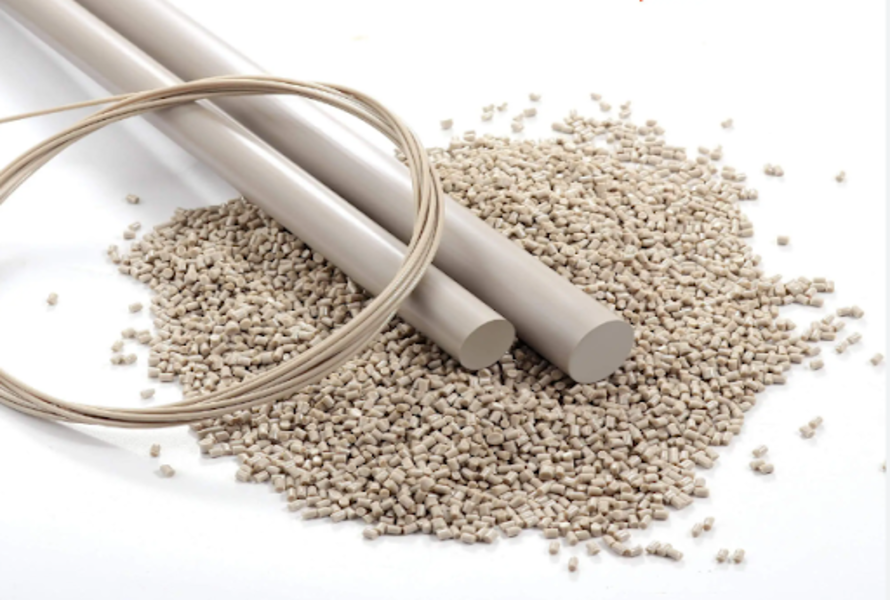
PEEK plastics also meet the criteria of durability and abrasion resistance
The highest temperature that PEEK plastic can withstand is about 300 degrees Celsius for a long time. Therefore, PEEK plastic is used in industries such as:
- Technology & electronics: Japanese businesses love PEEK plastic. They are used to produce electronic circuit boards, electrical connectors or compartments, computer equipment,...
- Large-scale mechanical production: PEEK plastic will also be utilized in equipment that transports and stores natural gas, ultrapure water or petroleum such as pumps, pipelines and pump valves.
- Aerospace: PEEK is the top load-bearing plastic material, so they can replace aluminum or metal. PEEK plastic is used to produce commercial or fighter aircraft parts, missile equipment,...
Read more: PEEK plastic: Definition and Application
1.5 HDPE anti-abrasion plastic
Petroleum is one of the main ingredients in the production of HDPE plastic. The molecular structure of HDPE plastic is very high and thick. Therefore, they possess stable durability and resistance to impact with strong force.
HDPE (High Density Polyethylene) is a synthetic plastic material widely used in industries today. In the chemical structure of HDPE plastic, they will have a strong connection of Ethylene and form long chains called Polyethylene.
This has helped the surface of HDPE plastic have effective hardness, flexibility and abrasion resistance. Besides, HDPE has a light weight ranging from 0.9 to about 0.98 g/cm3. In particular, the chemical structure of HDPE has very little branching so it has good strength.
It is the ability to withstand wear and abrasion that helps HDPE plastic have a longer life than other materials. In particular, strong acid solutions or solvents are not capable of affecting HDPE plastic.
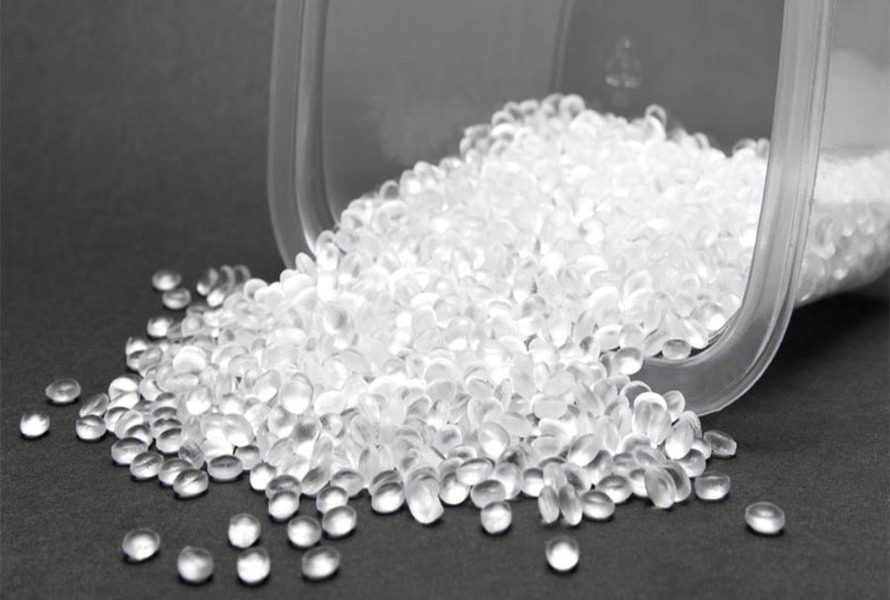
HDPE plastic has quite good strength and abrasion resistance
Therefore, HDPE plastic is produced into products such as drainage systems, construction materials, food wrap, plastic tools, machinery equipment or toy products.
Read more: HDPE (High density polyethylene) - What is it? Properties & common uses
2. Product introduction of PA6 Compound fiberglass
A thermoplastic product manufactured by EuroPlas' team of experienced technicians. The product PA 6 Compound glass fiber is a combination of fiberglass additives and PA resin base.
EuroPlas products have a standard glass fiber content of about 30 - 50%. In particular, fiberglass will meet the need to increase the durability of materials, helping them withstand strong impacts.
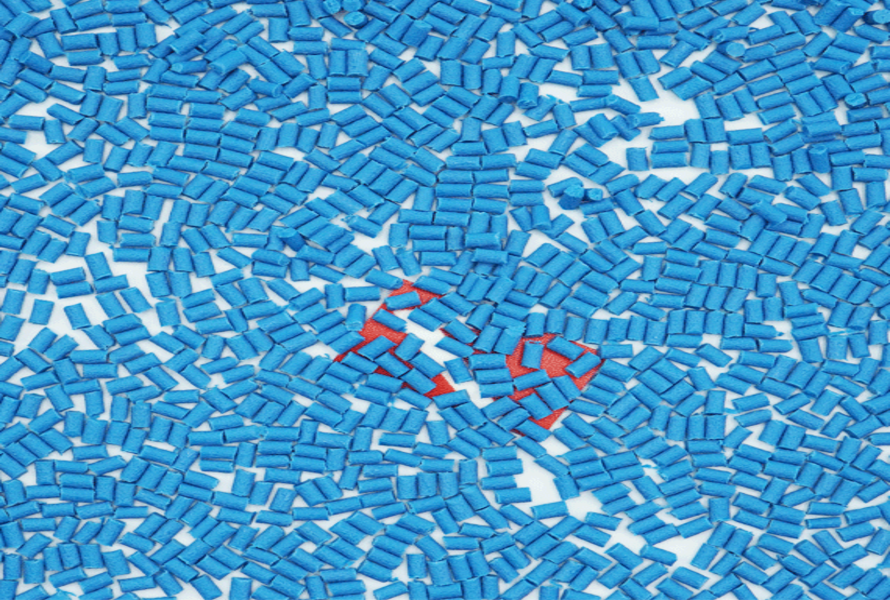
PA6 Compound fiberglass by EuroPlas
In addition, EuroPlas' glass fiber and PA plastic components also have chemical resistance, water resistance, and high temperature resistance. In addition, it is also a stable, insulating material and easy to process and PA6 anti-wear plastic widely used in the production of gears, bearings, transmission belts, carburetor components, computer components or household electrical components
EuroPlas has introduced to you the Top 5 load-bearing and abrasion-resistant plastic materials. Please continue to follow us to update the latest information on plastic products and information!