Polypropylene resin is among the most widely used thermoplastics in the world. With its lightweight nature, chemical resistance, toughness, and cost-effectiveness, polypropylene resin supports a vast number of products used daily. This article explores how different industries rely on it, backed with real-world applications and sources that demonstrate its critical role.
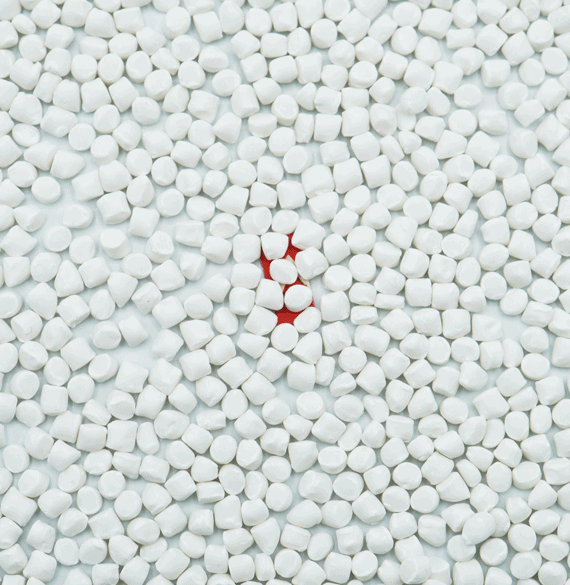
PP Filler Masterbatch - one of the EuroPlas products made from polypropylene resin.
1. Packaging industry
The packaging sector is the largest global consumer of polypropylene resin, accounting for over 30% of total usage according to Exir Polymer (Exir Polymer). It’s commonly found in yogurt cups, bottle caps, plastic wraps, and microwave-safe containers.
Polypropylene’s excellent clarity, impact resistance, and recyclability make it ideal for food packaging and household products. For example, Nestlé uses polypropylene for flexible food wrappers and containers. Amazon’s recyclable mailer bags also incorporate a polypropylene outer layer.
Its low density reduces overall packaging weight—cutting transport costs and carbon emissions while enhancing supply chain efficiency.
2. Automotive industry
Modern cars use polypropylene resin in dashboards, bumpers, interior panels, and battery cases. One reason is expanded polypropylene (EPP), which offers both strength and energy absorption while remaining light. A Knauf Automotive report shows EPP use in cars reduces weight by up to 10%, improving fuel efficiency (Knauf Automotive).
Volkswagen and Toyota have both integrated EPP in vehicle bumpers and side protection panels. In electric vehicles, lightweight polypropylene components contribute to better range and structural balance.
3. Medical and healthcare
The healthcare industry depends on polypropylene for its sterility and chemical resistance. It’s the material of choice for syringes, pill bottles, specimen containers, and surgical trays. Medical-grade variants such as Topilene (developed by Hyosung) are suitable for autoclaving and safe for direct human contact (Resmart).
Hospitals use polypropylene in face mask layers, IV fluid bottles, and medical vials. Becton Dickinson, a global leader in medical supplies, uses polypropylene in their syringe and diagnostic kit production.
4. Consumer goods and appliances
From storage boxes to food processors, polypropylene appears in countless household products. Its heat and chemical resistance, combined with flexibility, make it a go-to material for durable homeware. Brands like IKEA use polypropylene in kitchen accessories and furniture due to its safety and recyclability.
Additionally, polypropylene fibers are used in carpets, upholstery, and thermal clothing. Sportswear brands often blend it in base layers for thermal insulation and moisture-wicking properties.
5. Construction and infrastructure
Construction applications include piping, insulation, and geotextiles. Polypropylene’s ability to resist corrosion, moisture, and chemicals makes it suitable for plumbing systems and underground utilities.
Geotextiles made from polypropylene also help with erosion control, soil stabilization, and drainage in civil engineering projects. According to AC Plastics, it’s also common in barrier membranes and building wraps (AC Plastics).
Companies like DuPont and Propex use polypropylene in high-performance underlayments and woven construction textiles.
6. Electrical and electronics
In electronics, polypropylene resin is used in capacitors, cable insulation, and battery housings. Its superior dielectric strength ensures safe current insulation. It’s particularly valued in high-performance capacitors for power grids and consumer electronics.
According to EuroPlas, polypropylene’s thermal resistance and fire retardancy (with proper additives) make it suitable for appliance housings and protective casings (EuroPlas). Companies such as Panasonic and Vishay manufacture film capacitors using biaxially oriented polypropylene (BOPP) film.
7. Agriculture
In farming, polypropylene resin is used to make woven sacks, irrigation components, seedling trays, and greenhouse sheets. Its UV resistance extends product lifespan in outdoor settings. Bulk bag makers note that polypropylene bags are favored for their high load capacity and reusability in transporting crops and fertilizers (Bulk Bag Reclamation).
In India and Southeast Asia, polypropylene woven bags are the standard for rice and grain storage. Netting and shade cloths in greenhouses are also commonly made from polypropylene fibers.
8. Conclusion
Whether in your food packaging or your car’s bumper, polypropylene resin plays a key role in shaping modern life. Its versatility, affordability, and performance ensure it remains a dominant material across multiple industries.
As sustainability pressures grow, innovations in recycling and biobased polypropylene will further enhance its role in the future of responsible manufacturing.
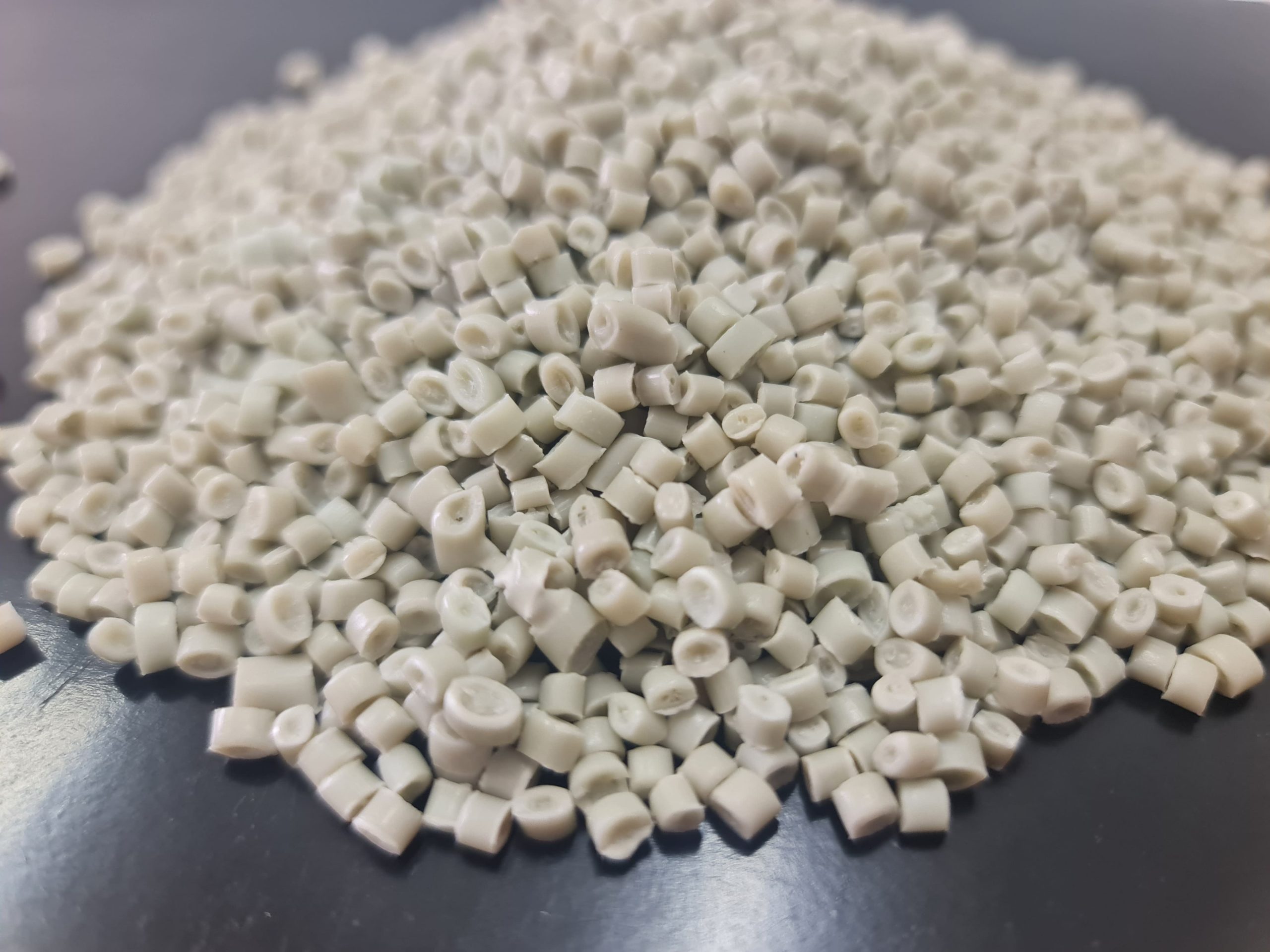
Polypropylene resin plays a key role in shaping modern life.
9. About EuroPlas
EuroPlas is one of the world’s leading manufacturers of plastic masterbatch and compound solutions, including high-performance polypropylene-based materials. With seven factories across Vietnam and Egypt and an annual production capacity of 800,000 tons, EuroPlas serves more than 95 countries globally.
Offering six major product lines—including filler masterbatch, color masterbatch, plastic additives, engineering compounds, bioplastics, and bio-fillers—EuroPlas delivers materials tailored to the specific needs of various industries. To learn more about sustainable polypropylene solutions, visit europlas.com.vn.