Injection molding is essential for producing complex plastic parts efficiently. Understanding key specifications is crucial for ensuring quality and optimizing production. This article highlights the important injection molding specifications to remember and their impact on final products.
1. Why You Need To Know Injection Molding Specifications
Injection molding is a key process by which high-quality components are produced efficiently, and thus it forms one of the bases of modern manufacturing. Therefore, the understanding of injection molding specifications is very important in several ways:
- Quality assurance: Specifications ensure that products meet the standards of the industry and customers, which translates into better quality and consistency.
- Process optimization: Knowledge of these specifications helps identify areas for improvement, reducing waste and minimizing defects during production.
- Cost efficiency: Properly applied specifications can enhance productivity to help lower manufacturing costs and increase profitability.
- Competitive advantage: The awareness of the most recent standards and best practices allows manufacturers to remain competitive in a fast-changing market.
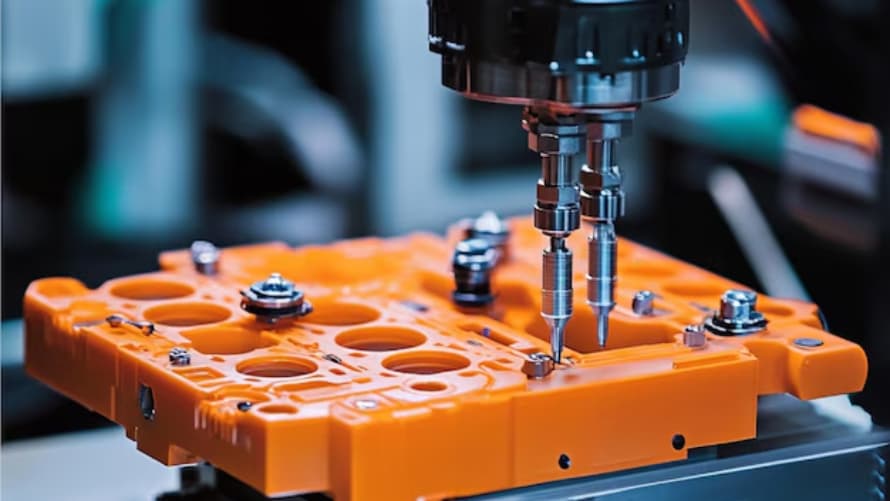
Knowing about injection molding specifications is essential.
2. Essential Specifications You Need To Remember
2.1. Injection volume
The theoretical injection volume is the most critical factor in the specifications of injection molding and gives the maximum amount of material that can be actually injected into the mold in one cycle. It is therefore a very important measure for understanding the capability of the injection molding machine to see if it can accommodate a certain part size.
2.2. Injection weight
Injection weight is one of the most important elements in the specification of injection molding, which refers to the amount of plastic material that can be injected in one cycle, usually polystyrene (PS). It is determined by the material density and theoretical injection volume, and it helps to evaluate whether the machine is suitable for production runs involving specific materials.
2.3. Injection rate
Injection rate shows the speed of injecting plastic into the mold cavity expressed through grams per second, g/s. It becomes really important to provide such an injection speed that allows quick filling and complete fulfillment of a mold with given material while not creating some defects like voids or incomplete filling.
2.4. Injection pressure
Among the specifications in injection molding specifications, injection pressure is one that shows the force with which the molten plastic is injected into the mold. This is one of the very critical parameters in overcoming mold resistance to ensure proper filing. A typical value is 700-2000 bar, depending on the material and part complexity.
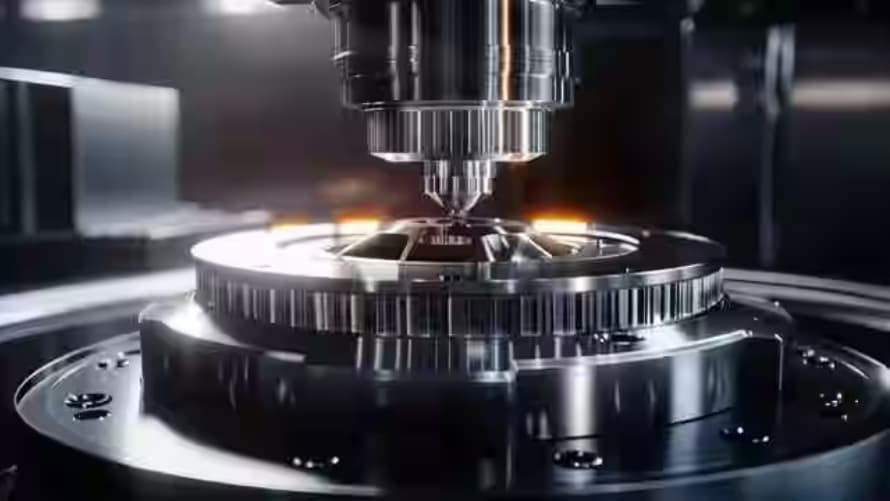
Injection pressure is one of the essential specifications you should know.
2.5. Screw speed
In injection molding, screw speed refers to the speed of rotation of the screw in its plasticizing phase and is normally measured in revolutions per minute (RPM). Applications of an optimal screw speed vary according to material viscosities and desired mixing, which would again affect the whole injection moulding process.
2.6. Clamping force
Clamping force is an important specification in injection molding specifications, provided by the machine to keep the mold closed while injection takes place. It is a way of preventing the opening of a mold under pressure and is measured in tons. The clamping force has to be sufficient enough to hold the injection pressure as specified by the process.
2.7. Mold opening stroke
The mold opening stroke specification represents the distance that an injection mold can open, for its disengagement from a clamping mechanism. This has always been very important for convenient part removal and is usually expressed in millimeters.
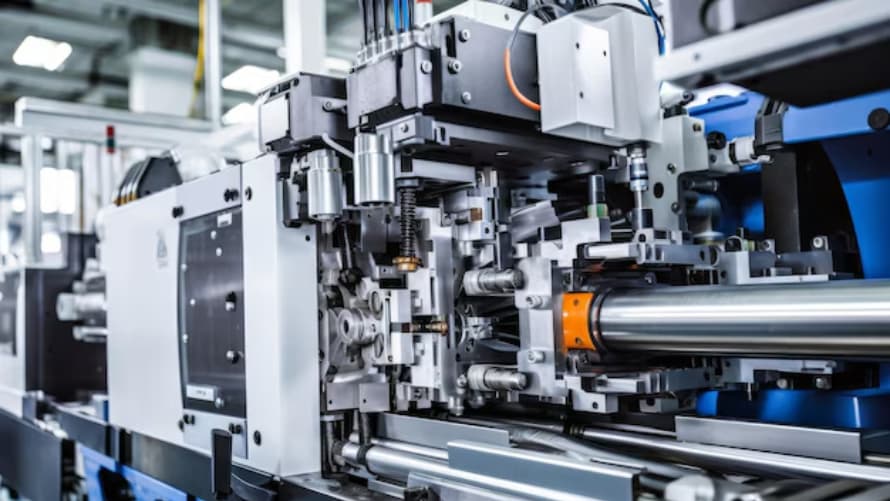
Mold opening stroke is one of injection molding specifications.
2.8. Oil tank
The oil tank is a very important feature in injection molding specifications; this holds hydraulic oil for the machine during operation. The capacity will always be big enough to sustain hydraulic performance through the injection molding process.
2.9. Ejector stroke
Ejector stroke is a very important parameter in injection molding specification, and it refers to the travel distance of the ejector system while ejecting the part from the mold. It should be long enough to assure a proper ejection of parts without breakage.
2.10. Ejector force
In injection molding specifications, ejector force refers to the force applied by the ejector system in order to push the part out of the mold. This is a critical force that has to be applied to ensure that the part is ejected cleanly without damage.
3. How These Specifications Affect Final Products
3.1. Injection volume
Injection volume, which dictates the amount of material that can be injected into the mold, is a very important regard in injection molding specifications. The correctly calibrated injection volume means that the mold will be full and that defects cannot happen to the final parts for maintaining dimensional accuracy.
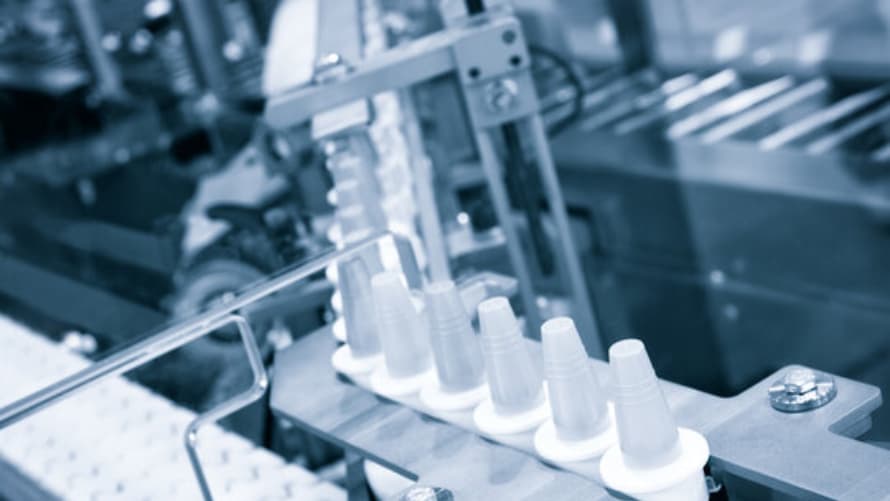
Injection volume is important in maintaining dimensional accuracy.
3.2. Injection weight
The injection weight is the weight of the plastic material, such as polystyrene, injected during one cycle, and it shall be an important parameter of an injection molding specification. The accurate and reliable injection weight is very important to maintain the consistency of part dimensions and mechanical properties, avoiding variability that can poorly affect product performance.
3.3. Injection rate
The rate of injection describes the speed at which the molten plastic is injected into the mold. Though it may be necessary to optimize the injection rates for cycle time reduction and efficiency enhancement, these must be balanced to avoid defects such as short shots or air traps-both critical considerations in injection molding specifications.
3.4. Injection pressure
The injection pressure overcomes mold resistance and hence is important for the proper filling of the molding; it forms a part of the injection molding specifications. Enough pressure avoids incomplete fills and defects, while too much pressure may create flash or material stress in the final product.
3.5. Screw speed
Screw speed affects melting and mixing in injection molding specs. An optimal speed ensures thorough material processing; too high a speed can cause overheating, while too low can lead to poor mixing and inconsistent product quality.
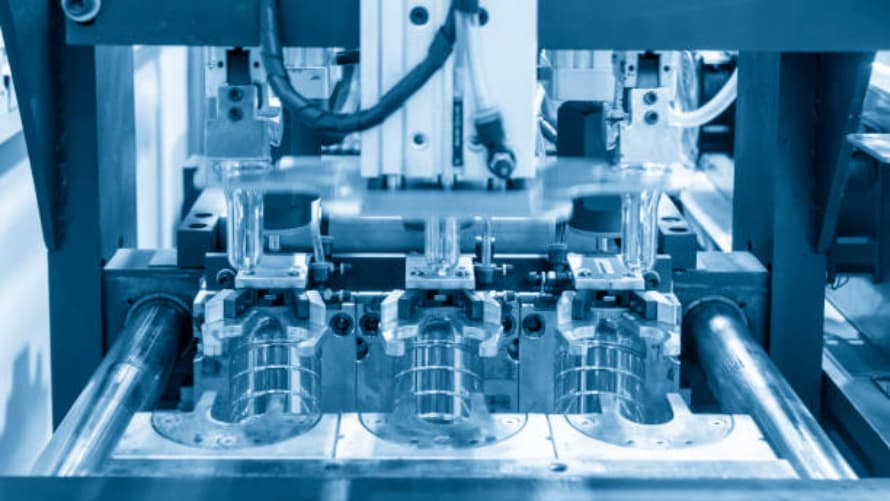
Screw speed related to the melting and mixing processes.
3.6. Clamping force
Clamping force is the means by which the mold is kept closed during injection and thus is a basic constituent of injection molding specifications. When well-calibrated force prevents mold separation and resultant defects in the final product, on the other hand, an insufficient force results in a dimensionally inaccurate part with surface flaws.
3.7. Mold opening stroke
Mold opening stroke is the other important injection molding specification that determines how parts will be easily ejected. Sufficient stroke length must be provided to prevent the part from sticking during ejection and causing damage to prevent smooth operation and continuous production.
3.8. Oil tank
Oil tank capacity affects the hydraulic system and is part of injection molding specs. Enough oil supply will give good running and efficiency so the machine will run well throughout the injection molding process.
3.9. Ejector stroke
Ejector stroke length is important to ensure parts are ejected out of the mold and is part of injection molding specs. Insufficient stroke will cause partial ejection and increase cycle time and risk of damage during part removal.
3.10. Ejector force
The most critical need for ejector force, in relation to the process, is for smooth removal of the molded part from the mold. It's a vital parameter in injection molding specification, basically sufficient to overcome friction without damage. Insufficient force may result in the part sticking and in defects, whereas excessive force may stress the part or damage the mold.
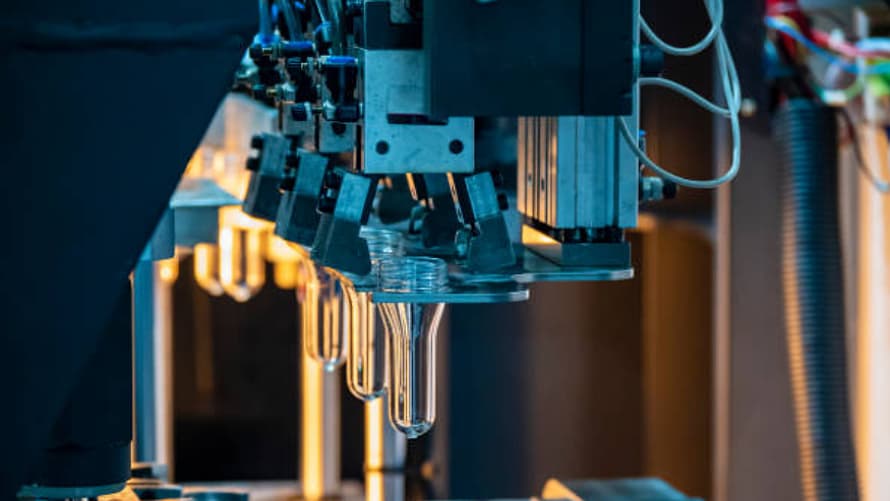
The smooth removal of molded pieces depends on ejector force.
4. Conclusion
Mastering injection molding specifications is crucial for manufacturers looking to produce high-quality plastic parts efficiently. By understanding and implementing these key specifications, businesses can optimize their production processes, reduce costs, and ensure the delivery of reliable and durable products.
5. About EuroPlas
Europlas is a reliable supplier in the world of plastic raw materials, particularly for injection molding applications. With a strong focus on high-quality products, especially filler masterbatch, Europlas empowers manufacturers to enhance their processes and achieve cost-effective solutions.
Feel free to contact us to discuss our products and how we can support your needs!