In the world of materials, TPE vs TPU have emerged as two prominent thermoplastic elastomers, each with its own set of characteristics and applications. TPE, or Thermoplastic Elastomer, and TPU, or Thermoplastic Polyurethane, offer a wide range of properties that make them suitable for diverse industries and applications. From automotive components to footwear and electronics, these materials play a significant role in product design and development. Understanding the differences between TPE vs TPU is crucial for professionals and enthusiasts alike to make informed decisions when selecting materials for their projects.
This comprehensive comparison aims to delve into the unique features, applications, and benefits of TPU vs TPE, enabling a deeper understanding of their potential and aiding in material selection for various industries. So let’s get started!
Table of Contents
- What is TPE?
- What is TPU?
- TPE vs TPU: What are the differences?
- About EuroPlas masterbatch
1. What is TPE?
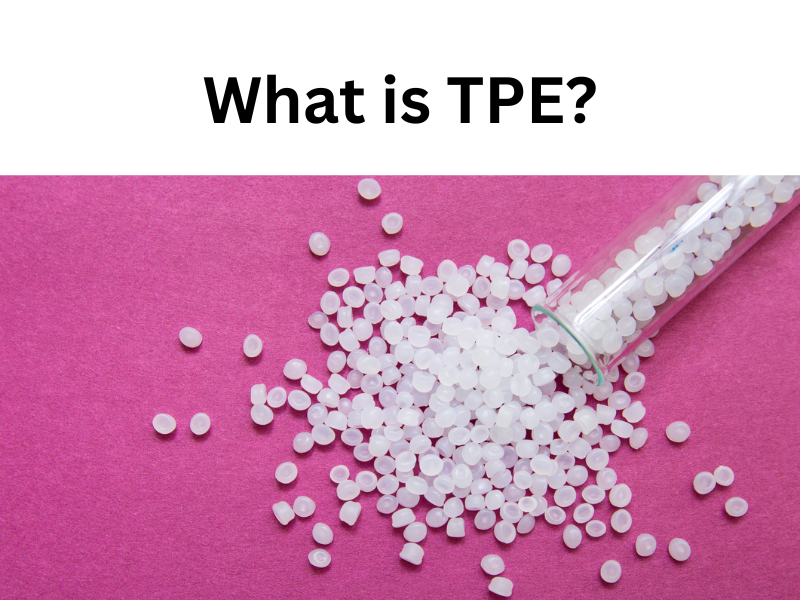
TPE
Thermoplastic Elastomer (TPE) is a versatile polymer material that combines the properties of thermoplastics and elastomers. It is a type of synthetic rubber that can be melted and reshaped multiple times without undergoing significant degradation. TPEs are known for their flexibility, resilience, and durability, making them suitable for a wide range of applications across various industries.
TPEs are composed of a polymer matrix, typically a thermoplastic material, with dispersed elastomeric particles. This unique combination provides TPEs with properties such as softness, stretchability, and resistance to impact. They exhibit elastomeric behavior, allowing them to be stretched and returned to their original shape without permanent deformation.
The manufacturing process of TPE involves blending the thermoplastic and elastomeric components, which can be done using various techniques such as injection molding, extrusion, or blow molding. This flexibility in processing methods allows TPEs to be molded into complex shapes and sizes, making them suitable for intricate designs.
TPEs offer several advantages over traditional rubber materials. They are lightweight, have good chemical resistance, and can be recycled, making them more environmentally friendly. TPEs also have a wider temperature range compared to rubber, allowing them to maintain their properties in both high and low temperatures.
Due to their versatility, TPEs are used in a wide range of applications. They are commonly found in automotive components, consumer products, electrical cables, medical devices, and soft-touch grips. TPEs have also gained popularity in the footwear industry, where they are used to create comfortable and flexible shoe soles.
2. What is TPU?
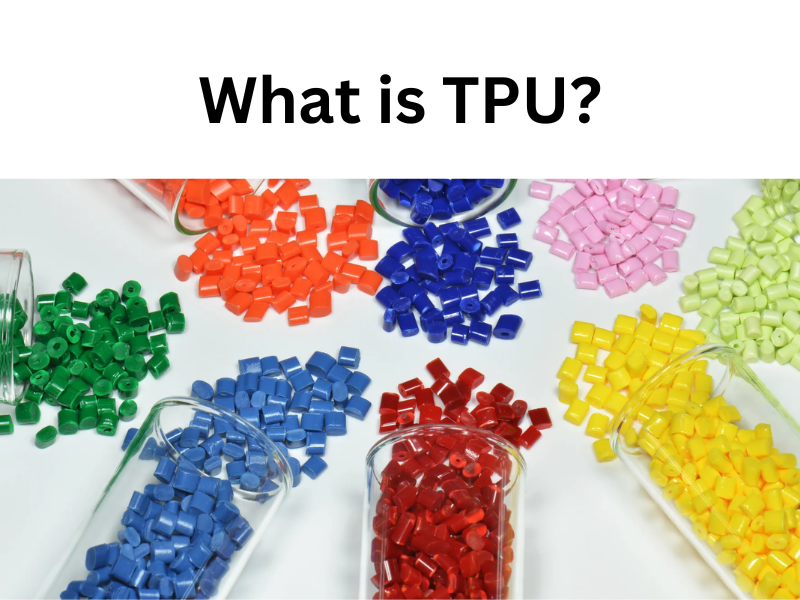
TPU
Thermoplastic Polyurethane (TPU) is a type of thermoplastic elastomer that offers a unique combination of properties, making it highly sought after in various industries. TPU is derived from the reaction of diisocyanates and polyols, resulting in a polymer with alternating hard and soft segments.
TPU possesses excellent mechanical properties, including high tensile strength, abrasion resistance, and elongation. It exhibits elastomeric behavior, allowing it to be stretched and compressed without permanent deformation. This flexibility and resilience make TPU suitable for applications that require both durability and flexibility.
One of the notable characteristics of TPU is its wide range of hardness levels. It can range from soft and flexible to rigid and tough, depending on the specific formulation and processing techniques. This versatility allows TPU to be tailored for different applications, from soft-touch grips and footwear soles to industrial seals and gaskets.
TPU also offers good chemical resistance, which enables it to withstand exposure to oils, solvents, and other harsh substances. Additionally, it exhibits excellent resistance to hydrolysis and microbial attack, making it suitable for outdoor and water-exposed applications.
In terms of processing, TPU can be easily melted and shaped using techniques such as injection molding, extrusion, and blow molding. It has good melt flow properties, allowing for intricate and complex designs to be achieved.
The diverse range of applications for TPU includes automotive parts, sportswear and outdoor gear, electronics, medical devices, industrial components, and more. Its ability to combine the properties of rubber and thermoplastics makes it a preferred choice for applications that require flexibility, durability, and customization options.
3. TPE vs TPU: What are the differences?
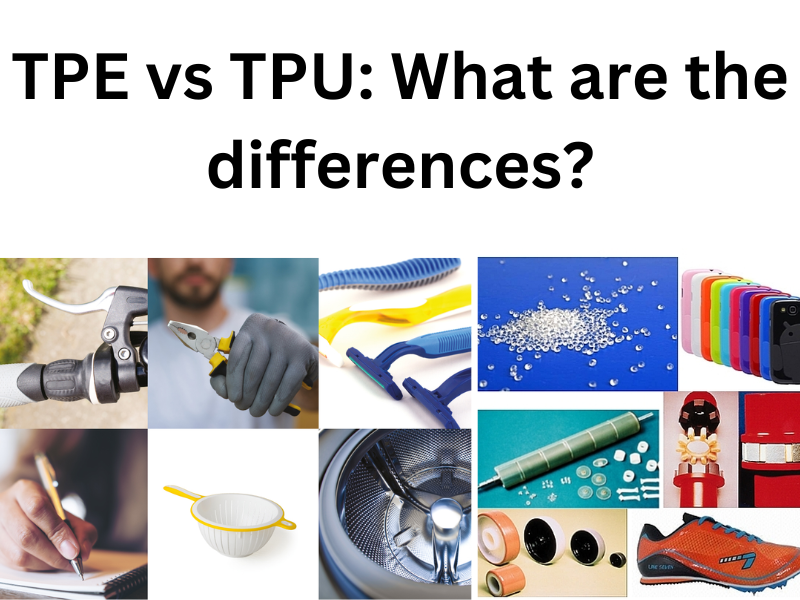
Differences between TPE vs TPU
TPE (Thermoplastic Elastomer) and TPU (Thermoplastic Polyurethane) are both thermoplastic elastomers, but they have distinct differences in terms of their composition, properties, and applications. Let's delve into the dissimilarities between TPU vs TPE to understand their unique characteristics more comprehensively.
3.1. Composition:
TPEs are typically composed of a thermoplastic matrix with dispersed rubber particles. This combination provides TPEs with the flexibility, resilience, and elasticity typically associated with rubber materials. The rubber component allows TPEs to be easily stretched and deformed without undergoing permanent deformation.
TPUs are derived from the reaction of diisocyanates and polyols, resulting in a polymer with alternating hard and soft segments. This composition gives TPUs their inherent toughness, durability, and flexibility. The alternating segments contribute to the excellent mechanical properties of TPUs, such as high tensile strength and abrasion resistance.
3.2. Hardness Range:
TPEs offer a wider range of hardness levels compared to TPUs. They can vary from very soft (e.g., gel-like) to semi-rigid, providing versatility in meeting different application requirements. The hardness of TPEs can be adjusted by modifying the ratio of the thermoplastic matrix and rubber particles.
TPUs also offer a range of hardness levels, but they tend to be more rigid compared to TPEs. TPUs can range from soft and flexible to rigid and tough, making them suitable for applications that demand both durability and flexibility. The hardness of TPUs can be tailored by adjusting the composition and structure of the hard and soft segments.
3.3. Mechanical Properties:
TPEs exhibit excellent elasticity and flexibility, allowing them to be repeatedly stretched and recovered without permanent deformation. They offer good resilience, impact resistance, and tear strength. TPEs are known for their soft and tactile feel, providing a comfortable grip. However, they may have lower tensile strength and abrasion resistance compared to TPUs.
TPUs possess high tensile strength, abrasion resistance, and elongation properties. They can withstand heavy-duty applications and offer superior durability. TPUs exhibit both flexibility and toughness, providing a balance between elasticity and rigidity. They are known for their resilience and ability to withstand demanding conditions.
3.4. Chemical Resistance:
TPEs generally have good resistance to chemicals, oils, and solvents, but their resistance may vary depending on the specific formulation. It is important to consider the specific application requirements and select a TPE grade with appropriate chemical resistance.
TPUs demonstrate excellent chemical resistance, making them suitable for applications that require exposure to harsh substances and environments. They can withstand contact with oils, fuels, chemicals, and many solvents without significant degradation, making them ideal for demanding industrial applications.
3.5. Processing Methods:
TPEs can be easily processed using techniques such as injection molding, extrusion, and blow molding. They have good melt flow properties, allowing for complex designs and intricate shapes to be achieved. TPEs can also be overmolded onto other materials, expanding their design possibilities.
TPUs are also amenable to various processing methods, including injection molding and extrusion. They exhibit good melt flow characteristics, facilitating the production of intricate parts and components. TPUs can be processed using multi-shot molding techniques to combine different materials or colors in a single manufacturing step.
3.6. Applications:
TPEs find applications in a wide range of industries, including automotive, consumer goods, electronics, medical devices, and more. They are commonly used for soft-touch grips, seals, gaskets, flexible components, and vibration-damping applications. TPEs have also gained popularity in the footwear industry for shoe insoles, cushioning materials, and flexible shoe soles.
TPUs are widely utilized in automotive parts, footwear, sportswear, industrial components, electronics, and more. Their toughness, abrasion resistance, and flexibility make them suitable for applications such as automotive seals, hoses, belts, protective covers, cable insulation, sporting goods, and outdoor gear.
In conclusion, while both TPE vs TPU are thermoplastic elastomers, they exhibit differences in terms of composition, hardness range, mechanical properties, chemical resistance, processing methods, and applications. Understanding these dissimilarities is crucial in selecting the appropriate material for specific use cases, ensuring the desired properties and performance are
4. About EuroPlas masterbatch
EuroPlas takes pride in being a leading masterbatch manufacturer in Vietnam, offering top-quality solutions for a wide range of industries. With our extensive expertise and cutting-edge technology, we provide an extensive selection of innovative masterbatch products that cater to diverse applications and requirements.
Discover the details of our comprehensive product offerings:
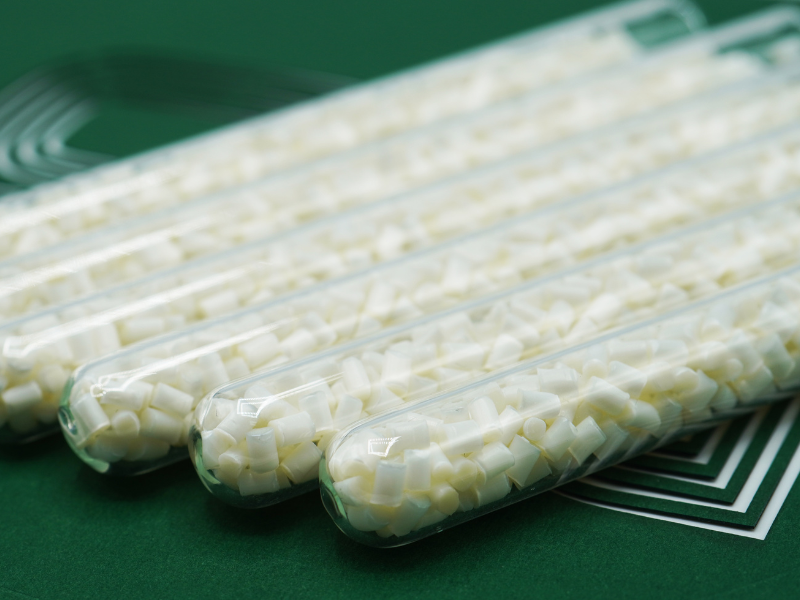
EuroPlas Bioplastic Compound
Our bioplastic compounds are meticulously developed to address the growing demand for sustainable and environmentally-friendly materials. These compounds are derived from renewable sources and boast excellent biodegradability while retaining the necessary mechanical properties required for various applications.
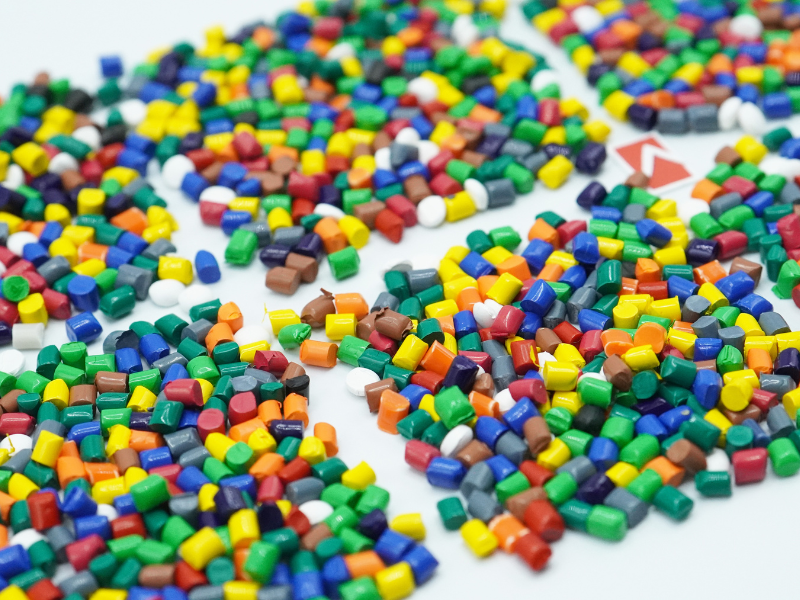
EuroPlas Color Masterbatch
EuroPlas color masterbatch products are designed to elevate the visual appeal of plastic products. Our vast selection of vibrant and consistent colors empowers manufacturers to achieve desired aesthetics, reinforce brand identity, and differentiate their products in the market.
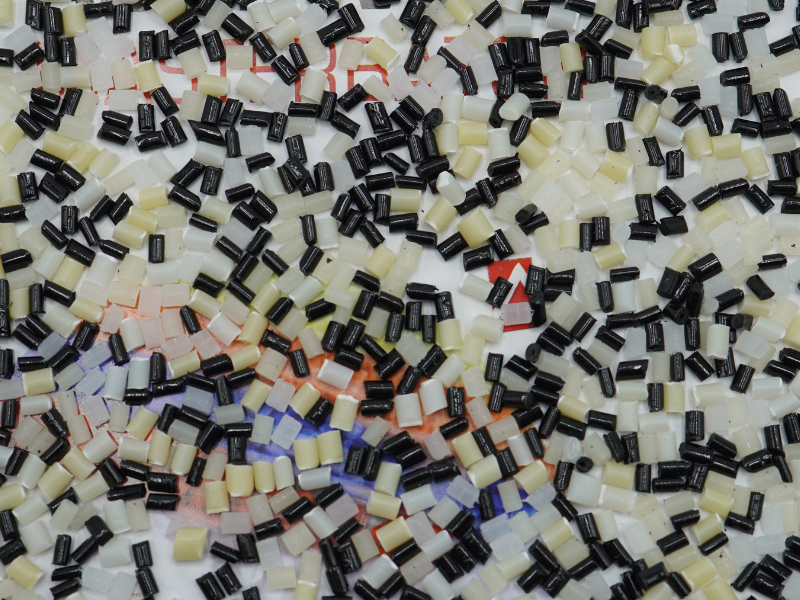
EuroPlas Plastic Additives
With a focus on enhancing the performance and functionality of plastic materials, our range of plastic additives offers tailored solutions. EuroPlas provides an extensive portfolio of additives, including UV stabilizers, antistatic agents, flame retardants, processing aids, and more. These additives bolster durability, optimize processing characteristics, and improve end-use properties, resulting in superior plastic products.
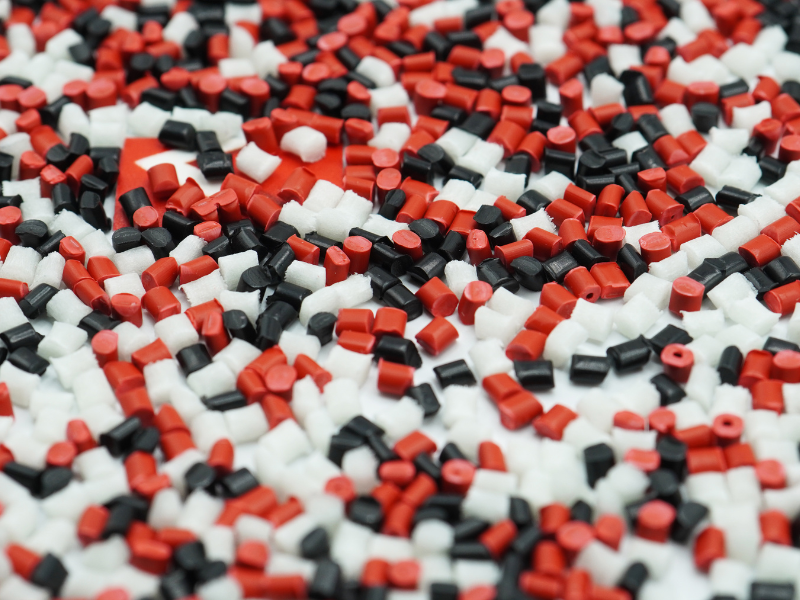
EuroPlas Engineering Plastic Compound
Our engineering plastic compounds are meticulously formulated to meet the stringent requirements of diverse industries. EuroPlas offers compounds with exceptional strength, impact resistance, chemical resistance, and heat resistance. These compounds are widely used in automotive components, electrical appliances, industrial parts, and other applications where superior performance is paramount.
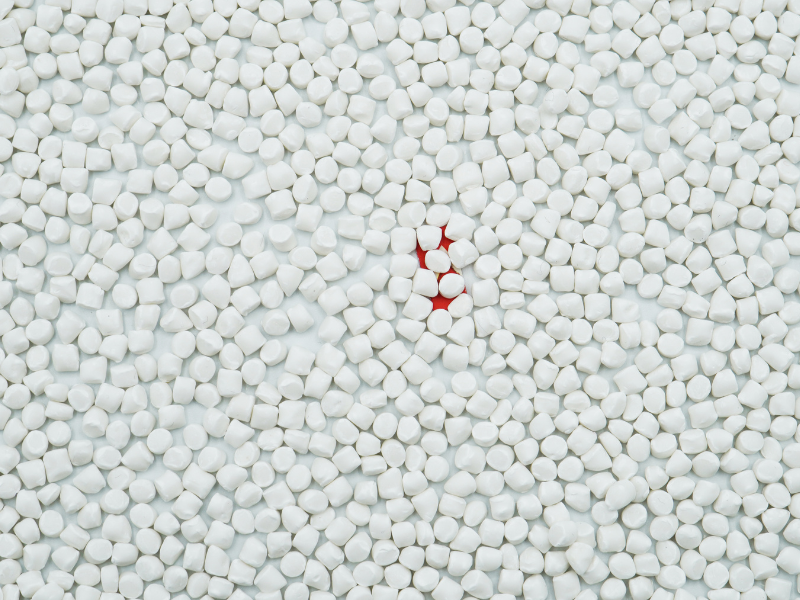
EuroPlas Filler Masterbatch
EuroPlas's filler masterbatch is made of PE or PP resin blended with calcium carbonate (CaCO3) and additives like wax and oil. It enhances mechanical properties, improves dimensional stability, and achieves desired weight reduction in plastic materials. Our high-quality filler masterbatch offers cost-efficiency without compromising quality, making it an ideal choice for various applications.
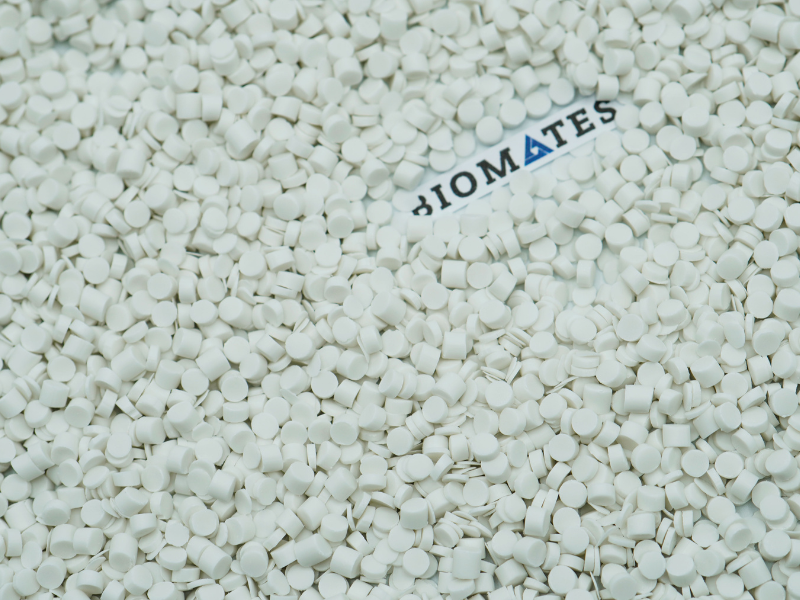
EuroPlas Bio Filler
EuroPlas bio filler products provide sustainable alternatives for enhancing the properties of plastic materials. Derived from renewable resources, our bio fillers improve tensile strength, impact resistance, and stiffness. Manufacturers can create environmentally-friendly products without sacrificing performance, making them an ideal choice for eco-conscious applications.
At EuroPlas, we prioritize quality, innovation, and customer satisfaction. Our team of experts works closely with clients to understand their specific requirements and deliver customized masterbatch solutions. With our state-of-the-art manufacturing facilities and rigorous quality control measures, we ensure that our masterbatch products meet the highest industry standards.
If you are looking for high-quality products, EuroPlas is here to be your trusted partner. Contact us today to discuss your specific requirements, and let our team assist you in finding the perfect solution for your application.