In the world of plastics, Thermoplastic Olefin (TPO) stands out as a remarkable and environmentally conscious option. This innovative material combines the best of both worlds: the durability of traditional plastics and the eco-friendly characteristics of natural materials.
In this guide, we will delve into the diverse applications, advantages, and environmental considerations surrounding TPO plastic. Whether you're a sustainability enthusiast, a materials science aficionado, or simply curious about the latest advancements in the field, join us as we unravel everything you need to know about TPO plastic.
1. What is TPO plastic?
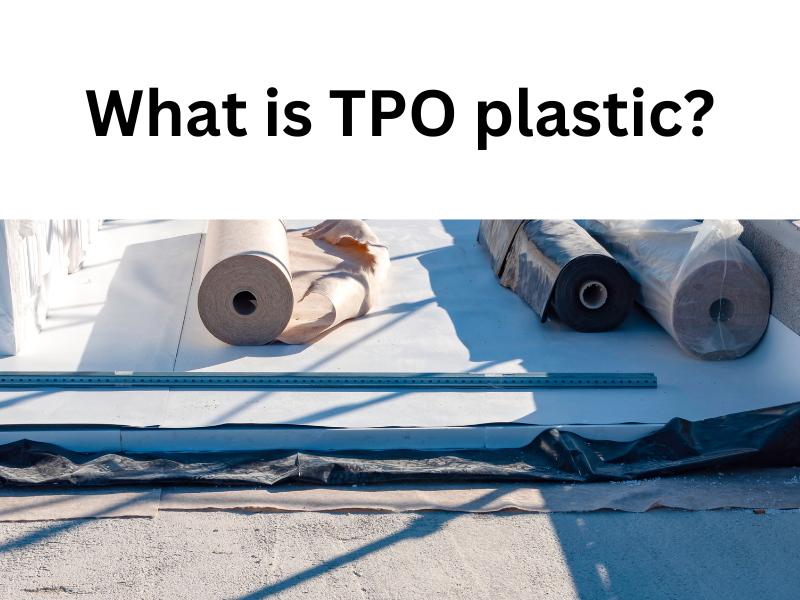
TPO plastic definition, is a versatile material known for its durability and flexibility. It's created by blending polypropylene and ethylene-propylene rubber, resulting in a composite that combines the strength of plastic with the elasticity of rubber. TPO plastic is resistant to UV radiation, chemicals, and extreme temperatures, making it a popular choice for various applications including automotive parts, consumer products, and more. Its ease of processing through methods like injection molding has further elevated its widespread use. In essence, TPO plastic offers a reliable, cost-effective, and adaptable solution for a wide array of manufacturing requirements.
2. How is TPO plastic made
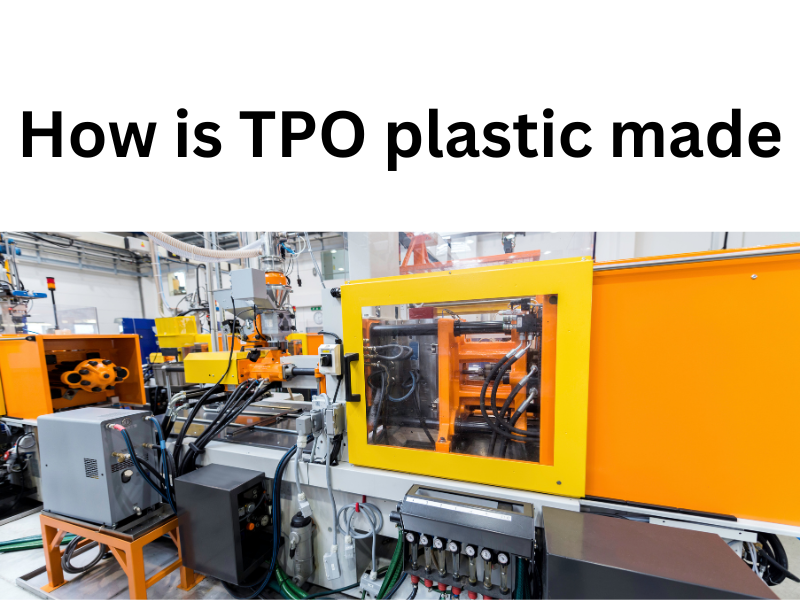
The manufacturing process of TPO (Thermoplastic Olefin) plastic involves a careful blending of materials to achieve its unique properties. TPO is synthesized through a combination of two main components: polypropylene (PP) and ethylene-propylene rubber (EPR/EPDM).
The process typically begins with the mixing of these components in precise proportions. Polypropylene, a thermoplastic polymer, provides the structural integrity and rigidity to the material. Ethylene-propylene rubber, on the other hand, contributes flexibility, impact resistance, and the elastomeric qualities that distinguish TPO from conventional plastics.
Once mixed, the composite is subjected to processes like extrusion or injection molding, depending on the desired end product. These methods allow for shaping TPO plastic into various forms, from sheets used in roofing to intricate automotive parts.
The result is a durable, weather-resistant, and versatile material suitable for a wide range of applications across industries. Its blend of plastic and rubber attributes makes TPO plastic a remarkable choice for modern manufacturing needs.
3. Advantages and Disadvantages of TPO plastic
3.1. Advantages of TPO plastic
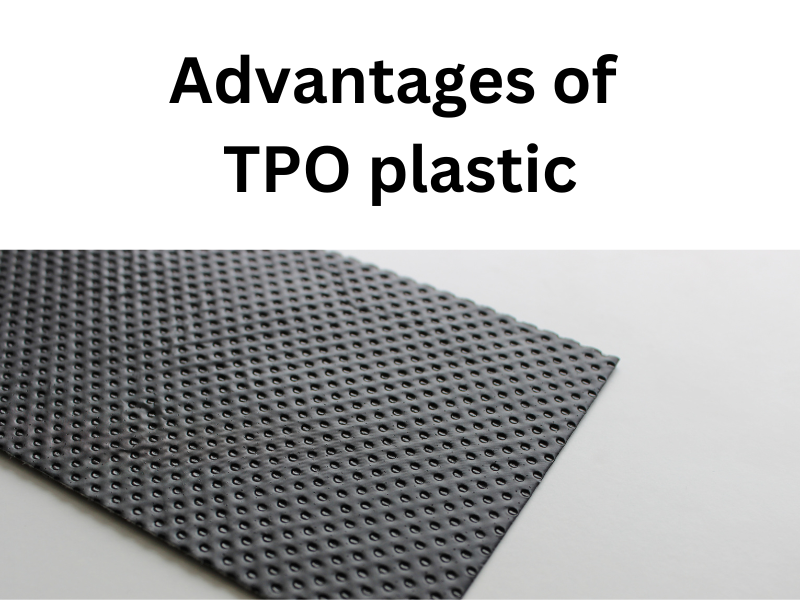
TPO (Thermoplastic Olefin) plastic offers a host of advantages that make it a preferred choice in various industries. Its unique composition of polypropylene and ethylene-propylene rubber results in several key benefits:
- Durability: TPO plastic's robust nature makes it highly resistant to impacts, tears, and punctures, ensuring longevity in demanding applications.
- Weather Resistance: Its exceptional resistance to UV radiation, extreme temperatures, and chemicals makes TPO ideal for outdoor use, from automotive components to roofing materials.
- Cost-Effectiveness: TPO's blend of properties provides a cost-effective solution, as its production costs are often lower compared to other materials with similar attributes.
- Easy Processing: The material can be easily processed through methods like injection molding and extrusion, reducing manufacturing complexities.
- Lightweight: TPO's relatively low weight contributes to fuel efficiency in automotive applications and simplifies installation in construction projects.
- Design Flexibility: Its versatility allows for various shapes and forms, enabling intricate designs for both functional and aesthetic purposes.
- Recyclability: TPO plastic's recyclable nature aligns with sustainable practices, minimizing environmental impact.
Overall, the advantages of TPO plastic underscore its role as a versatile and reliable material choice across a wide spectrum of industries.
3.2. Disadvantages of TPO plastic

While TPO (Thermoplastic Olefin) plastic boasts numerous advantages, it's important to also consider its limitations:
- Limited High-Temperature Resistance: TPO plastic may experience softening or deformation at high temperatures, which can restrict its use in applications exposed to extreme heat.
- Lower Chemical Resistance: Although TPO displays good resistance to many chemicals, it might not be suitable for environments with highly aggressive chemical exposure.
- Surface Appearance: In some cases, TPO's surface can be prone to scratches or scuffing, potentially affecting its visual appeal over time.
- Complex Recycling: Despite being recyclable, the blend of materials in TPO plastic can make the recycling process more challenging compared to single-material plastics.
- Material Variation: The properties of TPO plastic can vary based on the specific blend used, leading to inconsistent performance if not carefully managed during production.
- Limited Color Options: TPO plastics might have fewer color options compared to other plastics, which could impact certain design preferences.
It's crucial to weigh these disadvantages against the benefits to determine whether TPO plastic is the right choice for a given application. Careful consideration of the material's characteristics will ensure its suitability and optimal performance.
4. TPO material’s application
TPO (Thermoplastic Olefin) material stands as a versatile solution with a multitude of applications spanning various industries. Its unique blend of characteristics makes it a sought-after choice for a wide range of products and components.
4.1. Automotive Industry:
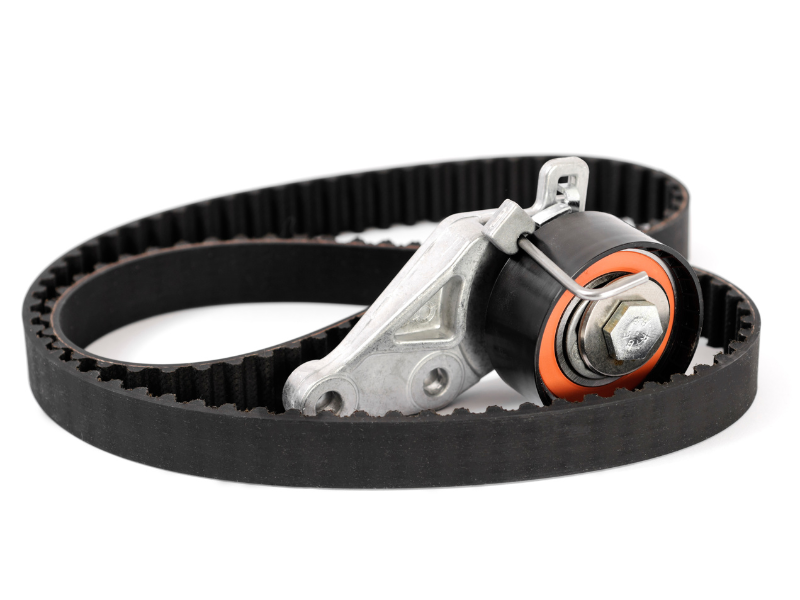
TPO's durability, impact resistance, and lightweight nature make it a staple in the automotive sector. It's commonly used for crafting exterior components like bumpers, body panels, and trim due to its ability to withstand harsh weather conditions and minor collisions. Its adaptability to color customization further enhances its appeal.
4.2. Construction Sector:

In the construction industry, TPO plays a crucial role in roofing membranes. Its resistance to UV radiation, water, and chemicals ensures longevity and efficient waterproofing, making it an optimal choice for both residential and commercial roofing applications.
4.3. Consumer Goods:
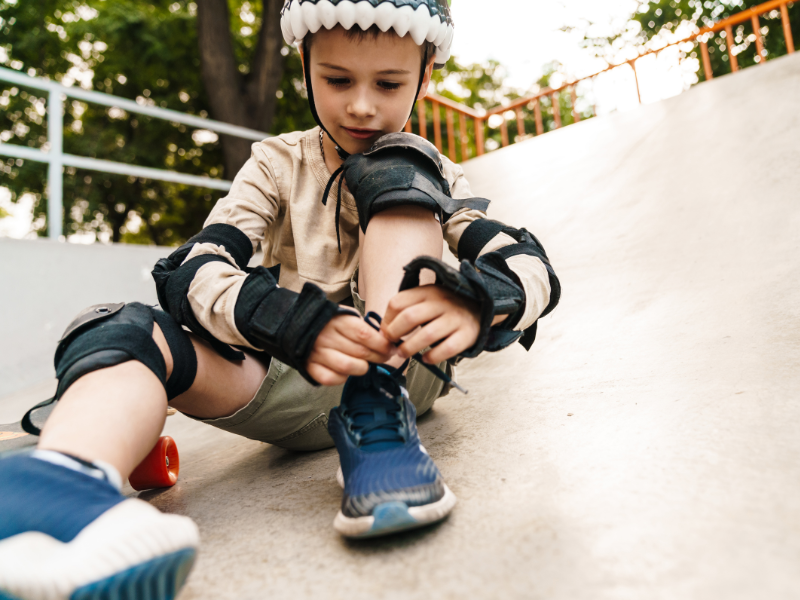
TPO's balance between flexibility and strength finds a niche in the creation of consumer products. Protective cases for electronics, sporting equipment, and recreational gear benefit from TPO's ability to absorb impact and provide reliable protection.
4.4. Medical Applications:
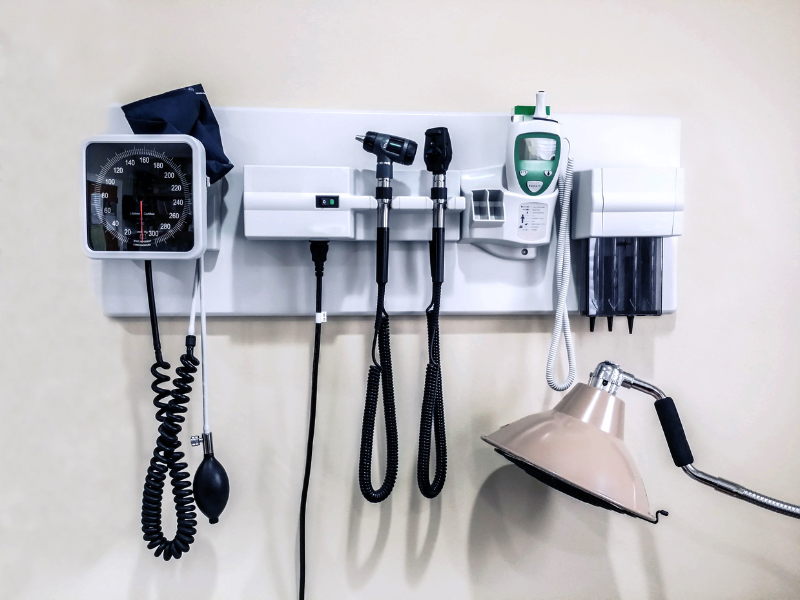
The medical field leverages TPO material's properties for a variety of uses, including manufacturing equipment housings, tubing, and gaskets. Its resistance to chemicals, combined with ease of sterilization, makes it a suitable material for healthcare environments.
4.5. Sustainable Solutions:
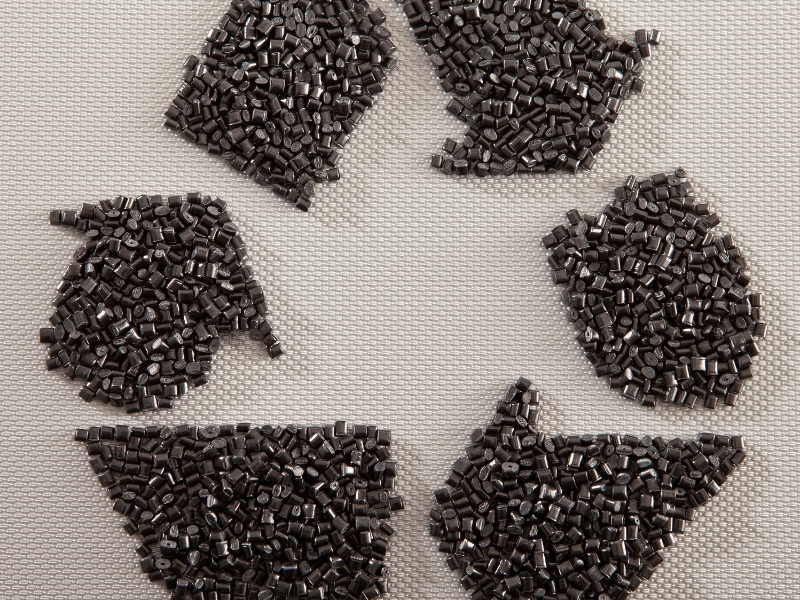
TPO's recyclability aligns with sustainability goals. Its use in various industries contributes to reducing environmental impact by promoting recycling and reducing waste.
In essence, TPO material's wide array of applications showcases its adaptability and reliability as a material choice. Its ability to combine strength, durability, and cost-effectiveness makes it a favored option for industries seeking versatile solutions for their manufacturing needs.
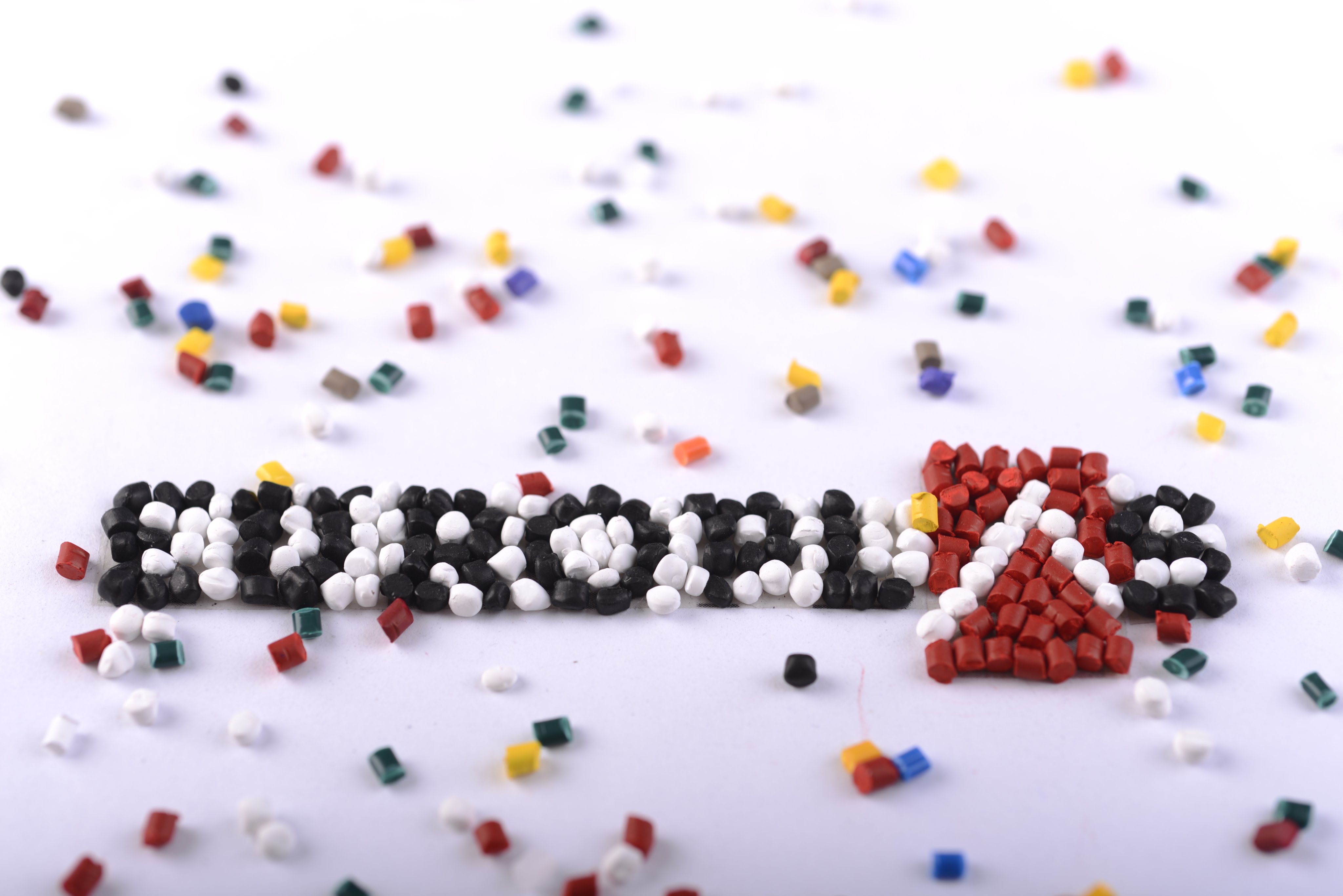
EuroPlas is your trusted source for a comprehensive range of high-quality plastic solutions, designed to meet various industrial requirements while upholding our commitment to sustainability.
- Filler Masterbatch: Revolutionize your plastic production with EuroPlas' filler masterbatch – a cost-effective solution that enhances properties like stiffness, heat resistance, and opacity. By substituting a portion of virgin resin with materials like calcium carbonate or talc, it reduces production costs. This versatile masterbatch finds applications in blowing films, injection molding, extrusion, and thermoforming across diverse industries.
- Bio Filler: Embrace eco-friendliness with EuroPlas' bio filler, an innovative product that accelerates plastic biodegradability within a year. Composed of natural starch and biodegradable additives, our bio filler is compatible with conventional and bioplastic resins. This makes it an excellent choice for eco-conscious applications such as food packaging, disposable tableware, and agricultural films.
- Color Masterbatch: EuroPlas recognizes the importance of visual appeal. Our color masterbatch ensures precise and consistent colors for a variety of plastic products. Incorporating high-quality pigments and additives, it can be seamlessly blended with different resins, making it suitable for toys, household appliances, cosmetics, and more.
- Plastic Additives: Enhance production efficiency and product functionality with EuroPlas' plastic additives. Our comprehensive range includes slip, anti-block, anti-static, anti-oxidant, and UV stabilizer agents. Widely used in films, pipes, and cables, these additives improve product performance and longevity while also minimizing waste.
- Engineering Plastic Compound: Achieve outstanding performance with EuroPlas' engineering plastic compounds – versatile solutions that combine engineering resins with various additives. These compounds enhance mechanical, thermal, electrical, optical, and chemical properties of plastic products, making them essential for industries like automotive, electronics, and medical devices.
With a wealth of experience spanning over 15 years, EuroPlas proudly exports innovative solutions to customers across 85+ countries. Leveraging unique natural resources and cutting-edge technology, we craft tailored products that cater to a wide array of industries and applications.
For more details about our exceptional product range, please visit our website or get in touch with us directly. Join hands with EuroPlas to shape a more sustainable future through advanced plastic solutions.