Discover how UHMWPE can revolutionize automotive components. This high-performance plastic offers a multitude of benefits, including exceptional strength, durability, and wear resistance. In this article, we will explore the advantages of using UHMW-PE in the automotive industry and discuss its applications in various components.
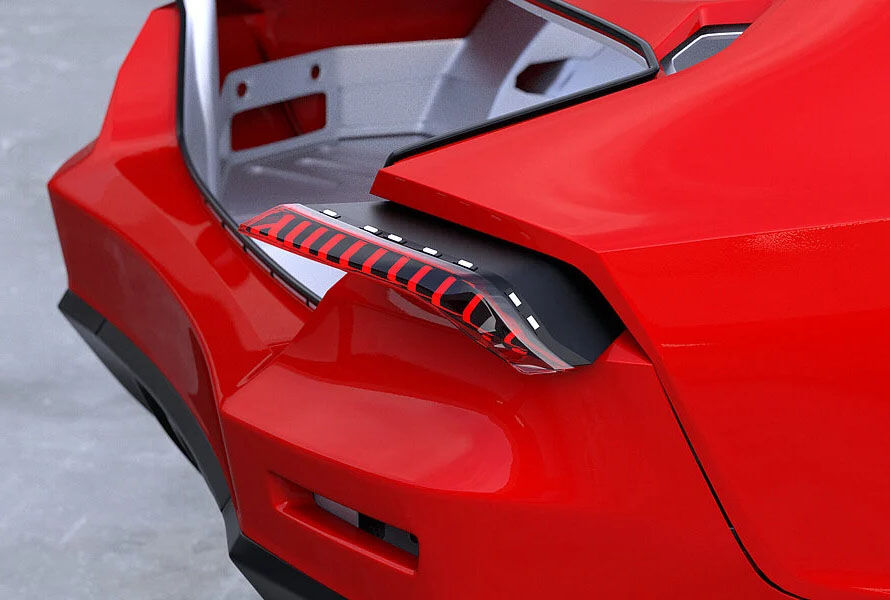
UHMW-PE offers numerous advantages in the automotive industry, highlighting its applications across a variety of components
1. What is UHMWPE?
UHMWPE, or Ultra-High Molecular Weight Polyethylene, is a specialized type of plastic renowned for its exceptional strength, durability, and resistance to wear and tear. This remarkable property stems from its unique molecular structure, with extremely long molecular chains that are much longer chains compared to standard polyethylene, and a molecular weight exceeding 3 million g/mol. This translates to a material that can withstand significant impact and friction, making it highly desirable for a wide range of applications across various industries.
Beyond its physical strength, UHMWPE boasts several additional benefits. It possesses a very low friction coefficient, minimizing resistance during movement and making it ideal for components like bearings and gears. UHMW-PE is also highly resistant to a broad spectrum of chemicals, allowing it to function effectively in harsh environments. While its coefficient of friction is comparable to PTFE (Teflon), UHMWPE's superior abrasion resistance sets it apart.
With its impressive combination of strength, chemical resistance, and low friction, UHMWPE offers a versatile and reliable solution for demanding applications.
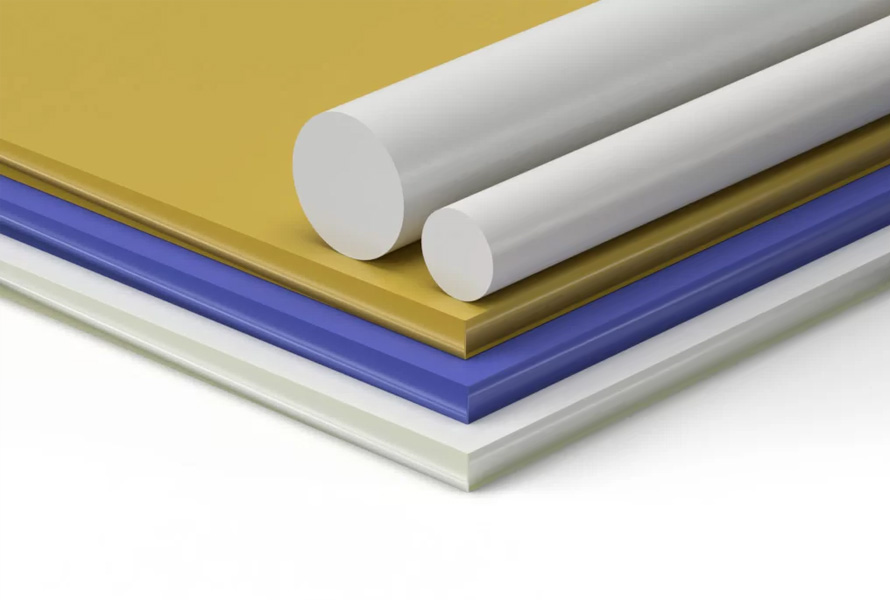
UHMWPE, short for Ultra-High Molecular Weight Polyethylene, is a unique plastic celebrated for its remarkable strength, durability, and outstanding resistance to wear and abrasion.
2. Key Benefits of UHMWPE in Automotive Applications
2.1. Benefits from UHMWPE's Molecular Structure and Properties
The unique molecular structure of UHMWPE makes it particularly advantageous for automotive applications.
- Exceptional Durability: Its high molecular weight results in outstanding durability, allowing it to withstand significant stress and strain without deformation. This robustness is crucial for automotive components that encounter heavy loads and repetitive motion, ensuring longevity and reliability in demanding conditions.
- High Impact Resistance: UHMWPE can absorb and dissipate energy upon impact, reducing the risk of damage and enhancing vehicle safety.
- Abrasion Resistance: UHMWPE’s impressive abrasion resistance protects parts from wear, prolonging their operational life and reducing maintenance needs
2.2. Advantages of UHMWPE Compared to Traditional Automotive Materials
UHMWPE offers several compelling advantages over traditional automotive materials such as metals and standard plastics. These benefits make UHMWPE an increasingly popular choice in automotive manufacturing.
- Superior Wear Resistance: UHMWPE's high molecular weight enables it to withstand abrasion and mechanical stress better than traditional materials.
- Enhanced Safety: The high impact resistance of UHMWPE enables it to absorb and dissipate energy effectively during collisions, enhancing passenger safety. Unlike traditional materials that may shatter into sharp fragments, UHMWPE’s non-splintering nature minimizes injury risks, making it a safer choice for critical parts like bumpers and dashboard panels.
- Lightweight and Fuel Efficiency: The lightweight nature of UHMWPE contributes to improved fuel efficiency and overall vehicle performance.
- Chemical and Corrosion Resistance: UHMWPE maintains its integrity in harsh environments, ensuring the longevity and reliability of automotive parts.
2.3. Advantages of Vehicle Safety Components
UHMWPE’s role in vehicle safety components is also paramount. Its ability to absorb energy during impacts enhances the effectiveness of safety features like bumpers and dashboards, ensuring they remain intact and functional in the event of a collision. This energy absorption capability is critical for protecting passengers and reducing the likelihood of injury.
Moreover, UHMWPE's resistance to wear and tear helps components made from UHMWPE maintain their integrity over time, and ensures the long-lasting performance of safety components like bumpers and dashboards.
2.4. Benefits of Longevity and Maintenance
- Reduced Maintenance: UHMWPE's durability and resistance to chemicals minimize the need for frequent replacements and repairs.
- Cost Savings: The material’s longevity and low maintenance requirements lead to cost savings over the lifespan of the vehicle, benefiting both consumers and manufacturers through reduced operational expenses and increased profitability.
2.5. Environmental and Economic Benefits
The environmental and economic benefits of UHMWPE are also noteworthy, including:
- Reduced Carbon Footprint: Utilizing UHMWPE will reduce vehicle weight, lower emissions, as lighter cars need less fuel and produce fewer greenhouse gas.This supports global climate initiatives and helps meet stricter environmental standards, enhancing efficiency and sustainability for new energy vehicles.
- Reduce waste from the automotive industry: UHMWPE’s durability results in fewer component replacements over the vehicle's life, minimizing the environmental impact of manufacturing and disposing of automotive parts.
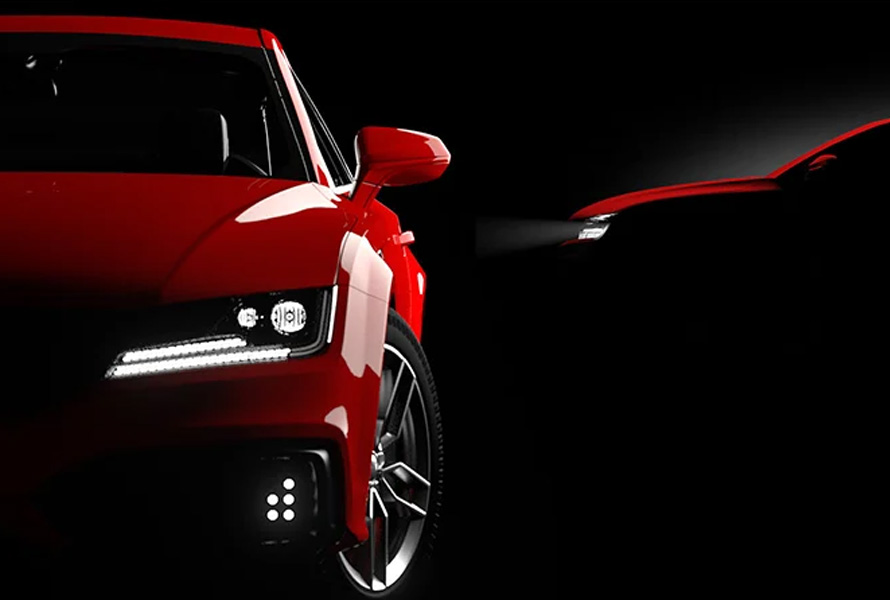
The distinctive molecular structure of UHMWPE provides significant advantages for its use in automotive applications
3. Applications of UHMWPE in the Automotive Industry
UHMWPE is a versatile material with numerous applications in the automotive industry due to its exceptional properties. Here are some key areas where UHMWPE is used:
3.1. New Energy Vehicle Applications
UHMWPE is highly versatile in new energy vehicles (NEVs), where its lightweight nature is essential for improving efficiency. It is utilized in critical components such as battery casings, cooling systems, and underbody shields, benefiting from its high impact resistance and chemical stability. This allows manufacturers to create more durable and efficient vehicles that can withstand the unique demands of electric propulsion.
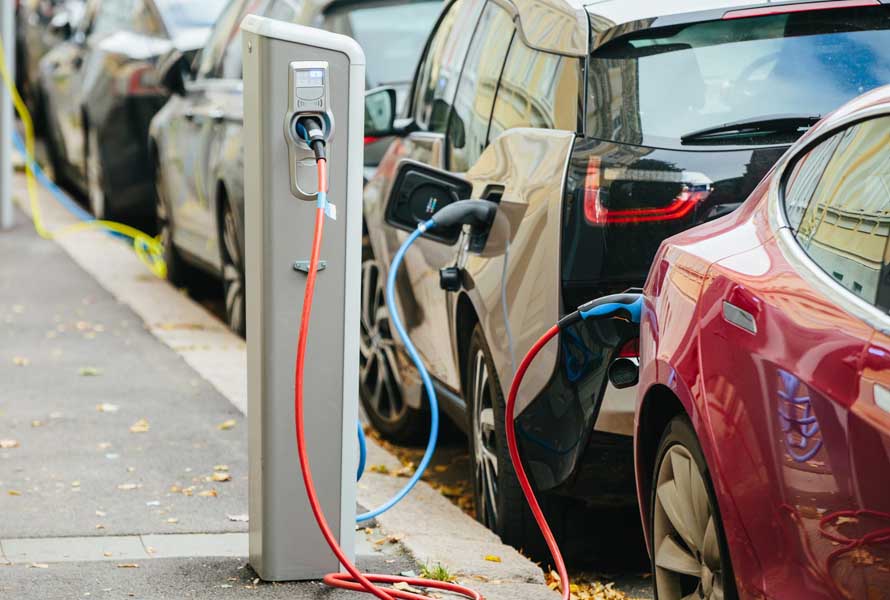
UHMWPE's lightweight, durable, and impact-resistant properties make it vital for NEV components
3.2. Applications in Automotive Interiors
In automotive interiors, UHMWPE enhances both functionality and comfort. Its durability makes it an excellent choice for high-wear components like dashboards and seat backs, ensuring they remain attractive and intact despite frequent use. Additionally, its lightweight properties aid in overall vehicle weight reduction, contributing to improved fuel efficiency while allowing for innovative ergonomic designs that enhance passenger comfort.
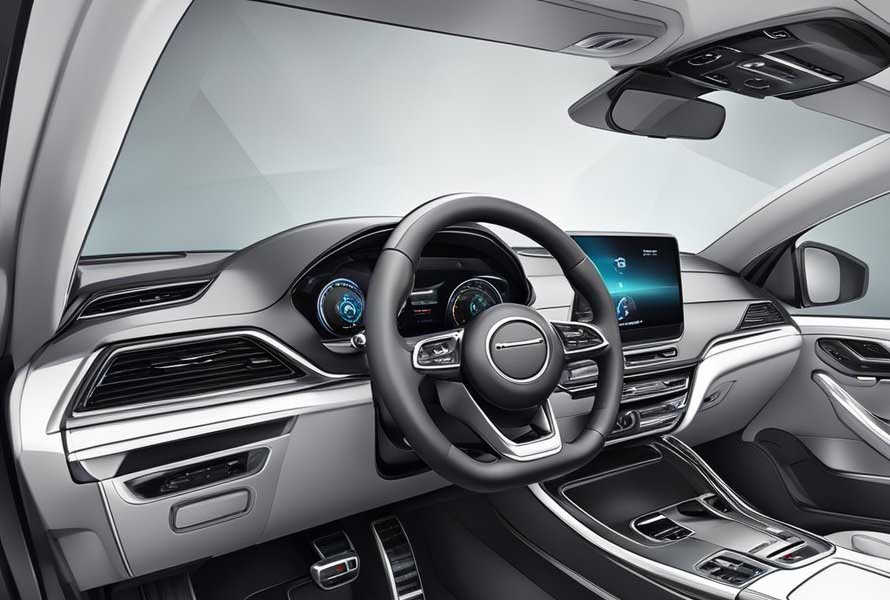
Used in automotive interiors, UHMWPE boosts comfort, durability, and reduces vehicle weight.
3.3. Applications for High-Stress Components
UHMWPE excels in high-stress automotive components where durability and impact resistance are paramount. Its ability to absorb shock ensures these parts can withstand rigorous conditions without failure.
- Gears and Bearings: Maximizing efficiency and reducing energy loss, UHMWPE’s low friction coefficient and wear resistance make it ideal for gears and bearings.
- Bushings and Liners: UHMWPE bushings and liners provide a smooth and durable interface between moving parts, reducing friction and wear.
- Bumpers: Protecting vehicles and passengers in collisions, UHMWPE's high impact resistance and energy absorption capabilities make it suitable for bumpers and other safety components.
- Dashboard Panels: Utilizing UHMWPE in dashboard panels provides a durable and impact-resistant surface.
Door Panels and Side Impact Beams: Absorbing energy and protecting passengers, UHMWPE is ideal for these critical safety components.
- Conveyor Belts and Rollers: Providing abrasion and chemical resistance, UHMWPE is suitable for conveyor belts and rollers in automotive manufacturing plants.
- Fuel Tanks and Chemical Containers: Offering excellent chemical resistance, UHMWPE is a good choice for fuel tanks and other containers that encounter corrosive substances.
- Other Components: UHMWPE can also be used in various other automotive components, such as gears, sprockets, pulleys, and seals.
4. Challenges in Using UHMWPE
While UHMWPE offers numerous advantages in automotive applications, its use is not without challenges. Understanding these limitations is crucial for manufacturers to effectively integrate this material into their designs and optimize its performance.
4.1. Low Melting Point
UHMWPE has a relatively low melting point compared to other engineering plastics, which can lead to thermal instability in high-temperature environments. This characteristic makes it unsuitable for applications that involve significant heat exposure, as the material may deform or lose its structural integrity. As a result, careful consideration of operating conditions is essential to avoid potential failures.
4.2. Processing Challenges
UHMWPE's high molecular weight offers exceptional strength and durability. However, this same property creates a hurdle during processing. Unlike many plastics that melt and readily flow into molds, UHMWPE has a relatively low melting point. At this temperature, the material doesn't melt uniformly, making it unsuitable for traditional injection molding techniques commonly used for plastic parts.
This necessitates the use of specialized processing techniques like extrusion and compression molding to achieve the desired shapes. These specialized techniques can add complexity and potentially increase manufacturing costs.
4.3. Cost Considerations
While UHMWPE offers long-term cost benefits due to its durability and reduced maintenance needs, the initial cost of the material can be higher compared to standard plastics, particularly for high-purity grades.
4.4.Recycling Challenges
While generally considered environmentally friendly, UHMWPE's disposal and recycling raise some concerns. Traditional recycling methods might not be as efficient for UHMWPE due to its unique properties.
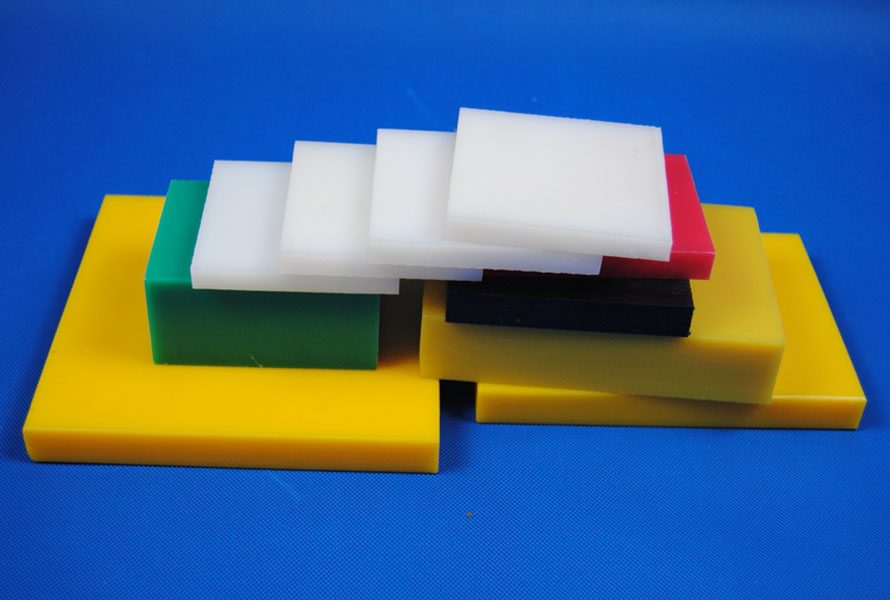
UHMWPE offers automotive benefits but faces challenges like low melting point, processing...
5. Future of UHMWPE in Automotive Applications
The future of UHMWPE in automotive applications looks promising. The automotive industry's relentless pursuit of lightweighting and fuel efficiency aligns perfectly with the strengths of UHMWPE. As electric and hybrid vehicles become more prevalent, the demand for advanced materials like UHMWPE is expected to rise, particularly in areas requiring robust performance under varied operational conditions.
Advancements in UHMWPE composites and blends will lead to even lighter and more robust components, contributing to improved vehicle performance and reduced emissions. This could encompass everything from battery casings and underbody shields in electric vehicles to lighter chassis parts and body panels in traditional vehicles.
Market analyses indicate a significant increase in the UHMWPE market within the automotive sector, fueled by innovation and advancements in processing techniques. Advances in processing techniques for UHMWPE are also expected to unlock a wider range of functionalities and design possibilities. New methods like additive manufacturing (3D printing) could enable the creation of complex and customized components with UHMWPE, enhancing both design freedom and performance optimization.
Additionally, UHMWPE surface treatments and coatings might lead to improved properties like scratch resistance, paintability, and fire retardancy, further expanding its design capabilities in automotive interiors and exteriors.
Growing environmental concerns are pushing the automotive industry towards sustainable practices. The inherent durability and low maintenance needs of UHMWPE contribute to its environmental friendliness.
6. Conclusion
To sum up, the integration of UHMWPE into the automotive sector presents numerous benefits that cannot be overlooked. Its lightweight and durable characteristics enhance vehicle performance while minimizing maintenance requirements. Applications in various components underscore its versatility and reliability. As the industry shifts toward more sustainable practices, UHMWPE is becoming a crucial material for future automotive innovations. By adopting this high-performance polymer, manufacturers can achieve better efficiency and longevity in their products, appealing to a more environmentally conscious market.
7. About EuroPlas’ PE Products
EuroPlas has established itself as a leader in the polyethylene products not only in Vietnam but also in the international market, offering a diverse range of high-quality materials.
A standout product in their lineup is the PE filler masterbatch, which allows manufacturers to enhance the physical characteristics of their plastic products while optimizing production costs. By incorporating filler materials like CaCO3, enables manufacturers to reduce their reliance on virgin plastics. This approach not only lowers production costs but also potentially minimizes the environmental impact associated with virgin plastic production and disposal. This masterbatch provides excellent filler properties, contributing to improved mechanical strength and processing capabilities.
PE filler masterbatch enhances product properties like heat resistance, flexibility, impact strength, etc.
EuroPlas is committed to environmentally responsible practices, ensuring that its production methods are sustainable and align with global standards. Through continuous improvement and customer-focused solutions, EuroPlas aims to be a reliable partner in the PE products sector.
For more information about our products and how we can support your business, contact EuroPlas today!