In response to escalating environmental concerns and the global plastic crisis, the demand for alternatives to traditional plastics has surged. One promising solution is bioplastic from cassava starch—a biodegradable material derived from renewable plant sources. This article delves into the production process, advantages, and challenges of cassava-based bioplastics, highlighting their potential in a more sustainable world.
1. Understanding Bioplastic from Cassava Starch
Bioplastic from cassava starch is a biodegradable material created using starch extracted from the cassava root (Manihot esculenta), a crop widely cultivated in tropical regions such as Southeast Asia, Africa, and South America. This plant is easy to grow, thrives in poor soil, and requires minimal fertilizers, making it a sustainable agricultural source.
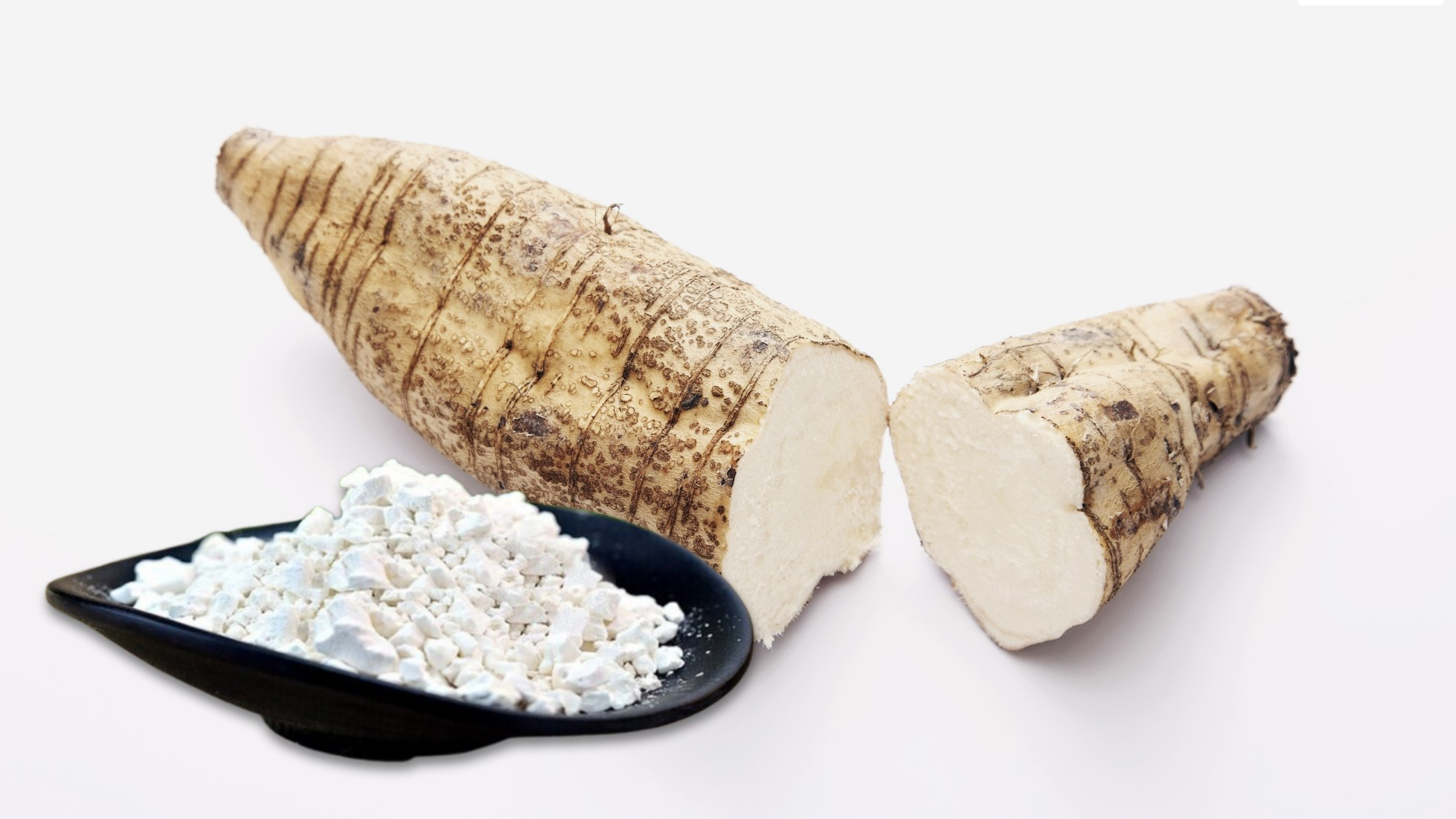
Bioplastic from cassava starch is a biodegradable material created using starch extracted from the cassava root.
Cassava starch is rich in amylose and amylopectin—polysaccharides capable of forming film-like materials when gelatinized and mixed with plasticizers like glycerol or sorbitol. These biofilms have properties similar to conventional plastic, including flexibility, transparency, and processability. Under composting conditions, bioplastic from cassava starch can decompose completely within 3–6 months, making it a highly attractive material in tackling plastic waste.
Besides its biodegradability, cassava-based bioplastic has physical characteristics that can be tailored for different applications. With proper formulation, it can be shaped, printed, and processed into various everyday products such as packaging, food containers, and disposable cutlery.
2. Production Process of Cassava Starch Bioplastic
The production of bioplastic from cassava starch involves several technical steps, requiring precise control to ensure consistent material quality.
First, fresh cassava roots are washed, crushed, and filtered to extract pure starch. This step is essential for eliminating impurities that could weaken the final product's mechanical properties. Next, the starch is mixed with water and plasticizers to form a gel. The type and amount of plasticizer used will determine the flexibility, tensile strength, and moisture resistance of the final bioplastic.
The resulting gel is heated to initiate starch gelatinization—breaking down starch granules and enabling molecular bonding with plasticizers. The mixture is then molded, cast, or rolled into sheets. Finally, it is dried to remove excess moisture and stabilize the material.
Researchers continue to enhance the base formulation by adding fibers like bamboo, coffee husk, or biodegradable polymers such as PLA to improve strength, elasticity, and water resistance.
3. Advantages of Cassava-Based Bioplastics
Bioplastic from cassava starch offers numerous environmental and economic benefits. Cassava, as a raw material, is renewable, fast-growing, and requires fewer agricultural inputs. This makes it ideal for sustainable bioplastic production.
Compared to petroleum-based plastics, cassava bioplastics generate lower greenhouse gas emissions and require less energy to produce. They are non-toxic, free from harmful additives, and safe for food contact and marine environments. More importantly, these bioplastics decompose quickly, leaving no microplastics behind.
Their structure is also versatile—manufacturers can adjust blends to create materials suitable for various industries, including food packaging, agriculture, medical supplies, and even disposable electronics components.
4. Challenges and Limitations
Despite its advantages, bioplastic from cassava starch faces several hurdles. The material’s mechanical properties are relatively weak—films tend to be brittle and degrade under humid conditions. This makes them unsuitable for products requiring long-term durability or water resistance without further treatment.
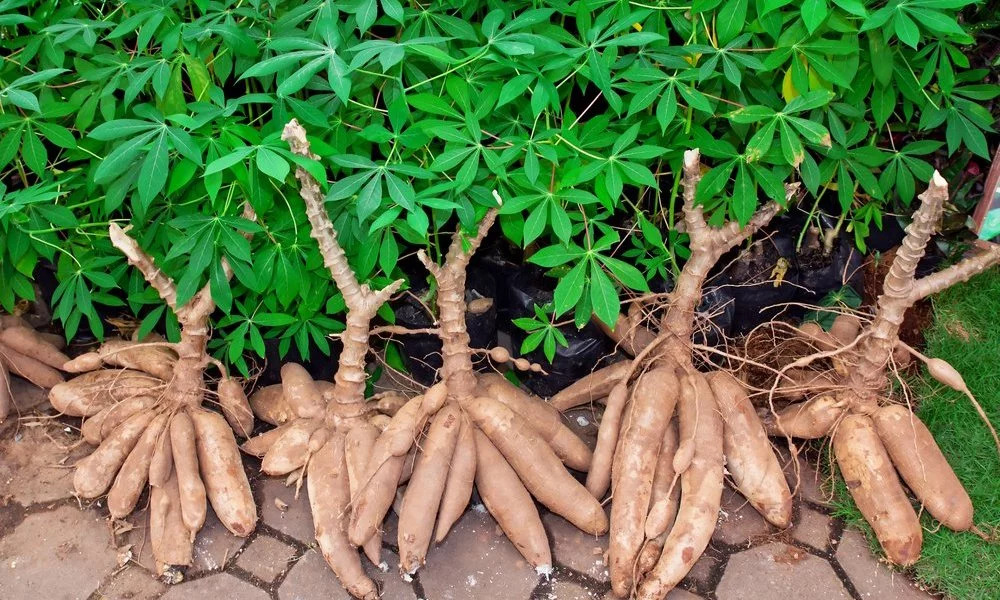
Despite its advantages, bioplastic from cassava starch faces several hurdles.
Another issue is competition with food crops. Cassava is a staple in many parts of the world, and increasing industrial demand may create pressure on farmland and food supplies.
Production costs are also higher compared to fossil-based plastics due to small-scale manufacturing and limited infrastructure. Finally, the lack of widespread industrial composting facilities limits the practical application of these biodegradable materials.
5. Current Applications of Cassava Bioplastics
Thanks to their biodegradability and safety, bioplastics from cassava starch are already used in multiple sectors. In packaging, they are used for biodegradable bags, food wrappers, and disposable containers—particularly for export businesses that must meet environmental compliance standards.
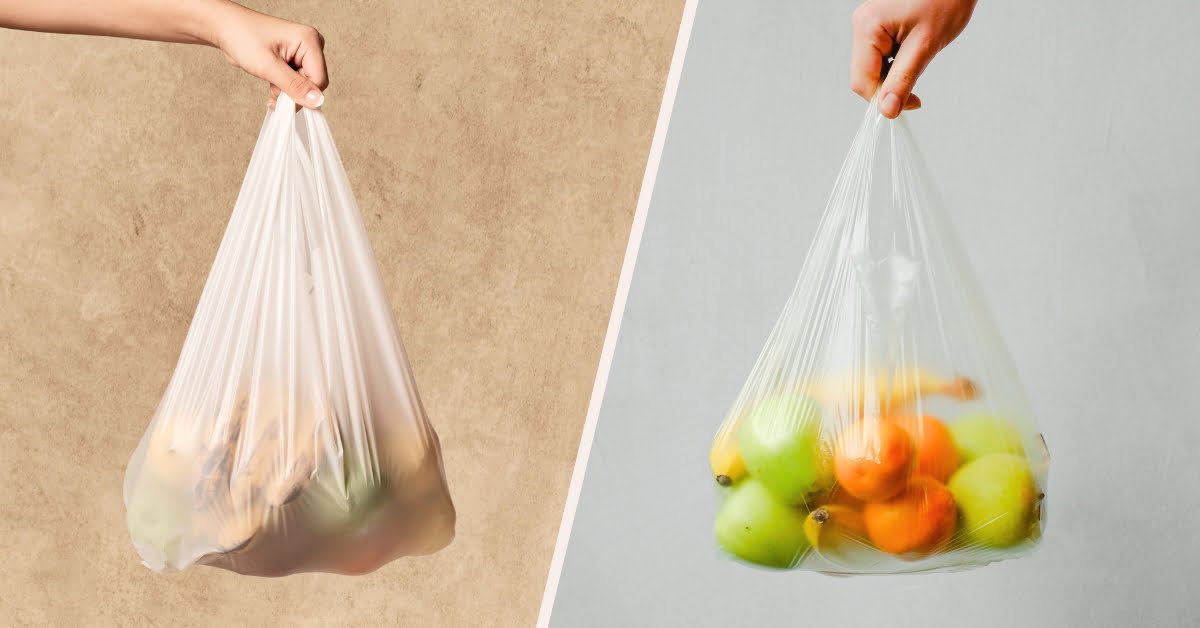
Thanks to their biodegradability and safety, bioplastics from cassava starch are already used in multiple sectors.
In agriculture, cassava mulch films can degrade naturally in soil after harvest, reducing plastic waste and labor costs. In food service, cassava-based utensils and straws are becoming common in cafes, restaurants, and eco-conscious chains.
The medical field also benefits from cassava bioplastics, applying them to disposable gloves, trays, and sterilized packaging in mobile clinics and remote regions.
6. Future Outlook
The future of bioplastic from cassava starch looks promising, especially with increasing policy pressure to ban single-use plastics and promote green alternatives. Incentives for eco-friendly materials and heightened consumer awareness further fuel the demand.
Research and innovation are key to improving the mechanical strength and water resistance of cassava bioplastics. Composite materials using PLA or PHA are under active development, allowing for broader industrial applications. Some startups are even exploring cassava bioplastics in 3D printing and automotive parts.
With collaborative efforts between governments, industries, and researchers, bioplastic from cassava starch could become a cornerstone material in the circular economy.
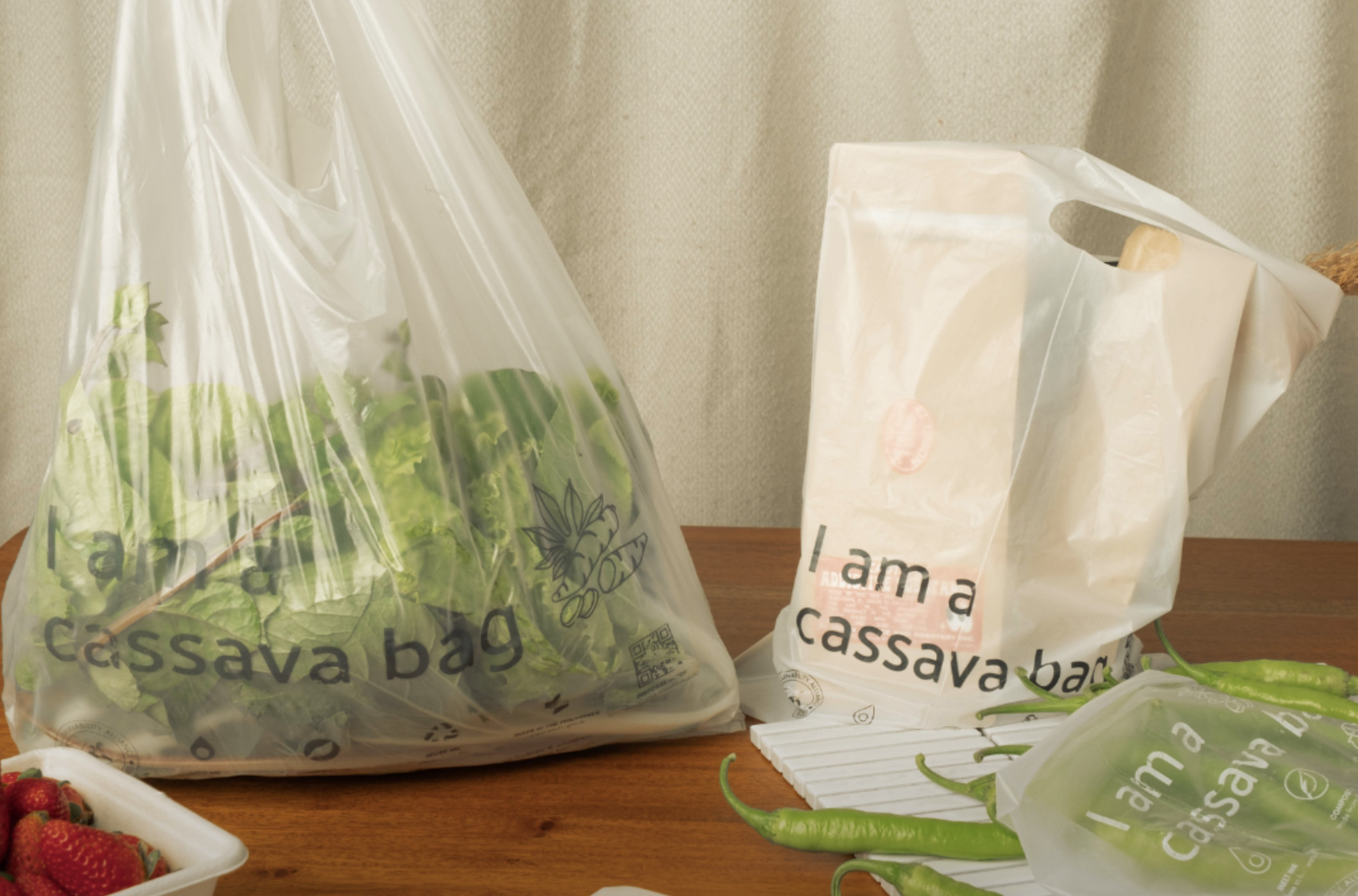
The future of bioplastic from cassava starch looks promising
7. Conclusion
Bioplastic from cassava starch represents a major advancement in the quest for sustainable materials. Although there are challenges related to strength, moisture sensitivity, and food competition, its environmental advantages make it a leading candidate for replacing traditional plastics in many applications. With ongoing innovation and support from industry leaders like EuroPlas, cassava-based bioplastics are poised to become an integral part of future green manufacturing.
8. About EuroPlas and BiONext
EuroPlas is one of the world’s leading plastic manufacturers, operating seven factories across Vietnam and Egypt with an annual capacity of 0,8 million tons. With a presence in over 95 countries, EuroPlas is committed to providing advanced and sustainable plastic solutions.
Among its six product lines, BiONext is the bioplastic compound brand that stands out. Developed using renewable feedstocks like PLA and PHA, and biodegradable co-polyesters such as PBAT, BiONext is tailored for industries seeking environmentally responsible alternatives. Although BiONext does not currently utilize cassava starch, it aligns with the same sustainability vision promoted by bioplastic from cassava starch initiatives.
Visit our Blog for the latest updates, or reach out directly via our Contact Page.