Currently, FRP plastic is commonly used in interior design, household appliances and electronic devices that require high technology. The article below will provide a detailed overview of information, advantages and disadvantages as well as practical applications of FRP plastic in life. Check it out now with EuroPlas!
1. Overview of FRP plastic
FRP has two main names: "Fiber Reinforced Polymer" or "Fiber Reinforced Plastic". This type of plastic is made up of two main components: polymer resin or plastic combined with fibers to thoroughly improve the properties of the material.
In particular, manufacturers use glass fiber to make reinforcing fibers. Besides, there are also many other fiber groups such as aramid fiber, carbon fiber or less commonly, cellulose plant fiber. Depending on the requirements of the material, people use different types of fibers with different tensile strengths and hardness.
FRP plastic is considered a small branch in the collection of synthetic composite materials and is divided into two different types based on the composition of the materials that make them up:
-
FRP has base materials of vinylester, polyester, epoxy resin, thermosetting resin. The substrates play a role in binding the reinforcements and helping them form a uniform mass to increase material durability.
-
FRP is reinforced with fibers such as: wood fiber, carbon fiber, glass fiber. This component will positively impact the physical and mechanical properties of FRP and help them withstand major impacts from external environmental factors.
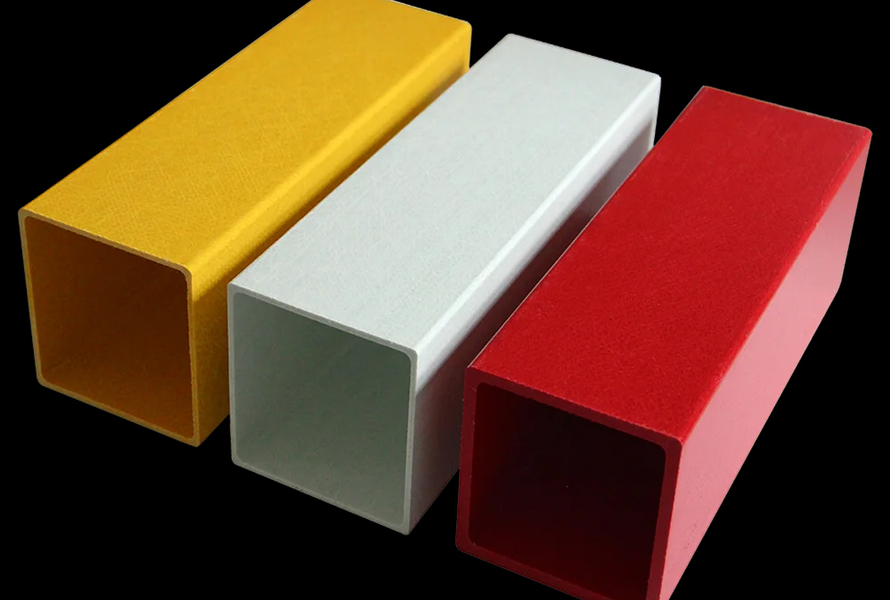
FRP plastic materials are applied in many fields.
This is general and basic information about FRP plastic materials. In the next section, EuroPlas will introduce to customers the advantages and disadvantages of this material.
2. Advantages and disadvantages of FRP plastic
The applicability of FRP plastics is quite high because they possess very flexible and popular advantages and are not inferior to the world's leading materials.
2.1. Advantages of FRP plastic
The most outstanding advantage of FRP is the material's hardness and blocky structure. This advantage is formed from the plastic base and a variety of reinforcing fibers such as glass, carbon or aramid fibers. Therefore, products made from FRP plastic have stable durability over a long period of time and can withstand impacts from environmental factors.
Hardness also helps FRP plastic possess the advantage of high bearing capacity. It is not an exaggeration to say that the block structure and reinforced fibers have pushed the durability and impact resistance of FRP plastic to a very high level. In addition, the surface of FRP plastic does a very good job of resisting abrasion when in contact and friction with other objects. Therefore, FRP plastic is applied in the automotive, marine or aerospace fields.
In addition, FRP plastic not only possesses stable mechanical properties but also has an equally good chemical structure because the material is resistant to chemicals and harsh environments. Therefore, FRP plastic can be used in the chemical industry or for materials research.
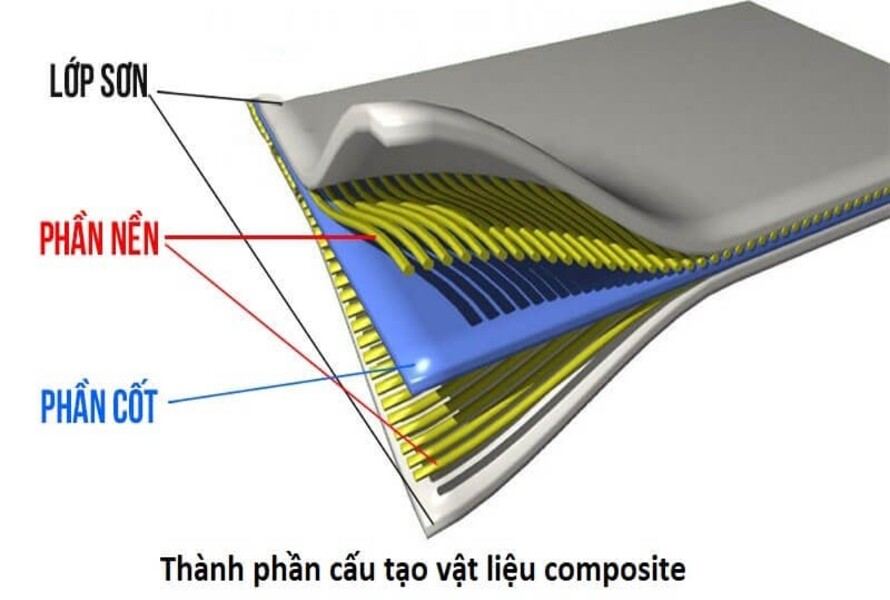
FRP plastic has high strength and durability thanks to its complex structure.
Because of the composition of structural fiberglass, FRP resin can be fireproof and heat resistant. The average heat resistance of FRP composite is from 100 - 150 degrees Celsius. Furthermore, FRP plastic can help manufacturers save quite a bit of cost because of its adaptability, ease of processing and soundproofing. Therefore, FRP plastic will increase safety when applied in heavy industrial fields.
As you saw in the overview of FRP plastics, they can be perfectly combined with fiberglass, carbon or aramid. Therefore, the flexibility and material adaptability of FRP plastic are evaluated very well. This will help manufacturers be more proactive and flexible in the manufacturing process, expand the application of materials as well as positively impact the cost of high-volume production.
2.2. Disadvantages of FRP plastic
In the opposite direction, FRP plastic also has its own disadvantages. The price of FRP plastic lines is not the same, for example: FRP plastic combined with carbon fiber will be 20 - 25 times more expensive than glass fiber FRP plastic.
The nature of FRP plastic is made up of many input materials: plastic base and reinforcing fibers. Therefore, they require quite high technical requirements from the manufacturer so as not to destroy the material structure and cause problems during the processing process. Not only that, these errors can greatly affect the aesthetics and functionality of the finished product.
The common characteristic of composite plastic materials is the complexity of their chemical, mechanical and physical structures because they are made up of many components. Therefore, the ratio of each component must be very precise so that composite plastic in general and FRP plastic in particular can maximize their performance.
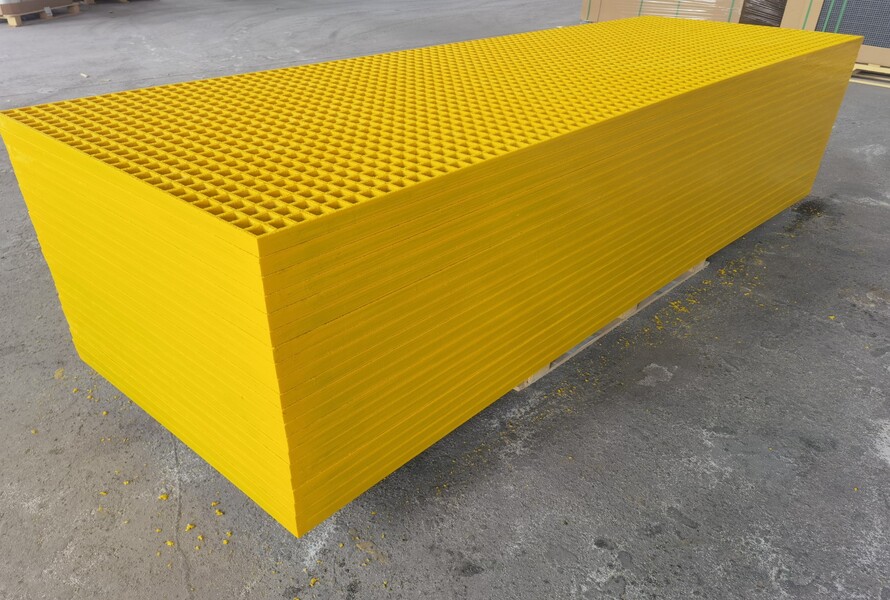
Application of FRP plastic into floor mats
To solve the above disadvantages, manufacturers must calculate costs and determine the quantity of input materials in as much detail as possible to avoid waste. Customers need to accurately plan the usage needs for each specific field to know which type of FRP plastic is suitable for that field. In addition, training and upgrading the skills of the workforce also plays an important role in the development strategy of Vietnam's plastic industry in general and composite materials in particular.
Despite its specific disadvantages, FRP plastics are also a suitable choice in many key industries today thanks to their optimal properties. EuroPlas will introduce to customers the practical applications in life of FRP plastic in the next section!
3. Application of FRP plastic
As EuroPlas introduced in the advantages section, FRP plastic is capable of being affected by chemicals without changing its physical and mechanical structure. Therefore, they are used in the medical field or in the production of liquid tanks.
In the automotive field, FRP plastic is used to produce bonnets, car wings and interior parts because they have surface durability, fire resistance and are safe for consumers' health.
In particular, the ability to withstand force, abrasion and heat helps FRP plastic be used in the space sector, typical examples are: space construction materials and aircraft parts.
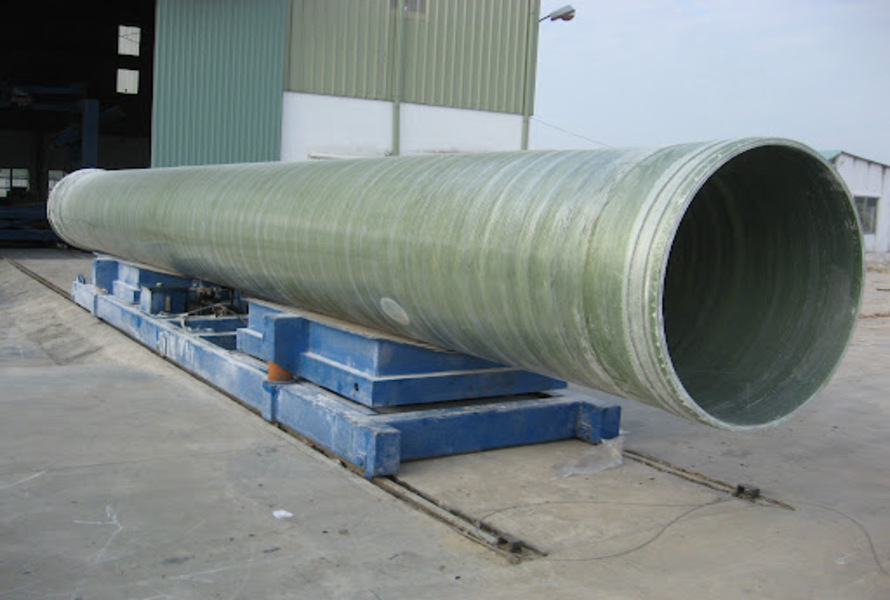
FRP plastic used to produce large industrial pipes
With reinforced glass fiber components, FRP plastic is not only waterproof but also very resistant to force. Therefore, they are materials used in the maritime industry to create boats, ships and ship parts.
FRP is used in the construction industry to create columns, beams and other materials, replacing traditional materials such as concrete and steel. FRP is also used to create load-bearing construction materials such as bridges, culverts and wall panels.
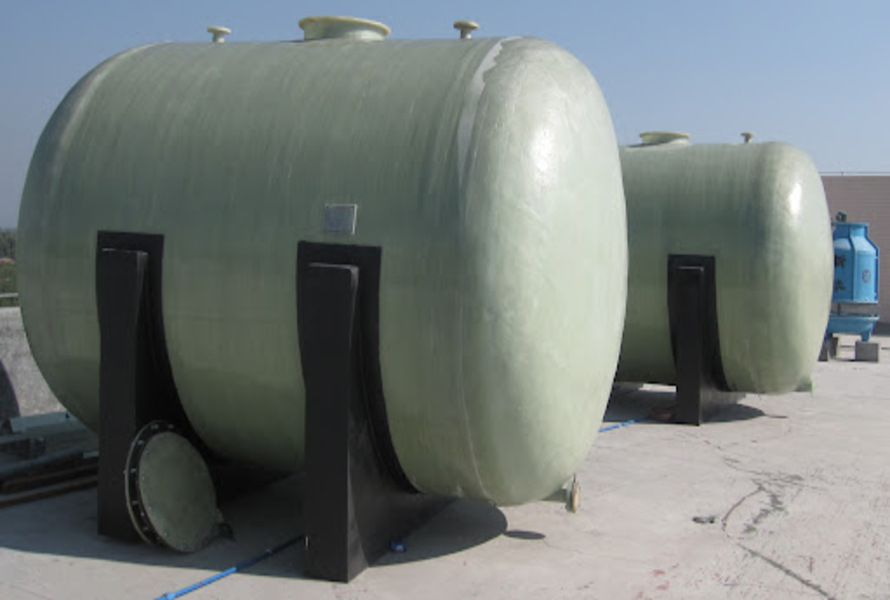
FRP plastic has high durability thanks to its complex structure.
4. Introduction to EuroPlas
The choice of fiberglass plays a core role in determining the overall quality of FRP plastic. Currently, EuroPlas is one of the suppliers of quality fiberglass and fully meets international standards. PA66 & PA6 Compound glass fiber is a group of engineering plastics made from PA66 & PA6 plastic base with glass fiber reinforcement.
PA66, PA6 fiberglass compound from EuroPlas has 30 - 50% glass fiber content. It is widely used in the production of gears, bearings, transmission belts, carburetor components, computer components or household electrical components.
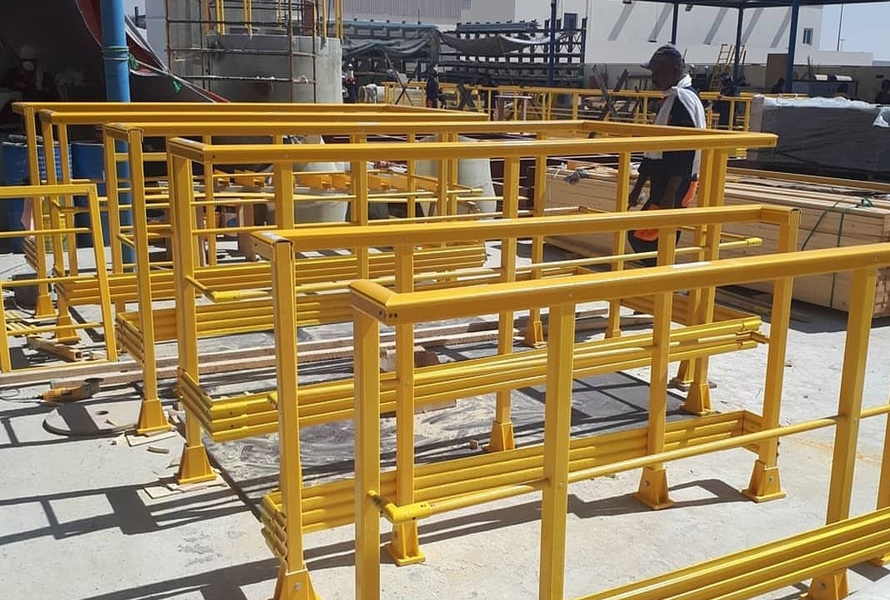
FRP plastic is used as reinforcement columns and frames in factories.
EuroPlas has always focused on product quality throughout the process since its establishment. In particular, EuP owns modern equipment such as extruders, blowers, injection molding machines,... along with standard measurement machinery systems such as heat strain gauges and impact resistance gauges. , tensile strength tester,... Thereby ensuring the highest product quality to customers.