Discover the exceptional properties of Nylon 6/12, a distinctive copolymer with a myriad of advantages. From its remarkable composition to its wide-ranging applications, this engineering resin boasts a unique blend of characteristics. Join us as we explore the diverse attributes and potential applications of PA 6/12, uncovering its true versatility in various industries.
1. What is Nylon 6/12?
Nylon 6/12, also known as Polyamide 6/12 or PA 612, is a copolymer with a distinct composition that sets it apart from other nylon materials. This stands as an engineering resin that occupies a unique position, combining the desirable attributes of Nylon 6 and Nylon 12. It offers a compelling alternative by delivering reduced moisture absorption compared to Nylon 6, while still presenting a more economical option compared to Nylon 12. C18H36N2O3 is the structure formula of Polyamide 6/12.
.jpg)
Structure formula of Polyamide 6/12
With a density ranging from 1.06 to 1.07 g/cm³ and a melting point of 218 degrees Celsius, nylon 6/12 possesses physical characteristics that enhance its overall performance. Its lightweight nature allows for versatility in applications without compromising strength or functionality. Additionally, the high melting point ensures thermal stability, enabling the material to withstand elevated temperatures without significant degradation.
Read more: Nylon 6: Definition, properties and common uses
2. The properties of PA 6/12
Nylon 6/12 exhibits several noteworthy properties that contribute to its widespread use
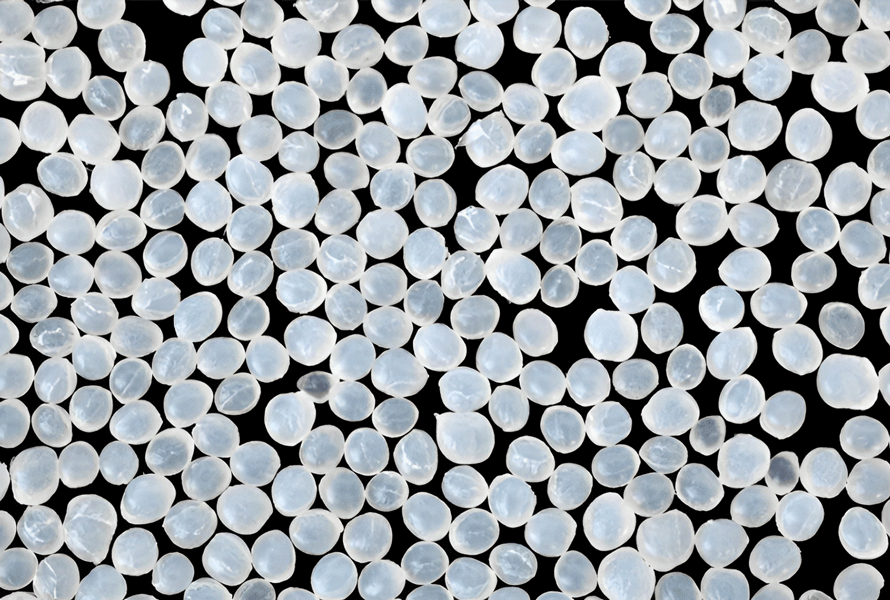
Polyamide 6/12
2.1. Mechanical Strength
One notable advantage of this material is its balanced mechanical properties. It combines strength, flexibility, and durability, making it suitable for various applications that require robust performance. Whether it's withstanding high levels of tension or enduring impact, nylon 6/12 demonstrates excellent mechanical strength.
2.2. Abrasion and chemical resistance
Nylon 6/12 exhibits exceptional resistance to abrasion and chemicals. This property makes it well-suited for applications where the material is exposed to harsh environments or corrosive substances. Its ability to withstand wear and tear over time contributes to its longevity and reliability.
2.3. Processability
Polyamide 6/12 is also known for its ease of processing. Its intermediate carbon chain allows for efficient manufacturing and shaping, making it a favorable choice for industries that require precise molding or fabrication. The material can be easily molded into various forms, such as fibers or pellets, to suit specific design requirements.
2.4. Moisture Resistance
Nylon 6/12 showcases reduced moisture sensitivity compared to other nylon variants. This property contributes to improved dimensional stability, meaning the material is less prone to swelling or warping when exposed to moisture or humidity. The reduced moisture absorption rate ensures that the material maintains its shape and properties over time.
2.5. Thermal Stability
With a relatively high melting point, nylon 6/12 demonstrates good thermal stability. It can withstand elevated temperatures without significant deformation or degradation. This characteristic is particularly advantageous in applications where exposure to heat or high temperatures is expected. PA 6/12's ability to retain its mechanical properties over a wide temperature range ensures its suitability for diverse operating conditions.
2.6. Electrical Insulation
It possesses excellent electrical insulation properties, making it a preferred choice for applications where electrical conductivity needs to be minimized. Its ability to effectively insulate electrical components helps prevent the unwanted flow of electricity and ensures the safe and efficient operation of electrical systems.
3. How to Produce Polyamide 6/12?
Nylon 6/12 is manufactured through the combination of two compounds (hexamethylenediamine and dodecanedioic acid) in a single precursor, similar to other nylon polymers that follow a two-number naming convention. Subsequently, this precursor undergoes polymerization to produce the final material.
The distinctive feature of Nylon 6/12 lies in the diacid component, which contains 12 carbon atoms. This molecular structure leads to increased spacing between the amide groups within the polymer chain. Consequently, PA 6/12 exhibits slightly lower mechanical characteristics and a reduced melting point compared to other nylon variations.
However, this alteration in molecular structure brings about a significant advantage. The increased spacing between the amide groups in Nylon 6/12 contributes to its improved resistance to moisture absorption. As a result, this particular nylon variant demonstrates heightened resistance to moisture, making it a preferred choice in applications where exposure to humidity or moisture is a concern.
Read more:
Pe vs nylon: Which one should be chosen?
4. Nylon 6/12's Applications
Nylon 6/12 finds a wide range of applications across various industries due to its unique combination of properties. Some notable applications include:
- Automotive Components: Polyamide 6/12 is used in the automotive industry for manufacturing various components such as fuel lines, tubing, engine covers, and gaskets. Its excellent chemical resistance and mechanical strength make it suitable for withstanding the demanding conditions of automotive systems.
.png)
Automotive Components
- Electrical Connectors: The electrical industry utilizes this type of materials for producing connectors and insulating components. Its electrical insulation properties, along with good dimensional stability, make it a reliable choice for ensuring the safe and efficient transmission of electrical signals.
- Industrial Parts: It is widely employed in the manufacturing of industrial parts such as gears, bearings, rollers, and bushings. Its high strength, wear resistance, and self-lubricating properties contribute to its effectiveness in heavy-duty applications.
- Consumer Goods: Nylon 6/12 is utilized in consumer goods manufacturing, including items like sporting equipment, handles, knobs, and various household products. Its durability, impact resistance, and aesthetic appeal make it a popular choice for these applications.
- Filament for 3D Printing: PA 6/12 is increasingly utilized as a filament material for 3D printing. Its excellent mechanical properties and resistance to moisture absorption make it a preferred choice for producing durable and functional printed objects.
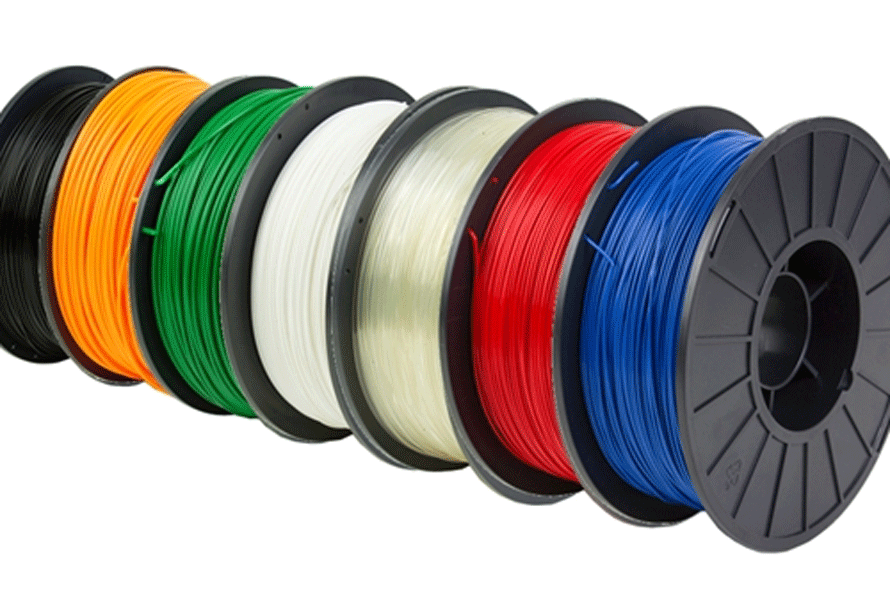
5. Can Nylon 6/12 Be Used in Plastic Injection Molding?
Yes. Polyamide 6/12 is well-suited for plastic injection molding applications. The process of injection molding involves melting the nylon 6/12 resin to a liquid state and injecting it into a mold cavity. Once cooled and solidified, this retains its shape and can be released from the mold as a finished plastic part.
Polyamide 6/12 is well-suited for plastic injection molding applications
The versatility in injection molding lies in its thermoplastic nature. It can undergo repeated heating and cooling cycles without significant degradation, allowing for efficient processing and recycling. This makes PA 6/12 a favorable choice for injection molding operations where material efficiency and recyclability are important factors.
Furthermore, this type of material can be enhanced with various additives to improve its properties for specific applications. For instance, the addition of glass fibers can increase tensile strength and stiffness, making it suitable for applications that require higher structural integrity. Other additives such as impact modifiers, flame retardants, UV stabilizers, and conductive materials can be incorporated to tailor the properties, enhancing its toughness, flame resistance, UV resistance, and conductivity.
By leveraging injection molding techniques and incorporating additives, manufacturers can produce nylon 6/12-based plastic parts with enhanced strength, durability, flexibility, and specific performance characteristics to meet the requirements of diverse applications.
6. About European Plastic Company
European Plastic Company is a reputable supplier of high-quality plastic materials for every business. We specialize in providing a diverse range of plastic materials, including filler masterbatch, engineering plastic compound, bioplastic compound, additives and among others. Our products are manufactured in state-of-the-art facilities and undergo rigorous quality control to ensure reliability and performance. We cater to various industries, offering materials suitable for automotive, electronics, packaging, construction, and more. With a customer-centric approach and a commitment to prompt delivery and technical support, EuroPlas is your trusted partner for all your plastic material needs.
Contact us now for further information!
Read more information here!