If you seek an engineering plastic renowned for high heat resistance, exceptional durability, and excellent electrical insulation, PPO plastic is the ideal choice. This material is steadily gaining prominence in the industry, offering groundbreaking solutions for applications demanding superior performance and longevity. So, what exactly is PPO plastic? How does it differ from the widely known PP plastic? Let's delve into the details with EuroPlas!
1. PPO Plastic Definition
PPO plastic is a high-grade thermoplastic engineering plastic belonging to the polyether polymer group, ranked among the top 5 most important engineering plastics globally. It is also known as PPE (Polypheylene Ether) or Polyphenylene Oxide.
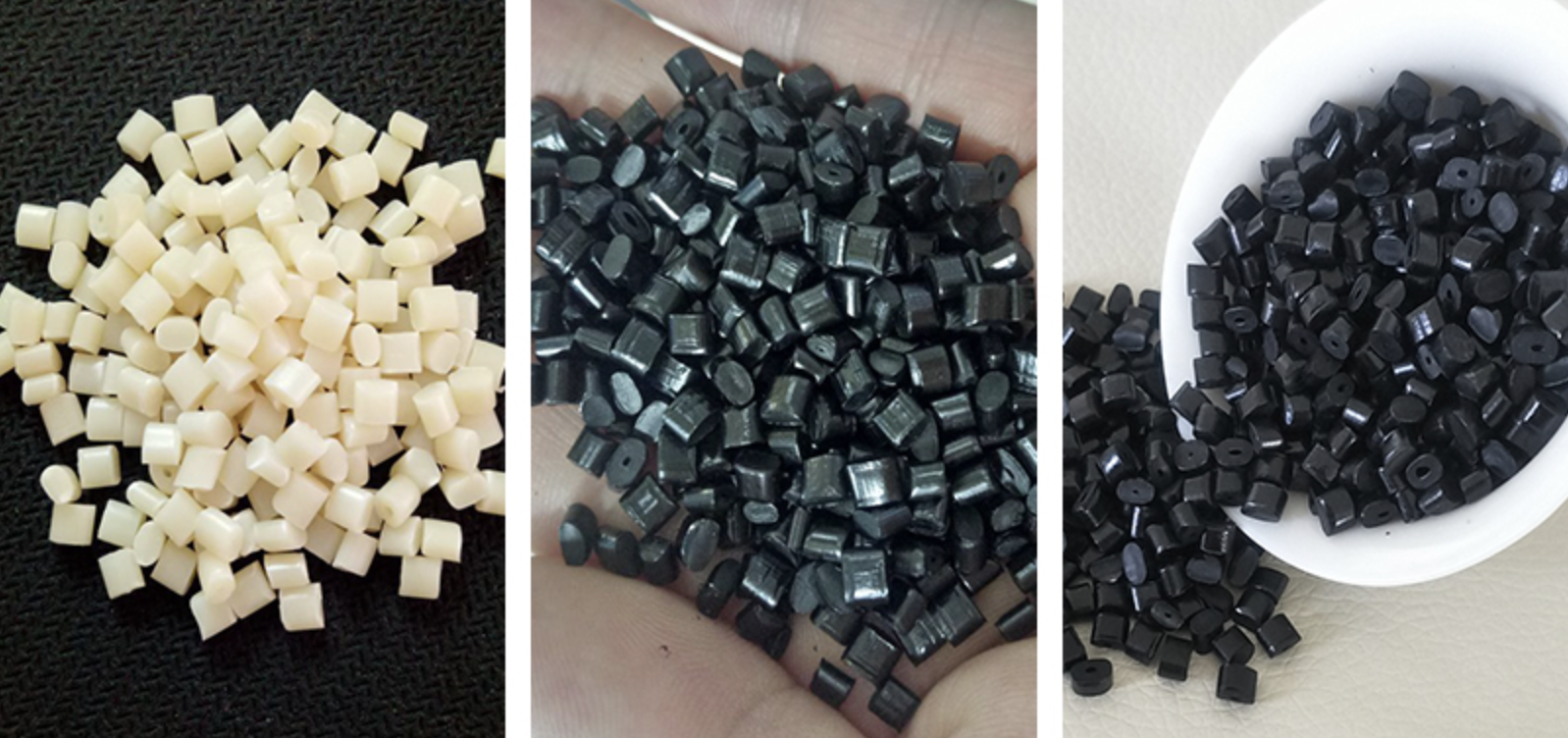
Synthesized from phenol through 2,6-decomposition via oxidative bond polymerization, PPO plastic exhibits an amorphous molecular structure and possesses exceptional chemical and physical properties. As a result, it is highly valued and widely used in numerous industries. The US General Electric Company pioneered the industrial production of PPO plastic, branding it as “Noryl”.
2. Outstanding features of PPO plastic
PPO (Polyphenylene Ether) plastic possesses numerous remarkable properties. Thanks to these advantages, it has become a preferred engineering material in various industries, especially electronics, automotive, and medicine. Below are the important properties of PPO plastic:
Long Life |
With good resistance to time and aging, PPO plastic becomes the suitable choice for applications requiring durability and reliability, bringing long-term economic value to users.
|
Electrical Insulation |
PPO plastic has excellent electrical insulation properties, helping to ensure the safety of electrical equipment and protect internal circuits.
|
Chemical Resistance
|
PPO plastic is a shield that protects the product from chemical attack (hydrocarbons, alkalis, acids and other chemicals) ensuring long life.
|
Dimensional Stability
|
PPO plastic does not deform in any case when temperature/humidity changes erratically, helping to ensure aesthetics and high precision.
|
Machinability
|
Despite its poor melt fluidity, PPO plastic can still be transformed into various shapes thanks to modern technologies to improve its processability and handling.
|
Fire Resistance
|
PPO plastic has good fire resistance. With the ability to self-extinguish, PPO plastic contributes to ensuring safety for users and the environment.
|
Heat and Thermal Resistance
|
PPO plastic can operate from -127°C to 121°C, making it the perfect choice for harsh environments where temperatures are constantly changing.
|
Impact and Abrasion Resistance
|
PPO plastic has good mechanical properties, abrasion resistance and high impact strength; ensuring the product avoids abrasion and damage caused by external agents.
|
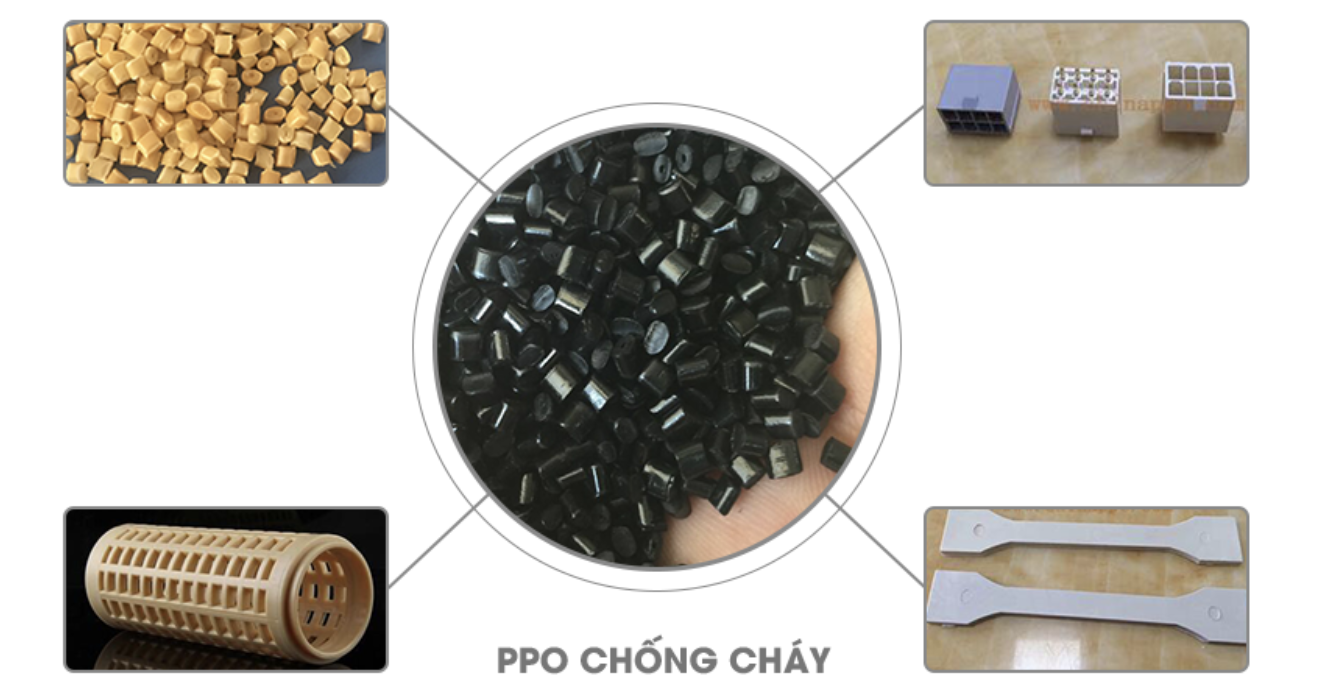
The increasing demand and development potential of PPO plastics have prompted manufacturers to continuously improve and develop new types of PPO plastics with higher performance to meet the increasingly diverse needs of the market. In general, the outstanding mechanical, chemical, electrical, and thermal properties of PPO plastics make them ideal materials for many demanding applications across industries.
3. Is PPO plastic related to PP plastic?
PPO and PP are two popular thermoplastics widely used in various applications. While they share some similarities, they also exhibit significant differences. Refer to the comparison table below to easily select the appropriate plastic for your needs:
Properties |
PPO |
PP |
Name |
Nhựa kỹ thuật cao cấp. |
Nhựa nhiệt dẻo phổ biến. |
Melting temperature
|
260°C |
160°C |
Tensile strength |
70 MPa |
35 MPa |
Impact strength |
High |
Medium |
Chemical resistance
|
Good, especially with organic chemicals. |
Good, but poor with some strong chemicals.
|
Insulation |
Excellent |
Good |
Self-extinguishing properties |
Yes |
No |
Applications |
Automotive components, electronic equipment, medical instruments.
|
Food packaging, textiles, household appliances.
|
Production process |
More complex |
Simpler |
Cost |
Higher
|
Lower |
PPO boasts a higher melting point, tensile strength, impact strength, and superior chemical resistance compared to PP. Additionally, PPO is self-extinguishing, making it a safe option for electronics and automotive applications. However, PPO is more complex to manufacture and consequently more expensive than PP.
Conversely, PP has a lower melting point, tensile strength, moderate impact strength, and good chemical resistance. Unlike PPO, PP is not self-extinguishing. Its advantages lie in its lower cost and simpler manufacturing process. PP finds extensive use in packaging, textiles, and household applications.
Therefore, PPO and PP are distinct plastics with different applications. The choice between PPO and PP hinges on the specific requirements of the application. If high-performance, excellent heat resistance, durability, and chemical resistance are essential, PPO is the preferred choice. For cost-effective, easily processed plastics suitable for packaging and single-use products, PP is more appropriate.
See more: PP Plastic: Everything you need to know
4. Applications of PPO plastic
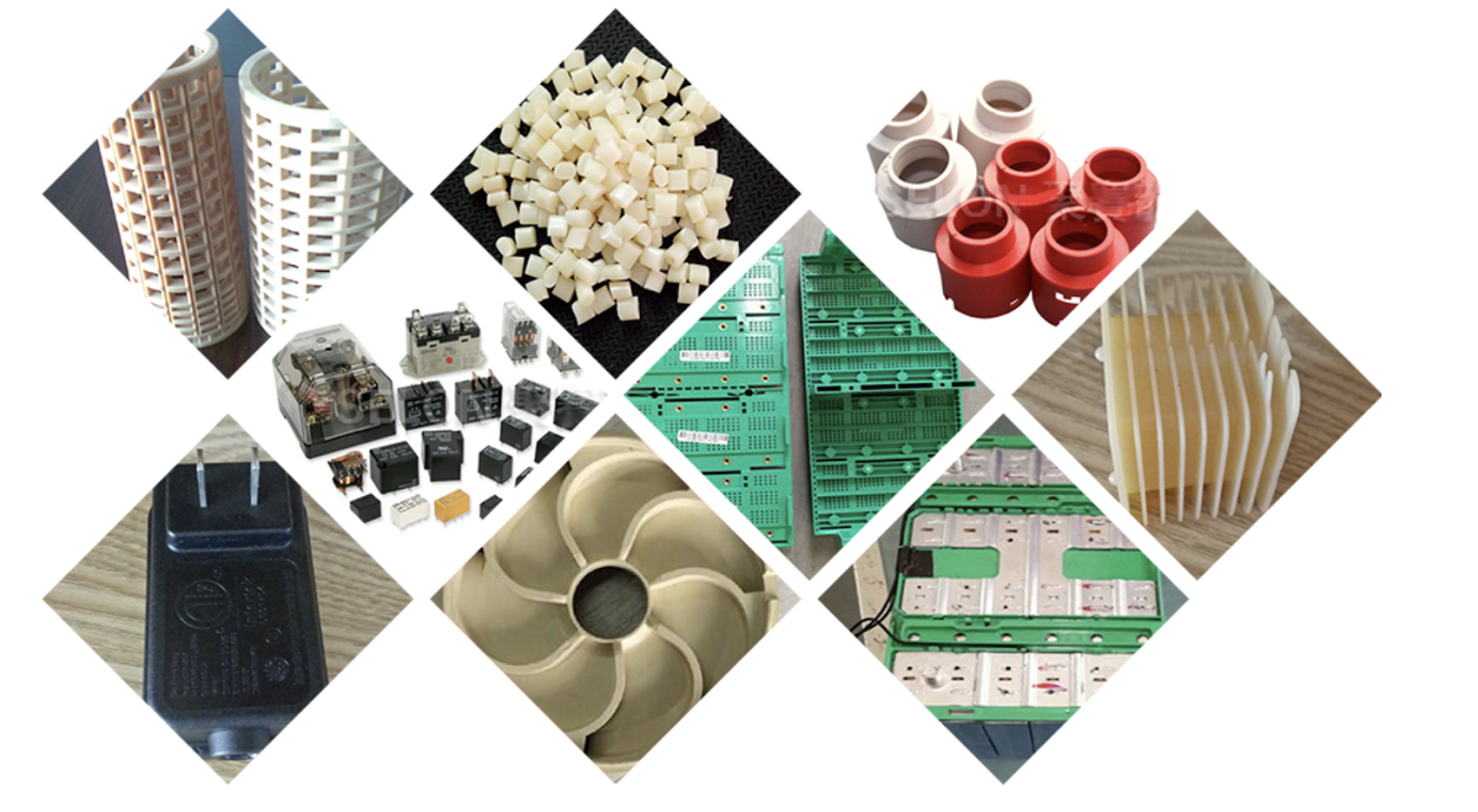
PPO plastic is widely used in many industrial applications due to its outstanding properties. Here are some common applications of PPO plastic in different industries:
- Automotive technology: Interior and exterior of cars, such as dashboards, guards, valves, fuel injectors, fuse covers, etc.
- Electrical and electronic: Mobile phones, computers, laptops, printed circuit boards (PCBs), tube sockets and other parts.
- Home appliances: Air fryers, bread makers, microwave ovens, etc.
- Electronic components: Plugs, jacks, switches, computer components, microchips, etc.
- Paint and coating industry: Mixed with paint compounds to increase gloss, mechanical strength, water resistance and scratch resistance.
- Chemical and medical industry: Anti-corrosion equipment, hot water tanks, valves, transformer shielding sleeves, relay boxes, insulating posts and surgical medical instruments.
- Plastic and rubber industry: Blended with rubber and other plastics to create compounds with better chemical and mechanical resistance.
5. Conclusion
PPO plastic, with its outstanding advantages in heat resistance, chemical resistance and mechanical strength, has affirmed its position as one of the leading engineering plastic materials today. Thanks to its dimensional stability and good machinability, PPO is widely used in industries requiring high precision such as automobiles, electronics and medicine. In the future, with the development of technology, PPO plastic promises to be applied even more in high-tech products.
6. About EuroPlas
EuroPlas is a pioneer in the field of filler masterbatch production. With many years of experience in providing effective plastic processing solutions, EuroPlas is committed to bringing customers high-quality plastic products that meet the most stringent standards. Coming to EuroPlas, customers will receive professional advice from a team of experienced engineers. Do not hesitate to contact EuroPlas via hotline and email or leave information via the form for quick advice and support.