From the water bottles we carry to the medical devices safeguarding our health, transparent plastics have become an indispensable part of our daily lives.
But raw plastic isn't inherently transparent. It's often cloudy and dull, limiting its applications. That's where the magic of additives comes in. These microscopes work their wonders behind the scenes, transforming ordinary plastic into clear and transparent masterpieces.
In this article, we'll explore the different types of additives available, and showcase their applications across various industries. So saddle in and prepare to see plastic in a light of unparalleled clarity afforded by the magic of additives!
Read more: What are plastic additives? 8 most common plastic additives in plastic industry
1. Factors that hinder plastic transparency
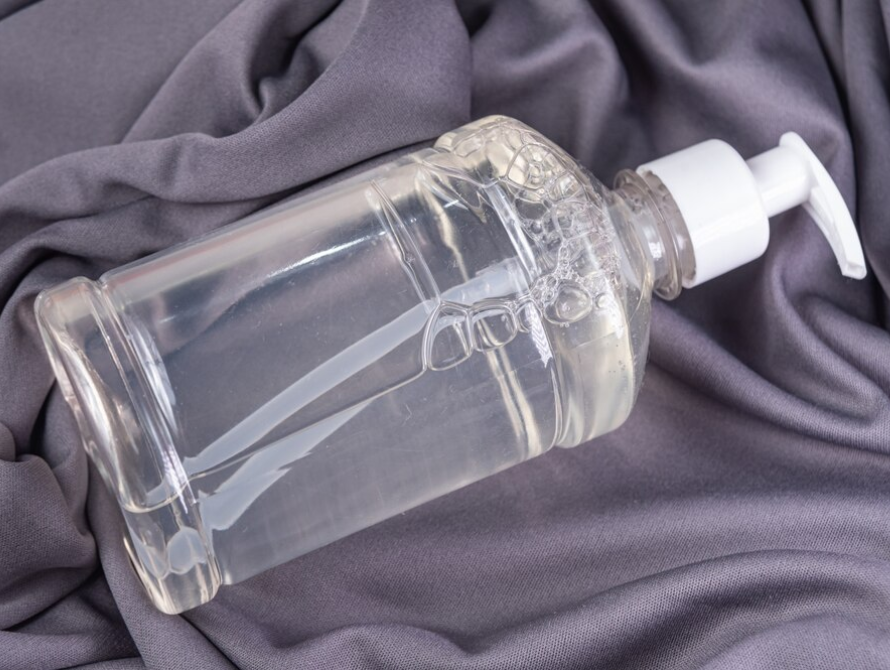
Additives unlock stunning clarity potential of plastic
Why do some plastics achieve dazzling transparency while others remain dull and cloudy?
Transparency, in essence, is a dance between light and the polymer chains that make up plastic. When light encounters these chains, it interacts in a complex way, sometimes passing through unimpeded and other times being scattered or absorbed. This interaction ultimately determines how transparent the plastic appears.
To quantify these effects, scientists use a measure called "clarity." It essentially indicates the percentage of light that passes through the plastic without being scattered. A higher clarity value signifies greater transparency and vice versa.
Various factors can throw a wrench into plastic transparency. Here are the main troublemakers:
- Crystallinity: Orderly structures let light pass, disorder scatters it.
- Scattering: Impurities like bubbles and fillers act like sand in water, making it cloudy.
- Manufacturing: Optimal conditions encourage order and reduce impurities, while the opposite reduces transparency.
- Degradation: UV light and oxygen break down the plastic, causing yellowing and transparency loss.
- Surface: Scratches and roughness act like tiny lenses, scattering light and making it hazy.
2. Clarity-enhancing additives
2.1. Nucleating agents
Nucleating agents enhance transparency by organizing the polymer structure
Plastic material as a sea of tiny, interconnected molecules. When these molecules arrange themselves in a specific way, they form structures called spherulites. The size and uniformity of these spherulites play a vital role in determining transparency.
Nucleating agents act like tiny seeds scattered throughout the plastic. They provide a "platform" for spherulite formation, encouraging them to form earlier and grow smaller and more uniform. This translates to a significant reduction in light scattering, which is the primary culprit behind a cloudy appearance.
The benefits don't stop there. Nucleating agents can also improve other properties of transparent plastics, such as:
- Increased mechanical strength: Smaller spherulites create a more tightly packed structure, making the plastic stronger and more durable.
- Reduced cycle time: Nucleating agents can accelerate the crystallization process, allowing manufacturers to produce finished products faster.
- Improved heat resistance: Smaller spherulites are less susceptible to thermal deformation, leading to a more stable product.
This makes them essential for applications where optical clarity is critical, such as lenses, packaging, and medical devices. Some commonly used nucleating agents include:
- Talc: A naturally occurring mineral commonly used in polypropylene and polyethylene.
- Sodium benzoate: A food additive that can be used in various plastic resins.
- Calcium stearate: A fatty acid salt used in polyvinyl chloride (PVC).
2.2. UV stabilizers
UV stabilizers shield plastic from the sun's harmful rays
What happens if you leave your transparent plastic object out in the sun for weeks? It starts to yellow, crack, and lose its pristine clarity. This is why the sun's ultraviolet (UV) radiation becomes an enemy of plastic transparency.
Fortunately, we have
UV stabilizers. These additives act like invisible shields that absorb harmful UV rays before they can damage the polymer chains in plastic. This prevents the formation of free radicals, which are the main culprits behind yellowing, brittleness, and reduced transparency.
Choosing the right UV stabilizer depends largely on the specific application. Factors like UV exposure level, desired lifespan, and compatibility with other additives all play a crucial role in the selection process.
There are different types of UV stabilizers, each possesses a unique feature:
- Absorbers: These guys soak up UV rays like sponges, preventing them from reaching the polymer chains. Think of them as sunbathers who intercept the harmful rays before they can hurt your skin.
- Hindered amine light stabilizers (HALS): These work a little differently. They act like undercover agents, deactivating the excited energy states created by UV radiation before they can cause damage. They're like secret service agents who neutralize threats before they escalate.
- Quenchers: These quickly extinguish the harmful free radicals generated by UV exposure before they can wreak havoc on the polymer chains.
By harnessing the power of UV stabilizers, we can ensure that our transparent plastics remain strong, beautiful, and true to their original form.
2.3. Antioxidants
Transparency-enhancing additives bring plastic to higher performance
Oxidative degradation, a natural process where oxygen and sunlight break down polymer chains, leading to the formation of yellowing chromophores. This is where antioxidants come in to protect your plastics from becoming dull and brittle.
Antioxidants absorb free radicals before they can cause damage to your material and prevent chain scission.
Here are some of the commonly used antioxidant heroes:
- Hindered phenols: These are workhorses, fighting free radicals and preventing chain scission.
- Phosphites: These offer long-term protection and are often combined with other antioxidants for synergistic effect.
Antioxidants often work best in combination with other additives. For example, UV stabilizers can be used alongside antioxidants to provide a double layer of protection against both environmental and oxidative degradation.
By incorporating antioxidants into the plastic mix, manufacturers can significantly enhance the longevity and visual clarity of their products.
A study shows that using antioxidants can extend the lifespan of transparent plastics, ensuring their aesthetic appeal and functionality for longer.
2.4. Polymer processing aids
While additives like UV stabilizers play a crucial role, another essential factor is often overlooked:
polymer processing aids (PPAs).
PPAs act like lubricants, easing the flow of the molten polymer and making the process smoother and more efficient. This, in turn, leads to fewer air bubbles getting trapped and fewer surface defects appearing, resulting in a more transparent final product.
In fact,
a research founds that using PPAs can improve transparency by up to 13%. Not only that, but it also reduces processing time and energy consumption, making it a win-win situation for both manufacturers and the environment.
There are various types of PPAs, each with its own unique properties and functionalities. Here's a quick overview of some common PPAs:
- Fluoropolymers: These are highly effective lubricants that create a slippery surface for the molten polymer to flow over.
- Organic phosphates: These offer good thermal stability and are widely used in polyolefins.
- Silicones: These are particularly useful for reducing die swell and improving surface finish.
2.5. Clarifying agents
Clearer views and enhanced functionality with transparent plastic cases
Clarifying agents come in various forms, each with its unique approach to combating this problem. Some, like organic nucleating agents, promote the formation of smaller, more uniform crystals within the plastic. These smaller crystals scatter less light, leading to improved transparency. Others, like optical brighteners, actually absorb ultraviolet light and re-emit it as visible light, effectively brightening the plastic and enhancing clarity.
Some of the most commonly used clarifying agents include:\
- Polyethylene glycol (PEG): A polymer that acts as a lubricant, reducing friction and improving the flow properties of the plastic, ultimately leading to better clarity.
- Optical brighteners: These clever molecules absorb UV light and re-emit it as visible light, enhancing brightness and clarity.
2.6. Surface modifiers
Additives enable fresh and clear packaging
Surface modifiers act like tiny bulldozers, leveling these peaks and valleys, creating a smooth, even surface that allows light to pass through unimpeded. This translates to a dramatic increase in transparency, enhancing the visual appeal and functionality of the plastic product.
Here are some examples of surface modifiers used in plastic:
- Fluorinated compounds: These add a low-surface-energy layer, similar to silicones, but offer better chemical resistance.
- Nanoparticles: These microscopic particles can fill in tiny imperfections and create an incredibly smooth surface, resulting in exceptional transparency.
Importantly, surface modifiers often work synergistically with other additives. For example, when combined with clarifying agents, they can amplify the clarity-enhancing effect, creating truly transparent plastic with unparalleled optical properties.
3. Applications and case studies
3.1. Transforming automotive headlights
By incorporating UV stabilizers and antioxidants, plastic headlight lenses are now significantly less susceptible to yellowing and degradation. This translates to improved visibility and safety, especially in challenging weather conditions.
Toyota has been using a UV-resistant coating on their headlights. This coating helps to prevent the yellowing and fading of the headlight lenses, which can significantly reduce their clarity and performance.
3.2. Revolutionizing food packaging
Building trust through transparency additives
Consumers are increasingly drawn to products with clearly visible contents, prompting the food packaging industry to embrace transparent plastics. However, maintaining transparency while protecting food from spoilage and harmful UV rays is not easy. By utilizing UV stabilizers and antioxidants, food packaging can now achieve the desired clarity while ensuring product quality and safety.
In
2018, Kraft Heinz redesigned the packaging for their Oscar Mayer hot dog brand, making it more transparent and showcasing the quality of the product. They reported a 7% increase in sales within the first year, attributing it to the improved product presentation and increased consumer trust.
4. The future of transparent plastics
New developments in additive technology are constantly pushing the boundaries of what's possible.
One exciting trend is the rise of nano-additives. These microscopic particles are designed to interact with light on a fundamental level, further minimizing scattering and maximizing transparency.
Sustainability is another driving force shaping the future of transparent plastics. Bio-based additives derived from renewable resources are gaining traction as a way to minimize environmental impact. Additionally, research is exploring ways to recycle transparent plastics more effectively, creating a closed-loop system that reduces waste and conserves resources.
Transparent electronics and interactive displays are also on the horizon, promising to revolutionize the way we interact with technology.
5. Conclusion
These minuscule transparent polymers are responsible for transparent OLED displays, scratch-resistant phone screens, and even life-saving medical gadgets. It is not easy to achieve the appropriate level of clarity. Nucleating agents, UV stabilizers, antioxidants, and other substances work diligently behind the scenes to resist dispersion, degradation, and other phenomena that reduce transparency.
For even more insights and expert advice on how plastic solutions can empower your business, head over to the
EuroPlas blog! We're passionate about exploring the latest innovations and sharing our knowledge with the world.