In contemporary times, plastic stands as a ubiquitous marvel, seamlessly woven into the fabric of industry, technology, and our quotidian existence. Yet, have you ever paused to ponder its intriguing origins? Within the confines of this article, we shall embark on a captivating journey through its historical tapestry, tracing the intricate evolution of plastic from its nascent beginnings to the sophisticated polymers that grace our modern lives today.
1. What are plastics? The history of plastics
Plastics is a group of synthetic materials made from polymers, which are large molecules composed of repeating structural units called monomers. These materials can be molded into various shapes while soft and then set into a rigid or slightly elastic form. Plastics are widely used in a variety of applications due to their versatility, durability, and relatively low cost.
The history of plastics dates back to the mid-19th century, but the modern era of plastics began in the early 20th century with the development of synthetic polymers. Here's a brief overview of the history of plastics:
Read more:
What is plastic? Everything you need to know about plastic
1.1. Natural Polymers
Before the invention of synthetic polymers, natural polymers such as rubber, tortoiseshells, and horns were used for various purposes. For example, ancient civilizations used rubber derived from latex for waterproofing and other applications.
1.2. First Synthetic Plastics
In the 19th century, scientists began experimenting with synthetic materials. One notable example is the creation of Parkesine by Alexander Parkes in 1856. This is one of the important steps that marked the appearance of synthetic plastics in history.
Parkesine was crafted by dissolving cellulose, a fibrous plant substance, in a liquid blend. Upon drying, this mixture solidified, enabling it to be molded into various forms, akin to contemporary plastics. Parkesine found extensive application in the manufacture of toys, ornaments, and diverse household items. It stands as the earliest precursor to the sophisticated synthetic plastics ubiquitous in our modern world.
1.3. Bakelite
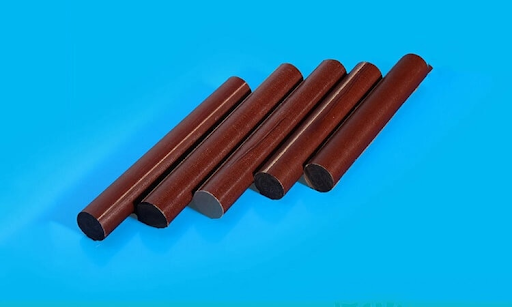
Bakelite - the first fully synthetic plastic
In 1907, Leo Baekeland invented Bakelite, the first fully synthetic plastic. Bakelite stands as a groundbreaking achievement in synthetic materials, being the inaugural plastic forged from chemical compounds, distinct from its predecessors reliant on natural elements. Prior to the advent of Bakelite, plastics were predominantly derived from organic sources or were simply modifications of natural compounds through chemical processes
Bakelite materializes through the intricate fusion of phenol and formaldehyde, catalyzed to yield a resilient, heat-resistant substance. This innovative process engenders a rigid plastic with exceptional thermal endurance, rendering it invaluable across diverse industrial and domestic spheres. Bakelite, thus, emerged as the foremost mass-produced synthetic plastic, heralding the onset of the transformative plastic materials revolution in the 20th century.
1.4. Development of other plastics
In the following decades, scientists and engineers delved deeper into the realm of polymer chemistry, leading to the creation of an array of diverse plastics. Each type of plastic brought unique properties, expanding the possibilities of their applications. Let's delve deeper into the development of these plastics:
1.4.1. Polystyrene (PS)
Developed in the 1920s, polystyrene is a versatile synthetic polymer made from monomer styrene. It is a commonly used plastic known for its rigid structure and excellent insulation properties. Polystyrene can exist in two forms: solid (as a plastic) and foam (commonly known as Styrofoam).
In its solid form, polystyrene is rigid and transparent, making it suitable for various applications. It is used in products like disposable cutlery, CD cases, laboratory ware, and even in the construction of models and prototypes due to its ease of molding and shaping. However, one of the most widespread uses of polystyrene is in its foam form.
Polystyrene foam, or Styrofoam, is a lightweight and buoyant material. Its excellent thermal insulation properties make it popular for packaging fragile items and insulating buildings. It is widely used in the food industry for disposable food service trays, plates, and cups due to its low cost and insulating abilities.
1.4.2. Polyvinyl Chloride (PVC)
PVC, discovered in the 1920s, is a versatile and widely used thermoplastic polymer. It is made from vinyl chloride monomers through a process called polymerization. PVC is known for its durability, chemical resistance, and versatility, making it one of the most commonly used plastics in the world.
PVC can be found in various forms, such as rigid or flexible. Rigid PVC is hard and strong, making it suitable for applications like pipes, fittings, and window frames in the construction industry. Flexible PVC, on the other hand, is softer and more pliable, often used in products like inflatable structures, electrical cable insulation, and medical tubing.
One of the key advantages of PVC is its resistance to chemicals, weathering, and abrasion. It is also flame-resistant, making it useful in a variety of applications where fire safety is a concern.
1.4.3. Nylon
Invented by Wallace Carothers in the late 1930s, Nylon is a synthetic polymer known for its strength, resilience, and versatility.
It can be produced in various forms, such as fibers, films, and molded parts. One of the primary uses of nylon is in the textile industry, where it is widely used to make clothing, hosiery, and stockings. Its durability, elasticity, and resistance to abrasion make it an excellent choice for these applications.
1.4.4. Polyethylene (PE)
Developed in the 1930s, polyethylene is the most common plastic and is known for its low cost, lightweight, and chemical resistance. There are different types of polyethylene, including high-density polyethylene (HDPE) and low-density polyethylene (LDPE), each with specific applications. HDPE is used for bottles, pipes, and toys, while LDPE is used in plastic bags and films.
1.4.5. Polypropylene (PP)
Invented in the 1950s, polypropylene is a thermoplastic polymer widely used in a variety of applications due to its unique combination of properties. One of the key advantages of polypropylene is its high melting point, which makes it suitable for applications involving high temperatures.
It is lightweight and has excellent chemical resistance, making it resistant to many acids, bases, and solvents. Polypropylene is also highly resistant to moisture and has low water absorption rates.
1.4.6. Polycarbonate (PC)
Discovered in the 1950s, polycarbonate is a high-performance thermoplastic polymer known for its exceptional strength, transparency, and heat resistance.
One of the most significant features of polycarbonate is its impact resistance. It is nearly unbreakable, making it an ideal choice for applications where safety and durability are paramount, such as in bulletproof windows, eyewear lenses, and safety helmets.
Its high impact strength also makes it suitable for use in electronic devices and automotive components, protecting fragile internal components in case of accidental drops or impacts.
1.4.7. Acrylic (Polymethyl Methacrylate or PMMA)
In the 1930s, acrylic was developed and became popular for its transparency and UV resistance. Acrylic, scientifically known as Polymethyl Methacrylate (PMMA), is a transparent thermoplastic that possesses exceptional optical clarity and is widely recognized for its glass-like appearance. It is a synthetic polymer made from methyl methacrylate monomers through a process called polymerization.
It allows for approximately 92% of visible light to pass through, making it a popular choice for applications where optical clarity is essential, such as in windows, lenses, and optical displays. Acrylic can be easily molded and shaped, providing versatility in design for various products.
1.4.8. Polyester
Polyester plastics, such as PET (Polyethylene Terephthalate), were developed in the 1940s. It is a versatile material known for its durability, wrinkle resistance, and excellent moisture-wicking properties. Polyester fibers are created through a chemical reaction involving petroleum-based products, primarily ethylene glycol and terephthalic acid.
Polyester stands out with its resilience, which makes it resistant to stretching and shrinking. Polyester fabrics are also highly resistant to environmental factors such as sunlight, mold, and mildew, making them ideal for outdoor applications. Polyester is commonly used in the textile industry for producing clothing, upholstery, and home furnishings.
1.4.9. Polyurethane (PU)
Developed in the 1930s, Polyurethane is a versatile and widely used polymer derived from the reaction between isocyanates and polyols.
One of the significant advantages of polyurethane is its exceptional durability and resilience. It is highly resistant to abrasion, impact, and weathering, making it ideal for applications that require robust materials. Polyurethane elastomers, in particular, offer excellent elasticity and flexibility, making them suitable for use in products like shoe soles, automotive suspension bushings, and industrial machinery components.
2. When was plastic first used commercially?
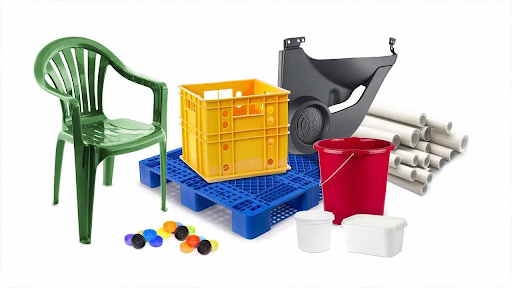
When was plastic first utilized for commercial purposes?
The commercial use of plastics began in the early 20th century, marking a turning point in industrial innovation. Bakelite was the first plastic to be used widely and commercially. It was invented by Belgian chemist Leo Baekeland in 1907. Bakelite was a versatile material that could be molded into various forms and retained its shape even after being heated and cooled. It had excellent electrical insulating properties, making it ideal for use in electrical equipment and a wide range of consumer goods.
The commercial production of Bakelite began in 1909 when Baekeland established the General Bakelite Company in the United States. Bakelite found extensive use in the manufacturing of items such as electrical insulators, radio and telephone casings, jewelry, kitchenware, and many other products. Its popularity and commercial success marked the beginning of the modern plastics industry.
Read more: What are the benefits of plastic?
3. What did people use before plastic?
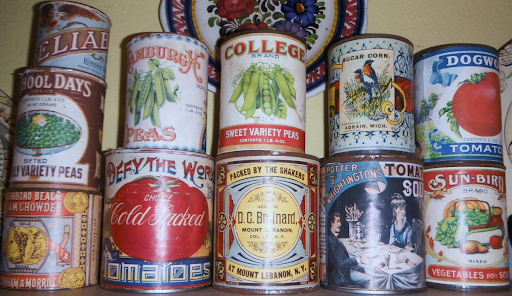
People used metal cans for packaging and preserving foods before plastic
Before the widespread use of plastic, people relied on natural materials for various purposes. Glass, metal, wood, paper, and cardboard were the primary materials used for packaging, storage, and consumer goods. Glass containers were common for preserving food, while metal cans revolutionized the food industry.
Fabrics, leather, and natural fibers were the mainstay in the fashion industry, showcasing the creativity of human craftsmanship. Clay and ceramics were used for making pottery, dishes, and decorative items. They were fired to high temperatures to achieve durability.
Items like bones, horns, and shells were used for tools, decoration, and ornaments. Leather, derived from animal hides, was used for clothing, bags, and various accessories. Plant-based materials such as straw, palm leaves, and bamboo were used for making baskets, mats, and other household items.
4. The future of plastic
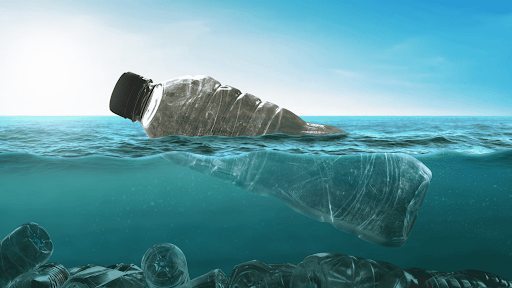
Plastic waste leads to environmental concerns
While plastic brought unparalleled convenience, it also posed significant challenges. The durability that made plastic so valuable also meant it didn’t readily biodegrade. Plastic waste started piling up, leading to environmental concerns. Images of polluted oceans and wildlife entangled in plastic have led us to increasingly discuss the sustainability of the earth and the need for responsible consumption.
In response to environmental concerns, scientists and engineers have been hard at work developing biodegradable plastics made from renewable sources, offering a sustainable alternative to traditional plastics. Recycling initiatives have also gained traction, aiming to reduce the environmental impact of plastic waste.
As we step into the future, The main challenge is how to balance convenience and sustainability. Plastic remains an important material in sectors such as healthcare, transportation, and technology. Scientists are exploring advanced recycling techniques and developing many new materials that are not only versatile but also environmentally friendly.
5. Conclusion
The evolution of plastics from ancient resins to the complex polymers we use today is a testament to human ingenuity and scientific progress. While plastics have undoubtedly revolutionized modern living, their omnipresence comes with environmental challenges. By understanding the journey of plastics, we can make informed choices, appreciating their value while preserving the planet for future generations.
6. Plastic products at EuroPlas
BiONext bioplastic compounds are derived from sustainable sources or fossil fuels. They feature a glossy, attractive surface and are easy to machine, meeting both functional and aesthetic requirements for the final product. What sets BiONext bioplastic compounds apart is their ability to decompose easily into water, CO2 gas, and biomass within just 12 months after disposal. This eco-friendly characteristic makes them ideal for various applications, such as bioplastic packaging, food wraps, biodegradable shopping bags, agricultural mulch films, lamination, food containers, disposable bowls, chopsticks, cups, spoons, and forks.
EuroPlas color masterbatch offers excellent dispersion, stable color shades, and high heat resistance, making it ideal for various industrial applications like film blowing, injection molding, and extrusion. We supply a range of colors including white, black, red, gray, purple, blue, brown, orange, and yellow. Additionally, we offer specialized color masterbatch options tailored to meet specific finished product requirements.
Plastic additives are essential components added during production to enhance processing efficiency and achieve specific product properties. As a reliable supplier, we offer a range of additives such as deodorizers, flame retardants, anti-fog agents, and more. We assist in selecting the appropriate additives and usage rates to tailor the final product to your exact specifications.
Engineering plastic compounds, also known as engineering thermoplastics, are specialized plastic materials that offer superior mechanical, thermal, chemical, and electrical properties compared to standard plastics. EuroPlas offers an ideal solution in the form of engineering plastic composites that combine flexibility, high quality, and multiple functionalities within a single material. Our range includes PBT GF-FR compound, blended PA6, PA66, PC fire retardant compound, ABS fiberglass compound, and ABS antistatic compound. These materials enable the creation of finished products that perform effectively, meeting diverse industrial requirements.
Filler masterbatch is a specialized additive used in plastic processing to enhance the properties of the final product. The primary purpose of filler masterbatch is to reduce the production costs of plastic products by replacing a portion of the polymer material with less expensive fillers. With over 16 years of experience, EuroPlas has been manufacturing and exporting filler masterbatch to numerous businesses across Asia, the Middle East, Africa, and Europe. Our extensive range of filler masterbatch options is designed to help you cut costs, enhance productivity, and create top-quality plastic products.
Biofiller, also known as biodegradable filler, refers to a type of filler material that is biodegradable and environmentally friendly. In recent years, EuP has expanded its biofiller offerings to include versatile product lines: BiOMates 01, BiOMates 02, and BiOMates 03. Each line is designed with distinct structures to cater to specific customer needs. BiOMates stands out as an excellent option for manufacturing eco-friendly items like biodegradable packaging, injection-molded products, and single-use plastic extrusions, owing to its exceptional advantages.