Understanding the differences between hygroscopic and non-hygroscopic plastics is crucial for manufacturers across various industries. The ability of plastics to absorb moisture can significantly affect their properties and performance in applications ranging from packaging to automotive parts. In this article, we will explore what hygroscopic and non-hygroscopic plastics are, their unique characteristics, and guide you on when to choose each type for your specific needs.
1. What Are Hygroscopic Plastics?
Hygroscopic plastics are materials that have the ability to absorb moisture from the environment. This characteristic can influence their mechanical properties, making it essential to manage their moisture content during processing and application. Common hygroscopic plastics include:
- Nylon (Polyamide): Known for its strength and durability, nylon is widely used in automotive parts, textiles, and industrial components. However, it readily absorbs moisture, which can affect its dimensional stability and mechanical properties.
- Polycarbonate (PC): Often used in electronics, automotive parts, and construction materials, polycarbonate's ability to absorb moisture can lead to issues such as stress cracking and reduced transparency if not properly managed.
- Acrylic (PMMA): Used in applications requiring clarity and weather resistance, such as displays and lighting, acrylic can absorb moisture, leading to changes in its optical properties and potential dimensional instability.
- Polyethylene Terephthalate (PET): Commonly used in packaging, especially for beverages, PET can absorb moisture, which can impact its processing and the final product's appearance and performance.
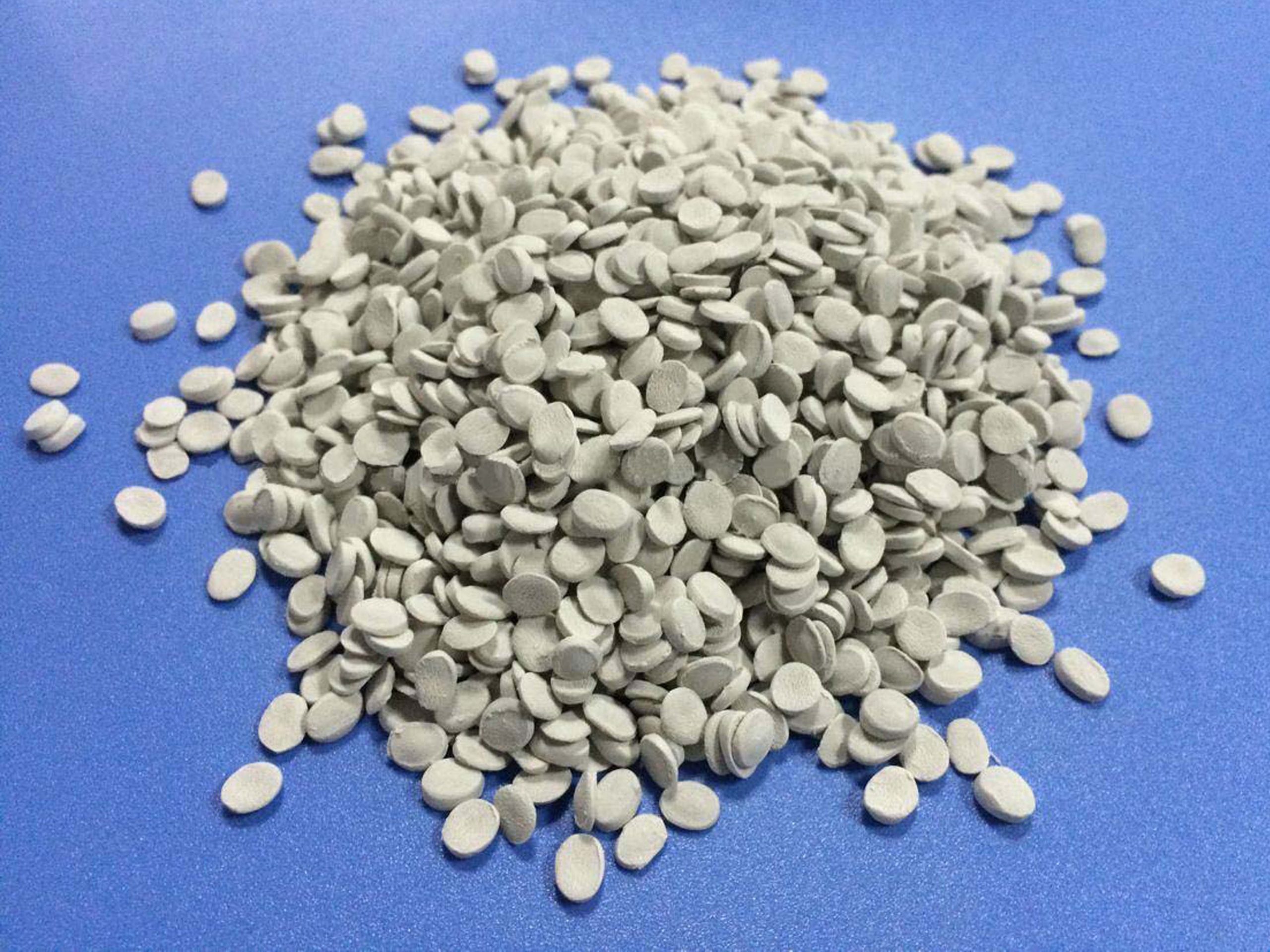
Hygroscopic plastics are materials that have the ability to absorb moisture from their surroundings.
The absorption of moisture by these plastics can lead to several issues, such as:
- Dimensional Changes: Swelling or shrinking of the material, affecting its fit and function in assemblies.
- Mechanical Property Alterations: Changes in strength, flexibility, and impact resistance.
- Processing Challenges: Moisture can cause defects like bubbles or voids during moulding, leading to reduced product quality.
2. What Are Non-Hygroscopic Plastics?
Non-hygroscopic plastics, on the other hand, do not absorb moisture from the environment. This makes them more stable and easier to handle in various conditions. Common non-hygroscopic plastics include:
- Polypropylene (PP): Widely used in packaging, automotive parts, and consumer goods, polypropylene is resistant to moisture absorption, maintaining its properties and dimensional stability.
- Polystyrene (PS): Used in packaging, disposable containers, and insulation, polystyrene does not absorb moisture, ensuring consistent performance in humid environments.
- Polyethylene (PE): Available in various densities, polyethylene is used in films, containers, and pipes. Its non-hygroscopic nature makes it suitable for applications exposed to moisture.
- Polyvinyl Chloride (PVC): Common in construction, medical devices, and consumer goods, PVC resists moisture absorption, maintaining its durability and performance over time.
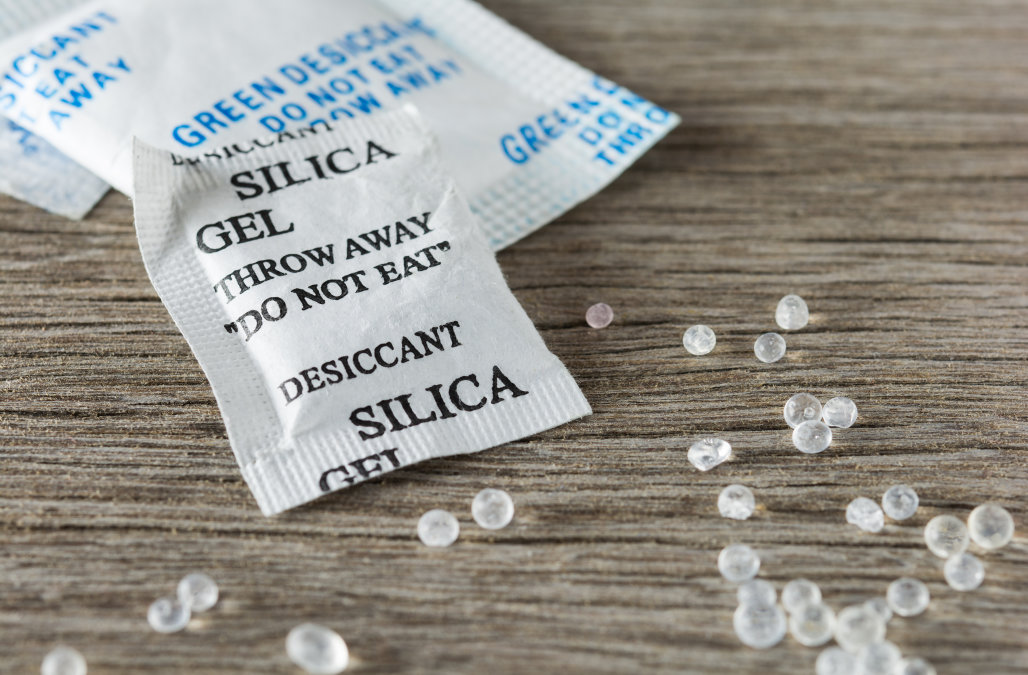
Non-hygroscopic plastics are used to absorb moisture in packaging.
Advantages of non-hygroscopic plastics include:
- Dimensional Stability: Consistent size and shape, even in humid environments.
- Ease of Processing: Reduced risk of defects related to moisture, such as bubbles or voids.
- Predictable Performance: Reliable mechanical properties and appearance, regardless of environmental conditions.
3. When To Choose Hygroscopic And Non-Hygroscopic Plastics?
Choosing between hygroscopic and non-hygroscopic plastics depends on your specific application requirements and environmental conditions. Here are some guidelines to help you decide:
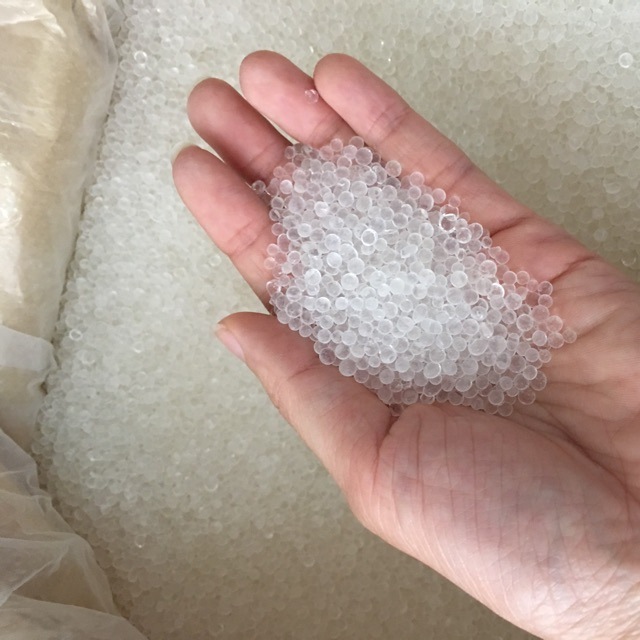
When should you choose hygroscopic plastics and non-hygroscopic plastics?
3.1. Choose Hygroscopic Plastics if:
- High Performance Needed: Applications requiring high strength, durability, or specific mechanical properties, such as automotive parts, industrial components, and certain consumer goods.
- Controlled Environment: Manufacturing processes where moisture content can be tightly controlled to prevent absorption issues, such as clean rooms or dehumidified environments.
- Post-Processing Treatments: Applications where post-processing treatments, such as drying, can mitigate the effects of moisture absorption.
3.2. Choose Non-Hygroscopic Plastics if:
- Moisture Exposure: Applications exposed to humid or wet environments, such as packaging, outdoor products, and medical devices.
- Dimensional Stability: Products requiring consistent dimensions and mechanical properties, regardless of environmental conditions, such as precision components and consumer goods.
- Ease of Processing: Manufacturing processes where minimal moisture management is desired to reduce complexity and defects, such as high-volume production of packaging and disposable items.
By understanding the characteristics and appropriate use cases for hygroscopic and non-hygroscopic plastics, you can optimize your manufacturing processes and ensure the quality and performance of your final products.
4. Conclusion
Selecting the right type of plastic for your application is critical to achieving optimal performance and durability. Hygroscopic plastics, with their moisture-absorbing properties, are suitable for high-performance applications where environmental control is possible. Non-hygroscopic plastics, on the other hand, offer stability and ease of processing in a variety of conditions. By carefully evaluating your specific needs and environmental factors, you can make an informed decision that enhances your product quality and manufacturing efficiency.
5. About EuroPlas
EuroPlas is a leading provider of plastic additives, offering a wide range of solutions for both hygroscopic and non-hygroscopic plastics. Our additives include odor absorbers, desiccants, flame retardants, anti-fog agents, anti-aging agents, processing aids, anti-static agents, UV stabilizers, and optical brighteners. At EuroPlas, we understand the unique challenges posed by different types of plastics and can help you select the right additives to enhance the performance and quality of your products. Whether you are dealing with hygroscopic or non-hygroscopic plastics, our experts are here to provide tailored solutions that meet your specific requirements. Contact EuroPlas today and visit our blog for the latest insights and advancements in plastic manufacturing.