Polypropylene is well-known for its outstanding insulating properties. Manufacturers usually use polypropylene compound with enhanced features to meet various requirements of electrical applications.
Let's explore the material's unique advantages that are suitable for electrical components and its different variations in this article! Follow along!
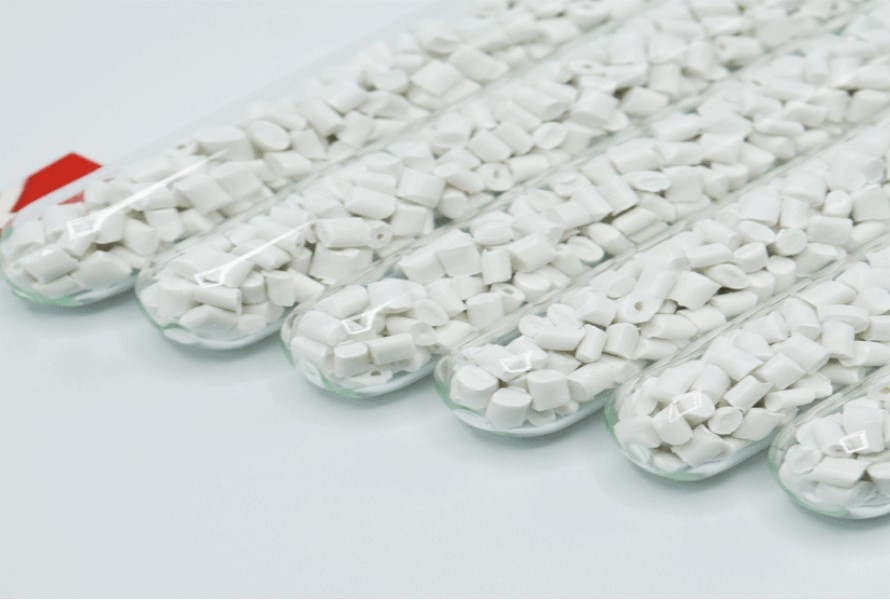
PP compound
1. Why Polypropylene Compound is a Popular Choice for Electrical Components
Many manufacturers choose polypropylene compound for their electrical components. Here are the reasons behind this:
- Excellent electrical insulation properties: Since the material features high dielectric strength, it's an extremely effective electrical insulator. Its low dielectric losses allow it to work well in high-frequency applications in the electronics and telecommunications sectors where minimal energy loss is essential.
- Thermal resistance: With a melting point of 160°C (320°F), polypropylene is essential in electrical components. Its thermal stability and resistance to high working temperatures guarantee electrical components' endurance in various conditions and climates.
- Chemical resistance: Polypropylene compound is resistant to certain chemicals, oils, solvents, and acids, making it suitable for electrical parts. The components are durable, even in harsh environments with corrosive substances.
- Low moisture absorption: This property of polypropylene compound helps electrical parts made from it withstand humid conditions.
- Affordability: The material is quite cost-effective to manufacture and process, making it an ideal option for mass production.
2. Types of Polypropylene Compounds for Electrical Parts
Polypropylene compounds can be tailored to improve properties and meet the final product's requirements.
Mobile charger from PP compound
Common types of this material include:
Polypropylene compound |
Ingredients |
Outstanding properties |
Applications |
PP flame retardant compound |
The main components of PP-FR compound are polypropylene (PP) resin and halogen/non-halogen flame retardant. |
Enhanced smoke reduction, self-extinguishing properties, and fire resistance |
- Building supplies, including insulation, roofing, and flooring
- Cables, circuit boards, and plastic coverings for appliances in the electrical and electronic sectors.
- It is also employed in the automotive sector to improve safety in vehicles and trucks.
|
PP conductive compound |
It's a combination of PP resin and carbon black conductive |
- Controlled electrical conductivity
- Higher stability compared to standard PP
|
- Electronic components
- Cable jackets
- Electrical equipment housing
|
PP BaSO4 compound |
It is made of PP resin, BaSO4, and suitable additives |
- Reduced shrinkage and deformation in high-temperature settings
- Enhanced formability and heat, chemical, and impact resistance
|
- Sanitary equipment
- House appliances
- Water filter equipment
|
PP glass bead compound |
It’s a combination of PP resin, glass beads, and specific additives |
- Improved mechanical stress under load
- Increased stiffness, transparent shaping, compression resistance, and thermal stability.
|
- Car interiors
- Home interiors
- Home appliances
|
PP glass fiber compound |
It combines PP resin, glass fiber and other specific additives |
- Increased flexural modulus and tensile strength
- Improved stiffness and reduced shrinkage
- Enhanced impact strength and thermal resistance
|
- Electric appliances
- Automobile applications
|
PP talc compound |
It consists of alc powder and appropriate additives based on end-product requirements. |
- Increased stiffness, flexural modulus, and strength
- Reduced creep tendency in increasing temperature environments
- Improved heat distortion temperature and dimensional stability
|
- Production of motorcycle and auto parts
- Other applications require good durability and high heat resistance (120-130oC) for a long time
|
3. Challenges and Considerations When Using PP Compounds
Though polypropylene compound is suitable for many electrical components, there are some disadvantages that manufacturers should consider, and changes should be made to mitigate the challenges and enhance the material's performance.
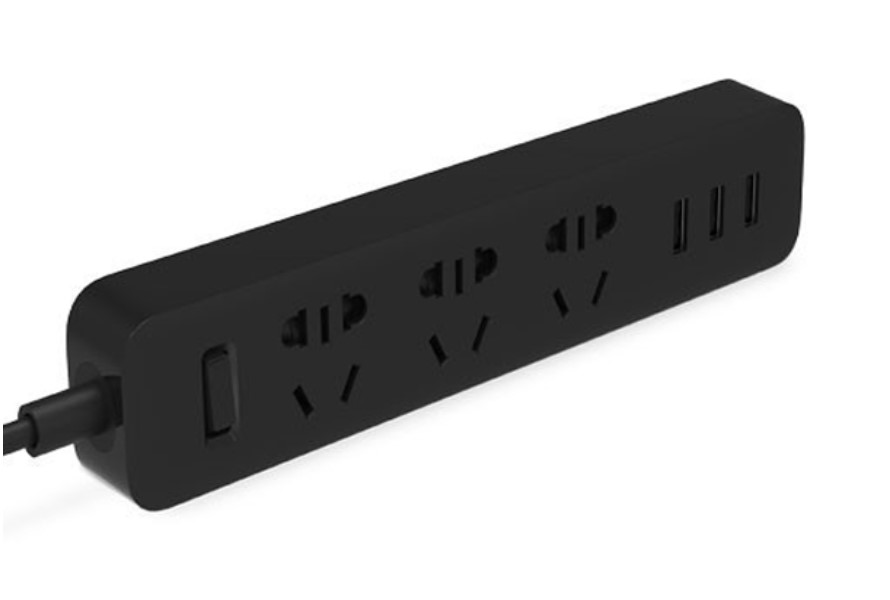
Electronic plug from PP compound
- Poor resistance to ultraviolet radiation: When polypropylene is exposed to sunshine, it might deteriorate over time due to its limited UV resistance. Brittleness, discoloration, and a loss of mechanical qualities may arise. Thus, UV stabilizers or other additives are usually needed for outdoor applications or extended exposure to sunlight in order to increase its weatherability and longevity.
- Brittleness at lower temperatures: Polypropylene compound usually has strong impact resistance at room temperature. However, it can become brittle at lower temperatures. This problem is especially critical in some situations, such as HVAC systems, outdoor electrical installations, and automobile parts. In certain applications, low-temperature performance can be improved by using modifiers or impact-resistant additives.
- Low bonding qualities: This challenge makes polypropylene difficult to paint. Treating the surface to increase the adhesion strength of paints and inks that may color polypropylene is one way to solve this problem.
- Dimensional stability: In applications requiring exact tolerances, polypropylene's high coefficient of thermal expansion may result in dimensional instability. In order to mitigate this issue and enhance dimensional stability in crucial applications, glass fibers or reinforcing agents are frequently added to PP composites.
- Flammability: Its flash point (the temperature at which a liquid releases flammable vapor to create a combination that can catch fire when it comes into touch with a spark or flame) is 260 degrees Celsius. When exposed to heat, polypropylene will potentially melt and catch fire. Therefore, flame retardant chemicals are commonly added to PP compounds for electrical components to increase fire resistance.
4. Conclusion
Polypropylene compound is an invaluable choice for modern electrical components. Its insulation properties make it suitable for many applications such as wire insulation, electrical connectors, and terminal blocks. With added reinforcement, the compound can meet various final product requirements and offers a cost-effective solution for business.
5. About EuroPlas' PP Compounds
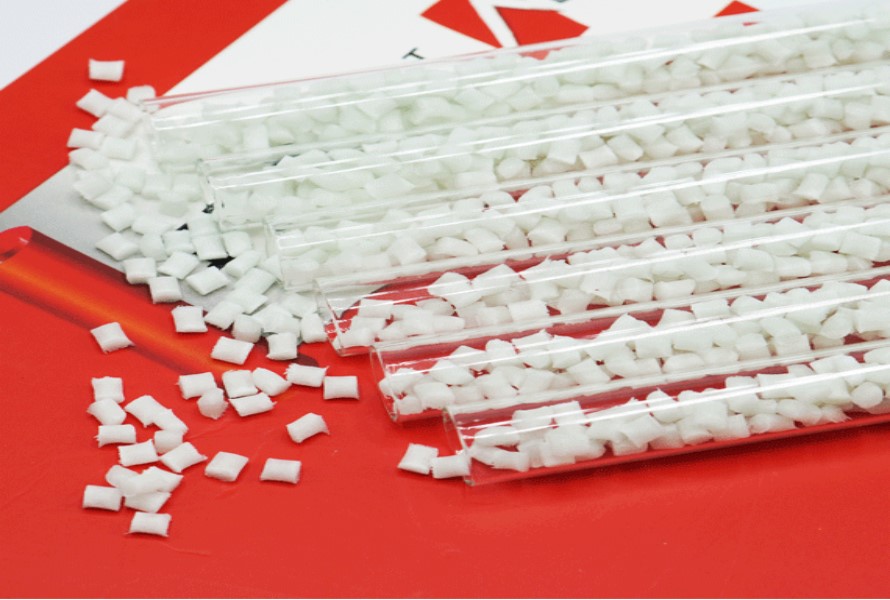
PP compound from EuroPlas
EuroPlas' PP Compounds are strategic tools for manufacturers to achieve durable, adaptable, and cost-saving qualities. We've developed various options suitable for different electrical parts. Our products can ensure safety in flame-retardant wiring, offer impact resistance in connectors, or provide UV protection for outdoor components.
Contact us now to catch up with the latest technologies!