Calcium carbonate is a versatile and commonly used material in the plastic industry. It is used as a filler to improve the properties of plastic products and to reduce the cost of production. The use of calcium carbonate in the plastic industry has been growing rapidly in recent years due to its many benefits, including its availability, low cost, and excellent performance.
In this blog, we will explore the reasons why calcium carbonate used in plastic industry so widely and what makes it a preferred choice among plastic manufacturers. Let’s get started!
Related:
- Top 3 calcium carbonate filler for plastic manufacturers
- Calcium carbonate filler is the most popular used for PP plastics
I. What is calcium carbonate?
1. Definition
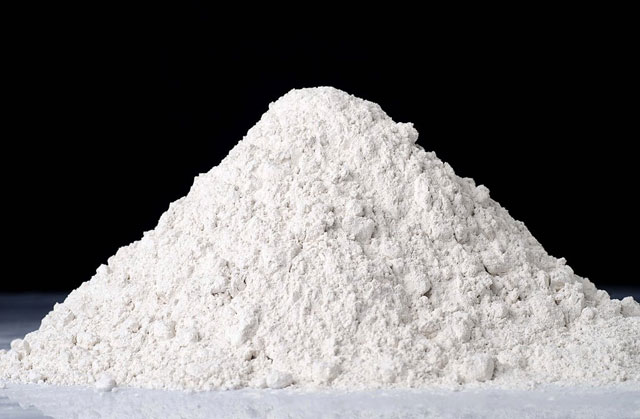
Calcium carbonate (CaCO3) is a chemical inorganic compound. The usage of chalk, which is a type of CaCO3, makes it one of the most well-known compounds that people come into contact with first. It is located in the earth's crust. It may be found in a variety of materials, including marble, limestone, and more. Despite coming in many forms, they are chemically equivalent and only physically differ from one another.
2. Properties
Calcium carbonate has several notable properties, including:
- Chemical composition: Calcium carbonate is a chemical compound with the formula CaCO3.
- Appearance: Calcium carbonate appears as a white, odorless, tasteless powder.
- Solubility: Calcium carbonate is insoluble in water but dissolves poorly.
- Reactivity: Calcium carbonate is a basic compound and reacts with acids to neutralize them.
- Decomposition: When heated, calcium carbonate breaks down, releasing carbon dioxide and calcium oxide (calcination of calcium carbonate and thermal breakdown of calcium carbonate are both conceivable at temperatures above 800°C)
- Hardness: Calcium carbonate has a relatively high hardness and is used as a filler in various industrial applications to improve the hardness and durability of products such as plastics, paints, and rubber.
- Neutralization: Calcium carbonate is commonly used as a neutralizing agent in agriculture, manufacturing, and medicine. It is added to soil to neutralize soil acidity, improving the growth of plants. In medicine, calcium carbonate is used as an antacid to treat indigestion, acid reflux, and heartburn.
- Versatility: Calcium carbonate is widely used in various industries, including construction, agriculture, and manufacturing. In construction, it is used as a building material and in the production of lime. In manufacturing, it is used as a filler, whitening agent, and neutralizing agent in products such as toothpaste, paper, and foods. Also, there are various calcium carbonate uses in plastic nowadays.
- Reactivity: Calcium carbonate reacts with acids to neutralize them, making it a useful component in various chemical processes. It is also used in the production of lime, which is used as a reagent in environmental and chemical processes.
3. Types of calcium carbonate
There are three polymorphic forms of calcium carbonate: calcite, aragonite, and vaterite.
- Calcite: This is the least soluble and most stable mineral. It is a mineral that helps make rocks, and sedimentary, metamorphic, and igneous rocks frequently include it. Sedimentary rocks like marble and limestone frequently include calcite. In addition to many other uses, it is widely employed in the production of building materials and the treatment of agricultural land.
- Argonite: Compared to calcite, it is less stable and more soluble. Aragonite is a rarer form of calcium carbonate that is found in marine environments and hot springs. Physical and biological factors, such as precipitation from freshwater and marine habitats, contribute to its formation. In addition to providing nutrients to marine life, argonite also keeps pH levels at their ideal range. It is applied to clean up wastewater that contains contaminants like lead, cobalt, and zinc.
- Vaterite: Vaterite is hexagonal in form and has a greater solubility than calcite and aragonite. It is also less stable. It can be discovered naturally in plants, biological tissue, gallstones, urinary calculi, and springs. It is used in a variety of personal care items and regenerative medicine.
II. Why calcium carbonate used in plastic industry
Calcium carbonate is widely used in the plastic industry as a filler (filler masterbatch/taical/CaCO3 filler/calcium carbonate filler). It is usually milky white granules composed mainly of CaCO3 and resin base, which is preferred for the following reasons:
- First, it is abundant and easily obtainable, making it a cost-competitive alternative to other filler materials (compared to BaSO4 filler masterbatch, for example). When calcium carbonate used in plastics, it improves the hardness, stiffness, dimensional stability, , and processability of final products.
- Another advantage of using calcium carbonate as a filler is its impact on the processing and stability of the plastic. In the right concentration, calcium carbonate can improve the flow behavior of the plastic and reduce warping and cracking during processing. It also has a positive impact on the stability of the plastic, improving its resistance to UV light and preventing discoloration over time. This leads to calcium carbonate plastic products that have a longer lifespan and maintain their appearance and functionality over time.
- Having calcium carbonate used in plastics is also environmentally friendly. Calcium carbonate is a naturally occurring and biodegradable material, making it an attractive option for companies looking to reduce their environmental footprint and create more sustainable products. It also contributes to reducing the carbon footprint of the plastic industry by reducing the amount of plastic required to produce a product, leading to lighter and more environmentally conscious products.
- In addition to the environmental benefits, the use of calcium carbonate as a filler in the plastic industry has economic benefits as well. By reducing the amount of plastic required to produce a product, the use of calcium carbonate can reduce the cost of production and lead to more competitive pricing for plastic products. This makes calcium carbonate an attractive option for companies looking to reduce costs and remain competitive in the marketplace.
In conclusion, calcium carbonate is a versatile and widely used filler material in the plastic industry due to its availability, low cost, and positive impact on the properties of plastic products. Its use has been growing rapidly in recent years, and it is likely to continue to be a preferred choice among plastic manufacturers in the future.
III. Calcium carbonate uses in plastic
1. Calcium carbonate filler for packaging products
Filler masterbatch made from CaCO3 and LDPE, LLDPE, MDPE, MPE and HDPE resins can be applied to LDPE, HDPE bag blowing products, helping to improve physical performance and properties.
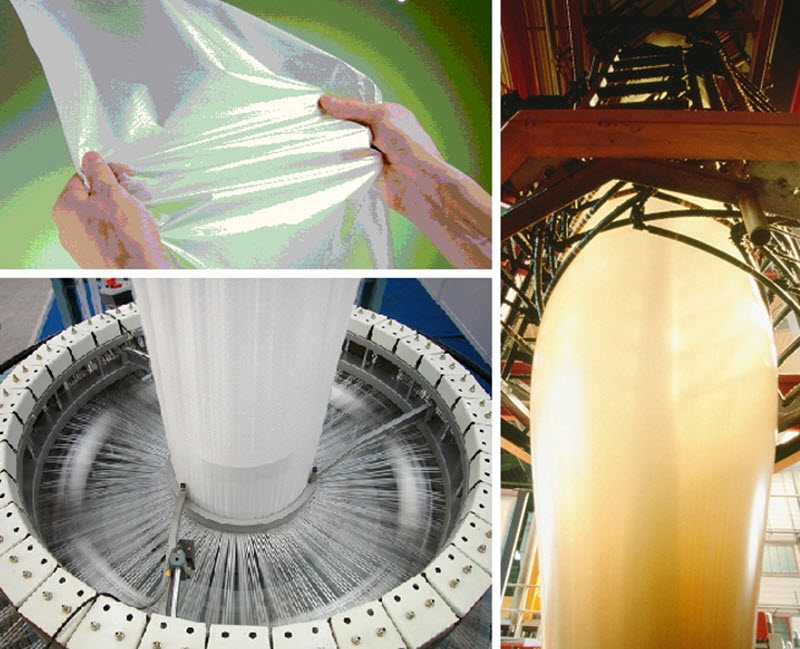
Calcium carbonate resin fillers bring advantages to the end product such as:
- Reducing the cost of raw materials
- Increasing product hardness
- Improving impact resistance by falling weight method
- Improving tear resistance
- Increasing air resistance for packaging products
- Increasing the shape of packaging products
The applications of calcium carbonate filler materials in packaging products are agricultural mulch, food wraps in supermarkets, shopping bags, heavy product bags...
2. Calcium carbonate filler for lamination products
Plastic fillers with CaCO3 as the main raw material and PE, PP resins are applied to film-coated products and laminated products.
Why use Taical in laminating products? The answer is that it offers the following benefits:
- Increasing formability for laminating and coated films
- Increasing film coverage, reducing color usage rate when coating
- Increasing the printing process on packaging products
3. Calcium carbonate filler for thermoforming sheet
Using CaCO3 with a ratio of up to 60% in PP has proven to be an alternative to PS. It gives the same performance of production line and product quality.
a. Improving thermo conductivity
- Faster melting in extruder
- More homogeneous molten plastic mixture
- Faster cooling on rolling screw
=> Higher extrusion line speed
b. Low coefficient of expansion
- Reducing plastic volume when melted
- Reducing friction with the machine's inner surface
- Reducing extruder load and extrusion head pressure
=> Increasing extruder productivity (by volume)
C. Improving mechanical properties
- Increasing stiffness
The graph shows that calcium carbonate helps the product to increase the horizontal and vertical elastic stress by 15% and 30%.
- Enhancing impact resistance
DDI increased by 250% (same weight or same thickness)
- Reducing shrinkage/shape deformation after processing
Yoghurt cup after 30 minutes at 140°C
- Increasing economic efficiency
Common applications of calcium carbonate fillers in thermoforming are disposable cups, plates, food trays, cups and lids, potted plants and seed trays, construction profiles, home appliances, car parts,...
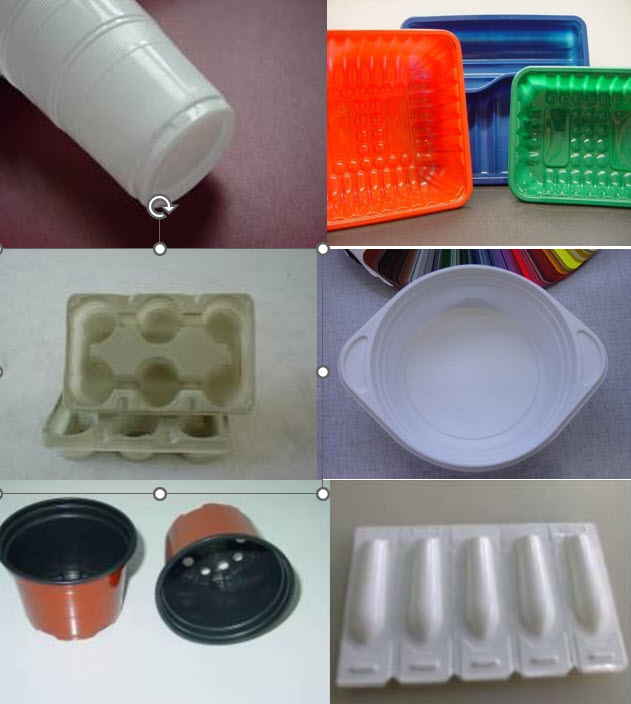
4. Calcium carbonate filler for bottle
The most important benefit of using calcium carbonate filler in bottle blowing application is the high heat transfer property and low specific heat of taical. Here are the important benefits of using CaCO3 in bottle blowing:
- Increasing elastic stress
- Maintaining top load and drop weight impact resistance.
- Increasing ESCR (Stress Cracking Resistance)
- Reducing production cycle time
- Reducing melting temperature
- Reducing the amount of TiO2 needed
- Better printability
5. Calcium carbonate filler for non-woven fabric
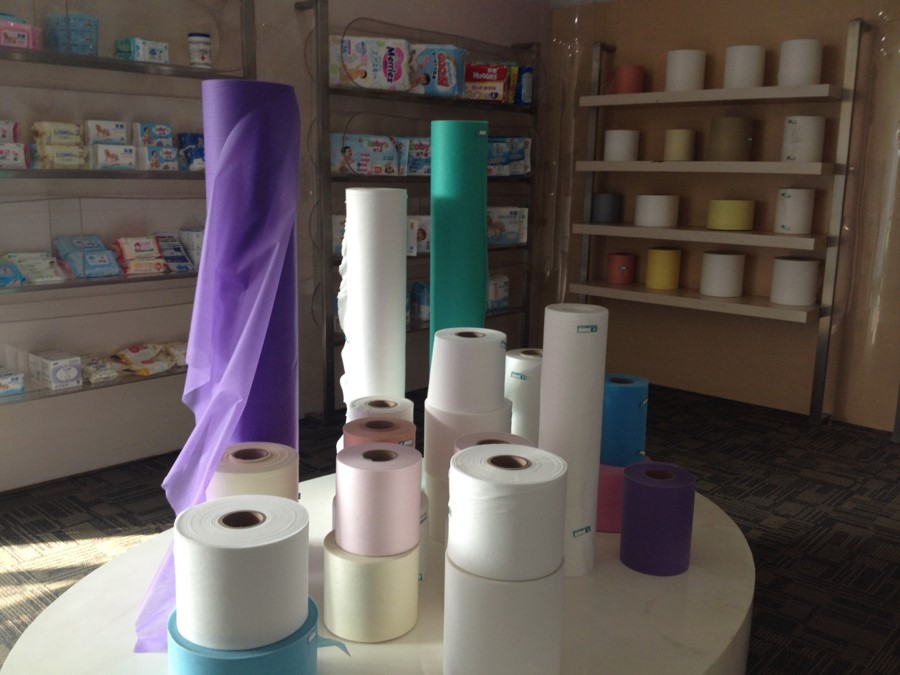
Non-woven fabrics are widely used products in daily life. Specifically, it is the material for the fields of:
- Hygiene: diapers for children and adults, hygiene products for women
- Medical: protective clothing
- Technical applications: architecture, coated fabrics, agricultural & geological mulch, filter equipment, disc covers, cleaning cloths,...
Using calcium carbonate filler for nonwovens offers the following benefits:
- Anti slip
- Soft touch
- Cool
- Elastic stress
- Antistatic
- Solderability
- Scroll speed
- Line performance
- Increasing productivity
- Reducing the cost of raw materials
6. Calcium carbonate filler for raffia and bag spinning
Calcium carbonate filler is commonly used in PE or PP woven bags, ropes/belts with anti-separation and anti-fibrillation effects. Masterbatch fillers with suitable CaCO3 strains will provide the following benefits:
- Reducing separation of oriented polypropylene
- Increasing hardness
- Reducing the amount of TiO2 used
- Reducing the proportion for raw materials
- Increasing the dimensional stability of the product
- Increasing the orientation of the yarn after extrusion
- Increasing yarn whiteness, reducing color usage rate
- Increasing the elastic modulus of the yarn
Image under scanning electron microscope (SEM): Yarn surface (top image) and yarn cross-section (bottom image)
7. Calcium carbonate filler for injection molding products
Europlast has developed CaCO3 filler widely used in injection molding applications. The product is manufactured with high-grade CaCO3 and special-shaped materials. It meets most of the Injection Molding (PE, PP, HIPS) plastic products requirements and enhances the mechanical properties of the product.
The use of CaCO3 filler in injection molding products is a proven solution to improve product properties and productivity. It is widely used in interior products, home appliances, and car parts.
The main benefits of using Calcium carbonate masterbatches include
- Higher stiffness
- Improved impact resistance
- Less shrinkage
- Better isotropic physical properties
- Improved product dimensional stability
- Higher heat distortion temperature under load
- Reduced machining cycle times due to faster cooling
IV. Finding calcium carbonate filler for plastics?
EuroPlas is a world’s largest calcium carbonate filler manufacturer based in Vietnam that offers a range of products, including calcium carbonate filler for plastics. Our masterbatch is made from high-quality, natural calcium carbonate that is ground into a fine powder and processed to meet the specific needs of the plastic industry. The product is characterized by its high purity, brightness, and excellent dispersion, making it an ideal choice for plastic manufacturers looking for a cost-effective and reliable filler.
We use state-of-the-art technology and equipment to manufacture high-quality calcium carbonate filler masterbatch and its products undergo strict quality control measures to ensure they meet international standards. With over 15 years of experience, our company's knowledgeable staff is always available to assist customers and provide technical support, ensuring that the best products are delivered to meet their specific needs.
Our commitment to customer satisfaction and quality control makes us a top choice for plastic manufacturers looking for cost-effective and high-quality filler. Hence, if you are looking for a reliable and trustworthy supplier of calcium carbonate filler masterbatch, please
contact us and we shall help you with everything!