Drying plastic before production is a critical step that often determines the success of the final product. Moisture in plastics can cause defects, affecting their performance, appearance, and overall quality. This article delves into why drying plastic is essential, the various methods available, and provides a detailed guide to drying different types of plastics effectively.
1. Why Do We Need To Dry Plastic First?
Drying plastic before processing is necessary to remove moisture that could lead to several issues during manufacturing. Here are the primary reasons why drying plastic is crucial:
.jpg)
Dry plastic before processing to remove moisture.
- Preventing Hydrolysis: Moisture can cause hydrolysis in certain plastics, breaking down polymer chains and reducing the material's mechanical properties. This is especially critical for hygroscopic plastics like nylon and polycarbonate.
- Avoiding Surface Defects: Excess moisture can lead to surface defects such as bubbles, voids, and streaks, which not only affect the appearance but also the integrity of the final product.
- Improving Dimensional Stability: Moisture can cause plastics to expand or contract, leading to dimensional inaccuracies in the final product. Proper drying ensures consistent size and shape.
- Enhancing Mechanical Properties: Removing moisture helps maintain the strength, flexibility, and impact resistance of plastics, ensuring they perform as intended in their applications.
2. Plastic Drying Methods
There are several methods to dry plastic effectively, each suitable for different types of materials and production scales. Here are the most common plastic drying methods:
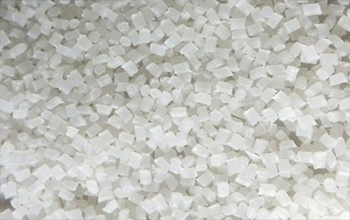
Plastic drying methods.
- Hot Air Dryers: These dryers use heated air to evaporate moisture from the plastic granules. They are suitable for non-hygroscopic plastics that require minimal drying.
- Desiccant Dryers: Desiccant dryers use a desiccant material to absorb moisture from the air surrounding the plastic granules. They are highly effective for hygroscopic plastics that need thorough drying.
- Vacuum Dryers: Vacuum dryers remove air pressure, reducing the boiling point of water and allowing moisture to evaporate at lower temperatures.
- This method is efficient and prevents thermal degradation of heat-sensitive plastics.Infrared Dryers: Infrared dryers use infrared radiation to heat the plastic granules directly, evaporating moisture quickly. This method is energy-efficient and provides fast drying times.
3. A Guide To Dry Plastic
Properly drying plastic involves setting the right temperature and drying time specific to each type of plastic. The table below provides a guide to drying different types of plastics, including the recommended temperature and drying time for optimal results.
Type of Plastic |
Drying Temperature (°C) |
Drying Time (hours) |
Nylon (Polyamide) |
80-90 |
2-4 |
Polycarbonate (PC) |
120-130 |
3-4 |
Acrylic (PMMA) |
70-80 |
3-4 |
PET (Polyethylene Terephthalate) |
150-160 |
4-6 |
ABS (Acrylonitrile Butadiene Styrene) |
80-90 |
2-3 |
PBT (Polybutylene Terephthalate) |
110-120 |
2-3 |
TPU (Thermoplastic Polyurethane) |
95-105 |
2-3 |
POM (Polyoxymethylene) |
80-90 |
2-3 |
PE (Polyethylene) |
65-75 |
1-2 |
PP (Polypropylene) |
80-90 |
1-2 |
4. Conclusion
Drying plastic is a fundamental step in the production process that ensures high-quality, defect-free final products. By understanding the importance of drying, choosing the appropriate method, and following the specific drying guidelines for different types of plastics, manufacturers can achieve optimal performance and reliability in their plastic products. Properly dried plastics lead to improved mechanical properties, dimensional stability, and overall product quality, making it an indispensable part of the manufacturing process.
5. About EuroPlas
EuroPlas is a leading provider of plastic additives, offering a wide range of solutions to enhance the quality and performance of your plastic products. Our additives include odor absorbers, desiccants, flame retardants, anti-fog agents, anti-aging agents, processing aids, anti-static agents, UV stabilizers, and optical brighteners. At EuroPlas, we understand the critical role of properly dried plastic in production and offer tailored solutions to help you achieve the best results. Whether you are dealing with hygroscopic or non-hygroscopic plastics, our experts can guide you in selecting the right additives and drying methods to optimize your manufacturing processes. Contact EuroPlas today and visit our blog for the latest insights and advancements in plastic manufacturing.