1. Introduction
Polyethylene Resin is one of the most widely used polymers in the world today. Its popularity is largely due to its unique combination of properties – it is lightweight, durable, chemically resistant, and cost-effective to produce. These characteristics make Polyethylene Resin the material of choice in a wide range of industries, including packaging, construction, healthcare, and automotive sectors.
In everyday life, Polyethylene Resin plays an essential role. Whether you are using a plastic bag, a water bottle, or a protective film for your food, you are directly benefiting from the advanced technology behind Polyethylene Resin. Its ability to be molded into various shapes and forms means that it is not only practical but also highly adaptable. This adaptability has led to its widespread use in products that touch nearly every aspect of modern living.
2. Types of Polyethylene Resin and Their Applications
2.1. Low-Density Polyethylene (LDPE)
LDPE is characterized by its low density and high flexibility, making it ideal for applications where a soft, pliable material is required.
- Applications: LDPE is commonly used in manufacturing plastic bags, food wraps, and squeeze bottles. Its transparency and flexibility allow for easy manipulation and durability in everyday use.
- Impact: The use of LDPE in packaging not only helps preserve food but also reduces waste by extending the shelf-life of products.
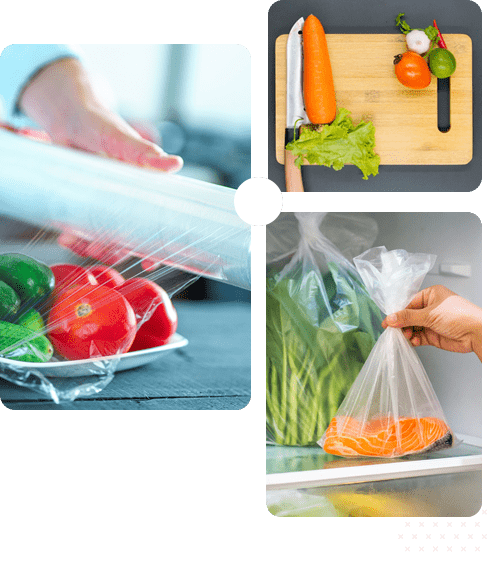
Applications of LDPE in the production of plastic bags and food wraps
2.2. High-Density Polyethylene (HDPE)
HDPE is known for its strength and rigidity, thanks to its highly crystalline structure.
- Applications: This type of Polyethylene Resin is widely utilized in producing rigid containers, water pipes, and large storage tanks. Its toughness ensures that products remain secure and intact under heavy loads or extreme conditions.
- Impact: HDPE’s durability is critical in industries that require reliable and long-lasting materials, such as construction and infrastructure, where safety and performance are paramount.
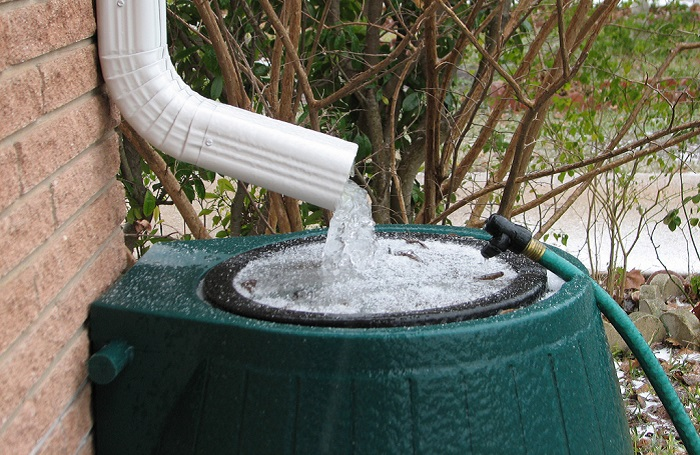
Applications of HDPE in the production of water pipes and large storage tanks
2.3. Linear Low-Density Polyethylene (LLDPE)
LLDPE offers a balance between the properties of LDPE and HDPE, featuring better tensile strength and puncture resistance than LDPE while maintaining a degree of flexibility.
- Applications: It is predominantly used in manufacturing stretch films, flexible packaging, and agricultural films.
- Impact: The superior strength of LLDPE ensures that the films and packaging produced are both secure and adaptable to various shapes, enhancing the protection of goods during storage and transportation.
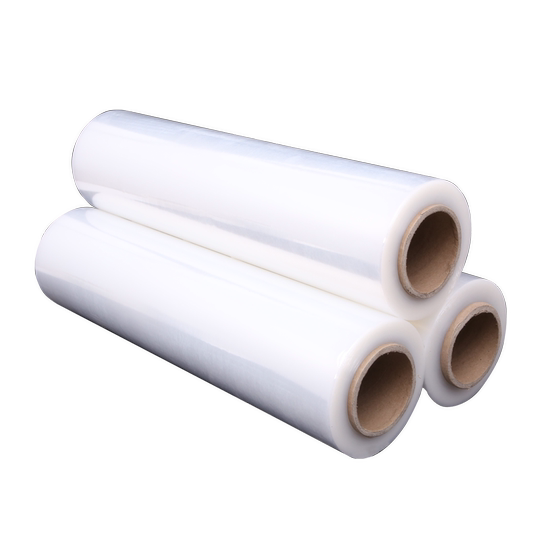
Applications of LLDPE in the production of stretch films and agricultural films
2.4. Ultra-High Molecular Weight Polyethylene (UHMWPE)
UHMWPE stands out due to its extremely long molecular chains, which result in exceptional strength and wear resistance.
- Applications: It is used in critical applications such as medical devices, prosthetics, and even bulletproof vests.
- Impact: The remarkable durability and resistance to abrasion make UHMWPE ideal for situations where safety and longevity are crucial. Its use in protective gear and medical applications demonstrates the high-performance nature of Polyethylene Resin in life-saving contexts.
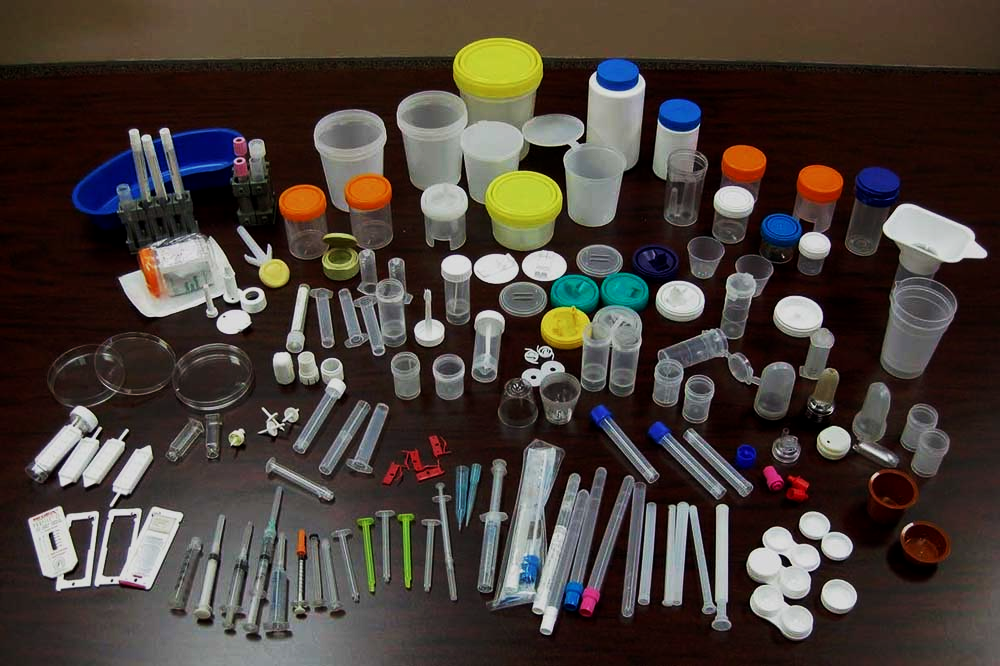
Applications of UHMWPE in the production of medical devices
3. Key Benefits of Polyethylene Resin in Everyday Life
3.1. Lightweight & Durable
One of the most significant advantages of Polyethylene Resin is its lightweight nature, which reduces transportation costs and energy consumption. Despite its low weight, this resin offers excellent durability.
Practical Examples: Products made from Polyethylene Resin can withstand daily wear and tear, whether they are packaging materials that protect food or containers that store water and chemicals. This combination of lightness and strength makes it a preferred choice in both consumer and industrial applications.
3.2. Chemical & Moisture Resistance
Polyethylene Resin exhibits outstanding resistance to chemicals and moisture.
Practical Examples: This property is particularly important in the food and medical industries where contamination must be minimized. Containers made from Polyethylene Resin can safely store a wide range of chemicals without degrading, ensuring that they maintain their integrity even under harsh conditions.
Impact on Health and Safety: In medical devices, the inert nature of Polyethylene Resin means it does not react with bodily fluids, making it an excellent choice for implants and other critical applications.
3.3. Cost-Effective & Easy Processing
The cost-effectiveness of Polyethylene Resin is another major factor in its widespread use. The production process is relatively simple, and the material itself is inexpensive compared to other polymers.
Practical Examples: The ease of processing allows manufacturers to produce large quantities of products quickly, reducing production costs and ultimately making the end products more affordable for consumers.
Economic Impact: The economic benefits extend to various industries where cost savings translate into competitive pricing and broader accessibility of products.
3.4. Recyclability & Sustainability
In today’s eco-conscious market, sustainability is a key concern, and Polyethylene Resin offers promising advantages.
Recycling Benefits: Polyethylene Resin can be recycled and reprocessed into new products, reducing the environmental footprint associated with plastic waste.
Future Outlook: With ongoing innovations in recycling technology and the development of bio-based alternatives, the sustainable aspects of Polyethylene Resin are expected to improve even further, making it an even more attractive material for environmentally responsible manufacturing.
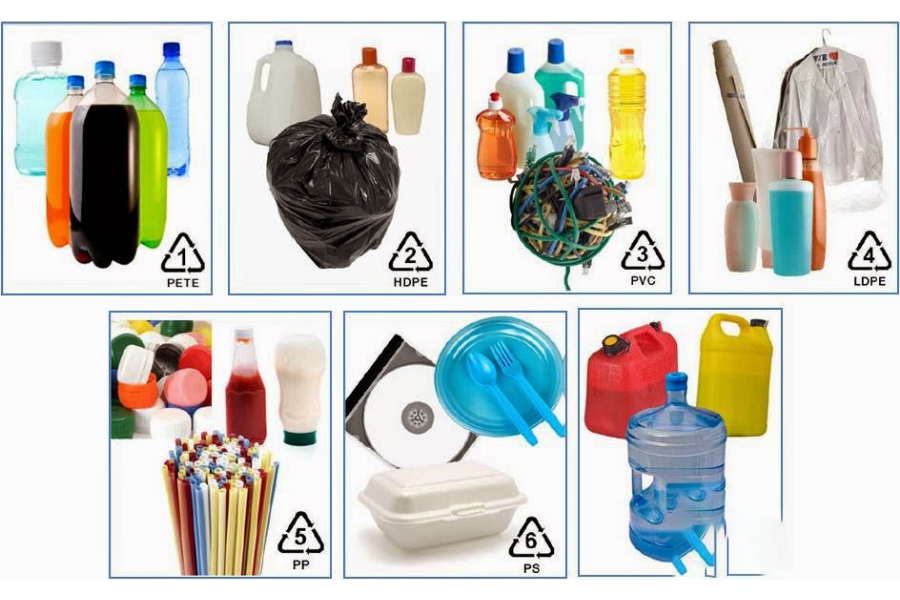
Recyclability of Polyethylene Resin
4. Future Trends in Polyethylene Resin
4.1. Bio-Based and Recycled Polyethylene
As the global community becomes increasingly aware of environmental issues, there is a strong trend toward the development of bio-based Polyethylene Resin.
Sustainability: Bio-based Polyethylene Resin is derived from renewable resources, offering a greener alternative to conventional petrochemical-based products.
Recycling Innovations: Advances in recycling technology are expected to further improve the efficiency of reprocessing Polyethylene Resin, reducing waste and promoting a circular economy.
4.2. Emerging Industrial Applications
The versatility of Polyethylene Resin means that its use is expanding into new and innovative applications.
Advanced Industries: Sectors such as automotive, aerospace, and electronics are beginning to incorporate specialized forms of Polyethylene Resin due to its lightweight and durable properties.
Health and Safety: In addition to traditional uses, the development of high-performance variants like UHMWPE for protective gear and medical devices underscores the material’s role in improving safety and performance in critical applications.
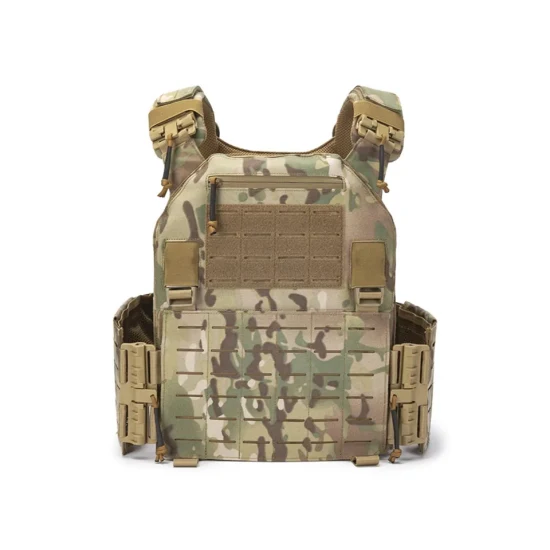
Applications of UHMWPE in the production of protective gear
4.3. Technological Integration
Ongoing research and technological advancements are expected to enhance the properties of Polyethylene Resin even further.
Performance Enhancement: Innovations in polymer processing and nanotechnology may lead to the creation of hybrid materials that combine the best features of Polyethylene Resin with other high-performance materials.
Customization: This trend towards material customization will allow manufacturers to tailor Polyethylene Resin to meet specific requirements, further increasing its applicability across diverse industries.
5. Conclusion
Polyethylene Resin is more than just a common plastic – it is a transformative material that underpins much of our modern lifestyle. Its versatility, cost-effectiveness, and environmental benefits make it indispensable across a range of applications. From everyday packaging solutions to high-performance industrial and medical products, Polyethylene Resin continues to drive innovation and improve quality of life.
In summary, Polyethylene Resin is important in real life because it is lightweight, durable, chemically resistant, and sustainable. Its various types, including LDPE, HDPE, LLDPE, and UHMWPE, cater to different needs and industries, ensuring that there is a solution available for almost every application. As research and development continue to push the boundaries of what is possible with Polyethylene Resin, we can expect even more innovative uses and improved performance in the future.
6. About EuroPlas’ PE Filler Masterbatch
EuroPlas is a leading manufacturer of innovative polyethylene packaging solutions. With a strong commitment to quality and sustainability, EuroPlas has established itself as a trusted brand in the plastics industry, providing high-performance products that meet the ever-evolving needs of various industries, including food, cosmetics and consumer goods.
One of EuroPlas’s standout products is PE Filler Masterbatch, designed to enhance the properties of polyethylene packaging. This product not only improves the quality of the packaging material but also reduces production costs. By incorporating calcium carbonate into the polyethylene matrix, PE Filler Masterbatch significantly increases the stiffness and impact resistance of the final product, making it more durable and reliable during transportation and storage.
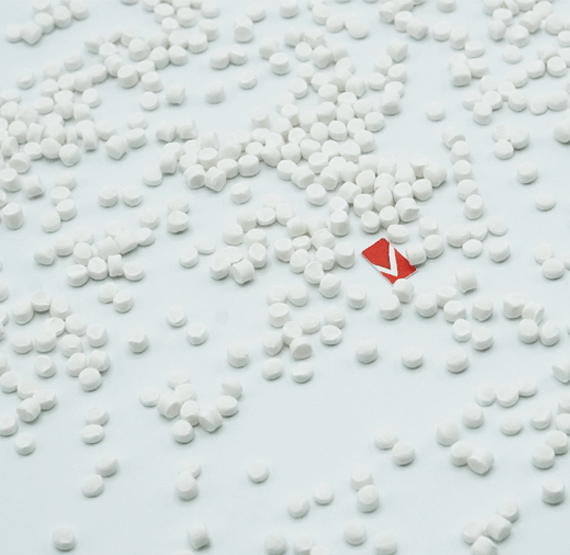
PE filler masterbatch of EuroPlas
EuroPlas’ polyethylene packaging solutions are known for their versatility. They are used in a wide range of applications, from flexible plastic films and bags to rigid containers, ensuring that businesses can find the right packaging for their specific requirements.
With a focus on innovation, quality and environmental awareness, EuroPlas has established itself as a leader in the Vietnamese PE packaging industry. If you are looking for quality and cost-effective PE packaging solutions, EuroPlas is a reliable choice. For more information, contact us today or visit our blog for in-depth insights on PE packaging solutions!