In the world of materials, certain characteristics reign supreme, determining their suitability for a wide spectrum of applications. Among these, durability, friction coefficient, and self-lubricity stand out as essential properties that dictate the performance and longevity of various components and systems. One material that consistently excels in these aspects is Ultra-High Molecular Weight Polyethylene (UHMW). In this article, let's find out why UHMW is different from other materials of the same type.
1. What is UHMW and its unique qualities?
UHMW is a thermoplastic material composed of long, linear chains of polyethylene molecules. The molecular weight of a material refers to the combined mass of all the atoms in a single molecule. UHMW stands out with exceptionally long molecular chains, resulting in a very high molecular weight. This distinct characteristic imparts remarkable properties to the material, making it exceptionally durable, resistant to wear, and possessing a low friction coefficient.
UHMW's exceptional molecular weight is just one of the many qualities that make it stand out among other materials. UHMW (Ultra-High Molecular Weight) exhibits others such as self-lubrication, a non-adherent surface, excellent chemical resistance, impact resistance, ease of machinability, and good noise-dampening properties.
It performs exceptionally well at extremely low temperatures, such as -259 degrees Celsius, and retains its abrasion resistance characteristics up to temperatures of 185 degrees Fahrenheit.
Let's delve deeper into some of the aspects:
- Noise reduction: UHMW compounds minimize noise generation by reducing friction and contact with other components during movement.
- Self-lubrication: The distinctive molecular structure of UHMW polymers results in a self-lubricating material that exhibits exceptional wear and abrasion resistance, while also providing high-impact strength.
- Corrosion resistance: UHMW polymers are highly resistant to corrosion, making them well-suited for applications involving contact with corrosive chemicals, such as acids.
- Low friction: UHMW polymers possess a low coefficient of friction, making them ideal for the production of chain channels, wear strips, belt scrapers, guides, and rollers. Research indicates that the dynamic friction coefficient for ultra-high-density polyethylene under dry conditions averages around 0.1, indicating minimal friction.
- Low moisture absorption: With an absorption rate of less than 0.01%, UHMW is a popular choice for a wide range of marine and other applications that require exposure to high levels of humidity and moisture.
Read more: A guide to ultra-high molecular weight polyethylene (UHMW plastic)
2. Unparalleled Durability
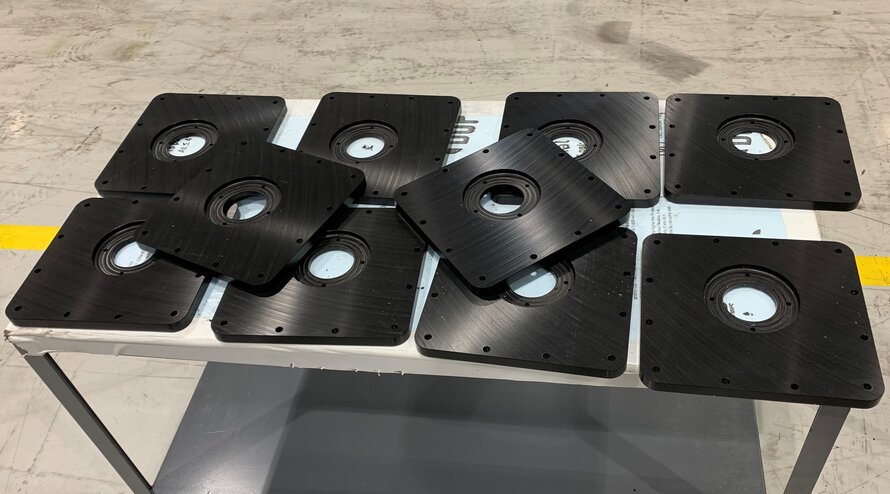
UHMW owning unparalleled durability has become a popular choice in various industries
The extended molecular chains in UHMW form a dense, tightly packed structure, resulting in exceptional durability. This inherent toughness makes it resistant to abrasion, impact, and various other forms of wear and tear. In fact, UHMW has a wear resistance six times higher than steel and fifteen times higher than carbon steel, making it one of the most durable materials available.
The molecular weight of UHMW can range from 3 to 6 million, so it is considered one of the heaviest molecules in the world. This high molecular weight gives UHMW incredible strength and durability, allowing it to withstand extreme conditions and heavy loads without showing signs of wear.
Thanks to exceptional durability, UHMW has become a popular choice in various industries, including automotive, aerospace, construction, and marine. In the automotive industry, UHMW is used for components such as gears, bearings, and bushings due to its ability to withstand high speeds and heavy loads.
In the aerospace industry, UHMW is used for aircraft components that require high strength and durability, such as wing flaps and landing gear. In the construction industry, UHMW is used for wear-resistant parts in machinery and equipment, while in the marine industry, it is used for boat hulls and propellers due to its resistance to saltwater corrosion.
3. Low Friction Coefficient
A material's friction coefficient refers to the amount of resistance it creates when two surfaces come into contact with each other. A low friction coefficient means less resistance, resulting in smoother movement and less wear on the surfaces. UHMW has an extremely low friction coefficient, making it an ideal material for applications where reduced friction is crucial.
A low friction coefficient is essential in many industries, including manufacturing, transportation, and medicine medical. In manufacturing, a low friction coefficient allows for smooth movement of materials and reduces the risk of damage or wear on machinery. In transportation, it reduces energy consumption and increases efficiency by reducing the amount of force needed for movement. In the medical field, a low friction coefficient is crucial for prosthetics and joint replacements, ensuring smooth and natural movement without causing damage to surrounding tissues.
UHMW's long molecular chains and smooth surface make it an ideal material for reducing friction. Its low coefficient of friction allows for easy movement, even under heavy loads; therefore, it has become a popular choice for conveyor belts, bearings, and other moving parts.
Additionally, UHMW's self-lubricating properties further reduce friction by creating a thin film of lubrication between surfaces, resulting in smoother and more efficient movement.
UHMW's low friction coefficient makes it a top choice for various applications where smooth movement and reduced wear are essential. In the food industry, UHMW is used for conveyor belts and packaging equipment to ensure the safe and efficient movement of food products without contamination. In the textile industry, it is used for spinning and weaving machinery to reduce friction and increase efficiency.
For the automotive industry, UHMW is used for gears and bearings to reduce friction and improve fuel efficiency. These are just a few examples of how UHMW's low friction coefficient has significantly impacted various industries.
4. Self-Lubricating
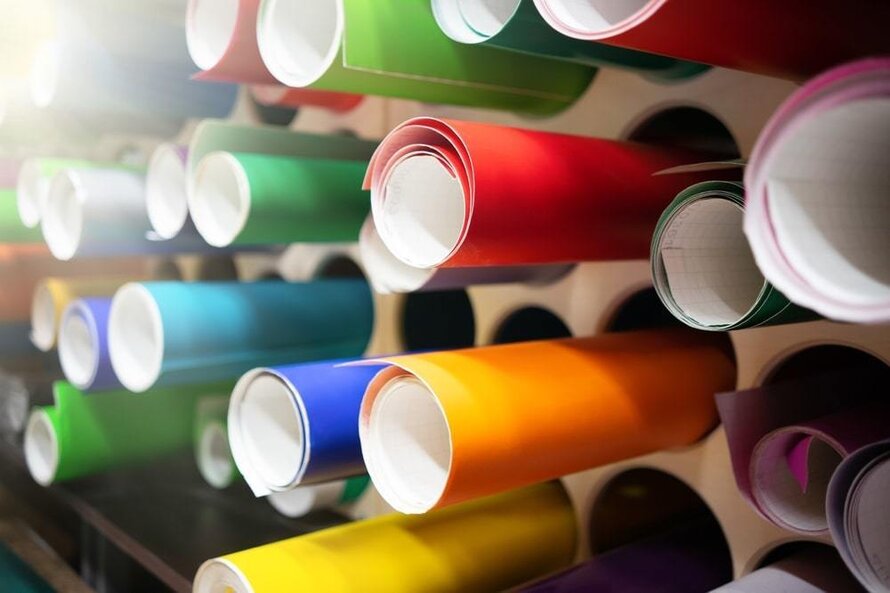
UHMW stands out as self-lubricating
One of the most unique qualities of UHMW is its self-lubricating properties. This means that it can create its own lubrication, eliminating the need for external lubricants such as oils or greases. This not only reduces maintenance costs but also makes it a cleaner and more environmentally friendly option.
UHMW's long molecular chains have a natural affinity for each other, causing them to repel water and other liquids. This results in a self-lubricating effect, where the molecules slide over each other with minimal resistance, creating a smooth and slippery surface. This property is especially beneficial in applications where traditional lubricants may not be suitable, such as in food processing or medical equipment.
Because of its self-lubricating properties, UHMW is a top choice for various applications where traditional lubricants may not be suitable or practical. In the food industry, UHMW is used for cutting boards, food processing equipment, and packaging machinery due to its ability to create a natural barrier against bacteria and other contaminants.
For the medical field, UHMW is used for surgical instruments and implants due to its biocompatibility and self-lubricating properties. These are just a few examples of how UHMW's self-lubricating properties have made it an invaluable material in various industries.
5. Conclusion
To sum up, UHMW stands out as a remarkable material due to its many properties, notably its exceptional durability, low coefficient of friction, and self-lubricating properties. From reducing wear and tear on machinery to increasing overall efficiency and performance, UHMW has proven time and time again why this material is unrivaled. As the materials industry continues to evolve, the more we can imagine the endless possibilities and innovations that UHMW will bring.
EuroPlas takes pride in being the world's largest producer of filler masterbatch, providing specialized material solutions to empower plastic businesses in enhancing their competitive edge. Additionally, we offer a wide range of prominent plastic materials, including engineering plastic compounds, bio filler, plastic additives etc. Stay tuned to our blog for the latest updates on various plastic materials. If you are interested in learning more about a specific type of material, do not hesitate to contact us. EuroPlas is always ready to assist you.