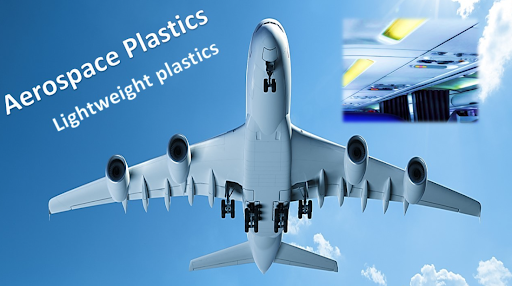
Aerospace plastics have been and are contributing greatly to reducing weight and improving fuel efficiency
Aerospace plastics are a special type of plastic used in the manufacturing process of aerospace equipment. For this use, aerospace plastics need to meet quite strict requirements such as light weight, durability over time, good impact resistance, resistance to harsh weather and resistance to chemicals. Thanks to that, aerospace plastics have been and are contributing greatly to reducing weight and improving fuel efficiency. In particular, aerospace plastics are inherently extremely flexible. These types of aerospace plastics can be molded into a variety of designs from simple to complex on aircraft systems.
1. How Does Aerospace Plastics Help?
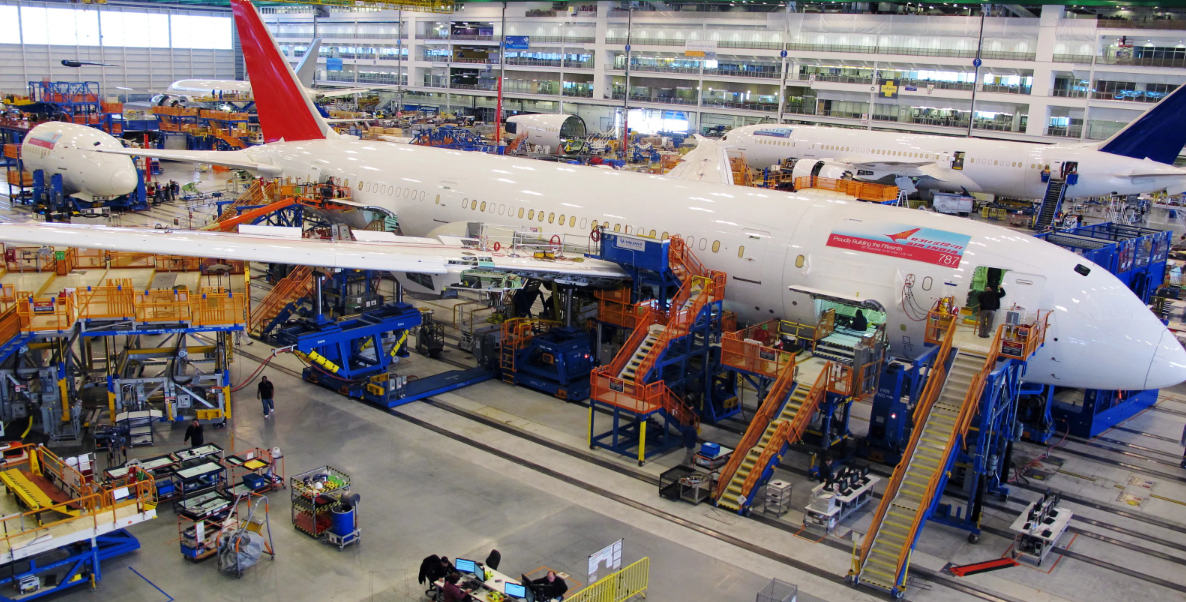
Aerospace plastics help people find more creative and cost-effective solutions in both production and operation
Aerospace plastics contribute to the development of this industry by improving the efficiency, performance and safety of aircraft. Taking advantage of the benefits of aerospace plastics helps people find more creative and cost-effective solutions in both production and operation. Here are the benefits that aerospace plastics bring:
Reduced weight: Thanks to their significantly lighter weight than traditional metals, aerospace plastics help reduce weight significantly. This is one of the extremely essential benefits to improve fuel efficiency, increase load capacity and improve the overall performance of both aircraft and spacecraft.
Improved durability: Aerospace plastics possess good resistance to harsh conditions. They can work well in high temperature environments, strong mechanical stress and chemical exposure but with extremely low damage rates. The durability of aerospace plastics helps components perform better and maintain the integrity of the machine over time. As a result, maintenance and repair are also reduced.
Cost-effective: Thanks to the light weight of aerospace plastics, fuel consumption is also significantly improved. Saving fuel costs is one of the key factors contributing to the development of commercial aviation. In addition, aerospace plastics possess high durability, so the need for maintenance is lower, leading to lower long-term costs.
Flexibility in design: Most lines of aerospace plastics are very flexible in the shaping process. They are suitable for a variety of manufacturing processes such as injection molding, extrusion, 3D printing, blow molding, etc. Thanks to that, engineers can design increasingly creative and convenient aircraft structures.
Heat and chemical resistance: Operating in the aviation environment also means that aerospace plastics must withstand extremely harsh operating environments. They meet the needs of operating in erratic weather and extreme temperature changes. In addition, the process of operating aircraft also requires aerospace plastics to ensure good maintenance when exposed to specialized chemicals for a long time.
Improved safety: Aerospace plastics are considered extremely reliable materials for long-term use in extremely harsh conditions. Therefore, they are also considered a reputable material that helps ensure the safety of aerospace systems.
Electromagnetic shielding: Protecting sensitive electronic devices from interference is one of the roles of aerospace plastics. From there, aerospace plastics help aircraft operations to be smoother and more precise.
Read more: What is plastic? Everything you need to know about plastic
2. A List Of Aerospace Plastics
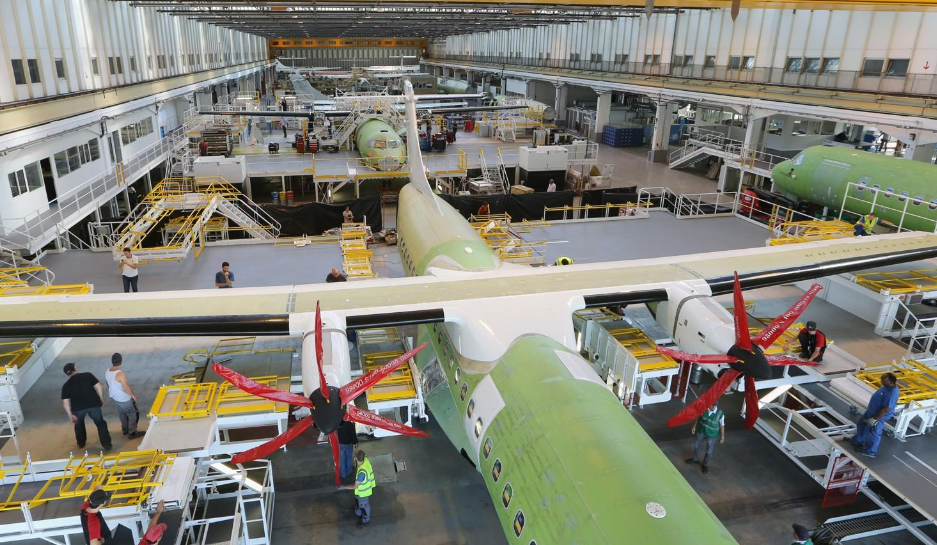
Aerospace plastics are divided into many diverse groups, so it is important to stay informed about each individual group
2.1. Polyetheretherketone (PEEK)
PEEK is a popular aerospace plastic. It is a high-performance, semi-crystalline thermoplastic polymer. This type of aerospace plastic is known for its high mechanical strength and stability. Some of the typical properties of PEEK include high tensile strength, excellent chemical resistance, and the ability to withstand continuous temperatures up to 250°C (482°F). It also exhibits good resistance to friction and wear.
For aircraft, this type of aerospace plastic is used in demanding applications such as bearings, seals, and structural components in engines where high temperature environments are common. In addition, this type of aerospace plastic is also popular in electrical insulating parts.
2.2. Polytetrafluoroethylene (PTFE)
Among the aerospace plastics, PTFE is also a frequently mentioned plastic. It is also known as Teflon. This is a fluorinated polymer with a non-stick, low-friction surface. PTFE has good chemical resistance, a low coefficient of friction, and limited reactivity in all chemical environments. In addition, this type of aerospace plastics can operate at temperatures up to 260°C (500°F).
In the aerospace industry, PTFE is used to make coatings and linings for aircraft components. This type of aerospace plastic provides friction-reducing and wear-resistant properties for equipment. It is also used in electrical insulation, seals, and gaskets.
2.3. Polycarbonate (PC)
PC plastic is also one of the prominent types when talking about aerospace plastics. This is a durable thermoplastic polymer known for its transparency and good impact resistance. In addition, this type of aerospace plastic has good dimensional stability and is optically clear. It can withstand temperatures up to 135°C (275°F) and is relatively easy to mold. PC plastic is transparent, so it perfectly meets the needs of optical components.
Common applications that this type of aerospace plastics often contributes to are aircraft windows, cockpit canopies, aircraft light covers, etc.
2.4. Polyimide (PI)
In the group of aerospace plastics, PI plastic is a fairly popular line today. This is a high-performance polymer with excellent thermal stability and mechanical properties. It can withstand high temperatures up to 400°C (752°F). Low thermal expansion makes it very popular in components that require good heat resistance.
For the aerospace industry, this type of aerospace plastics is used to design insulation parts, flexible circuits and high-temperature aerospace components. This type of aerospace plastics is essential for components exposed to extreme temperatures.
2.5. Polyphenylene sulfide (PPS)
PPS is a plastic line that is of great interest when it comes to aerospace plastics. They belong to the group of thermoplastics that are resistant to high temperatures, resistant to chemicals and have high dimensional stability. This type is also one of the groups with excellent heat and chemical resistance. It is known that they can operate continuously for a long time in an environment with temperatures up to 260°C (500°F). In addition, this type of aerospace plastics also exhibits low moisture absorption and high mechanical strength. In particular, PPS operates durably in harsh chemical environments.
Thanks to its chemical resistance and high stability, aerospace plastics are often used to design parts in fuel systems, electrical insulation devices, and chemical transmission parts on aircraft.
3. Conclusion
In conclusion, aerospace plastics play a pivotal role in advancing the aviation and aerospace industry. Their unique properties such as light weight, durability, and resistance to harsh conditions make them indispensable in the creation of ever-advancing aerospace technologies. Aerospace plastics are divided into many diverse groups, so it is important to stay informed about each individual group. Understanding the properties and strengths of each type will go a long way in optimizing product performance.
4. About EuroPlas
EuroPlas is proud to be one of the most reputable and trustworthy material suppliers worldwide. You can easily find and buy bio-filler, color masterbatch, plastic additives, engineering plastic compounds, and bioplastic compounds, etc., with just a click. Besides, please visit EuroPlas' blog today to update more useful materials information. We are a provider of optimal material solutions with a series of high quality plastic lines. Our solutions meet the diverse needs of the world's industries, not only in terms of high standards and reliability but also in terms of environmental obligations.