The ever-evolving plastics industry has introduced a myriad of material processing techniques, including injection molding, extrusion, blow molding, and thermoforming. Among these, plastic extrusion stands out as a frontrunner due to its cost-effectiveness and remarkable versatility, making it a preferred choice for numerous manufacturers. However, selecting the appropriate plastic for the extrusion process can be a daunting task without the necessary expertise. This comprehensive guide serves as your key to unlocking the details of the most common plastics employed in extrusion, along with their distinct advantages and applications. Empowered with this knowledge, you can confidently make the most informed decision for your specific manufacturing requirements.
1. What is Extrusion?
Emerging from centuries-old ingenuity, extrusion has ascended to the forefront of plastic processing techniques, revolutionizing the manufacturing landscape. This versatile method transforms thermoplastic resins into continuous, elongated products, offering a plethora of advantages that set it apart from conventional manufacturing approaches. At the heart of the extrusion process lies the heating and subsequent forcing of molten plastic through a shaped die, culminating in the formation of a continuous product. Not only does extrusion ensure product quality and precision, but it also enhances the inherent properties and performance of the plastic material.
1.1. Extrusion: A Symphony of Advantages
Extrusion stands as a testament to manufacturing prowess, orchestrating a harmonious blend of economic efficiency, diverse applicability, and the creation of high-quality products that enrich our lives. Its suitability for producing intricate plastic components, surpassing the dimensional limitations of other processing methods, has propelled extrusion to the forefront of various industries. Let's delve into the diverse realms where extrusion reigns supreme:
- Construction: Plastic pipes, shaped profiles, sheets,...
- Interior Design: Plastic doors, window frames, cabinets,...
- Automotive: Bumpers, wheel covers, wiring harnesses, and a myriad of components.
- Aerospace: Aircraft interior components, exemplifying precision and performance.
- Electronics: Computer casings, mobile phone housings, and the intricate world of electronics.
- Packaging: Bottles, food wraps, and the art of preserving products.
1.2. The Plastic Extrusion Process: A Step-by-Step Journey

Step 1. Pour resin (usually granules) into the funnel. The resin moves gradually from the hopper to the hopper neck and storage compartment.
Step 2. As the plastic pellets encounter the preheating zones, they embark on a thermal adventure, their temperature gradually rising until they transition into a molten state. This viscous, liquid plastic, now primed for transformation, enters the extruder barrel.
Step 3. To ensure uniform consistency and eliminate trapped air pockets that could compromise the final product, the molten plastic undergoes homogenization and degassing processes. Homogenizers meticulously blend the molten plastic, while degassing units purge any entrapped air, ensuring a flawless final product.
Step 4. The heart of the transformation lies in the die, a precisely shaped orifice that awaits the molten plastic. As the plastic encounters the die, it is forced through its intricate contours, emerging with the desired cross-sectional profile.
Step 5. Exiting the die, the freshly extruded product encounters cooling mechanisms, typically water baths or air jets. These cooling measures rapidly solidify the plastic, locking in the desired shape and form.
Step 6. The final stage involves cutting the continuous product to the specified lengths and applying any necessary finishing treatments. These treatments may include polishing, embossing, or printing, depending on the desired product characteristics.
2. Unveiling the Ideal Plastics for Extrusion
Extrusion, a marvel of modern manufacturing, has revolutionized the production of a vast array of plastic products. Selecting the appropriate resin for the extrusion process is paramount to ensuring the quality, performance, and cost-effectiveness of the final product. To guide you through this crucial decision, let's delve into the realm of the most common and suitable extrusion-grade plastics:
2.1. Polyethylene (PE)

Polyethylene (PE), derived from ethylene monomers, stands out as a versatile and widely used thermoplastic resin due to its exceptional properties: Lightweight and flexible, Excellent chemical resistance and affordability.
Applications of Polyethylene:
- Packaging: Bags, films, containers, and geomembranes
- Construction: Pipes, fittings, and insulation
- Consumer Products: Toys, housewares, and appliances
- Industrial Applications: Electrical insulation, wires, and cables
Subcategories of Polyethylene:
- Low-Density Polyethylene (LDPE)
- High-Density Polyethylene (HDPE)
- Linear Low-Density Polyethylene (LLDPE)
2.2. Polypropylene (PP)

Polypropylene (PP), derived from propylene monomers, has emerged as a workhorse in the plastics industry due to its remarkable balance of properties: High strength and rigidity, Excellent impact resistance, Good chemical resistance and High melting point.
Applications of Polypropylene:
- Automotive: Bumpers, interior components, and fibers
- Construction: Pipes, fittings, and roofing materials
- Textiles: Fibers for carpets, upholstery, and sportswear
- Housewares: Appliances, furniture, and containers
Subcategories of Polypropylene:
- Polypropylene Copolymer (PP Copo)
- Homopolypropylene (PP homo)
- Random Copolymer Polypropylene (PP Random)
2.3. Polystyrene (PS)

Polystyrene (PS), derived from styrene monomers, offers a combination of versatility and affordability, making it a popular choice.
Applications of Polystyrene:
- Packaging: Food containers, disposable cups, and packaging films
- Construction: Insulation materials, wall panels, and decorative trim
- Consumer Products: Toys, appliances, and electronics
- Office Supplies: Binders, pens, and rulers
Subcategories of Polystyrene:
- General Purpose Polystyrene (GP PS)
- High-Impact Polystyrene (HIPS)
- Crystal Polystyrene (CRYSTAL PS)
2.4. Polyvinyl Chloride (PVC)

Polyvinyl Chloride (PVC), derived from vinyl chloride monomers, offers a blend of cost-effectiveness, versatility, and fire retardancy, making it a popular choice for extrusion applications. However, PVC plastic possesses lower stability than PE and PP plastic, and can release toxic gasses when burned.
Applications of PVC:
- Construction: Pipes, fittings, and window profiles
- Wires and Cables: Electrical insulation and cable sheathing
- Flooring: Vinyl flooring and floor tiles
- Medical Devices: Tubing, catheters, and blood bags
Subcategories of PVC:
- Rigid PVC (uPVC)
- Flexible PVC (fPVC)
2.5. Acrylonitrile Butadiene Styrene (ABS)
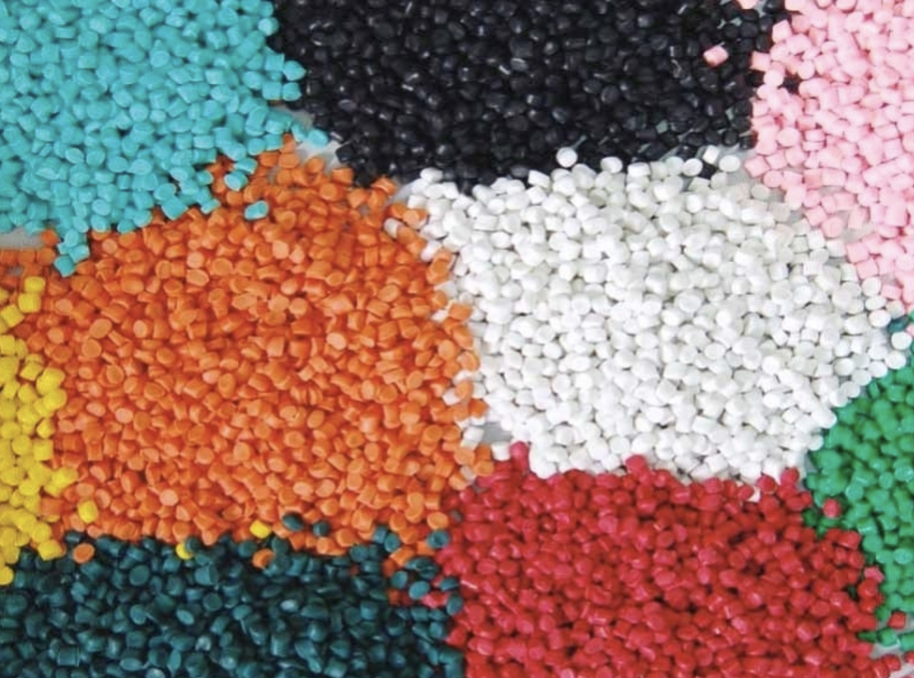
Acrylonitrile Butadiene Styrene (ABS) is a versatile plastic known for its sturdiness, good impact resistance, ease of processing, and reasonable price. However, ABS has lower chemical resistance compared to PE and PP plastics.
Applications of ABS:
- Automotive: Interior components, bumpers, and trim panels
- Appliances: Housings for electronics and home appliances
- Luggage: Suitcases and travel bags
- Toys and Games: Building blocks, toy parts, and game components
Subcategories of ABS:
- Impact-resistant ABS
- Fireproof ABS
- Standard ABS
Notes: The selection of the appropriate resin for extrusion hinges on a careful evaluation of several factors:
- Desired Product Properties
- End-Use Application
- Processing Parameters
- Cost Considerations
By meticulously assessing these factors, you can make an informed decision that optimizes the extrusion process and delivers high-quality products that meet your specific needs. Embrace the power of extrusion and transform your product vision into reality.
3. Conclusion
In the realm of extrusion, selecting the appropriate resin is paramount to achieving product excellence. The chosen resin directly influences the quality, performance, and cost-effectiveness of the final product. To make an informed decision, it is advisable to consult with experts in plastics and extrusion techniques.
4. About EuroPlas
EuroPlas stands as a leading provider of comprehensive solutions for the plastics industry, proudly affirming its position as the world's leading filler masterbatch supplier, providing customers with unique and optimal plastic material solutions. Our team of experienced professionals and diverse product portfolio are committed to delivering exceptional customer satisfaction. If you are seeking expert guidance on material selection for your extrusion project, EuroPlas is your trusted partner. Contact us today for a free consultation or leave your details through our online form to receive prompt assistance. Together, we can navigate the intricacies of resin selection and empower you to achieve extrusion excellence.