ABS vs PE are both thermoplastic materials extensively employed in numerous industrial sectors. When we compare ABS vs PE plastics, what are the differences between them, and which one is better for processing? Let's explore this with EuroPlas in this article.
1. An Overview of ABS vs PE
What is ABS?
ABS, which stands for Acrylonitrile Butadiene Styrene, is created by polymerizing three monomers: acrylonitrile, butadiene, and styrene. ABS is a thermoplastic material widely used in various applications. It possesses properties of rigidity, flexibility, heat and chemical resistance, ease of processing, and comes in a variety of colors.
What is PE?
Polyethylene (PE) plastic is a thermoplastic material produced from ethylene, a hydrocarbon with the chemical formula C2H4. PE is one of the most common plastics in the world, accounting for approximately 36% of total plastic production. PE comes in many types, each with different physical and chemical properties.
PE is produced by polymerizing ethylene at high pressure and temperature. The polymerization process creates long chains of ethylene molecules linked together. The length of these molecular chains and the arrangement of the ethylene molecules determine the physical properties of PE.
.jpg)
An Overview of ABS vs PE
2. Comparison of ABS vs PE Plastics
ABS vs PE plastics exhibit different physical and chemical properties, specifically as follows:
2.1. External Appearance
ABS typically has a smooth, glossy surface, whereas PE has a waxier or smoother appearance. ABS is often used in applications emphasizing aesthetics, such as consumer products or automotive parts, while Polyethylene is more commonly used in industrial applications.
2.2. Density
ABS is denser than PE. The density of ABS ranges from 1.03 to 1.06 g/cm³, while the density of PE ranges from 0.91 to 0.96 g/cm³. The difference in density is understood to make ABS generally sturdier and harder than PE.
2.3. Chemical Resistance
ABS can resist a variety of chemicals, including acids and bases, while PE is more resistant to water and other solvents. This difference makes ABS a preferred choice for applications requiring chemical resistance, such as automotive or aerospace components.
2.4. Melting Temperature
ABS has a higher melting temperature than PE. The melting temperature of ABS ranges from 221-243°C, whereas the melting temperature of PE ranges from 105-135°C. Therefore, ABS has a higher heat tolerance than polyethylene.
2.5. Manufacturing
ABS vs PE have different manufacturing requirements. ABS processing is quite common and can be done through injection molding or extrusion, while PE is typically extrusion molded. The differences in the manufacturing process are utilized in various applications.
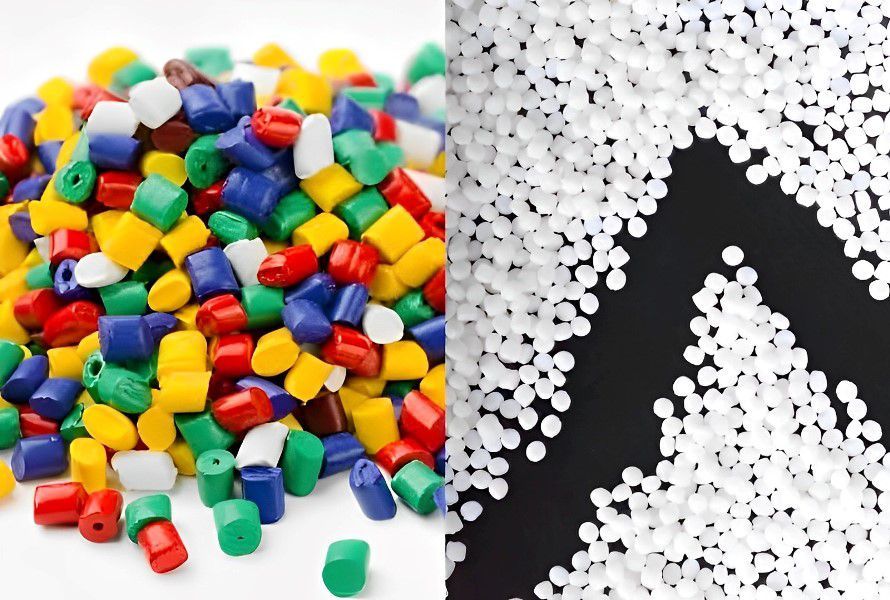
Comparison of ABS vs PE Plastics
2.6. Applications
ABS Plastic
- Automotive Parts: Interior decorative details, dashboard components, bumper overlays.
- Consumer Products: Toys, electronic devices, and sports equipment due to their aesthetic appeal, flexibility, and ease of processing.
- Pipes and Fittings: ABS pipes and fittings are used in water and drainage systems due to their chemical resistance, durability, and high-temperature tolerance.
- Safety Equipment: Helmets and safety gear due to their impact resistance and high durability.
- Musical Instruments: Clarinets and saxophones due to their high durability and excellent moisture resistance.
.jpg)
Applications of ABS Plastic
PE Plastic
- Packaging Materials: Bags, films, and plastic boxes due to their lightweight, durability, and flexibility.
- Pipes and Fittings: Water supply, gas distribution, and wastewater systems benefit from PE's chemical resistance, durability, and flexibility.
- Insulation: PE is used in electrical insulation due to its high dielectric strength and moisture resistance.
- Medical Equipment: Syringe tubing, tubing connectors, and conduits due to their compatibility, flexibility, and chemical resistance.
- Agriculture: Greenhouse films, coverings, and silage bags benefit from PE's moisture resistance and high durability.
.jpg)
Applications of PE Plastic
3. Comparing ABS vs PE Plastics: Which is Easier to Machine?
ABS (Acrylonitrile Butadiene Styrene) and Polyethylene (PE) are both machinable plastics, but the ease of machining depends on specific machining processes and application requirements. Here are some factors to consider when comparing the machinability of ABS and PE plastics:
- Machining Processes: Both ABS vs PE can be machined using various processes, including milling, drilling, turning, and routing. The specific machining process will depend on the type of part and application requirements.
- Cutting Speed: ABS is typically machined at higher cutting speeds compared to PE. This is because ABS is harder than PE and requires higher cutting speeds to maintain a good surface finish.
- Chip Formation: ABS tends to produce longer, stringy chips during machining, while polyethylene produces shorter, more pellet-like chips. The difference in chip formation can affect the efficiency and quality of the machining process.
- Wear Resistance: ABS has higher wear resistance than polyethylene, which can lead to faster tool wear during machining. ABS can be machined with carbide cutting tools, which have higher wear resistance than high-speed steel tools.
- Surface Finish: ABS generally has a smoother surface finish compared to polyethylene due to its higher hardness and lower coefficient of friction.
- ABS is often more challenging to machine due to its higher hardness and stiffness but can yield smoother surface finishes. Polyethylene is easier to machine but may not be suitable for applications demanding high strength or rigidity.
In conclusion, the choice between ABS vs PE for machining depends on the specific requirements of your application, the desired surface finish, and the machining equipment and tools available.
.jpg)
Comparing ABS vs PE Plastics: Which is Easier to Machine?
4. EuroPlas manufactures technical ABS and PE filler masterbatch plastics
4.1. Technical ABS compound and color masterbatch
Established in 2007 in Vietnam, EuroPlas has its headquarters in Hanoi. The company specializes in producing and supplying ABS plastic products, including:
- Engineering plastic compound ABS: EuroPlas provides various types of technical ABS compound plastics, catering to the diverse needs of customers. These products are manufactured to international standards, offering high quality and superior durability.
- Color masterbatch: EuroPlas offers a wide range of colorful ABS masterbatch products, with vibrant and eye-catching colors. These products help manufacturers create unique and impressive plastic products.
EuroPlas has a broad distribution network worldwide, serving customers in over 70 countries. The company is committed to delivering high-quality ABS plastic products with competitive prices and excellent customer service.
.jpg)
Technical ABS compound and color masterbatch
4.2. EuroPlas' PE Filler Masterbatch
EuroPlas produces filler masterbatch for various types of plastics, including PE (Polyethylene). EuroPlas' PE filler masterbatch is used to enhance the properties of PE plastic, including its strength, hardness, heat resistance, and chemical resistance. Additionally, EuroPlas' PE filler masterbatch can help reduce the production cost of PE plastics.
PE filler masterbatch is a type of filler material made from CaCO3 (calcium carbonate), PE base resin, and suitable additives. When added to plastic materials, PE filler masterbatch can provide the following benefits:
PE filler masterbatch is more cost-effective than virgin plastic resin, making it a cost-saving option for production.
- It enhances the hardness of the product, making it more impact-resistant and durable.
- It improves the product's stability, preventing deformation during use.
- It improves the product's printability, resulting in better color and image quality.
.jpg)
EuroPlas' PE Filler Masterbatch
EuroPlas' PE filler masterbatch offers a cost-effective solution for improving the properties and reducing the production costs of PE plastics.