Joining HDPE pipe correctly is crucial to ensure leak-free, long-lasting piping systems used in water, gas, and industrial applications. With its flexibility and durability, HDPE (High-Density Polyethylene) has become a top choice for modern infrastructure—but how exactly are these pipes connected? This article explores the most common HDPE pipe joining methods, their advantages, and how to choose the right technique for your project.
1. What is HDPE pipe?
HDPE pipe is a type of flexible plastic pipe made from thermoplastic HDPE (high-density polyethylene) that is created by the copolymerization of ethylene and small amounts of other hydrocarbons. This type of plastic pipe has strong molecular bonds and high molecular density that makes it resistant to harsh chemicals. Also, it does not leak or corrode and has many outstanding advantages in terms of durability and strength. Today, HDPE pipes are used globally to replace obsolete concrete or steel pipes in a few industries.
Related: Plastic pipe production process - the ultimate guide
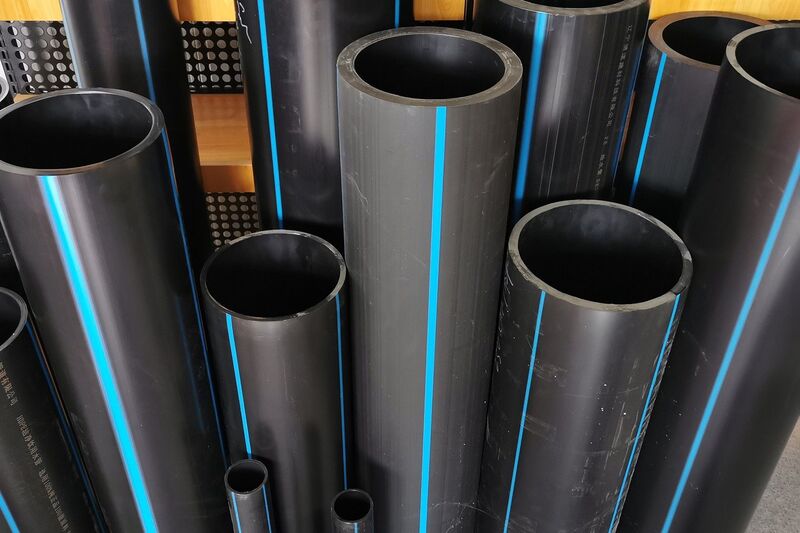
What is HDPE pipe?
2. HDPE pipe benefits
2.1. Corrosion resistance
HDPE pipes are mainly used in liquid and gas transportation because they are not corroded by the chemicals present in the liquid or gas they transport. So they don’t cause leakage or blockage problems.
2.2. High-pressure resistance
HDPE pipe is capable of withstanding high pressure without being deformed or damaged. Therefore, they can handle the unstable water pressure of domestic water systems and wastewater transportation systems.
2.3. Leak-free joints
Unlike traditional metal pipe systems, which are connected by mechanical joints. HDPE pipe systems can be joined using heat fusion methods. This method involves heating two HDPE pipe surfaces to a specific temperature, then the pipe cools, and it creates monolithic, permanent, and leak-free pipe joints.
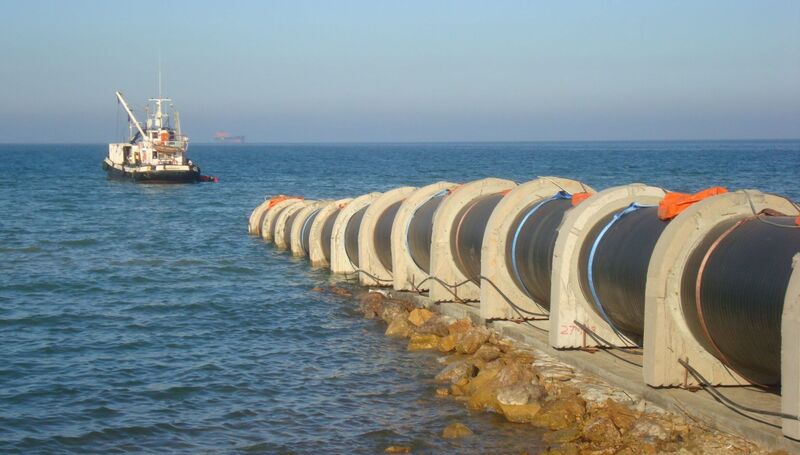
Application of HDPE pipe
2.4. Extended lifespan
The lifespan of HDPE pipes is longer than metal pipes (lasts only 20 to 50 years). It is estimated to range from 50 to 100 years depending on different applications.
2.5. Environment-friendly
HDPE pipes are recognized as having a minimal impact on the environment. The production of HDPE pipes takes less energy than non-plastic pipes anddoes not release dangerous toxins into the air during manufacturing.
2.6. Cost savings
The cost of manufacturing and processing plastic pipes is cheaper than the production of metal pipes. In addition, HDPE pipes are light in weight, so they save more on transportation and installation costs.
Because of the above benefits, HDPE pipe application is commercial and residential water supply, industrial liquids transportation, irrigation pipeline system, sewage systems, and supply of gas fuels.
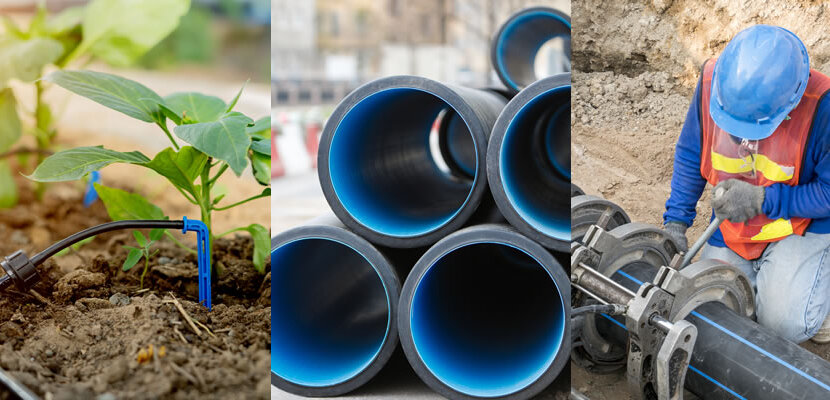
HDPE pipes are light in weight, so they save more on transportation and installation costs.
3. How is HDPE pipe most commonly joined
The principle of thermal fusion is to heat two HDPE pipe surfaces to a specified temperature, and then fuse them by applying a sufficient force. This force causes the molten pipes to mix together resulting in fusion. The joints after properly fusing are completely leak-free. The joint area is firmly equal to the pipe itself in both strength and pressure characteristics.
There are four common HDPE pipe connection methods including butt fusion, socket fusion, saddle fusion, and electrofusion.
3.1. Butt Fusion
This is the most common welding method currently used for joining HDPE pipes. The two ends of the HDPE pipes are heated by using a butt welding machine to heat them to a certain temperature. Then they are pushed forward under proper pressure to fuse together. This technique produces a permanent, and flow-efficient connection.
The six steps butt fusion method is:
- Clean, clamp and align the pipe ends
- Face the pipe ends to set up clean, parallel surfaces, perpendicular to the center line
- Align the pipe ends
- Heat the pipe interfaces
- Connect the two pipe ends together by applying the proper force
- Hold until the joint is cool
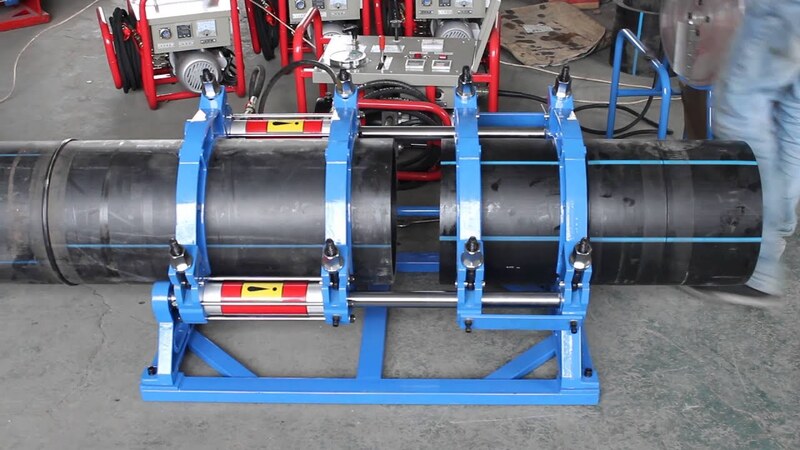
Butt fusion is the most common welding method currently used for joining HDPE pipes.
3.2. Socket Fusion
This technique consists of simultaneously heating both the external surface of the pipe end and the internal surface of the fitting until they reach a certain fusion temperature, inserting the pipe end into the socket, and holding it in place until the joint cools. This method usually refers to joining pipe to fitting instead of pipe to pipe.
These are the general steps of socket fusion:
-
Clean the pipe end and the inside face of the fitting
- Square and prepare the pipe end
- Heat the parts until an appropriate temperature
- Connect the pipe end and the fitting
- Let them cool
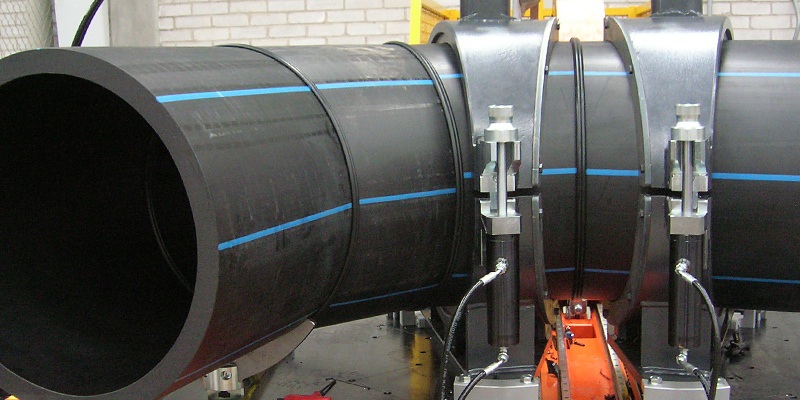
Socket fusion method
3.3. Saddle fusion
Saddle fusion is similar to socket fusion, but is used to join a perpendicular fitting to the surface of a pipe. This consists of simultaneously heating both the external surface of the pipe and the matching surface of the "saddle" type fitting until both surfaces reach the specific temperature. This may be implemented by using a saddle fusion machine that has been designed for this technique.
T
Here are six basic steps used to create a saddle fusion joint:
-
Clean the pipe surface where the saddle fitting is to be situated
-
Put the saddle fusion machine on the pipe
-
Arrange the surfaces of the pipe and fitting following the procedures
-
Heat both the pipe and the saddle fitting
-
Push down and hold two parts together
-
Cool the joint and unfix the fusion machine
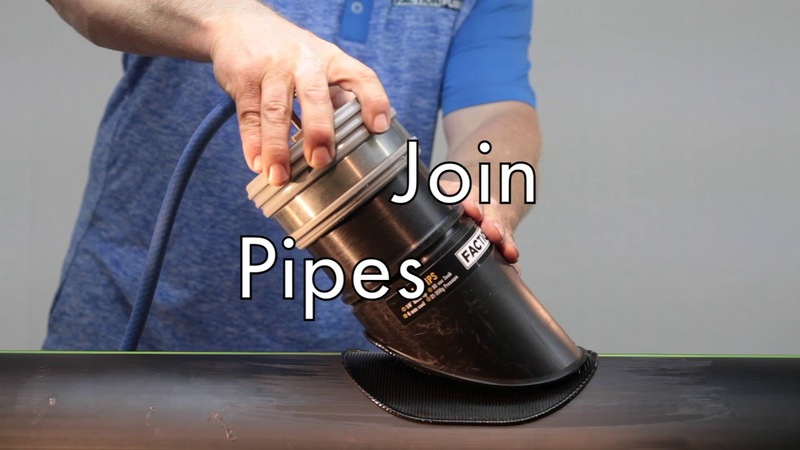
Saddle fusion method
3.4. Electrofusion
This technique of HDPE pipe jointing is quite different from the other fusion joining methods. The main difference is the way to heat the pipe or fitting surfaces. In normal heat fusion joining, a heating machine is used to heat the pipe and fitting surfaces. But the electrofusion joint is heated internally either by a conductor or by a conductive polymer. Heat is created when an electric current is passed through the conductive material in the fitting. Then the pipes are cooled and they will stick together.
Ordinary steps when implementing electrofusion joining are:
-
Prepare the pipes and electrofusion machine
- Mark the pipes
- Align and keep the pipe fixed
- Apply the electric current
- Cool parts and unfix the clamps
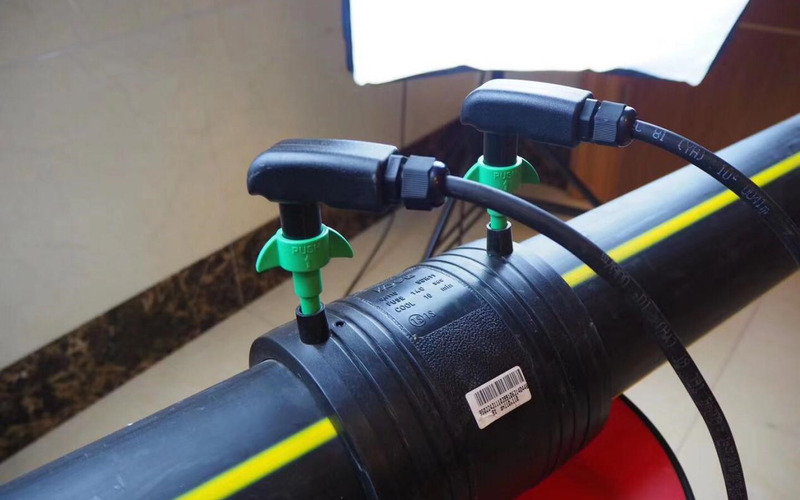
Electrofusion method
4. Conclusion
In summary, HDPE pipes are most commonly joined through methods such as butt fusion, electrofusion, saddle fusion, and socket fusion, each offering unique advantages depending on the specific requirements of the project.
Choosing the right joining method depends on factors such as pipe size, project scope, and environmental conditions. By selecting the appropriate technique, HDPE piping systems can ensure long-lasting durability, superior flow performance, and cost-efficiency for a wide range of applications.
5. About EuroPlas
With 7 factories located in 6 Vietnam's provinces and one in Egypt, EuroPlas has proven itself to be the world's leading manufacturer of filler and color masterbatch, plastic additives, engineering plastic compounds, bioplastics and biofillers. EuroPlas has affirmed its pioneering position in providing comprehensive solutions for the plastics industry. By constantly innovating and developing, EuroPlas focuses on meeting the increasingly diverse needs of the market.
EuroPlas is committed to providing customers with high-quality products and professional consulting services. For detailed advice, please contact EuroPlas via the form on the website. EuroPlas is committed to responding as soon as possible.