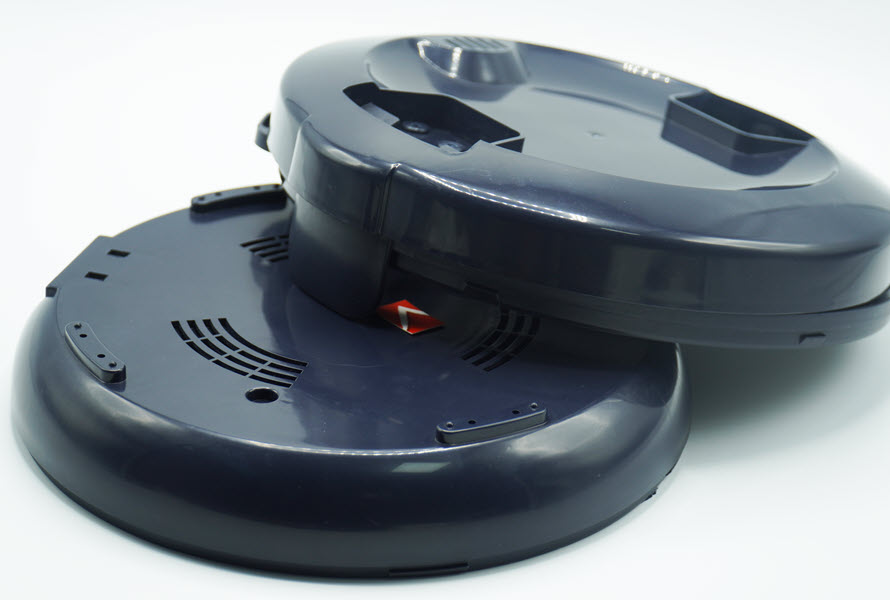
Injection molding is one of the most popular processing methods in the plastic industry. Despite being widely used, manufacturers are still very likely to have errors when injection molding. As a plastic raw material supplier with more than 15 years of experience, we will share with you some common defects of injection molded plastic products and offer the right solution in this article.
I. An overview of injection molding
Injection molding is a method of processing plastic products by injecting molten plastic into a mold. This is a widely used processing method in the production of finished plastics, especially thin-walled objects such as plastic shells. Basically, the plastic injection molding process will be as follows:
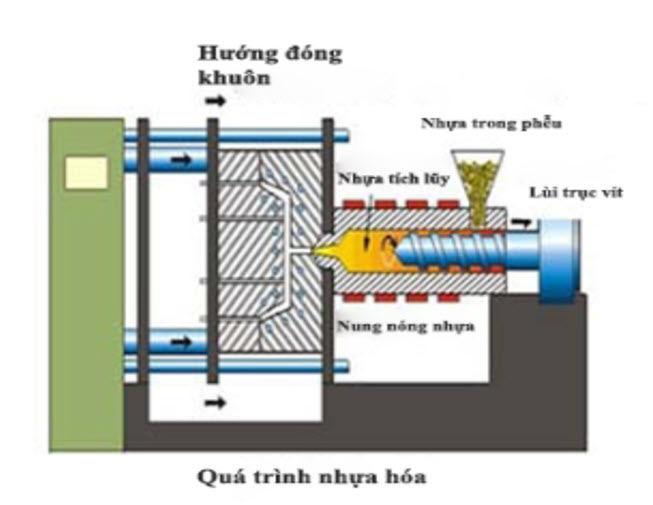
Step 1: Plastic materials (primary or recycled plastic particles) are fed into the machine through the feed hopper. From the feed hopper, the plastic granules are fed to a helical screw system (located along the cylinder). After that, the plastic particles are melted by a heating system arranged around the cylinder.
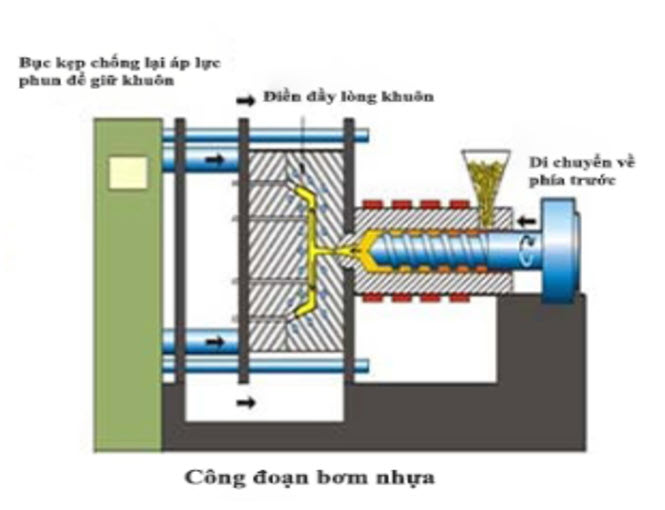
Step 2: The screw system will pressurize to inject molten plastic into the mold. This system acts as a plunger that pushes the molten plastic forward with great pressure.
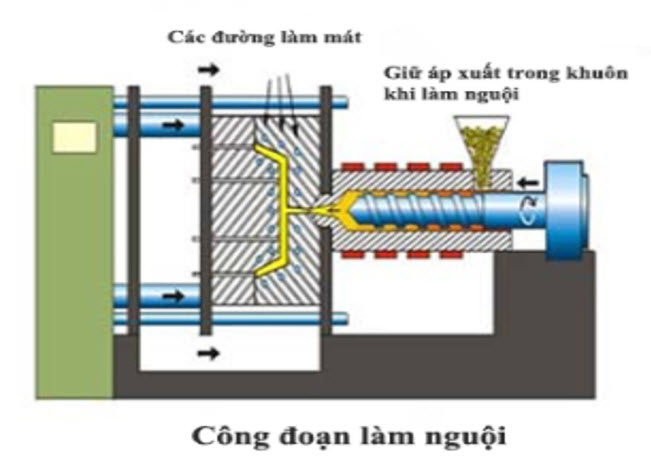
Step 3: The cooling system will work to cool the mold. The plastic in the mold at this time will cool down and turn to a solid state. When the plastic is completely solid, it can be taken out.
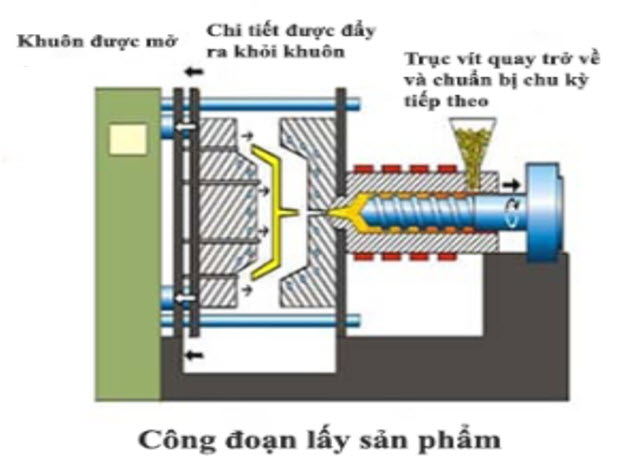
Step 4: The mold will be opened slowly to leave a certain amount of space, from which we can take the product out.
II. Injection molding troubleshooting
1. Warpage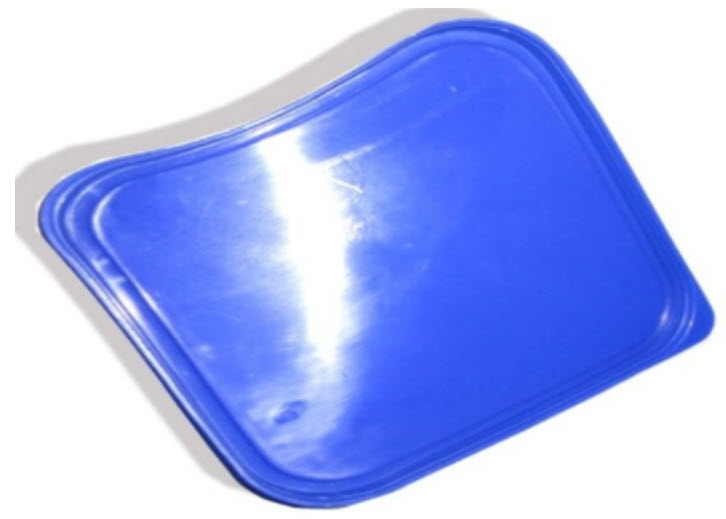
Cause
|
Solution
|
Due to shrinkage of plastic material (reinforced sugar-free plastic material ...)
|
Consider plastic materials, research and use appropriate materials
|
Pressure drop during pressing
|
Increase pressure
|
High cooling temperature
|
Increase cooling time or reduce mold temperature
|
2. Sink marks
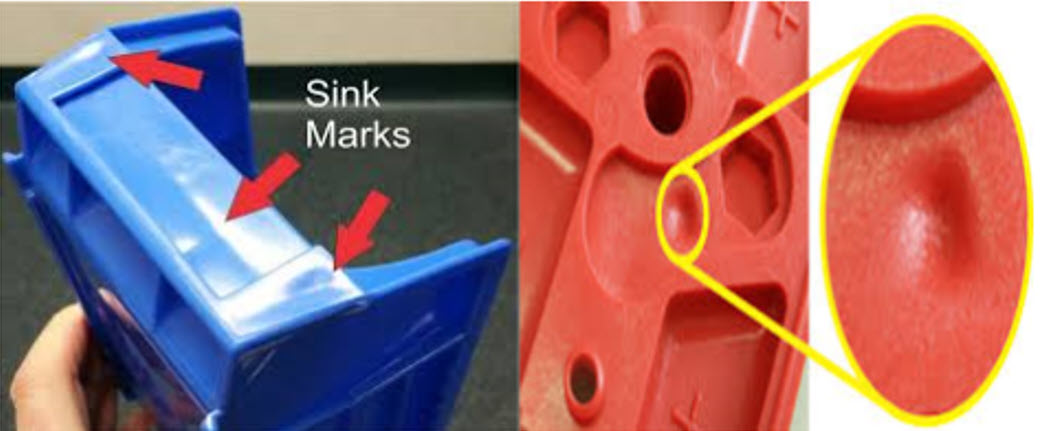
The cause of surface dents on the finished product is mainly due to the shrinkage of the plastic product and the inappropriate pressing mode. To avoid this error, you should:
- Keep low pressure, short time
- Small nozzle size
- Reduce mold temperature
- Reduce product thickness (design more ribs to increase force, arrange injection port near high thickness position (mold design)
3. Lacking plastic
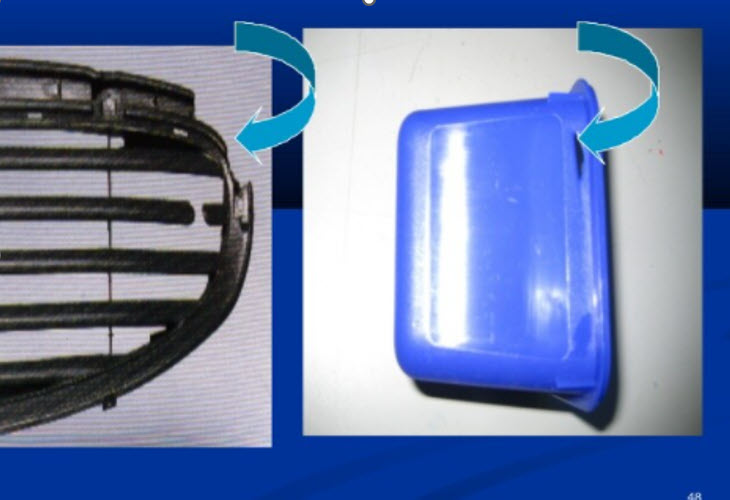
The cause of the finished product's lack of plastic can be due to the exhaust system on the mold, high resistance to the conveying system (the feed channels are too small), or the details of the finished product being too complicated. To avoid this error, you can check, clean the exhaust system, increase the injection pressure, and redesign the finished parts.
4. Weld line on the product
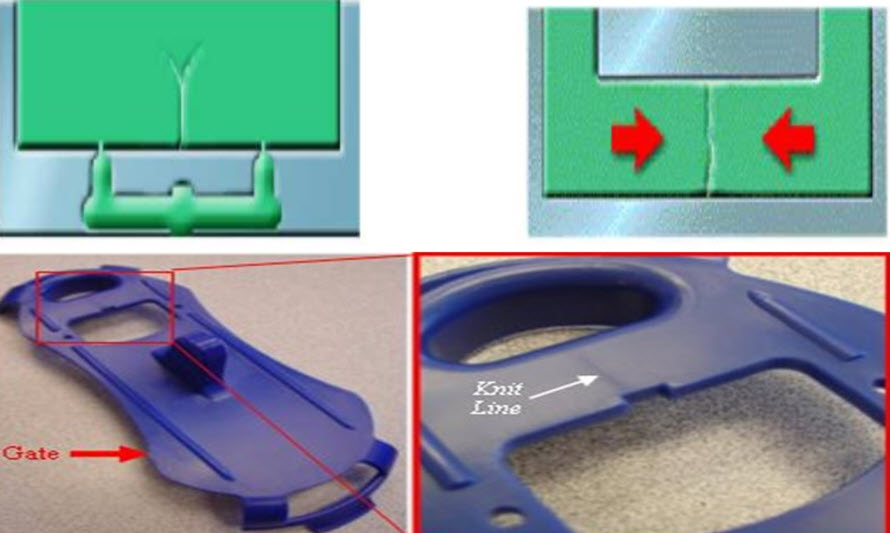
The weld on the product occurs when the resin flows from different directions merge but the solubility is not uniform. In this case, you should increase the injection pressure, injection speed and mold temperature.
5. White streaks on the product
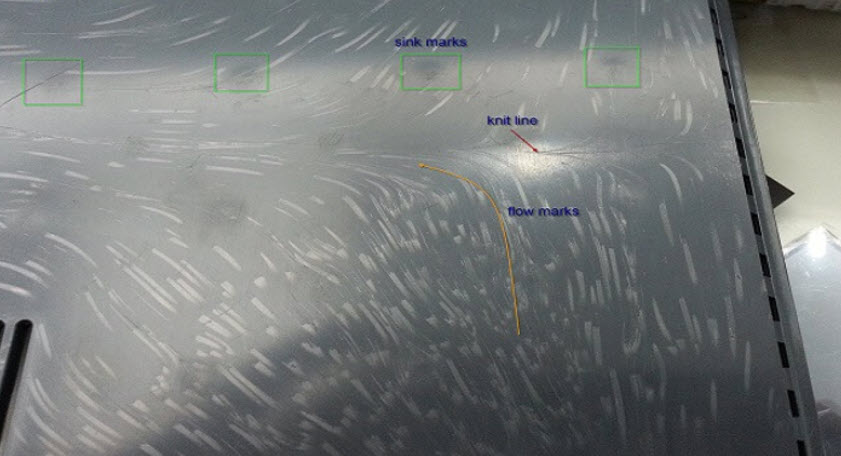
This phenomenon occurs because the air cannot escape or there is a decomposition component that produces air during the production process.
Cause
|
Solution
|
Ingredients contain water
|
Drying of raw materials (within the allowable humidity range)
|
Material temperature too high (melting decomposition)
|
Lower melting point
|
Materials containing other fillers (e.g. lubricants)
|
Reduce use or replace with other additives
|
Pigment decomposition (pigment has poor heat resistance)
|
Choose a powder that is resistant to high temperatures
|
Spray speed too fast (cutting decomposition or air blocking)
|
Reduce injection rate
|
Air is trapped in the barrel
|
|
Mixed materials or poor thermal stability
|
Substitute raw materials or use plastic with good stability
|
III. Common defects of taical in injection molding
Taical beads (also known as filler masterbatch) are additives used in the process of forming plastic products, with the main ingredient being CaCO3, primary resin, and some other additives. A few common errors in the use of taical beads in the plastic injection molding process are:
- Poorly dispersed taical particles (causing patchy, uneven colors)
- Damp taical seeds cause white streaks on the product
- Using taical beads of different colors makes the color of the finished products not uniform
Europe Plastics Joint Stock Company is currently the world's largest supplier of filler masterbatch with a capacity of 600,000 tons/year and has been present in over 85+ countries. Taical beads of European Plastics are the solution to optimize costs and improve product features for enterprises producing plastic-finished products. During 15 years of development, we are always confident in our commitment to the quality of our products and services.
For more information, please fill out the form or contact us directly via email/phone number.