Polypropylene vs polycarbonate, two exceptionally versatile and widely utilized materials, occupy the center stage in the realm of plastics. With their distinct characteristics, these substances prove themselves to be tailored for specific applications spanning diverse industries. This comprehensive article embarks on an in depth examination of the disparities between polypropylene vs polycarbonate, unraveling their unique properties, conducting a cost comparison, and analyzing their extensive range of applications. By shedding light on these crucial aspects, readers will be equipped with a profound understanding of the similarities and differences between these two materials, enabling them to make well informed decisions when faced with the task of material selection.
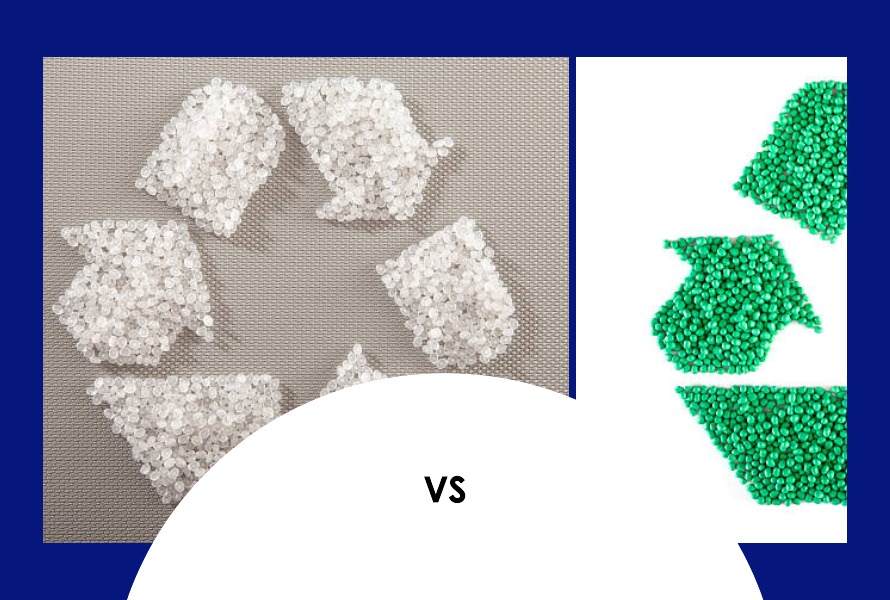
Polypropylene vs Polycarbonate
Table Of Contents
- What is Polypropylene?
- What is Polycarbonate?
- Polypropylene vs Polycarbonate: Comparison
- Conclusion
- Polypropylene & Polycarbonate Engineering Plastic Compound from EuroPlas
- FAQs
1. What is Polypropylene?
Polypropylene, also known as PP, is a thermoplastic polymer produced from propylene monomers. Esteemed for its remarkable amalgamation of properties, polypropylene emerged as a widely manufactured plastic. Demonstrating formidable strength, commendable chemical resistance, and excellent heat resistance, polypropylene proves suitable for an array of applications.
Within the automotive industry, polypropylene finds its purpose in crafting robust components such as bumpers, dashboards, and door panels, capitalizing on its exceptional strength and impact resistance. Furthermore, in the realm of packaging, this material exhibits its prowess in food containers, bottles, and caps, owing to its commendable chemical resistance and capacity to endure high sterilization temperatures.
.jpg)
Polypropylene
2. What is Polycarbonate?
Polycarbonate, commonly called PC, is a transparent thermoplastic renowned for its impact resistance and optical clarity. Formulated from carbonate groups and derived from bisphenol A (BPA), polycarbonate boasts unique properties that engender immense value in industries where transparency and durability reign supreme.
In safety, polycarbonate is pivotal in fabricating glasses and goggles, leveraging its exceptional impact resistance and optical clarity. Simultaneously, within the construction sector, it emerges as the material of choice for roofing panels and skylights, given its peerless durability and capacity to withstand the harshest weather conditions.
.jpg)
Polycarbonate
3. Polypropylene vs Polycarbonate: Comparison
A. Polypropylene vs Polycarbonate: Properties
Strength and Durability:
Polypropylene possesses commendable strength and durability, manifesting good resistance to impact and fatigue. This material retains its robustness even in low temperatures, rendering it ideal for outdoor applications. Conversely, polycarbonate has garnered a reputation for its extraordinary impact resistance and unwavering toughness. Its virtually unbreakable nature positions it as the goto choice for applications necessitating heightened durability.
Heat Resistance:
Polypropylene exhibits commendable heat resistance, boasting a melting point typically spanning from 130°C to 171°C (266°F to 340°F). However, polycarbonate surpasses this mark with superior heat resistance, showcasing a higher melting point ranging from 225°C to 250°C (437°F to 482°F). This quality renders polycarbonate suitable for high temperature applications.
Chemical Resistance:
Demonstrating excellent chemical resistance, polypropylene stands impervious to numerous acids, bases, and solvents. Consequently, it finds widespread employment in the chemical industry. Polycarbonate, too, offers commendable chemical resistance, albeit with susceptibility to specific chemicals like certain solvents and alkalis.
Transparency and Clarity:
While polypropylene naturally remains translucent, achieving transparency may necessitate additives or specialized processing. By contrast, polycarbonate embodies transparency, providing exceptional optical clarity and light transmission. This characteristic establishes polycarbonate as the material for applications mandating transparency, including optical lenses and safety glasses.
Flexibility and Impact Resistance:
Polypropylene flexes its versatility and impact resistance, effortlessly enduring bending and deformation without succumbing to breakage. Striking a balance between rigidity and flexibility, it fulfills diverse application requirements. As previously mentioned, polycarbonate shines in
impact resistance, deftly absorbing substantial impact energy without shattering. Consequently, it is worthy of applications demanding high levels of impact resistance, such as safety equipment and protective gear.
.jpeg)
Polypropylene vs Polycarbonate Properties
B. Polypropylene vs Polycarbonate: Cost
Comparison of the Cost:
Regarding cost, polypropylene generally prevails as the more economically viable choice over polycarbonate. While actual prices may vary depending on region, market demand, and material grades, polypropylene typically assumes a lower price point than its polycarbonate counterpart. This cost effectiveness renders it an attractive option for a myriad of applications.
Factors Influencing the Cost:
Multiple factors come into play when determining the cost of polypropylene vs polycarbonate. Raw material availability, manufacturing processes, and market demand influence pricing dynamics. Moreover, the desired properties and performance requirements of the end product can considerably impact the chosen material's cost.
.jpeg)
Polypropylene vs Polycarbonate Cost
C. Polypropylene vs Polycarbonate: Applications
Applications of Polypropylene:
Polypropylene boasts extensive employment across a range of industries and applications, including:
Packaging materials: Polypropylene is commonplace for manufacturing containers, bottles, and flexible packaging. Its commendable barrier properties and moisture resistance find resonance, particularly within the food and beverage industry.
Automotive components: Polypropylene's excellent chemical resistance, low weight, and impact strength secure its prevalence in automotive applications, spanning from bumpers and interior trim to battery cases.
Applications of Polycarbonate:
Polycarbonate garners unparalleled significance in applications necessitating transparency, impact resistance, and durability. Common domains of use encompass:
Electronic and electrical components: The electronics industry warmly embraces polycarbonate for manufacturing items like laptop casings, phone cases, and electrical connectors.
Safety equipment and optical applications: Polycarbonate's high impact resistance and optical clarity render it an invaluable resource in safety gear, including helmets, face shields, and goggles. Its adoption extends to optical applications such as eyeglass lenses and camera lenses.
Suitability for Specific Applications:
The selection between polypropylene vs polycarbonate hinges on the specific requirements inherent in the application. Polypropylene's affordability and chemical resistance often confer advantages, while polycarbonate's exceptional impact resistance and optical properties make it the material of choice. Understanding the application's precise demands is paramount in determining the appropriate material.
.jpeg)
Polypropylene vs Polycarbonate Applications
4. Conclusion:
In summary, polypropylene vs polycarbonate emerge as invaluable plastics with distinctive properties and applications. Polypropylene, lauded for its strength, heat, and chemical resistance, proves its mettle in packaging materials and automotive components. Conversely, polycarbonate outshines its counterparts with its unrivaled impact resistance, transparency, and optical clarity, solidifying its place in electronic components and safety equipment. When choosing between these two materials, meticulous consideration of properties, costs, and specific application requisites assumes the utmost significance.
When considering the selection of either polypropylene or polycarbonate for a particular application, it becomes paramount to undertake a meticulous evaluation of the specific requirements. This careful assessment ensures the identification of the material that best aligns with the job at hand. It is imperative to recognize that each material possesses its own distinct set of advantages and disadvantages, thereby necessitating a comprehensive understanding of these disparities in order to arrive at an informed decision. The ultimate determination, influenced by a multitude of factors such as cost, performance prerequisites, and the unique demands inherent in the application, will dictate the most suitable choice. By thoroughly considering these variables, one can ensure that the chosen material not only meets the desired criteria but also optimizes the overall outcome of the project.
5. Polypropylene & Polycarbonate Engineering Plastic Compound from EuroPlas:
EuroPlas, a reputable supplier and manufacturer of premium polypropylene vs polycarbonate engineering plastic compounds, leads the industry. Equipped with profound expertise and an unwavering commitment to excellence, EuroPlas provides tailored solutions to meet specific requirements across various sectors.
Our polypropylene engineering compounds epitomize outstanding performance and reliability. By harnessing advanced technologies, these compounds enhance the inherent properties of polypropylene, boosting strength, impact resistance, chemical resistance, and heat resistance. Applications in the automotive, packaging, electrical, and consumer goods industries benefit from EuroPlas' polypropylene compounds.
Similarly, EuroPlas offers a range of renowned high-quality polycarbonate engineering compounds known for their superior mechanical strength, impact resistance, transparency, and heat resistance. These polycarbonate compounds represent excellence in meeting the stringent demands of the electronics, automotive, aerospace, and optical sectors.
Our typical compound engineering plastic products are: PC flame retardant compound, PC glass fiber compound, PP flame retardant compound,...
EuroPlas differentiating factor lies in its unwavering dedication to innovation and customization. EuroPlas deeply understands their specific needs by forging close partnerships with clients, thereby developing bespoke solutions. Our engineering plastic compounds manifest consistent quality, reliability, and adherence to industry standards.
Choosing EuroPlas as your supplier or manufacturer of polypropylene vs polycarbonate compounds opens doors to advanced technology and a commitment to customer satisfaction. EuroPlas strives to deliver high-performance materials designed to tackle the unique challenges posed by your applications.
Whether polypropylene compounds tailored for packaging solutions or polycarbonate compounds primed for demanding electronic components, EuroPlas emerges as a trusted partner, providing superior products to propel your success. Please contact us for more details about compound engineering plastic products.
.jpeg)
Polypropylene & Polycarbonate Engineering Plastic Compound from EuroPlas
6. FAQs:
Q: Is polypropylene recyclable?
A: Yes, polypropylene stands as a recyclable material. Its recycling endeavors commonly yield new plastic products, including containers, automotive parts, and fibers. Nonetheless, local recycling facilities and regulations may dictate the recycling process and availability.
Q: Can polycarbonate withstand high temperatures?
A: Polycarbonate exhibits remarkable heat resistance, enabling it to endure high temperatures. With a higher melting point than polypropylene, polycarbonate finds its place in applications necessitating temperature resilience.
Q: Is polycarbonate more expensive than polypropylene?
A: Generally speaking, polycarbonate commands a higher price tag than polypropylene. Raw material availability, manufacturing processes, and market demand influence the cost differential. Nonetheless, specific prices may vary depending on the region and material grade.
Q: Can polycarbonate be used for outdoor applications?
A: Polycarbonate proves its mettle in outdoor applications thanks to its impressive durability and resistance to UV radiation. Prolonged exposure to sunlight does little to degrade or discolor polycarbonate, rendering it a suitable choice for outdoor deployments.
Q: Is polycarbonate suitable for food contact applications?
A: Indeed, polycarbonate occupies a prominent position in food contact applications. It meets regulatory requirements and boasts approval for use in various food related products such as water bottles, food containers, and kitchen utensils. Ensuring compliance with food grade standards is crucial when selecting the specific polycarbonate.