1. Black masterbatch – the basic component in manufacturing black plastic objects
Black masterbatch is one of the most basic color masterbatches that EuP had proudly launched to the market. In daily life, black objects are widely used since it is easy to combine the black color with other colors. Moreover, black features seem to look cleaner than others. To create black color for plastic products following customers’ requirements, manufacturers use black masterbatch. Let's find out about the production process and application of this product in daily life and industries!
1.1. Black masterbatch manufacturing process
The basis of producing a color masterbatch is mixing the primary resin with other substances, for example, fillers, pigments, and additives. Similarly, to produce a black masterbatch, the manufacturer first mix black carbon powder, base resin, and other additives according to the well-investigated formula, then mix by a mixer at high speed for about 10 minutes. The mixture after being mixed will be passed through the extruder to pour into a sheet, then be cooled, and then passed through a cutter to cut into masterbatch particles. The finished master batch is then mixed with primary plastic granules and other additives into a mixture of plastic materials. This mixture will undergo different processing technologies depending on the product shape that customers require (injection molding, extrusion, blowing film ...).
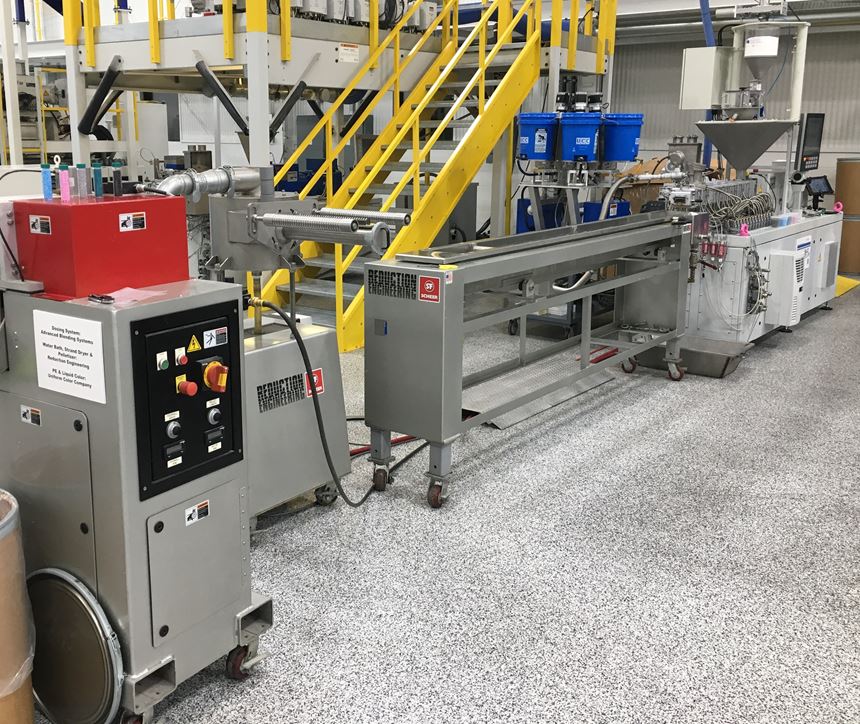
The black masterbatch category under the brand Europlas does not include only one type of product. In response to the different requirements, we studied and developed five different types of black master batches based on black carbon proportions ranging from 20 to 50%. There are 2 types of black carbon used for coloring the plastic, which is P (powder) and HAF (high abrasion furnace) pigment. Here are 5 black masterbatches produced by EuP:
- EMPE 0020 includes 20% of HAF black carbon
- EMPE 0030 includes 30% of HAF black carbon
- EMPE 0040 consists of 40% of HAF black carbon
- EMPE 0050 consists of 50% of HAF black carbon
- EMPE 0030P includes 30% of P carbon powder
1.2. Is using black masterbatch to color plastics an advanced method?
In addition to color masterbatch, usually manufacturers also apply different ways to color the plastic. For instance, manufacturers can apply the method called color coating on the surface of the products by printing, spraying, and plating colors onto the outer surfaces of the products. These traditional ways will help the producers save production costs. However, there was one on the outside of products coated with colors so after a period of time, the color will be faded. In contrast, the method of adding the black masterbatch directly into the plastic mixture and then heating until they are molten will help the color spread more evenly in the mixture. After the plastic is cooled and solidified, the color will remain even when left outdoors for a long time.
Depending on the type of product required and the ratio of other ingredients, the concentration of color pigments used for the overall mixture is between 0.5% and 3%. This coloring technique is more labor intensive and the production cost can be higher but it will give the product a beautiful color and long-lasting appearance.
1.2. Notes when using black masterbatch to produce plastic products
Black masterbatch has the advantage of being compatible with plastic because it is made from the corresponding plastic substrate, so the color provided by the grain can be maintained for a long time without being faded. The black carbon powder is not only used to create color for the product but also has the responsibility to shield light, especially UV radiation and antioxidant products. However, if the product content exceeds the ideal ratio, it will negatively affect the production process or the quality of the finished product. For example, when color masterbatch is added with too large an amount, the viscosity within the mixture increases, making the casting process difficult, and reducing the mechanical features of the product. The more additives you use, the less will even reduce the transparency of plastic.
One more thing that needs to be noted when producing black masterbatch is the toxicity of black carbon, which common name is soot. This is considered a substance that can cause lung cancer. Workers are the ones with the highest incidence since they are often in contact with soot at work by breathing in and contacting the skin or eyes. Therefore, at the factories and mines, strict guidelines are needed to ensure that employees do not have the risk of inhaling unsafe carbon in the raw form.
3. Application of Europlas brand black masterbatch in diverse fields
Masterbatch is one of EuP's main supply products. EuP specializes in producing black masterbatch, white masterbatch, and other color masterbatches according to customer requirements. In general, black masterbatch is widely used in household plastic products and in other industries. In the past, it can be seen that electronic devices, monitors, or white computer keyboards were very popular in the 90s, but now they are gradually changed to black to serve the user's tastes. Automobile equipment accessories, extruded plastic pipes, agricultural films, and technical materials are also produced with black.
Black masterbatch produced by EuP is strictly compliant with European and international safety standards, so products will ensure the highest quality. The use of special pigments according to customer requirements and additives with special characteristics, Europlas
color masterbatch will ensure that the final product shows less plastic with other products market.