HIPS (High Impact Polystyrene) is a thermoplastic polymer material that has become a popular choice for many industries due to its low cost, versatility, and ease of processing. This material is made from monomer styrene and a rubber-like substance called butadiene, making it a copolymer of polystyrene and polybutadiene. Although HIPS plastic has many advantages, there are also some disadvantages that should be considered before choosing this material for a specific application.
In this blog, we will explore the advantages and disadvantages of HIPS plastic, and some of the best-in-class HIPS compounds available on the market. Whether you are a manufacturer looking to optimize production processes or a product designer seeking to improve product performance, this blog will provide valuable insights into this material. Let’s get started!
Related:
- ABS engineering plastic - definition and applications
- PC - PBT plastic: definition, properties, applications, and more
- Polyvinyl chloride vs polycarbonate: which one is better?
- The significance of polyolefins - PP, PE
1. HIPS plastic - what is it?
1.1. Definition:
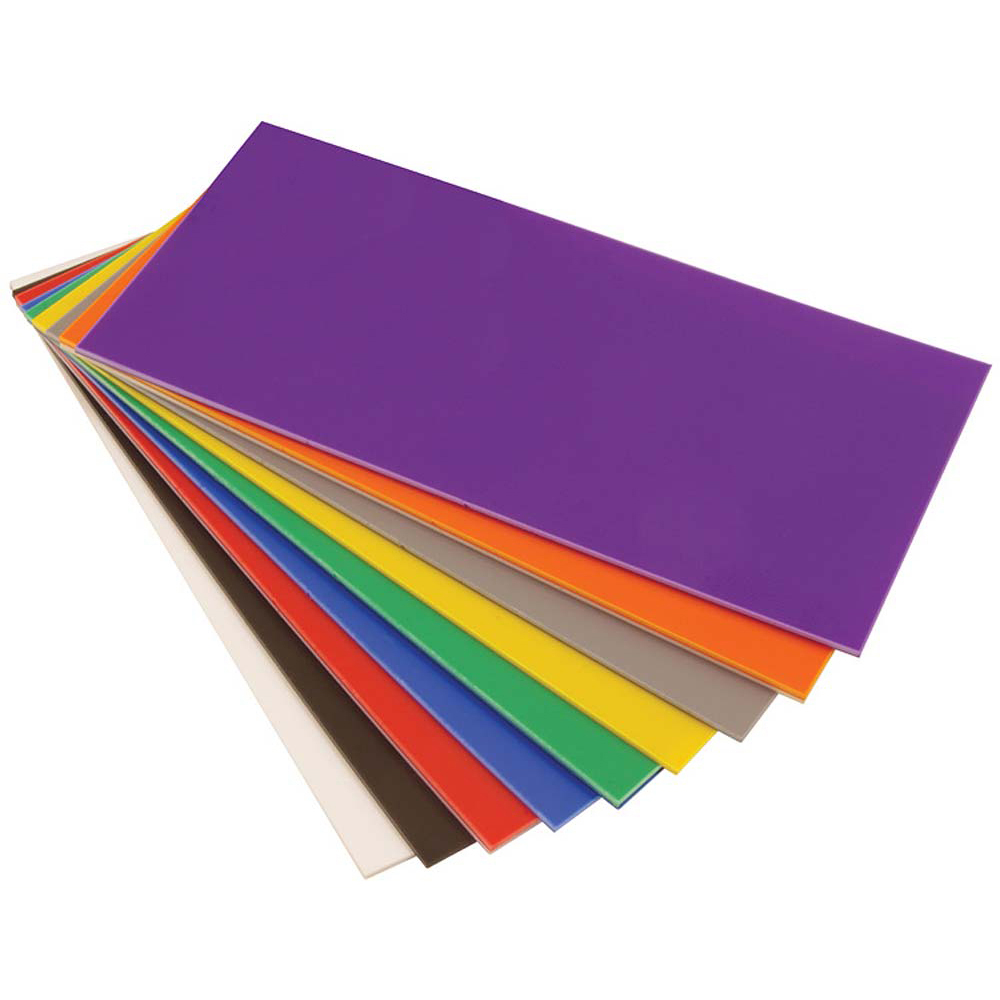
HIPS, or High Impact Polystyrene, is a versatile and cost-effective plastic material that is widely used in a variety of applications due to its unique properties. The material is made from a combination of two monomers, polystyrene, and polybutadiene. The characteristics of HIPS are lightweight, impact resistance, and ease of processing, making it an ideal choice for many applications.
HIPS is a popular and cost-effective plastic material that provides a wide range of benefits for its users. We’ll explore its applications right below.
1.2. Applications:
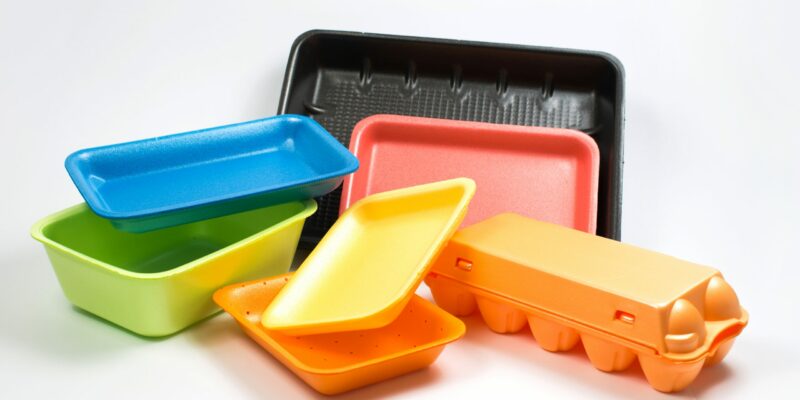
Thanks to its amazing properties, HIPS plastic is widely used in a variety of applications: Here are some common applications:
Product packaging: Due to its low weight, resistance to moisture, and simplicity in molding into various forms and sizes, HIPS is frequently utilized in packaging applications. The packaging of consumer items including toys, electronics, and cosmetics frequently uses this method.
Signs and displays: HIPS is a popular choice for signs and displays due to its good dimensional stability, which allows it to hold its shape even when exposed to changing temperatures and humidity levels.
Automotive interior parts: Because of its strong impact resistance and manufacturing ease, HIPS is employed in the fabrication of several automotive interior parts, including instrument panel components.
Toys: HIPS is used in the manufacture of toys and other children's products due to its lightweight, impact resistance, and ability to be easily molded into different shapes and colors.
Electrical and electronic equipment: HIPS is frequently used as a casing for electrical and electronic equipment because of its exceptional dimensional stability and resistance to moisture.
Medical devices: Due to its high impact resistance, low weight, and simplicity of processing, HIPS is utilized in the manufacture of a variety of medical equipment, including orthopedic splints.
Food packaging: Because HIPS is easily moldable into a variety of forms and sizes and has strong moisture resistance, it is used to make food packaging such as clamshell containers.
2. Advantages and disadvantages of HIPS plastic
While HIPS has several advantages over other materials, it also has some disadvantages that limit its use in certain applications. This section will provide an overview of the key advantages and disadvantages of HIPS plastic.
2.1. Advantages of HIPS plastic
HIPS is a relatively lightweight material, making it easy to handle and transport, and reducing the overall weight of HIPS products.
The presence of polybutadiene in HIPS gives it good impact resistance, making it suitable for use in products that may experience rough handling or bumps during transportation.
HIPS has good dimensional stability, meaning that it retains its shape and size even under changing temperature conditions, making it ideal for use in packaging applications.
HIPS is resistant to moisture, making it a good choice for packaging food products and other goods that are sensitive to moisture.
HIPS is easily molded into different shapes and sizes using techniques such as injection molding or blow molding. It can also be colored, printed on, and decorated, making it a versatile and cost-effective material for mass production.
HIPS can be easily joined to other materials using adhesives or by welding, making it ideal for use in applications where it needs to be attached to other components.
HIPS is recyclable and biodegradable. Therefore it’s an environmentally friendly material that reduces waste and environmental impact.
HIPS is a relatively inexpensive material compared to other plastic materials, making it a cost-effective choice for many applications.
2.2. Disadvantages of HIPS plastic
HIPS is vulnerable to degradation by many chemicals, including solvents, acids, and alkalis, which can cause it to become brittle, discolor, or break down over time.
HIPS has a low-temperature resistance and can become brittle at low temperatures. So it’s unsuitable for applications that are exposed to extreme temperatures.
HIPS has limited resistance to UV light and can become yellow and brittle over time when exposed to UV light, reducing its overall lifespan.
HIPS has poor flame resistance and will ignite and burn easily, making it unsuitable for use in applications where fire safety is a concern.
HIPS has poor tensile strength and is not as strong as other plastic materials.
HIPS is not biocompatible and should not be used in medical applications where it may come into direct contact with human tissue.
HIPS should not be used in applications where it will come into direct contact with food, as it may release harmful chemicals that can contaminate the food.
HIPS is not ideal for outdoor use, as it is vulnerable to degradation by UV light, moisture, and extreme temperatures, which can reduce its overall lifespan.
3. Common HIPS plastic compounds
Components: HIPS conductive compounds are made by blending HIPS resin with carbon black, which is a highly conductive material. The combination of these two materials results in a plastic compound that has excellent electrical conductivity.
Features:
- Provide all the functions of a single material. This eliminates the need for additional materials, such as conductive coatings or conductive inks, which can reduce production costs and increase production efficiency.
- HIPS conductive compounds can be tailor-made to meet the specific requirements of end-products,
- Improve product’s mechanical properties, color stability, and dimensional stability.
Applications: The applications of HIPS conductive compounds are diverse, ranging from mobile chargers, power sockets, and earphones, to electronic components and pallets, which require good electrical conductivity and improved mechanical properties.
Components: HIPS flame retardant compounds are a special type of plastic material that are designed to prevent the spread of fire on plastic surfaces. These compounds are made by blending HIPS resin with flame-retardant materials, which are added to meet the specific flame-retardant requirements of the end product. Depending on the requirements, HIPS flame retardant compounds can be manufactured with different levels of UL94-standard flame retardants, including V0, V1, and V2.
Features:
- Provide all the functions of a single material. This eliminates the need for additional materials, such as flame retardant coatings or sprays, which can reduce production costs and increase production efficiency.
- Can be tailor-made to meet the specific requirements of end-products
- Improve product’s mechanical properties, color stability, and dimensional stability.
Applications: The applications of HIPS flame retardant compounds are diverse, ranging from mobile chargers, power sockets, and earphones, to electronic components, pallets, and keyboards. The use of HIPS flame retardant compounds in these products helps to prevent fire spread on plastic surfaces, minimizing the damage caused by fire. This makes HIPS flame retardant compounds an ideal material for use in products that need to meet fire safety regulations.
4. EuroPlas - a reliable HIPS plastic supplier
EuroPlas is the world’s leading masterbatch manufacturer, specializing in the production of high-quality plastic compounds, including HIPS compounds. Our extensive experience and expertise in the field of plastic help customers produce products that meet the specific requirements of various industries.
At EuroPlas, the manufacturing process is based on cutting-edge technology and strict quality control measures. Our state-of-the-art facilities and experienced technical team ensure product consistency in quality, performance, and color. Additionally, EuroPlas offers a range of support services, including product development, testing, and technical support, to ensure that customers receive the best products and service possible
Whether you are looking for standard or customized HIPS compounds, EuroPlas is a trusted supplier that can meet your needs. Contact us directly to discuss your specific needs and requirements.