PEEK polymer or Polyetheretherketone is a thermoplastic polymer with outstanding performance that has transformed the world of materials studies. It's widely used in numerous sectors, including automotive, oil and gas, aerospace, and medical.
PEEK, together with Polyether ketone (PEK), Polyether ether ketone ketone (PEEKK), and other compounds, belongs to the poly aryl ether ketone family. This semi-crystalline thermoplastic is the most well-known member thanks to its excellent strength and remarkable resistance to high temperatures, chemicals, wear and tear.
Let's explore this article to see what PEEK is used for in the electronics industry! Follow along!
Read more: PEEK plastic: Definition and Application
1. Applications of PEEK Polymer in Electronics Industry
PEEK insulated wires
Here are the most highlighted applications of PEEK polymer in the electronics industry:
- Electrical Insulation: PEEK has a low dielectric constant and strong dielectric strength, making it a great electrical insulator. It is utilized in electronic components, including connectors, circuit boards, and insulating coatings where protection from high voltages is essential.
- Cable Insulation: PEEK is utilized in cables and wires where high-performance insulation is needed since it offers exceptional mechanical qualities, chemical resistance, and flame retardancy. It guarantees durability and performance in crucial applications.
- Connector Components: The material is popular in constructing electrical connection housings. Thanks to its great strength, stiffness, and wear resistance, it can be used as a connection in difficult situations with frequent temperature changes and mechanical stress.
- Semiconductor Processing Equipment: PEEK is resistant to the harsh chemicals and high temperatures required for wafer cleaning, etching, and depositing. Therefore, many manufacturers consider it a reliable material for semiconductor processing equipment.
- Printed Circuit Boards (PCBs): Applications requiring the strong ability to withstand high-frequency and high temperatures, such as printed circuit boards (PCBs), can find PEEK useful as a substrate material. Its dimensional and thermal stability across various circumstances supports electronic components in harsh conditions.
- Sensor Housings: PEEK polymer is a good material for housing sensors and transducers in numerous electronic devices. It guarantees the long-term protection and functionality of the sensor's constituent parts due to its great dimensional stability and ability to resist moisture absorption.
- Coatings & Encapsulation: PEEK can be used to encapsulate delicate electronics or as a protective coating for electrical components. It prolongs the life and efficiency of electronic devices by offering thermal and chemical protection.
- Antenna Components: PEEK is utilized for antenna components in telecommunications and other wireless applications thanks to its resilience to environmental deterioration and ability to preserve electrical characteristics at high frequencies.
2. Why is PEEK Polymer Ideal for the Electronics Industry?
PEEK sheet and rod
PEEK polymer is an excellent choice for many electronics applications. It's because it boasts various outstanding features, including:
PEEK can withstand a constant usage temperature of 260°C (500°F), making it ideal to use for electronic applications. It's also suitable for thermally demanding settings such as the oil and gas industry, process industries, and car engines and transmission applications. Besides, the materials can tolerate wear and friction in dynamic applications such as thrust washers and seal rings.
PEEK polymer is a semi-crystalline carbon fiber with remarkable stiffness and strength at various temperatures. Its specific strength is higher than that of alloys and metals.
PEEK is more resilient than other polymers and some metals over an extended period of time due to its semi-crystalline structure, which offers exceptional creep and fatigue resistance. (Fatigue refers to a material's brittle failure under repeated cyclic loading, and creep refers to a material's persistent deformation under continual tension)
PEEK polymer is difficult to ignite or burn. Its excellent flammability performance allows it to resist combustion up to 600°C and emit little smoke when burned at high temperatures. That's why it's not only widely used in the electronics industry but also in commercial aircraft.
Though its characteristics change slightly, the PEEK molecule's stability allows for frequent re-melting and reprocessing. Thus, it minimizes the environmental impact and encourages the profitable reuse of production waste material.
3. Conclusion
PEEK polymer offers many excellent properties, such as mechanical strength and resistance to heat and chemicals. Thus, it's a trustworthy semi-crystalline thermoplastic material in many electronics applications that requires durability and reliable performance.
4. EuroPlas - Where you can find the best plastic materials
EuroPlas is known as a leader in the masterbatch field since the company satisfies a wide range of requirements for unique plastic raw material solutions to optimize production costs and improve the competitiveness of the customers.
Here is the list of outstanding products from EuroPlas:
Filler masterbatch
With more than 15 years of producing and exporting filler masterbatch to thousands of businesses around the world, EuroPlas is proud to offer a wide range of filler masterbatch to help manufacturers save cost, enhance productivity and produce high-quality plastic products.
EuroPlas filler masterbatch combines calcium carbonate CaCO3, primary resin, and other plastic additives based on the customers' requirements. The products have many advantages, such as reduced shrinkage, improved stiffness, and bend strength, the capability to enhance stability, printability, and surface quality of the final products, and energy savings. It's ideal for injection molding, blow molding, PVC pipe manufacturing, packaging, plastic frames, door production, etc.
Color masterbatch
Color masterbatch from EuroPlas is a solution for end-product aesthetics. It's made from high-quality pigments, carrier resin, and some special additives, creating a colorful and attractive appearance. EuroPlas provides a wide range of colors and effects, from simple to complicated, of color masterbatch.
Besides the help to meet color requirements, the material saves time and cost as manufacturers can use it directly in the production process. Plus, it causes no harm to the environment.
Plastic additives
Plastic additives are a necessary substance used in the production process to improve the material's performance. Besides, they help the plastic become more durable, thanks to the enhanced chemical and physical resistance.
EuroPlas has a wide range of additives for plastic, such as Flame retardants, Desiccants, Odor removing additives, Anti-UV additives, Anti-aging additives, Anti-fog additives, Antistatic additives, Anti-blocking additives, and Processing-aid additives.
Engineering plastic compound
EuroPlas engineering plastic compound is full-function-in-one-material to save time and production costs. The combination is made of resin, additives, and reinforcements (based on the end-product requirements).
All EuroPlas products are various, including PA6, PA66 blend compound, PBT GF-FR compound, ABS Glass fiber compound, ABS Antistatic compound, PC flame retardant compound, and ABS. All are of high quality and flexibility. If you're looking for a material for automobile, electronics manufacturing, interior decoration, and renewable energy, you should not miss these products from EuroPlas.
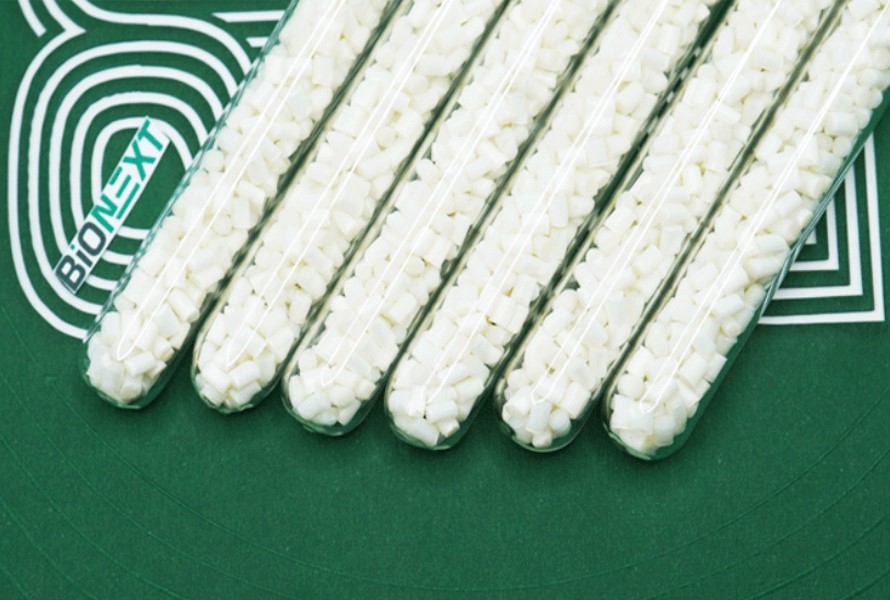
Bioplastic compound
As a professional, EuroPlas understands the industry's ongoing trend and demand for green, biodegradable plastic. And the company is also concerned about sustainable development and the environment; thus, a list of high-quality EuroPlas bioplastic compounds is produced to be used in various aspects, including automotive & transport, construction, fibers, electronics, household appliances, and especially food packaging.
BioNEXT, a bio compound exclusively developed by EuroPlas, can be decomposable within 12 months after use. The company guarantees that the end product passes strict quality control management to meet all the requirements.
Contact EuroPlas right now for the best price of all products!