Currently, PEEK plastic is widely used in many fields. Besides thermoplastic and thermosetting plastic, this is also one of the quality industrial plastic lines. Nevertheless, many individuals need more comprehension regarding intricate aspects of polyetheretherketone (PEEK) plastic in daily life and manufacturing processes. EuroPlas offers a comprehensive range of exceptional characteristics within its plastic line. Let us engage in a collaborative consultation.
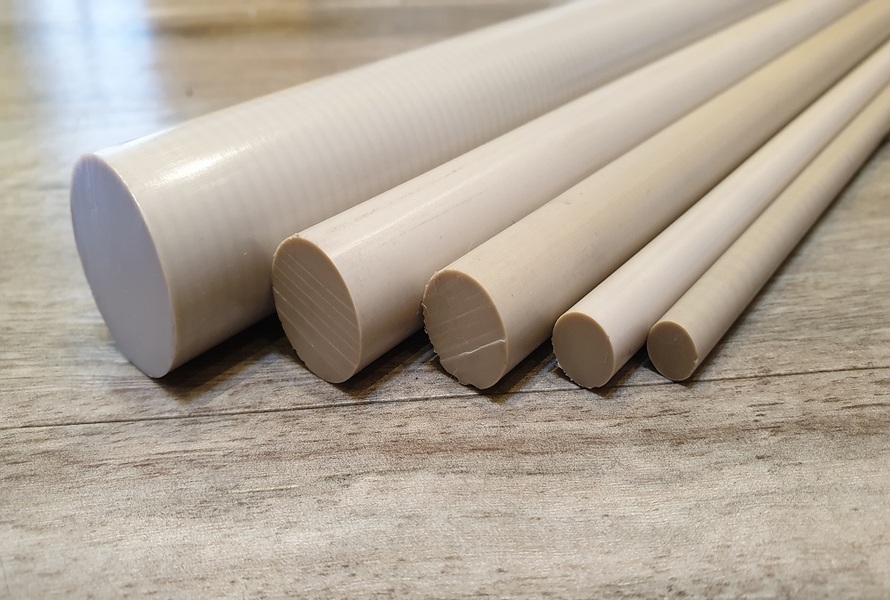
Picture 1: PEEK plastic is in round shape
1. Overview of PEEK plastic
What is the definition of Plastic PEEK? There exists a considerable degree of confusion among customers regarding the underlying concept and notable attributes of this particular fuel line. PEEK resin is manufactured using a molding procedure involving polyetheretherketone resins at optimal temperatures.
The scientific nomenclature for PEEK Plastic is Poly Ether Ether Ketone. The substance was first identified in 1978 by the ICI Corporation, a company based in the United Kingdom. The primary chemical composition of PEEK Resin consists of several interconnected Benzene rings, linked together by two functional groups: an ether group (-O-) and a ketone group (-C(=O)-).
Typically, the dimensions of PEEK plastic are categorized into two distinct sorts, as outlined below:
The most commonly used size for plastic PEEK in sheet form is 600x1000mm, with thickness options ranging from 5 mm to 60mm.The plastic PEEK in bar shape has an average diameter ranging from φ5 to φ200mm, with a standardized length of 1000mm.
Furthermore, it should be noted that PEEK plastic is manufactured in a diverse range of colors, including but not limited to dark brown, black, white, and gray, to cater to the market's demands. PEEK plastic is widely recognised as a highly esteemed plastic material on a global scale, renowned for its exceptional quality. It is frequently employed as a substitute for metal in various applications.
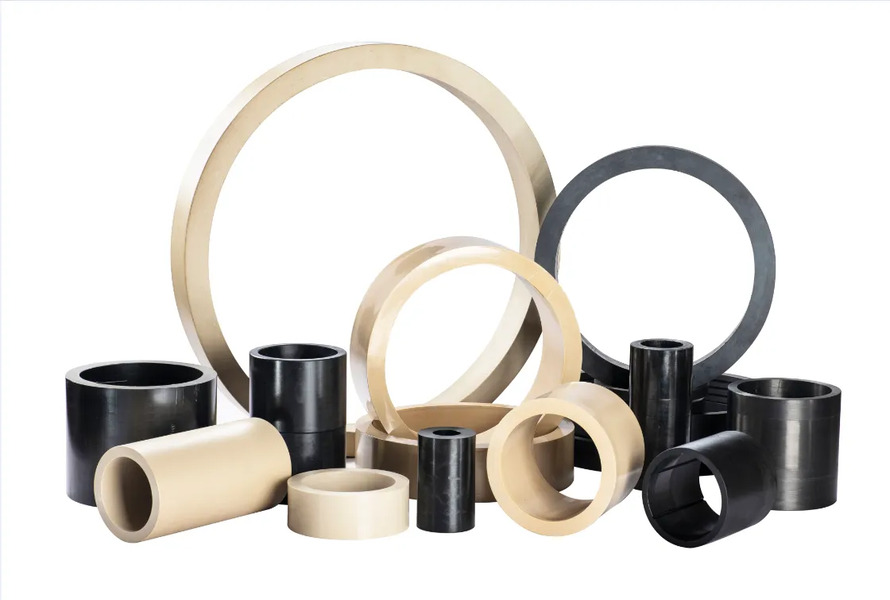
Picture 2 PEEK resin is manufactured using a molding procedure involving polyetheretherketone resins at optimal temperatures.
Furthermore, PEEK plastic is classified as a distinct variant of construction plastic due to its exceptional characteristics, including remarkable heat resistance, an elastic modulus measuring 3.6 Gpa, and a tensile strength of 170 MPa.
Specifically, the PEEK polymer exhibits two distinct glass transition temperatures, namely 140 degrees Celsius and 275 degrees Celsius, which are characterized by a high level of detail. In addition, the mechanical qualities and chemical resistance of PEEK plastic are noteworthy factors contributing to its increasing popularity.
Various additives often used in plastic production, such as PTFE, graphite, ceramic, carbon, or glass, are used in the processing of PEEK plastic to enhance its operating temperature capabilities. According to experts, PEEK plastic is widely regarded as environmentally friendly and does not have any adverse effects on natural ecosystems.
2. Typical specifications of PEEK plastic
Specifications |
PEEK Plastic - Poly Ether Etherketone |
Specific gravity (Unit: g/cm3): |
1.3 |
Water permeability calculated in 24 hours at a temperature of 23 degrees Celsius: |
Approximately 0.14 |
Tensile strength Mpa: |
About 87 |
Expansion (Unit: %): |
80% |
Flexural strength Mpa: |
From 142 |
Durability upon impact (Unit: Lzod j/m): |
Up to 3700 |
Hardness calculated according to the Rockwell system: |
88 |
Long-term temperature tolerance: |
M98 |
Short-term temperature tolerance: |
Nearly 260 Celsius Degree |
Melting point: |
Reaches 300 degrees Celsius |
Lowest temperature: |
Minus 40 Degrees Celsius |
Resistivity (Unit: Ω・cm): |
Standard 1 x E16 |
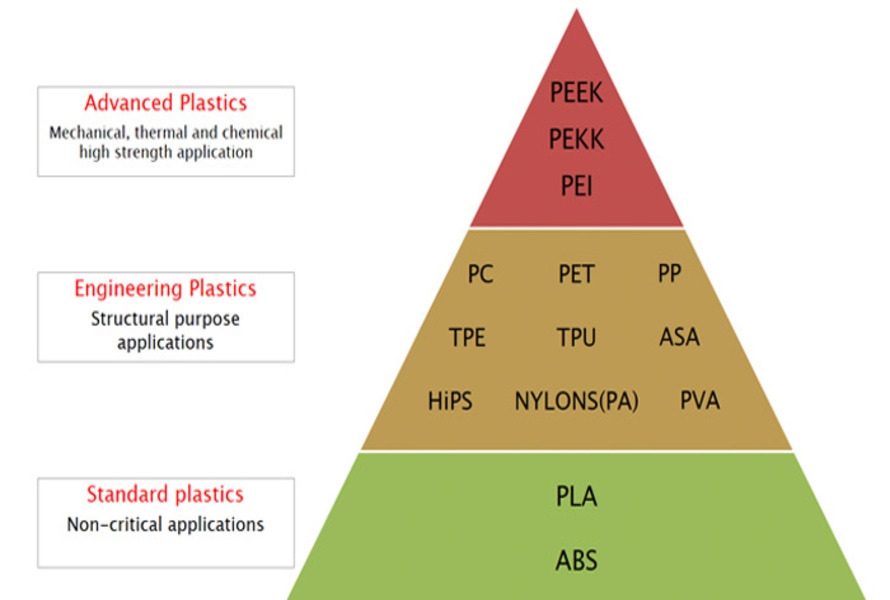
Picture 3 PEEK plastic has the highest standards and properties of all current industrial plastic materials
In the next section, we will send you the outstanding advantages that help PEEK plastic gain the trust of the market as well as be fully utilized in many large-scale factories.
Read more: What is compounding in polymer? Common types of polymer compounding
3. Advantages of PEEK plastic
PEEK plastic possesses all the impressive advantages of heat resistance, force resistance and appropriate physical and chemical properties in each specific production field.
It is not an exaggeration to say that the quality of PEEK Plastics cannot be argued because they have been rigorously tested for application in the aerospace field. This shows that all chemical and physical properties must be perfect. Let;s take a look about 4 main benefits of PEEK Plastics:
3.1. Resistance to impurities and chemicals
Leading industry experts have stated that the corrosion resistance of PEEK plastic is considered nearly equal to Nickel steel - one of the most famous durable materials in the construction industry.
In particular, strong Sulfuric Acid is the only chemical compound that can destroy the structure of PEEK plastic; conventional chemicals or organic solvents are still not capable of doing this. This property still works very well even under high temperature conditions.
That is why PEEK plastic becomes a suitable choice for medical devices that are frequently exposed to chemicals while still ensuring safety for human health.
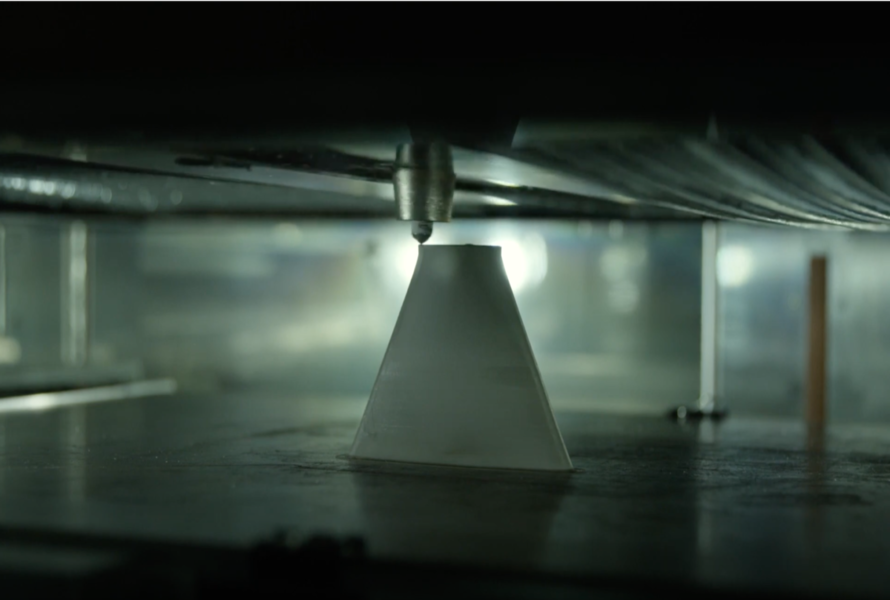
Picture 4 PEEK chemical resistance brought to the new level
3.2. Perfect heat resistance
PEEK plastic can tolerate an average temperature of 260 degrees Celsius throughout the processing phase. This is a much higher temperature than conventional plastics, which is only about 150 degrees Celsius.
In addition, eek plastic reaches a melting temperature of up to 334 degrees Celsius and factories need to use a temperature of nearly 400 degrees Celsius to successfully mold PEEK plastic. The strongest point of PEEK plastic is that its physical properties are difficult to change in high temperature environments.
Furthermore, this material can only be sterilized using high-pressure steam in an industrial autoclave because it is resistant to steam and hot water. PEEK plastic is also particularly tough to break down because of its property. As a result, the information is used in the space and aviation industries.
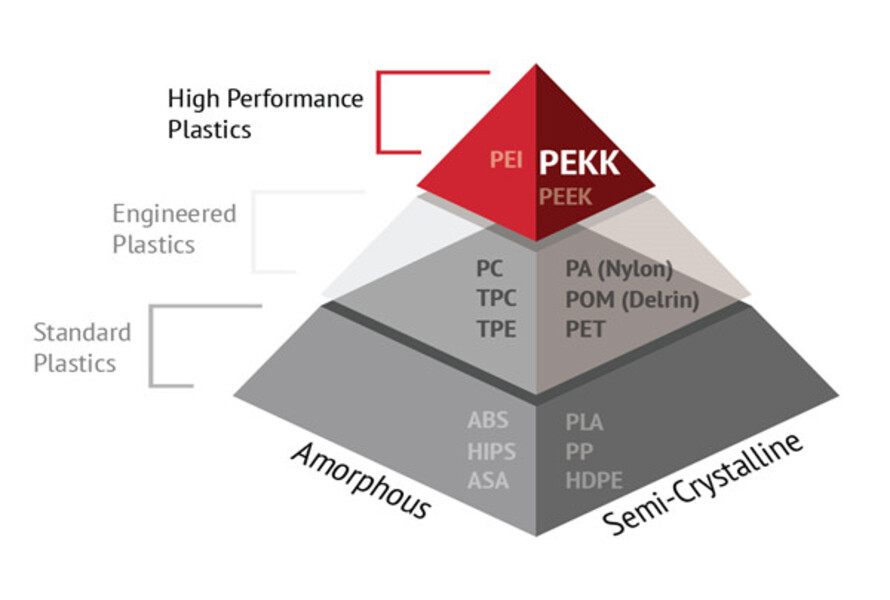
Picture 5 PEEK plastic has the highest heat resistance
3.3. Safety for consumers' health
The Japanese Food Hygiene Law and the US FDA have recognized the safety standards of PEEK plastic for human health so that this material is commonly used in the food and pharmaceutical industries. PEEK plastic is also a suitable material in fields that require strict friction coefficients as well as corrosion resistance. Because the ingredients inside PEEK plastic contain graphite and carbon fiber content
3.4. Radiation resistance
PEEK plastic has radiation resistance that surpasses Polystyrene compound, this is the industrial plastic material with the best radiation resistance. In particular, PEEK plastic can withstand radiation levels up to 1100 Mrad.
In addition, PEEK plastic is the only type of plastic that is highly resistant to fire and explosion without needing any additional materials or substances during the production process because it is a very stable polymer compound. The standard fire resistance level of the material ranges from UL 94V - 0 to HB.
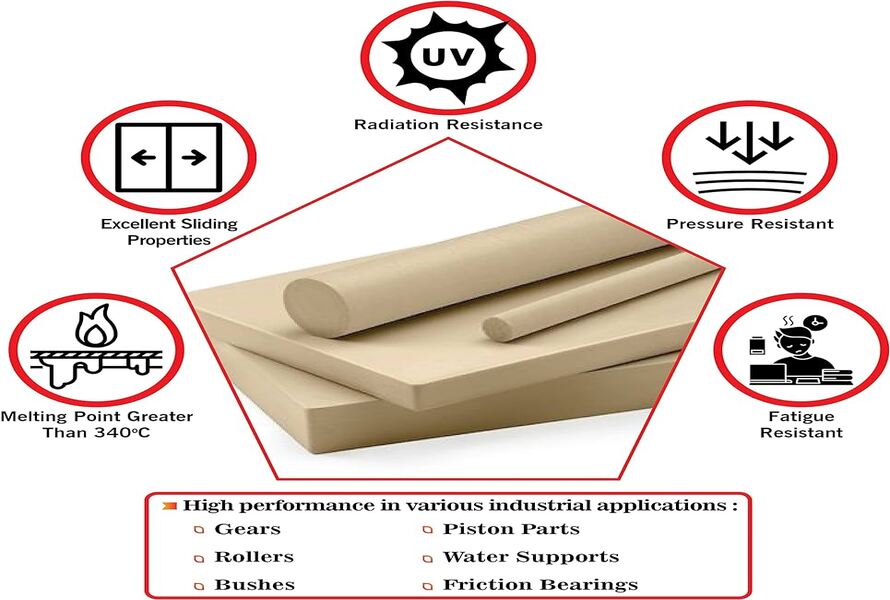
Picture 6 PEEK plastic possesses full standards suitable for humans and is very durable
4. Disadvantages of PEEK plastic
However, PEEK plastic also has a few disadvantages that businesses or factories need to pay attention to before making purchasing decisions. The material only has 2 weaknesses, namely:
4.1. High price compared to other types of plastic
PEEK Plastic possesses many leading characteristics among all types of industrial plastic materials. Therefore, the price of this material is not too cheap. By the end of 2022, the average PEEK plastic price is about 170,000 VND/kg.
This price can be about 39 times higher than engineering plastics and nearly 50 times higher than regular plastics. Materials also experience price fluctuations, but not to such a large extent. Therefore, business and factory owners must pay careful attention to this so that the operating process and cost optimization can occur most effectively.
4.2. High technical requirements
EuroPlas mentioned that PEEK plastic is the most durable plastic material. Therefore, the disadvantage of this material is that it can easily chip and crack during processing or cutting at large factories. Substandard blades are likely to crack or break when exposed to PEEK plastic during processing.
.jpg)
Picture 7 PEEK plastic production requires high technical
This is the reason why technicians must have many years of experience and detailed understanding of each type of machine as well as the properties of this material.
However, these disadvantages do not hinder the popularity of PEEK plastic in life and heavy industries. Many fields have taken full advantage of PEEK plastic and brought the best products to the market. Let's consult with EuroPlas.
5. Common applications of PEEK plastic
Currently, PEEK plastic appears in almost every field from small to large scale such as: technology - electronics, mechanics, healthcare, aviation,...
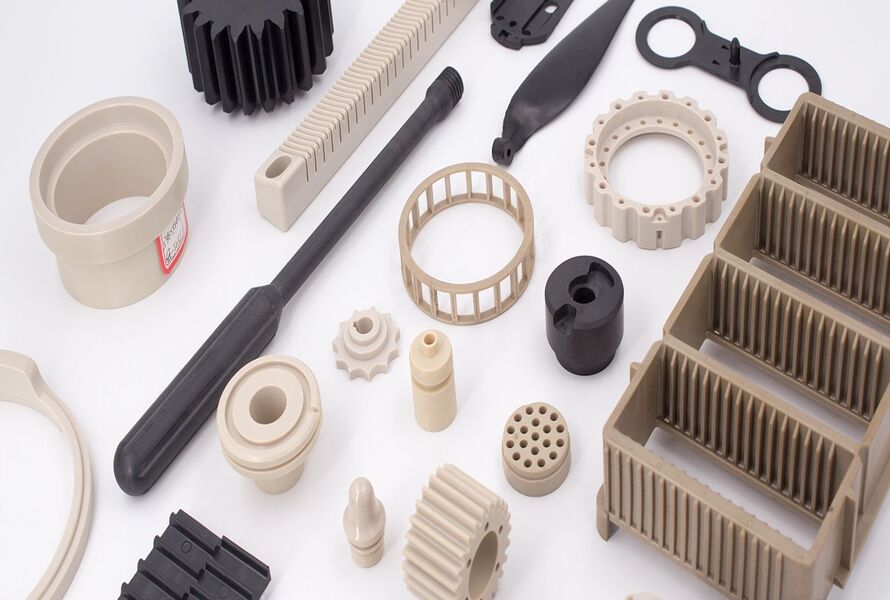
Picture 8 The Applications of Peel Plastic
5.1. Electronic and technology equipment
PEEK resin not only has excellent electrical insulation but also maintains it during harsh processing with high pressure, high humidity as well as high temperature. It is an important ingredient for the production of wafer carriers, interconnect devices or insulating membranes in the semiconductor industry.
To achieve the best corrosion resistance and heat insulation, paint made from PEEK powder resin will be coated on the surface of the metal as well as undergo thermal spraying methods. In particular, Japanese businesses prefer PEEK plastic and use it largely in the manufacturing and production of integrated electronic circuits.
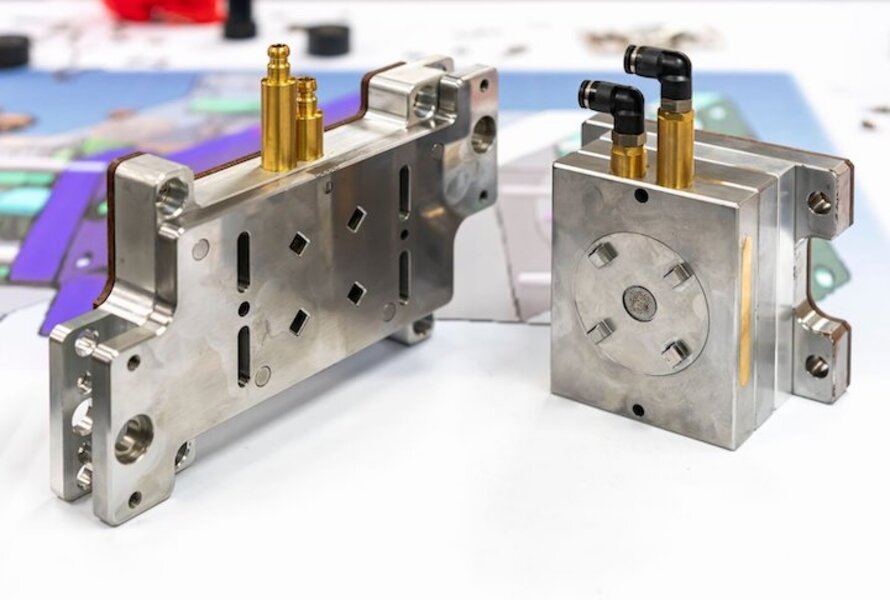
Picture 9 PEEK resin not only has excellent electrical insulation but also maintains it during harsh processing with high pressure.
5.2. Large-scale mechanical production
Next, PEEK plastic will also be utilized in transportation and storage devices for natural gas, ultrapure water or petroleum, such as pumps, pipelines and pump valves. PEEK plastic becomes the material to produce measurable equipment the amount of petroleum deep below tanks to ensure absolute safety for workers.
Products such as piston rings, gaskets, and products exposed to chemicals are also made from PEEK resin. Furthermore, the properties of PEEK resin are extraordinary because it can bond tightly with other adhesives under high-temperature conditions.
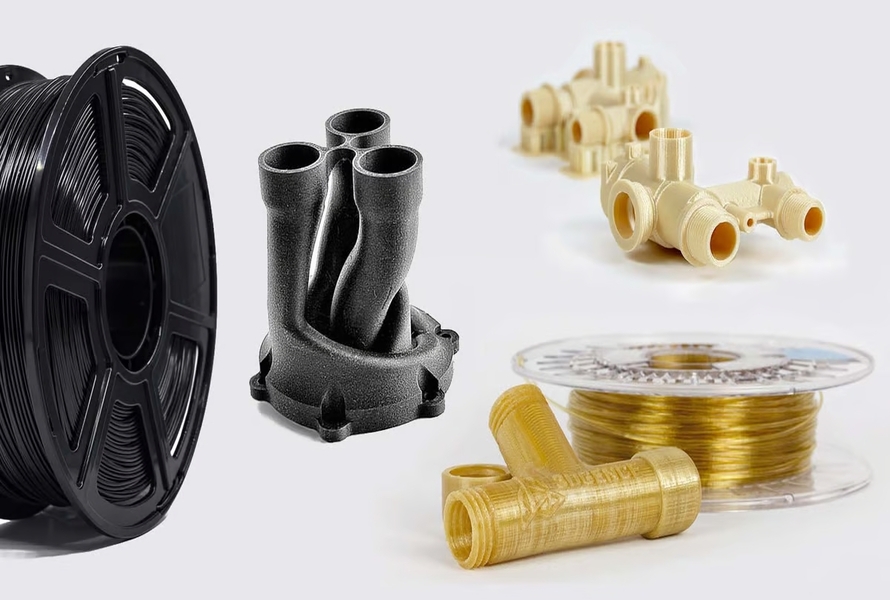
Picture 10 PEEK Plastics are used to manufacture connectors, water-pipes, or pump heads
Therefore, connector products of automatic machine systems are also a potential market suitable for this material.
5.3. Medical equipment
Thanks to its anti-corrosion solid characteristics, safety for consumer health, and good compatibility with biological substances, PEEK plastic is used in producing dental and medical equipment for surgery. It can make artificial bones instead of conventional metal materials. Scientists have also verified that the elastic modulus of PEEK plastic is utterly compatible with the human body and does not cause any chemical reactions.
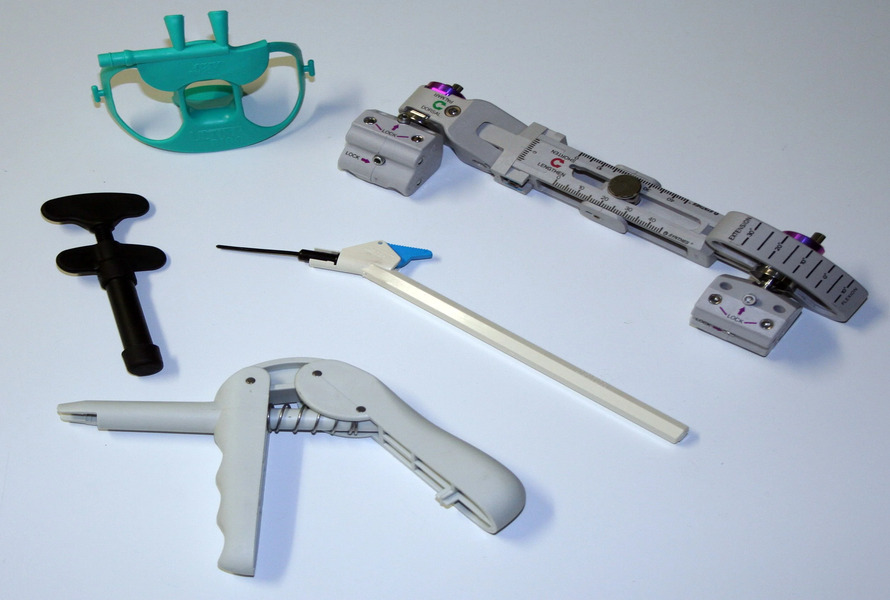
Picture 11 PEEK Plastic manufactures medical instruments
5.4. Energy and aerospace
As we all know, the heat resistance level of PEEK plastic is the highest among industrial plastics. Therefore, it can replace metals and aluminum to produce various aircraft parts. It increases aviation safety and minimizes engine burn during long-haul commercial flights.
In particular, the space industry is also an important field exposed to many equipment and high temperatures. And PEEK plastic is also the perfect choice. PEEK plastic also appears in nuclear power plants because of its ability to withstand radiation, hydrolysis, and high temperatures. Coil and cable reels are popular products of this material.
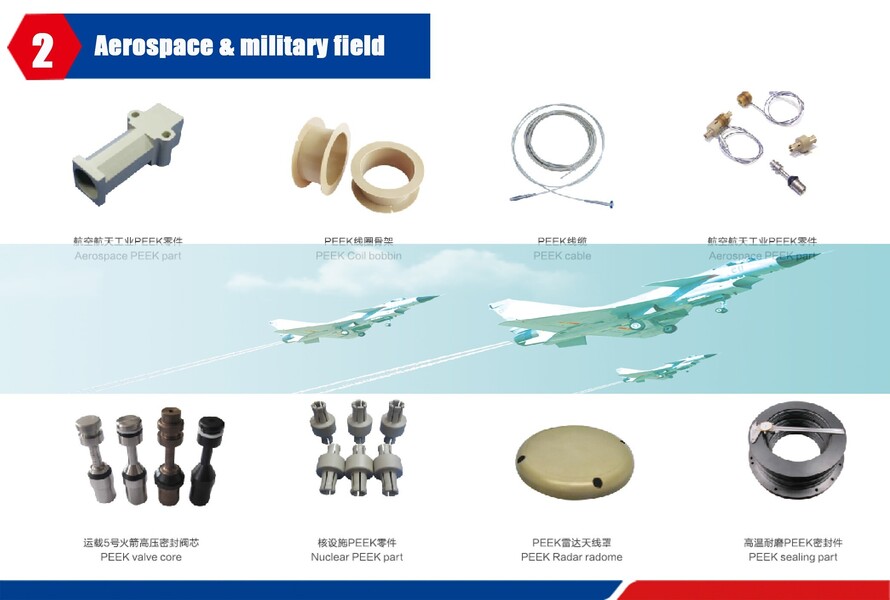
Picture 12 PEEK polymer material is utilized in Energy and Aerospace
5.5. Automobile
Polymer PEEK material has many advantages in terms of wear resistance, lightweight, and high strength, so it can quickly be processed into components with minimal tolerances, ensuring absolute safety for vehicles during long trips. The material is still capable of replacing other synthetic materials.
6. Conclusion
EuroPlas has provided you with the most detailed information about PEEK plastic material and its common applications. We hope that this article will bring useful knowledge to support your production process and life.
EuroPlas offers different kinds of engineering plastic compounds, some of them are:
- PBT GF-FR compound: PBT GF-FR compound is an engineering plastic comprising PBT plastic with glass fiber reinforcements, color, and flame retardant additive. Thanks to its long-term heat aging stability as well as mechanical and financial benefits, the PBT GF-FR compound is widely utilized in kitchen equipment, household appliances, electrical engineering, and car interiors. Besides, it also enhances the final products' durability and longevity.
- PA6, PA66 blend compound: PA6 and PA6 are two typical types of PA plastic. While PA6 has a lower melting temperature but is easier to process, distorts less, and is cheaper, PA66 has lower water absorption but higher temperature resistance, stiffness, and abrasion resistance than the other. PA6, PA66 blend compound comprises PA6/PA66 resin, elastomer, and impact strength modifiers, so it is resilient with strong mechanical properties.
- PA66, PA6 Glass fiber compound: Polyamide-6 (PA6) and Polyamide-66 (PA66) are ideal engineering thermoplastics in manufacturing because it is stiff, strong, and heat resistant. And those polymers even achieve a higher level of properties with reinforcing agents such as glass fiber, glass beads, talc...
- PC flame retardant compound: Polycarbonate (PC) is a thermoplastic material widely used in manufacturing due to its unique characteristics such as being lightweight, durable, and resistant to impact and high temperatures. It also has excellent optical clarity and is an excellent electrical insulator.
Please continue to follow EuroPlas to quickly update the latest news about industrial plastic lines!