In the automotive industry, automotive UV stabilizers play a crucial role in maintaining the essential physical and aesthetic properties of exterior and interior components, including bumpers, door trims, airbags, and instrument panels. With the development of advanced polymer additives, UV stabilizers have become an increasingly essential component in the production of high-quality automotive components. In this article, we will delve into the technical properties of UV stabilizer automotive and examine their impact on the industry.
Related:
- What are plastic additives? 8 most common plastic additives in plastic industry
- UV stabilized vs UV resistant for plastic - a complete comparison
- UV stabilizers for plastics - everything you need to know
- Why are UV Masterbatches expected to be a key product for the Indian market?
- UV stabilizers in plastic: 4 common types and applications
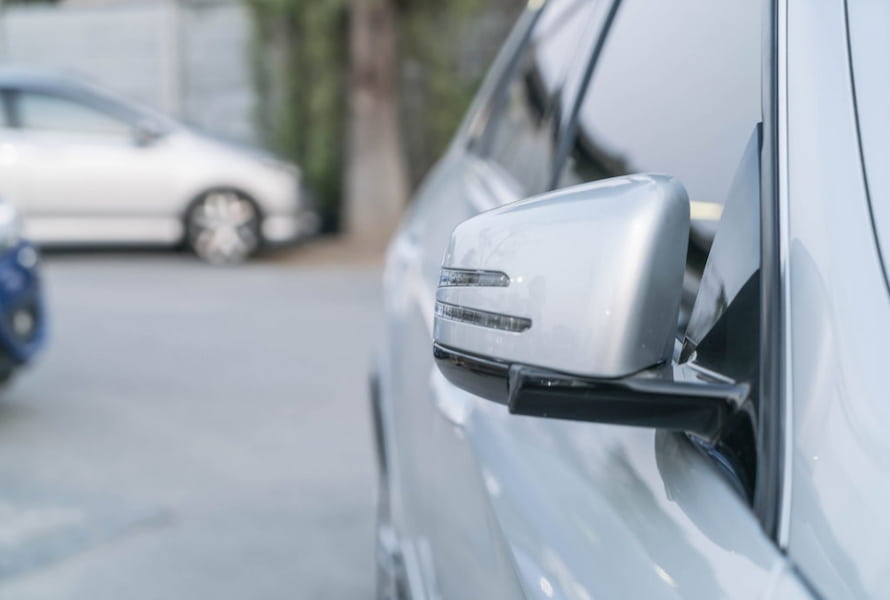
1. Why Automotive Need UV Stabilizers?
1.1. What Are Automotive UV Stabilizers?
Automotive UV stabilizers are special additives used in the manufacturing of plastic components in the automotive industry. They help protect the plastic parts from degradation due to exposure to harsh environmental conditions, such as ultraviolet (UV) light, heat, and moisture. The primary function of UV stabilizers is to prevent color fading, microcrack formation, and loss of physical properties in plastic components, such as bumpers, door panels, door trims, instrument panels, airbags, seat back covers, and body side moldings.
The use of UV stabilizers ensures that automotive components retain their essential physical and aesthetic properties and prolong their service life. The standards for performance requirements in end-use environments for automotive components are set by the Society of Automotive Engineers (SAE) in North America.
1.2. How Do UV Light Stabilizers Work in Automotive?
UV light stabilizers play a crucial role in protecting automotive components from the damaging effects of UV light. These stabilizers are added to the polymers used in various automotive parts, including bumpers, door panels, door trims, instrument panels, airbags, seat back covers, and body side moldings, to enhance their ability to withstand harsh environmental conditions.
UV light stabilizers work by preventing the formation of microcracks and limiting color fading in the components, thereby maintaining their essential physical and aesthetic properties. This helps to ensure the longevity and performance of automotive parts, even when exposed to prolonged exposure to UV light. The use of UV light stabilizers in automotive applications is important for maintaining the appearance, performance, and sustainability of these products.
1.3. How Do UV Stabilizers Deal with Automotive Weathering Requirements?
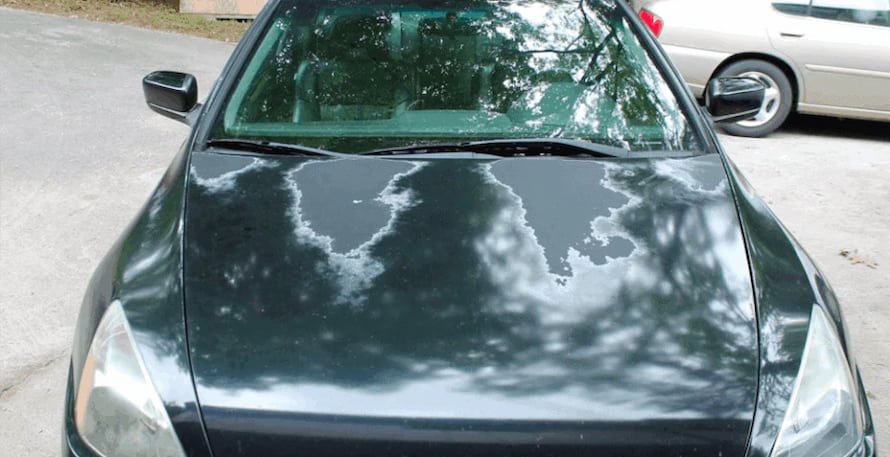
Automotive parts are frequently exposed to demanding environmental conditions such as sunlight, heat, and moisture, which require materials that can endure the exposure and maintain their performance over their lifetime. The Society of Automotive Engineers (SAE) in North America sets standards for both interior and exterior automotive parts and determines performance requirements in actual usage environments.
For example, exterior components like bumpers and taillight casings must be able to withstand continuous exposure to UV light and water spray without losing their physical properties, as outlined in SAE J2527. Meanwhile, interior components like instrument panels and airbag covers must also be able to withstand prolonged exposure to UV light and higher temperatures, as specified by SAE J2412, although they are not subjected to the same water exposure tests as exterior components.
These above conditions can cause significant damage to the materials used in automotive applications, leading to discoloration, cracking, and premature aging. To address these challenges, automotive manufacturers often add UV stabilizers to the materials they use, in order to extend the life and performance of their products.
Another reason why automotive applications require UV stabilizers is that they help to improve the appearance of automotive parts and components. By preventing discoloration and cracking, UV stabilizers help to maintain the original look and feel of automotive parts and components, even after prolonged exposure to the elements.
1.4. UV Stabilizers for Automotive Components
.jpg)
Finally, UV stabilizers are important in automotive applications because they can help to improve the sustainability of these products.
Plastics are increasingly used in place of traditional materials, but the harsh environments in which automotive components are used require manufacturers to use UV light stabilizers to ensure the longevity and durability of polymeric components. This is the case despite the fact that plastics are increasingly used to replace traditional materials. When combined with polymers like PP, TPO, and TPE, advanced UV light stabilizer solutions for the automotive industry provide manufacturers with additional advantages. These benefits include low VOC, low fogging, and low odor qualities.
By extending the life of automotive parts and components, UV stabilizers can help to reduce the need for frequent replacements, which can be both expensive and wasteful.
The use of UV stabilizers in automotive applications is critical for maintaining the performance and appearance of these products, even under harsh environmental conditions. By preventing damage from UV rays, UV stabilizers help to ensure the longevity, safety, and sustainability of automotive products.
2. Technical Properties of Automotive UV Stabilizers
UV stabilizers are added to polymers to prevent or reduce the effects of photo-degradation and extend the service life of automotive components. Below are some of the significant technical properties of automotive UV stabilizers that you can considered before choosing a quality UV stabilizers for your products:
2.1. Absorb UV light
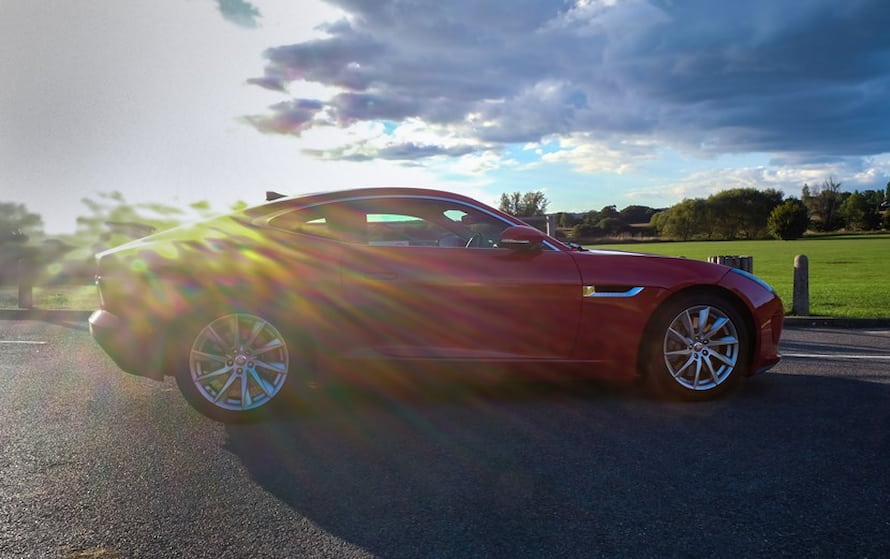
One of the key technical properties of automotive UV stabilizers is their ability to absorb UV light. This helps to reduce the amount of UV light that reaches the polymer and thus reduces the rate of photo-degradation. UV stabilizers are designed to absorb a specific range of wavelengths, depending on the type of polymer they are being added to. Some UV stabilizers are also designed to absorb UV light over a broad range of wavelengths, making them highly effective for a wide range of applications.
2.2. Improve the thermal stability of polymers
Another key technical property of automotive UV stabilizers is their ability to improve the thermal stability of polymers. This helps to prevent the formation of microcracks, which can weaken the structure of the polymer and lead to mechanical failure. UV stabilizers can also help to limit color fading, as well as improve the overall resistance to environmental degradation, including moisture, heat, and chemicals.
2.3. Chemical resistance
Automotive UV stabilizers can help improve the resistance of plastic parts to chemical attacks, including exposure to fuels, oils, and other automotive fluids.
2.4. Improved mechanical properties
UV stabilizers can enhance the mechanical properties of plastic parts, such as strength and flexibility, allowing them to better withstand the stresses and strains of use.
2.5. Highly compatible with polymers
In addition, automotive UV stabilizers are also designed to be highly compatible with a wide range of polymers, including polycarbonate, polyethylene, polypropylene, and many others. This compatibility helps to ensure that the performance of the polymer is not diminished when the UV stabilizer is added and that the overall performance of the polymer is enhanced.
2.6. Cost-effective material
Finally, automotive UV stabilizers are also designed to be cost-effective, making them a popular choice for manufacturers looking to improve the durability and performance of their products. These stabilizers are typically added in small quantities to the polymer, and they have a long shelf life, making them easy to store and use.
In short, automotive UV stabilizers play a critical role in improving the performance and durability of plastic parts used in the automotive industry. These properties, combined with their compatibility with a wide range of polymers and cost-effectiveness, make UV stabilizers an essential ingredient in the production of automotive components.
3. Finding Automotive UV Stabilizers for Your Products?
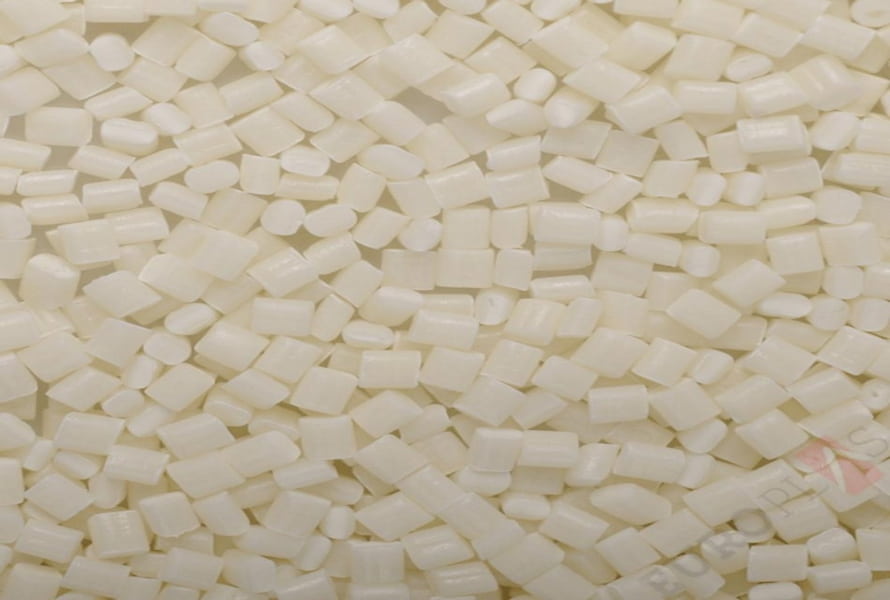
Automotive UV stabilizers of the European Plastic Joint Stock Company (EuP) has been strongly trusted by numerous plastic manufacturers in Vietnam and around the world. Using anti-UV additive of EuP can help you minimize and prevent degradative impacts of UV lights on end-products.
Advantages of automotive UV stabilizers from EuroPlas:
- Prevent UV light's negative impacts on end-products
- Maintain end-products' mechanical properties and improve end-products' durability
- Great dispersion without spots
- Strongly absorb organic UV lights
- Permanent effectiveness
As the leading producer of filler masterbatch in the world, EuroPlas is pleased to provide a special plastic material solution that aids clients' factories in reducing production costs and boosting market competitiveness. EuP is dedicated to giving users the best possible experience. As a result, consumers can be entirely confident in the quality of the goods and services when they use our automotive UV stabilizers products.
If there is a need, please contact us via the form to get the earliest advice and support!