When it comes to yarn extrusion, selecting the right additive masterbatch is paramount for achieving exceptional performance and meeting specific requirements. By incorporating additive masterbatches into the extrusion process, manufacturers can enhance yarn properties, improve process efficiency, and differentiate their products in a competitive market. This comprehensive guide will shed light on the key factors to consider when choosing the ideal additive masterbatch for yarn extrusion.
Read more: What are plastic additives? 8 most common plastic additives in plastic industry
1. Importance of additive masterbatch in yarn extrusion
Additive masterbatches play a crucial role in yarn extrusion, where they are used to enhance the properties and performance of the yarn. The importance of selecting the right additive masterbatch for yarn extrusion cannot be overstated. Here are some key reasons why it is essential:
- Property Enhancement: Additive masterbatches allow manufacturers to tailor the properties of the yarn to meet specific requirements. Whether it's improving antimicrobial properties, UV resistance, flame retardancy, or static control, the right selection of additive masterbatch ensures that the yarn possesses the desired characteristics.
- Product Differentiation: In a competitive market, product differentiation is crucial. By selecting the appropriate additive masterbatch, manufacturers can create yarn with unique features and functionalities that stand out from their competitors. This can include properties such as enhanced brightness, improved softness, or advanced performance attributes, giving the yarn a competitive edge.
- Process Optimization: Additive masterbatches can optimize the yarn extrusion process. They can improve the processability of the polymer melt, enhance flow properties, reduce friction, and prevent issues like melt fracture. This leads to smoother processing, increased production efficiency, and reduced downtime.
- Consistency and Uniformity: The use of additive masterbatch ensures consistent and uniform dispersion of additives throughout the yarn. This is crucial for achieving consistent performance and appearance in the final product. Uniform dispersion prevents issues such as uneven coloration, streaking, or poor distribution of functional additives, ensuring high-quality yarn production.
- Cost Optimization: The right selection of additive masterbatch can contribute to cost optimization. By incorporating additives in a concentrated form, manufacturers can reduce the overall consumption of additives, minimize wastage, and lower production costs. Additionally, additive masterbatches may offer cost advantages over purchasing individual additives separately.
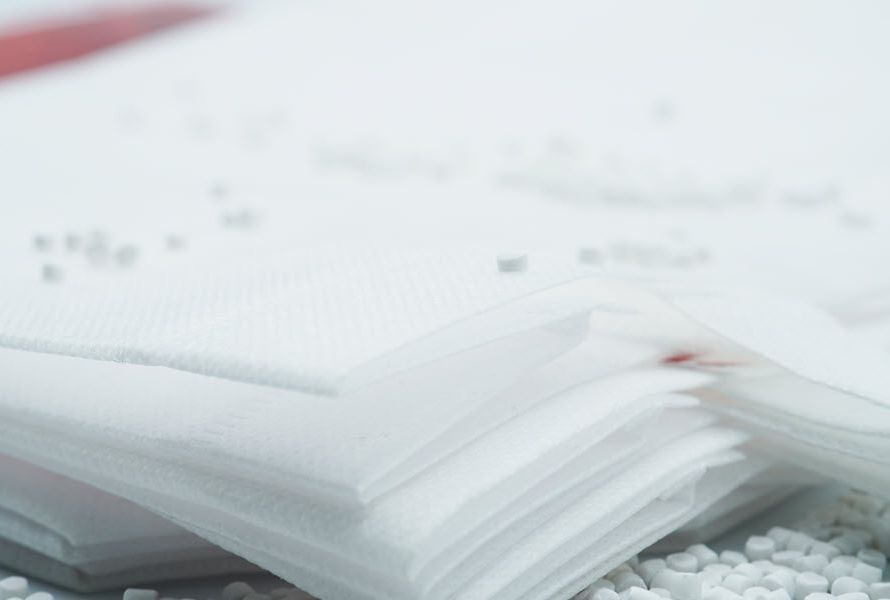
In yarn extrusion, additive masterbatches are essential because they improve the characteristics and functionality of the yarn.
2. Understanding Additive Masterbatch
Additive masterbatch refers to a concentrated mixture of additives that are incorporated into a polymer resin during the manufacturing process. The masterbatch is typically in a solid or pellet form and is added to the base polymer in specific proportions to achieve desired properties or enhancements in the final plastic product
The purpose of additive masterbatch is to simplify the addition of additives to the polymer manufacturing process. By pre-blending the additives into a masterbatch form, manufacturers can ensure uniform dispersion and accurate dosing of additives in the final product, leading to consistent performance and quality. This approach also allows for efficient handling and storage of additives since they are combined into a single concentrated form.
In yarn extrusion, additive masterbatches are commonly used to enhance the properties and performance of the yarn. Here are some types of additives commonly used in yarn extrusion:
- UV Stabilizers: These additives help protect the yarn from the damaging effects of ultraviolet (UV) radiation, preventing color fading and degradation when exposed to sunlight.
- Antioxidants: Such agents are employed to inhibit the degradation of the yarn caused by oxidation, thereby extending its lifespan and preserving its mechanical properties.
- Slip Agents: These agents reduce the friction between yarn fibers, improving the yarn's processability during extrusion and facilitating downstream processes like weaving or knitting.
- Antistatic Agents: These agents help reduce the buildup of static electricity in the yarn, minimizing issues such as lint attraction and static discharges.
- Flame Retardants: These compounds are incorporated into the yarn to enhance its fire resistance properties, making it safer in applications where fire hazards may be a concern.
- Lubricants: These additives are used to reduce friction and improve the flow of the polymer during extrusion, resulting in smoother yarn production and better processability.
- Colorants: Color additives are added to achieve desired hues and shades in the yarn, allowing for a wide range of color options.
- Antimicrobial Agents: In hygiene-sensitive applications, antimicrobial additives may be included to inhibit the growth of bacteria, fungi, and other microorganisms, ensuring the yarn's cleanliness and hygiene.
- Processing Aids: Processing aids are additives that assist in the extrusion process, enhancing melt flow, preventing melt fracture, or improving surface smoothness.
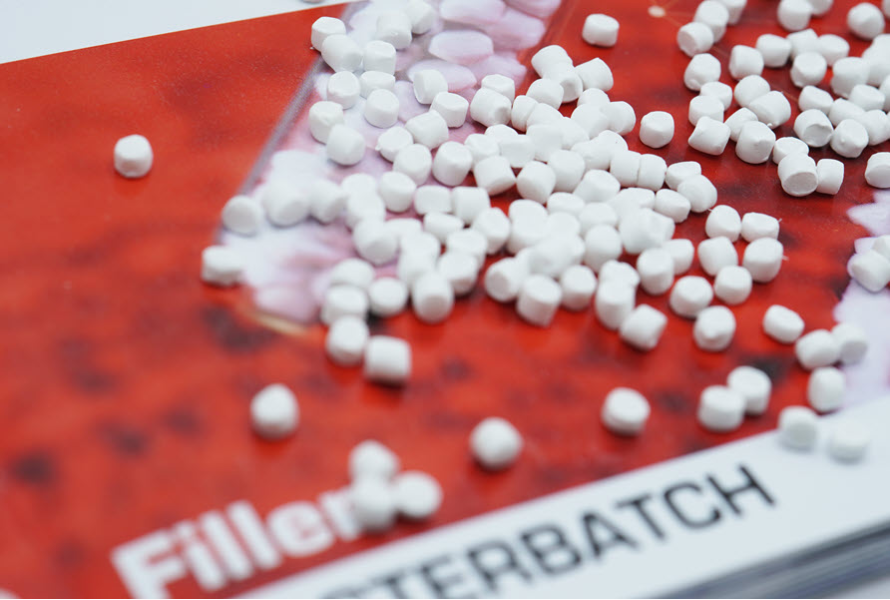
A concentrated mixture of additives added to a polymer resin during the manufacturing process is referred to as an additive masterbatch.
3. Popular additive masterbatch choices for yarn extrusion
When choosing an additive masterbatch for yarn extrusion, several important factors should be considered. These factors include:
- Desired Properties: Identify the specific properties you want to enhance in your yarn, such as color, UV resistance, flame retardancy, antimicrobial properties, or static control. This will help you select an additive masterbatch that aligns with your desired outcomes.
- Compatibility: Ensure that the additive masterbatch is compatible with the polymer used in your yarn extrusion process. Different polymers have varying compatibility requirements, so it is essential to choose a masterbatch that is specifically designed for your polymer type.
- Concentration Levels: Consider the recommended concentration levels of the additive masterbatch. The concentration should be sufficient to achieve the desired properties without negatively impacting the overall performance or processability of the yarn.
- Dispersion: Look for an additive masterbatch that provides excellent dispersion properties. Effective dispersion ensures that the additives are uniformly distributed throughout the yarn, leading to consistent performance and appearance.
- Regulatory Compliance: If your yarn is intended for specific applications, such as medical textiles or children's products, ensure that the additive masterbatch meets the relevant regulatory standards and requirements. This may include compliance with safety regulations, environmental standards, or specific industry certifications.
- Supplier Reputation: Choose a reputable supplier with a track record of delivering high-quality additive masterbatches. A reliable supplier will provide consistent product quality, technical support, and reliable delivery, ensuring a smooth manufacturing process.
- Cost-effectiveness: Consider the cost-effectiveness of the additive masterbatch. Evaluate the overall cost of the masterbatch, including its concentration levels, performance benefits, and potential savings in terms of reduced additive consumption or improved production efficiency.
- Sustainability: In line with growing environmental concerns, consider additive masterbatches that promote sustainability. Look for options that use recycled materials, reduce waste generation, or minimize energy consumption during the manufacturing process.
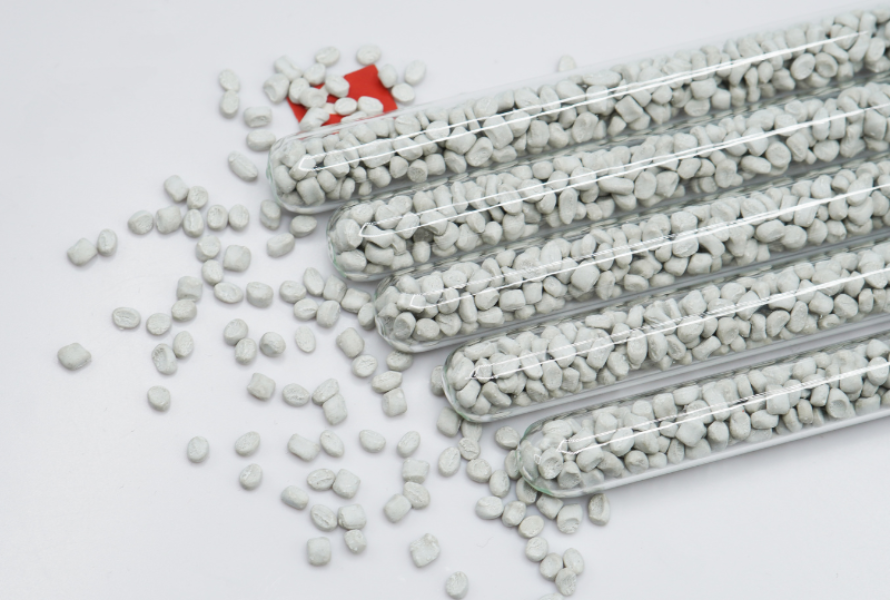
There are a number of crucial considerations to make when selecting an additive masterbatch for yarn extrusion.
3.1. UV stabilizers for outdoor applications
One popular and widely-used additive masterbatch for yarn extrusion, especially in outdoor applications, is UV stabilizers. These specialized additives play a crucial role in protecting yarns from the harmful effects of ultraviolet (UV) radiation, which can cause significant damage over time. In outdoor environments, where yarns are exposed to prolonged sunlight, UV stabilizers are essential for maintaining the yarn's colorfastness, physical integrity, and overall performance.
UV stabilizers act as a shield against UV radiation by absorbing or reflecting the harmful UV rays before they can penetrate and degrade the yarn. This protection helps to prevent color fading, loss of strength, brittleness, and other forms of degradation that can occur when yarns are exposed to intense sunlight. By incorporating UV stabilizers into the yarn extrusion process, manufacturers can ensure that their products maintain their original appearance and performance characteristics for an extended period, even in challenging outdoor conditions.
The selection and incorporation of UV stabilizers in yarn extrusion involve careful consideration of factors such as the required level of UV protection, the specific polymer used in the yarn, and the desired performance characteristics. Manufacturers can choose from a range of UV stabilizer options, including organic UV absorbers, inorganic UV blockers, and combinations thereof, to tailor the protection to their specific application requirements.
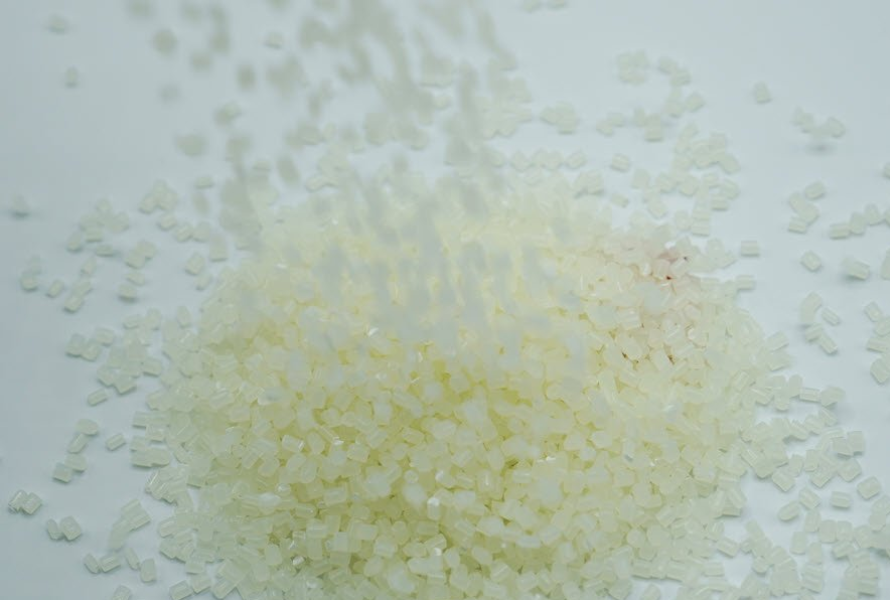
UV stabilizers are a common and extensively used additive masterbatch for yarn extrusion, particularly in outdoor applications.
3.2. Antimicrobial additives for hygiene-sensitive applications
In hygiene-sensitive applications, such as medical textiles, healthcare products, or personal care items, antimicrobial additives play a crucial role in ensuring cleanliness and preventing the growth of harmful microorganisms. Antimicrobial additive masterbatches are specifically designed to incorporate agents that inhibit the growth and proliferation of bacteria, fungi, and other microbes, thereby maintaining a hygienic environment and reducing the risk of infections.
Yarns treated with antimicrobial additives provide an added layer of protection against the colonization and spread of microorganisms. These additives work by disrupting the cellular functions of microbes, inhibiting their ability to multiply and survive on the yarn surface. By incorporating antimicrobial additive masterbatches during yarn extrusion, manufacturers can create yarns with built-in antimicrobial properties that are effective in reducing the microbial load and preventing the development of unpleasant odors.
When selecting antimicrobial additive masterbatches for yarn extrusion, it is important to consider factors such as the desired level of antimicrobial efficacy, compatibility with the yarn polymer, and regulatory compliance. Different antimicrobial agents offer varying degrees of effectiveness against specific types of microorganisms. It is crucial to choose an additive masterbatch that has been tested and proven to provide the necessary antimicrobial protection for the intended application.
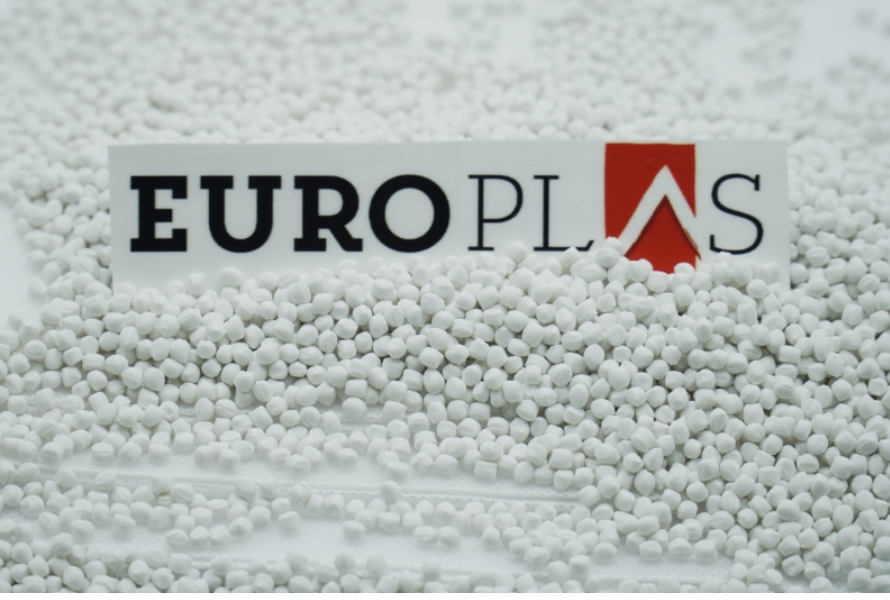
When it comes to maintaining hygiene and stopping the growth of dangerous microorganisms, antimicrobial additives are necessary.
3.3. Flame retardant options for safety considerations
In applications where safety is a primary concern, incorporating flame retardant additives into yarn extrusion is essential to reduce the risk of fire and enhance overall safety. Flame retardant additive masterbatches are specifically designed to impede or slow down the spread of flames, providing valuable time for evacuation or intervention in case of a fire incident.
Flame retardant additives work by interrupting the combustion process and limiting the flammability of the yarn. They can either act through physical mechanisms, such as forming a protective barrier that prevents oxygen from reaching the flame, or through chemical reactions that inhibit the formation of flammable gases or promote the formation of char, which acts as a barrier against further combustion.
When selecting flame retardant additive masterbatches for yarn extrusion, it is crucial to consider factors such as the desired level of flame retardancy, compatibility with the yarn polymer, and compliance with relevant safety standards and regulations. Additionally, it is important to assess the long-term stability and durability of the flame retardant properties to ensure that they will be effective throughout the lifespan of the yarn.
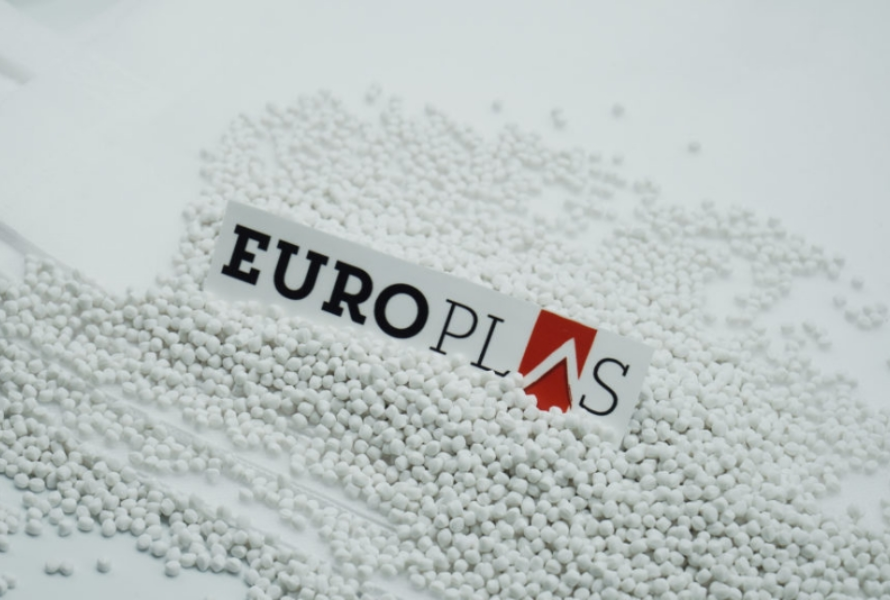
Incorporating flame retardant additives into yarn extrusion is critical to reducing the risk of fire and improving overall safety.
4. Conclusion
Selecting the right additive masterbatch for yarn extrusion is crucial for several reasons. It allows manufacturers to tailor the yarn's properties to meet specific requirements, such as antimicrobial properties, UV resistance, flame retardancy, or static control. This customization enables product differentiation, giving the yarn unique features and functionalities that stand out in the market.
When making decisions regarding additive masterbatch selection for yarn extrusion, it is crucial to gather information, consult with experts or suppliers, and evaluate the specific requirements of the application. By considering factors such as desired properties, compatibility, performance, and cost-effectiveness, manufacturers can make informed decisions that lead to optimized yarn production and enhanced product performance.
EuroPlas is a renowned provider of high-quality additive masterbatches for various industries. With a commitment to innovation, performance, and sustainability, EuroPlas offers a wide range of additive solutions designed to enhance the properties and performance:
- Clarifying additive
- Optical brightener additive
- Odor removing additive
- Desiccant
- Flame retardant
- Anti-fog additive
- Anti-aging additive
- Processing-aid additive
- Anti-static additive
- Anti-UV additive
- Anti-blocking additive
If you want more information about our products, please visit Search Plastic additive | EuroPlas - the world's No. 1 filler masterbatch manufacturer or contact us right now!