Plastic emerges as one of the world's most versatile and widely used materials, capable of assuming any shape, color, and size and finding applications across various industries. However, what sets plastics apart is their diversity; different plastic types possess unique properties, advantages, and disadvantages. Identifying and selecting the most appropriate plastic variant for your project can lead to cost savings, improved quality, and environmental protection. Understanding these distinctions is paramount to making informed choices and fostering sustainable practices.
1. What are the Different Types Plastic?
Plastics can be classified into seven main categories depending on their chemical structure and composition. Each class has a number and a symbol indicating the plastic type. These symbols are usually found on the bottom of plastic containers and products. Here are the most common types of plastic and their characters:
Seven Different Plastic Types
2. How to Identify Plastic Materials?
Several methods can help you identify the plastic material you need for your project. Some of these methods are:
- Appearance Identification: You can look at the color, transparency, thickness, and texture of the plastic material to get some clues about its type. For example, PET is usually straightforward, HDPE is generally opaque, PVC is typically white or gray, LDPE is usually thin and stretchy, PP is usually semi-transparent or coloured, PS is typically transparent or foamed, and other plastics can have various appearances depending on their additives.
- Density Identification: You can measure the density or specific gravity of the plastic material by weighing it in air and water. Water's density of 1 g/mL serves as the benchmark. Should the plastic sink in water, its density exceeds that of water; conversely, if it buoyantly floats, its density is less than that of water. For instance, PET displays a density of 1.38 g/mL, HDPE records a density of 0.95 g/mL, PVC displays a density of 1.4 g/mL, LDPE registers a density of 0.92 g/mL, PP maintains a density of 0.9 g/mL, PS demonstrates a density of 1.05 g/mL, and other plastics exhibit various thicknesses depending on their additives.
- Combustion Identification: You can burn a small piece of plastic in a safe and ventilated area and observe the flame's color, smell, and behavior. Different plastics have different combustion characteristics that can help you identify them. Each type of plastic exhibits its combustion characteristics: PET burns with a yellow flame akin to burning paper, HDPE engenders a yellow flame emitting a scent reminiscent of candle wax, PVC yields a green flame accompanied by the fragrance of chlorine, LDPE dances with a blue flame, and the aroma of candle wax, PP emanates a yellow flame with an oil-like scent, PS produces a yellow flame exuding a styrene odor, while other plastics showcase distinct combustion features based on their particular additives.
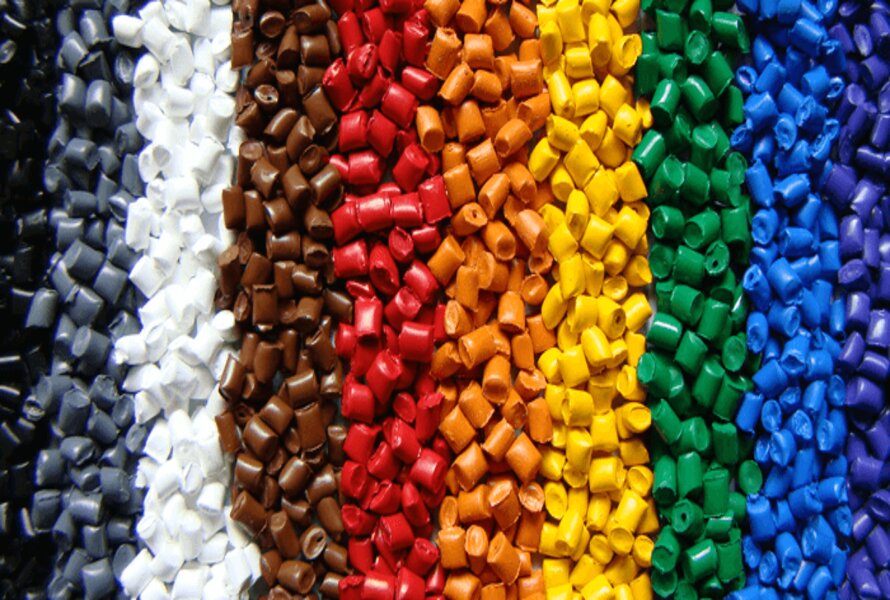
Identify different types plastic by color
3. Which Plastic is the Best for Your Project?
The selection of the appropriate plastic for a project remains to be determined due to the diverse advantages and disadvantages of different polymers in varying conditions. To make an informed decision, several essential factors must be considered. Cost, influenced by availability, type, quality, quantity, and price, necessitates thorough evaluation.
Strength, encompassing tensile, flexural, impact, compressive, and shock resistance, plays a critical role in choice. Flexibility, determined by elongation, modulus, elasticity, and stiffness, should align precisely with project needs. Durability, considering wear, abrasion, corrosion, weathering, aging, and degradation, is of utmost importance. Thermal, electrical, optical properties, and environmental impact should be carefully assessed for the most suitable plastic selection.
Which Plastic is the Best for Your Project?
4. Symbols of plastics
Plastics, being versatile synthetic materials, can be molded into various shapes for diverse purposes. Derived from polymers or monomers sourced from natural elements or fossil fuels like petroleum, plastics' properties and characteristics are influenced by their composition and the incorporation of additives and fillers. Two primary categories of plastics are thermoplastics, which can be melted and reshaped repeatedly, and thermosets, which remain rigid once cured. Symbols found on plastic products help identify their type, properties, recyclability, and safety, aiding consumers, manufacturers, recyclers, and regulators in their classification and usage.
Plastic recycling symbols
5. Meaning of symbols on plastic
Plastic item symbols possess diverse meanings based on shape, color, numerical value, lettering, or wording. Standard symbols and explanations include:
- Recycling symbol: This triangular emblem, formed by three arrows in a loop, indicates recyclable plastic or products made from recycled materials. A number may specify the plastic resin type, such as PET, HDPE, PVC, LDPE, PP, PS, or others.
- Resin identification code: Developed by SPI in 1988, this code aids recyclers in identifying plastic resins (1 to 7) used in products.
- Green dot: Used in Europe, it shows that the producer supports packaging waste recycling, not product recyclability.
- Mobius loop: Resembles the recycling symbol, signifying recyclable or recycled content products.
- Compostable symbol: Shows a seedling emerging from soil, indicating biodegradability and compostability.
- Tidyman symbol: Depicts proper disposal and discourages littering.
Flame symbol: Warns that the product is flammable and should be kept away from heat sources.
- Glass-and-fork symbol: Assures that the product is safe for food contact.
- Hourglass symbol: Indicates an expiration or best-before date.
Meaning of symbols on plastic
6. Symbols on the bottom of plastic bottles
The symbols on plastic bottles are symbols that help you know the type, properties, recyclability, and safety of the plastic bottle you are using. These symbols usually have the shape of a triangle with three arrows and a number or letter inside or under it. The numbers from 1 to 7 correspond to different types of plastics, each with its own advantages and disadvantages. The letters are usually the abbreviation of the type of plastic. You can refer to the following table to understand better:
Number
|
Letter
|
Type of plastic
|
Application
|
Recyclability
|
Safety
|
1
|
PETE
|
Polyethylene terephthalate
|
Bottles for water, soda, juice, cooking oil, liquid soap,…
|
Can be recycled into polyester fibers, fabrics, carpets,…
|
Should not be reused many times as it may release harmful substances for hormones
|
2
|
HDPE
|
High-density polyethylene
|
Bottles for milk, beverages, water containers, plastic bags, pipes,…
|
Can be recycled into new bottles, trash cans, toys,…
|
Safe and durable, does not release harmful substances
|
3
|
PVC
|
Polyvinyl chloride
|
Food wrap film, water pipes, computer cables, toys,…
|
Difficult to recycle and pollutes the environment
|
Very toxic as it contains phthalates and bisphenol A that harm hormones and reproduction
|
4
|
LDPE
|
Low-density polyethylene
|
Plastic bags, food bags, shrink film, spray bottles,…
|
Can be recycled into new bags, trash cans,…
|
Safe and does not release harmful substances
|
5
|
PP
|
Polypropylene
|
Food containers, plastic cups, spray bottles, medicine bottles,…
|
Can be recycled into new bottles, trash cans,…
|
Safe and does not release harmful substances
|
7. Introduction EuroPlas Compounds
If you are seeking top-notch plastic materials that are both cost-effective and of superior quality for your project, look no further than EuroPlas – the world's leading filler masterbatch manufacturer. EuroPlas boasts an extensive range of products engineered to optimize plastic production and elevate your competitive edge. Here is a glimpse of EuroPlas' impressive product line and its diverse applications:
- Filler masterbatch: A cost-efficient solution that substitutes a portion of virgin resin with filler materials like calcium carbonate or talc. This not only reduces production costs but also enhances plastic products' properties and performance, including stiffness, heat resistance, opacity, and printability. Filler masterbatch finds its application in blowing films, injection molding, extrusion, and thermoforming.
- Bio filler: An eco-friendly option that renders plastic products biodegradable within a year. Comprising natural starch and biodegradable additives, bio filler can be mixed with conventional or bioplastic resins, making it ideal for food packaging, disposable tableware, and agricultural films.
- Color masterbatch: Elevating the aesthetics of plastic products, color masterbatch offers exact and consistent colors. It contains high-quality pigments and additives that can be blended with various resins, making it suitable for toys, household appliances, and cosmetics.
- Plastic additives: Enhancing production efficiency and functionality of plastic products through property and behavior modifications, plastic additives encompass a wide range of agents, such as slip, anti-block, anti-static, anti-oxidants, and UV stabilizers. These additives are widely used in applications like films, pipes, and cables.
- Engineering plastic compound: Delivering high-performance and functionality, engineering plastic compounds are all-in-one solutions. They combine engineering resins and various additives to enhance mechanical, thermal, electrical, optical, and chemical properties of plastic products. These compounds are commonly employed in automotive parts, electronic components, and medical devices.
With over 15 years of experience and expertise, EuroPlas has been exporting these innovative solutions to thousands of customers in more than 85 countries. Utilizing unique natural resources and cutting-edge technology, EuroPlas crafts tailor-made products to cater to diverse industries and applications. For more information on EuroPlas and its exceptional product offerings, visit our website or contact us directly. For additional insights and plastics-related tips, consider perusing their blog.
EuroPlas is the world's leading manufacturer