Flame retardant plastic additives were born to meet the diverse production and use conditions of plastic materials in many different fields. They are not only the main factor in minimizing flammable agents, but are also resistant to UC rays, do not create smoke and do not affect the mechanical properties of all materials. Therefore, plastic materials combined with fire-retardant plastic additives are capable of being applied in heavy fields such as: Electronic equipment, Aerospace, and Military. In the article, EuroPlas will help you distinguish the 5 most common types of fire retardant additives, specifically: Halogen, Phosphorus, Nitrogen fire retardant additives and inorganic fire retardant additives. Refer now!
Read more: What are plastic additives? 8 most common plastic additives in plastic industry
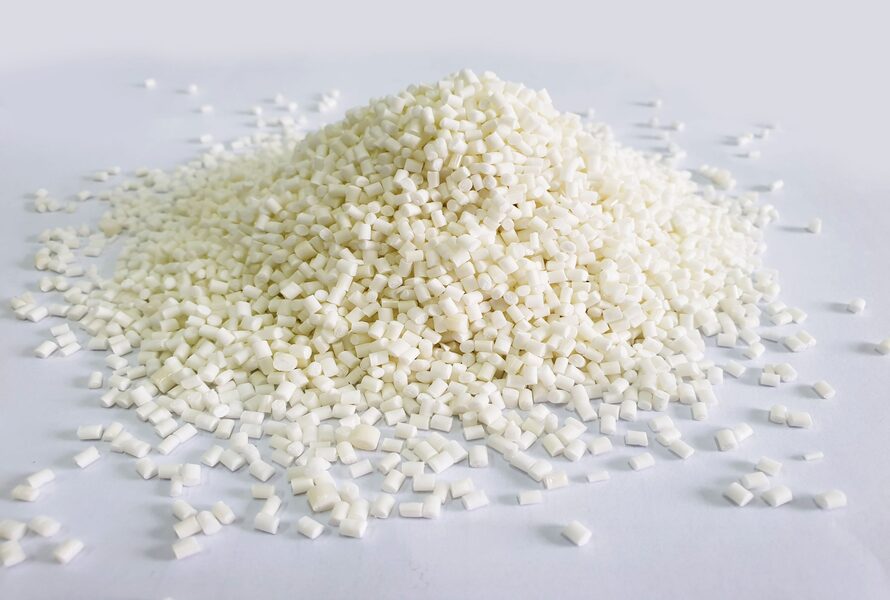
1. Halogen flame retardant plastic additives
First, plastic additives are produced with Halogen flame retardants. The compound consists of two main components: Bromine or Chlorine. Halogen is the most popular fire retardant today and is used in many fire centers around the world.
The main characteristic of Halogen flame retardants is their direct impact on the ability to maintain flames and inhibit their spread into the environment in the shortest time. Strong acids such as HCL or HBr in gas form are the main participants during that process. Some popular Halogen-based flame retardants include: Decabromodiphenyl oxide (DECA), Tetrabromobisphenol A (TBBA), Hexabromocyclododecane (HBCD), TBBA-bis-(2,3-dibromopropyl ether)
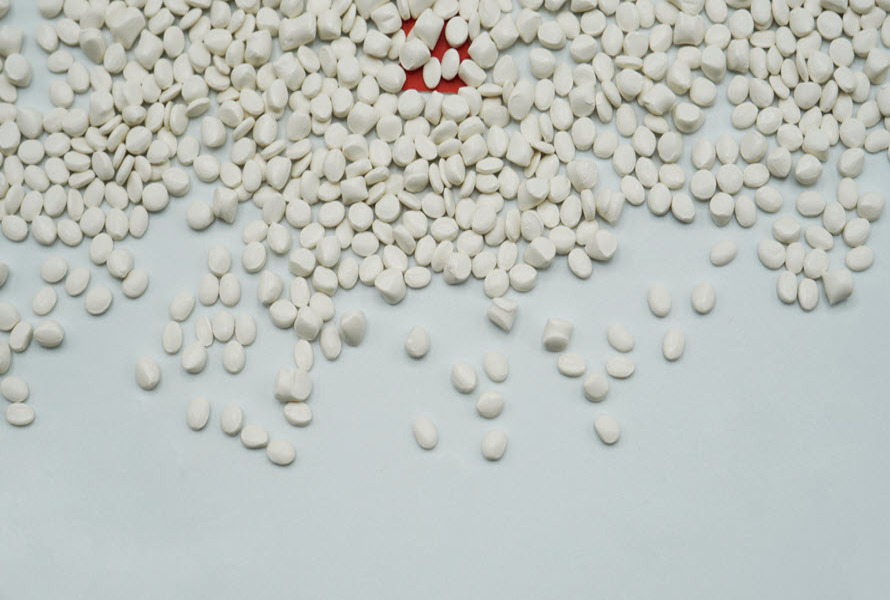
In general, Halogen radicals will be released when materials or products are exposed to high temperatures to disrupt and inhibit the igniting agents of the surrounding environment. Because of this, Halogen flame retardant plastic additives are commonly used in the textile, electronics and aviation industries.
Besides, there are also many studies discussing the health safety issues of Halogen compounds in daily life. That is the reason why plastic additive manufacturers have created many more Halogen-free additives and replaced them with Coupling Agents, typically: Phosphorous, Nitrogen flame retardant additives and other additives. Inorganic. Refer to the next section to distinguish the differences between these types of fireproof plastic additives!
2. Phosphorus flame retardant plastic additive
The main ingredients of phosphorus flame retardant plastic additives include 5 chemical compounds: ammonium polyphosphate (APP), red phosphorus, organic phosphate and phosphonate, choroaliphatic. The basic feature of this additive is to slow down the growth and spread of fire for a certain period of time.
In particular, phosphorus flame retardant plastic additives not only possess the flame retardant mechanism of Halogen compounds but also directly impact the fire or excessively high temperature environment through the gas phase and the mechanism of metal hydrate. with the ability to condense vapor to extinguish flames or create a crystal layer to protect the base material.
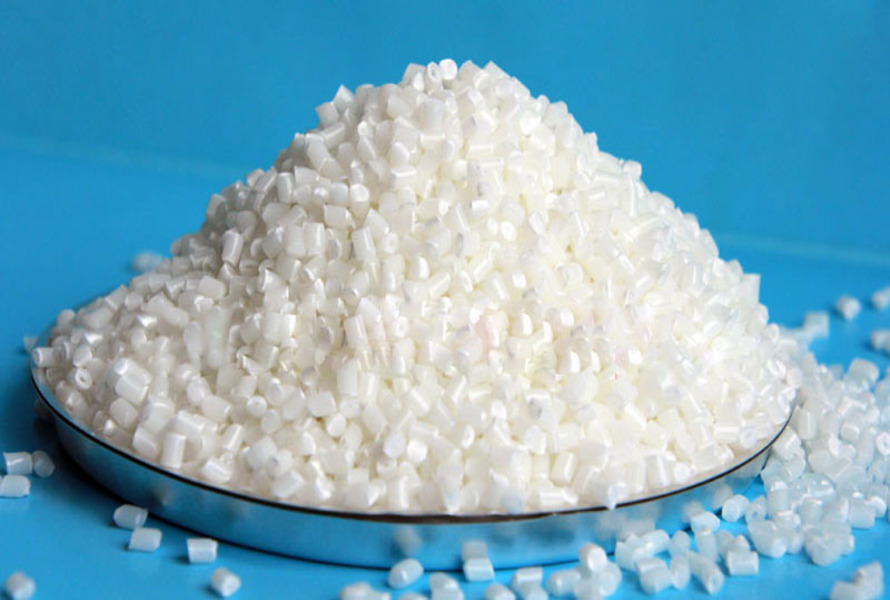
Accounting for the majority of the volume of phosphorus flame retardant plastic additives is Phosphate Esters. Besides, resorcinol diphosphate (RDP) and bisphenol A diphosphate (BDP) also contribute equally importantly. Phosphorus flame retardant plastic additive is combined with plastics such as PPO, PVC, ABS / PC.
Like Halogen flame retardants, Phosphorus flame retardants are also used in everyday plastic products and even in heavy mechanical industries that are often exposed to high temperature environments. In addition, they are also used for products that have large contact surfaces with air and are flammable such as: Rubber products, furniture, polyurethane foam materials (mattresses).
3. Nitrogen flame retardant additive
Currently, Nitrogen fire retardant compounds are combined with phosphorus to provide the most optimal performance. The operating principle of Nitrogen fire retardant additive is to form a barrier between the surface of the material and outside oxygen as well as to prevent a large amount of heat from the surrounding environment.
Similarly, when this additive is exposed to fire or high temperatures, it will produce a direct amount of NO2 gas and contribute to pushing Oxygen away from the surface of the object. In particular, fire-retardant plastic additives will work and protect materials from many directions to minimize the access and development of fire.
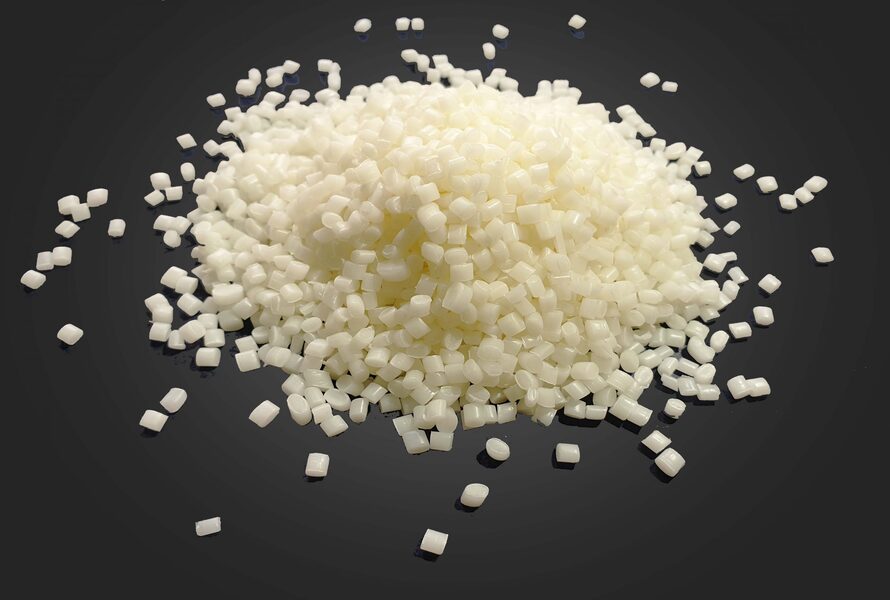
4. Inorganic flame retardant plastic additives
Mineral-based plastic additives are also known as typical inorganic compounds such as Hydroxide and Magnesium Hydroxide. These are inorganic substances that do not affect the health of consumers even when exposed to high temperatures. On the contrary, they have very well promoted the ability of the material to prevent flammable particles.
When exposed to an environment with gradually increasing high temperatures, inorganic flame retardant plastic additives begin to release water vapor and carbon dioxide molecules to contribute to the cooling and heat reduction of the material surface, so the material It will be very difficult to start a fire.
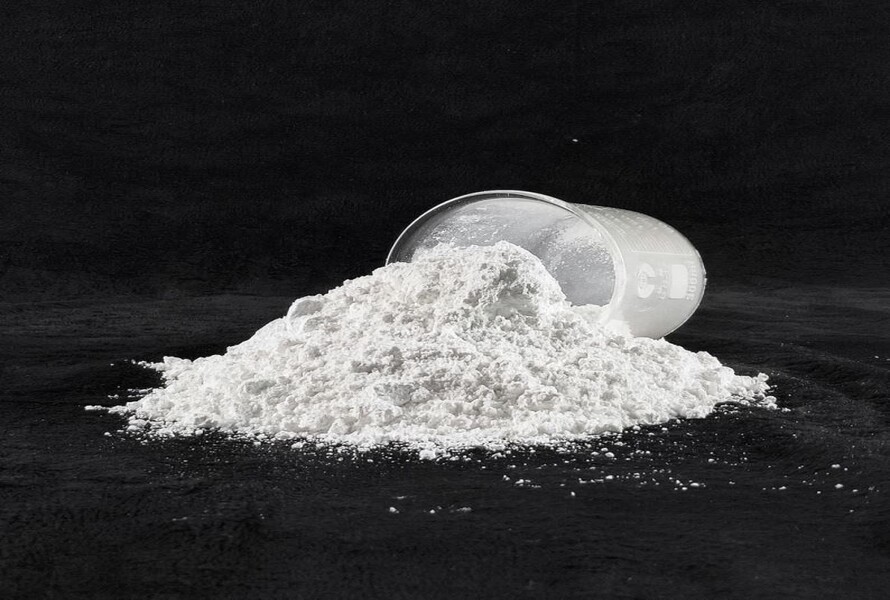
Flame retardant plastic additives are applied in fields that place consumer health safety at the highest level such as: children's toys, mother and baby products, and food packaging.Currently, besides inorganic fire retardants, organic fire retardant additives produced from natural ingredients such as plants and animals are also commonly used in many industries.
In general, flame retardants must ensure two main factors: They not only protect materials from fires and high heat sources, but must also be guaranteed not to produce any chemical compounds that have negative effects. department on consumer health. Plastic production technology is also very developed, which means the popularity and upgrading of plastic additives will be significantly improved. They are applied in a variety of fields and are compatible with most popular plastics on the market.
5. Application of flame retardant plastic additives
With their diversity and important characteristics, flame retardant plastic additives are applied in many different fields. Let's refer to EuroPlas now:
-
Electronic industry: With the outstanding development of technology, corporations have promoted investment in circuit board products and electronic components. These are also products that are often exposed to environments with gradually increasing temperatures over long periods of time. Therefore, flame retardant plastic additives will be incorporated in the production process, for example in computer components or electric vehicle batteries. They will keep the surface and internal elements of the material at a stable temperature and will not release heat to the environment.
-
Construction field: This is also a field that strictly requires safety and fire prevention factors. All electrical circuit systems, water and household appliances must ensure the highest insulation standards to minimize the risk of fire. Therefore, fireproof plastic additives are commonly used in this field.
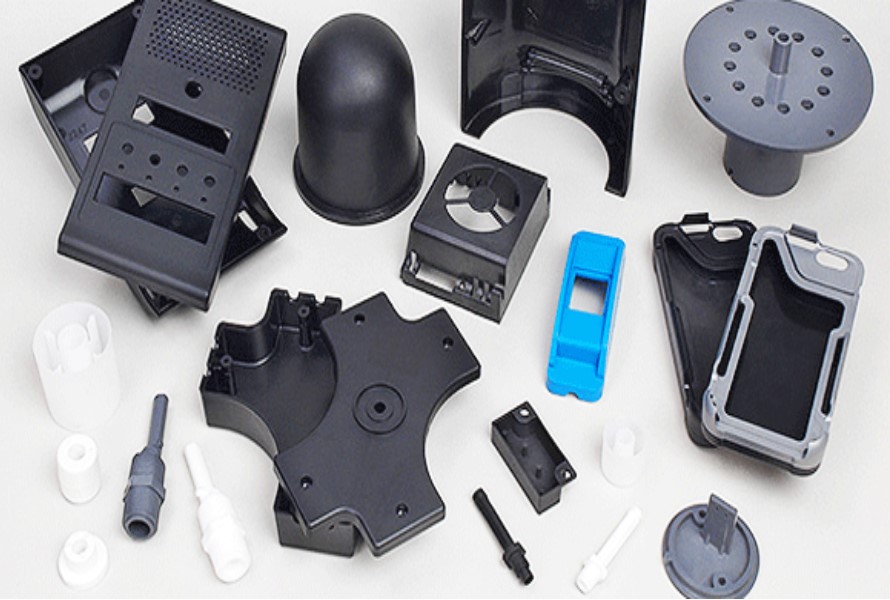
-
Aerospace: This is the field of the future and is being researched by countries around the world. Not only that, the heat resistance level of products in this field is very high, up to thousands of degrees Celsius. Without the participation of fire-retardant plastic additives, it would be almost impossible for the production process to take place. In particular, this is the field that needs to use the highest amount of plastic additives with high frequency and large enough surface thickness to ensure heat and fire insulation standards.
-
Household appliances: Plastic products used in daily life also need to have good insulation in all cases. Inorganic plastic additives are often used in this field such as children's toys because they do not emit chemicals that affect consumers' health.
-
Packaging production field: Packaging is widely used in many fields such as F&B, Hospitality. During storage and transportation, flame retardant plastic additives will help the packaging limit exposure to flammable factors, avoid UV rays and ensure food safety. Organic and inorganic plastic additives will be used a lot in this field because they are produced from natural fuels and ensure the health of consumers and do not affect food quality.
-
Transportation and supply chain: Flame retardant plastic additives are also used to produce auto parts such as engines, radiator systems, shock absorbers, etc. Most vehicles travel long distances and The engine will inevitably overheat. Therefore, fireproof plastic additives will be an indispensable component in the production process.
6. Introducing fireproof plastic additives at EuroPlas
EuroPlas provides many types of plastic additives such as: deodorizing additives, desiccant additives, fire retardant additives, anti-fog additives, anti-aging additives, processing aids, anti-static additives, Anti-UV additives and additives to increase clarity and brightness. Among them, fireproof plastic additives are also one of the outstanding products.
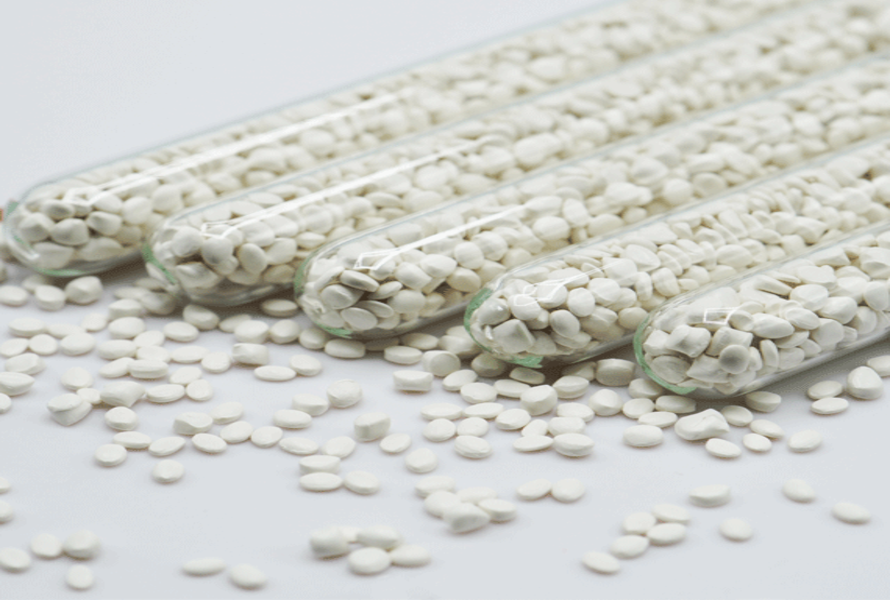
EuroPlas brand fire retardant additives have outstanding properties such as high impact resistance, good thermal and dimensional stability, and good scratch resistance. Our products meet UL 94 standards: V0, V1 and V2 to ensure quality during processing and when using the product. Below are some outstanding features of fire retardant additives:
-
Limit the spread of fire through the mechanism operating on the plastic surface
-
Disperses well with base resin
-
Does not reduce product properties.
-
Affordable price.
-
Does not cause machine corrosion.
Fireproof additive products at EuroPlas also set the following 3 standard specifications:
-
Storage: The product is stored in cool, dry conditions
-
Transportation: By road or by sea according to agreement between both parties
-
Recommended usage rate: 5-7%.
The above article has introduced you to the detailed characteristics of 4 types of fireproof plastic additives. Please continue to follow EuroPlas to update the latest news about bioplastic material product lines!