In plastic manufacturing, colour is crucial for brand identity, product functionality, and quality assurance. Colour masterbatch plays a vital role in achieving consistent and vibrant colours in plastic products. But how do manufacturers ensure each batch delivers uniform colour, dispersion, and performance?
This article explores the detailed processes and methods used to test colour masterbatch before it reaches your production line.
1. What is Colour Masterbatch?
Colour masterbatch is a concentrated mixture of pigments or dyes, and special additives encapsulated in a carrier resin. It's used to add colour to plastic during the molding or extrusion process, offering better dispersion, easier handling, and improved colour consistency compared to direct pigment dosing.
Colour masterbatch is widely used across various industries, including packaging, automotive, consumer goods, medical devices, and textiles.
Read more: What is color masterbatch and how was masterbatch produced?
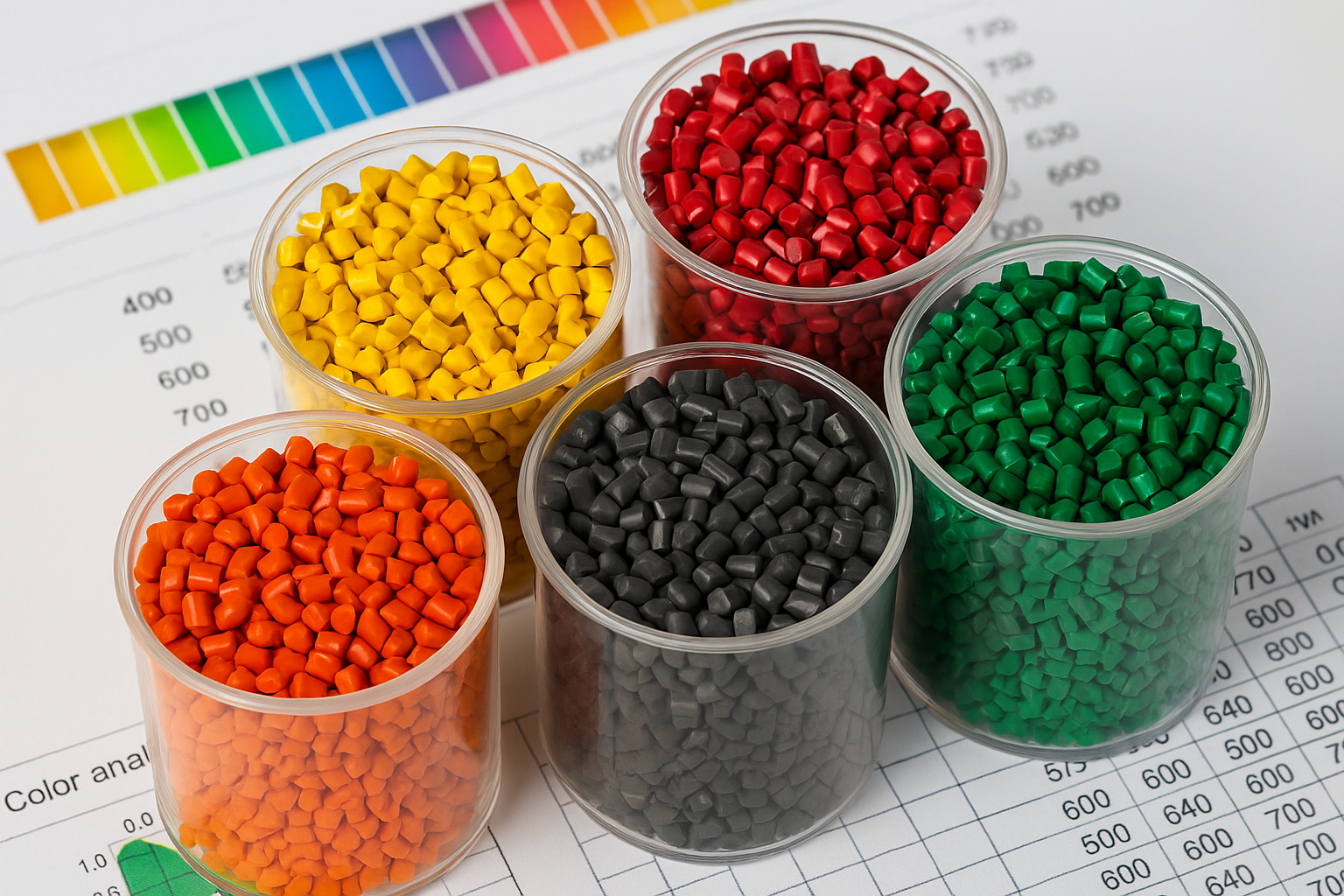
Colour masterbatch is a concentrated mixture of pigments or dyes, and special additives encapsulated in a carrier resin.
2. Why Testing Colour Masterbatch Matters
Even slight inconsistencies in colour can lead to product rejection, increased waste, or damage to brand perception. Testing ensures:
- Consistency in colour shade across batches
- Accurate pigment concentration
- Good dispersion of colour in the base resin
- Compliance with industry standards (RoHS, FDA, REACH, etc.)
- Resistance to heat, light, and environmental conditions
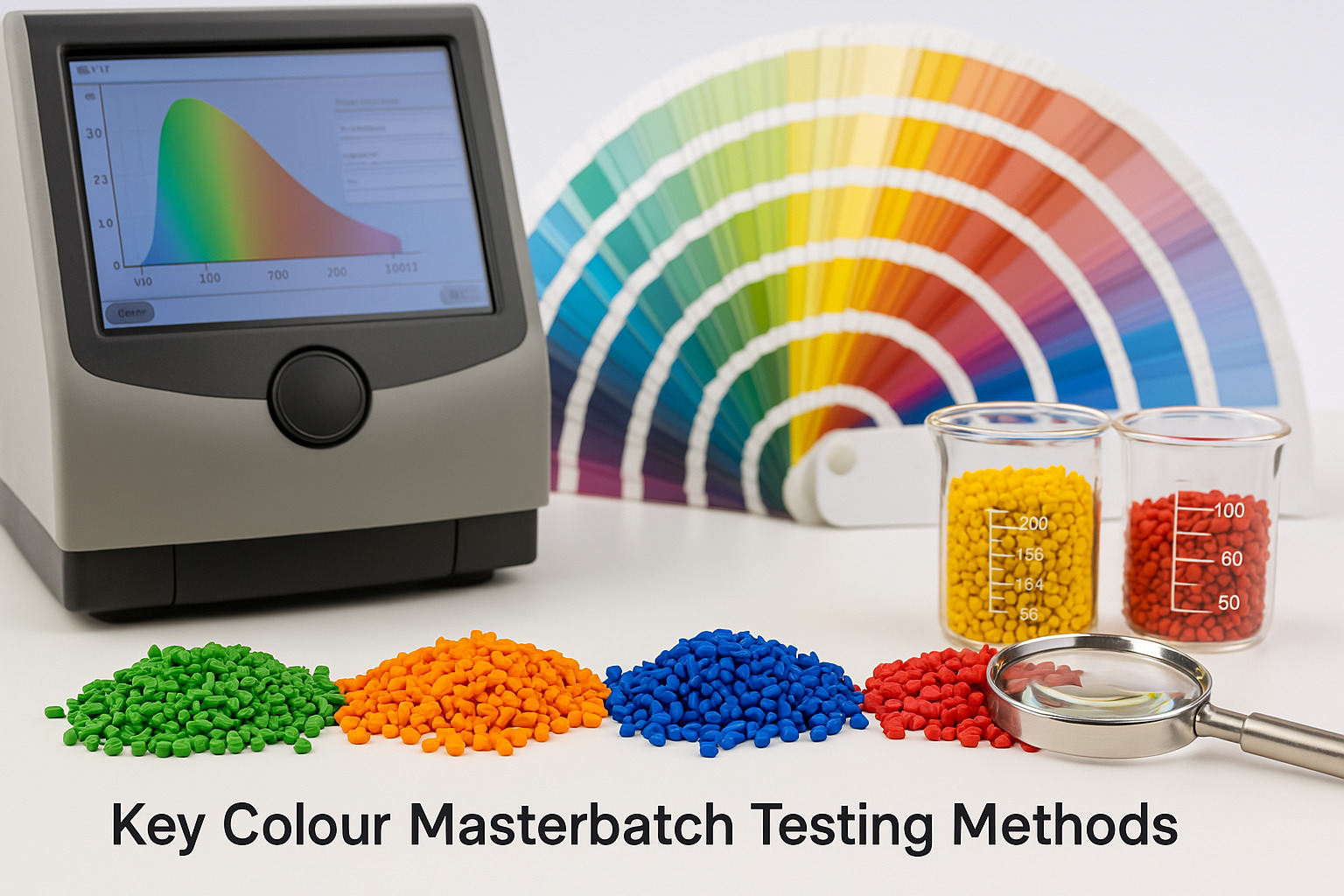
Even slight inconsistencies in colour can lead to product rejection, increased waste, or damage to brand perception.
3. Key Colour Masterbatch Testing Methods
3.1. Colour Matching & Spectrophotometry
Spectrophotometers measure the reflected light from a coloured sample and compare it to a target standard, typically in the CIELAB (Lab*) colour space.
Key parameters measured:
- Delta E (ΔE): Colour difference between the masterbatch sample and the standard
- L* (lightness), a* (red-green), b* (yellow-blue)
- Tight ΔE values (typically under 1.0 or 2.0, depending on the application) indicate good colour matching.
3.2. Dispersion Testing
Dispersion refers to how uniformly pigments are distributed in the polymer matrix. Poor dispersion leads to streaks, inconsistent colour, and weaker mechanical properties.
Common tests include:
- Microscopic analysis (optical or electron microscope)
- Melt flow dispersion on film or plaque samples
Masterbatch should display a uniform appearance with no visible specks or agglomerates.
3.3. Melt Flow Index (MFI) Testing
Melt Flow Index, commonly abbreviated as MI, is a measure of the melt flow of plastic, also known as Plastic Flow Index (Melt Flow Rate-MFR). This index is primarily used to evaluate the flow characteristics of plastic materials under specific temperature and pressure conditions.
Measured in: grams per 10 minutes (g/10 min) under specified load and temperature
Too high or too low MFI may indicate processing issues or incompatible carrier resin.
Read more: Significance of Melt Flow Rate - Melt Flow Index in plastics processing
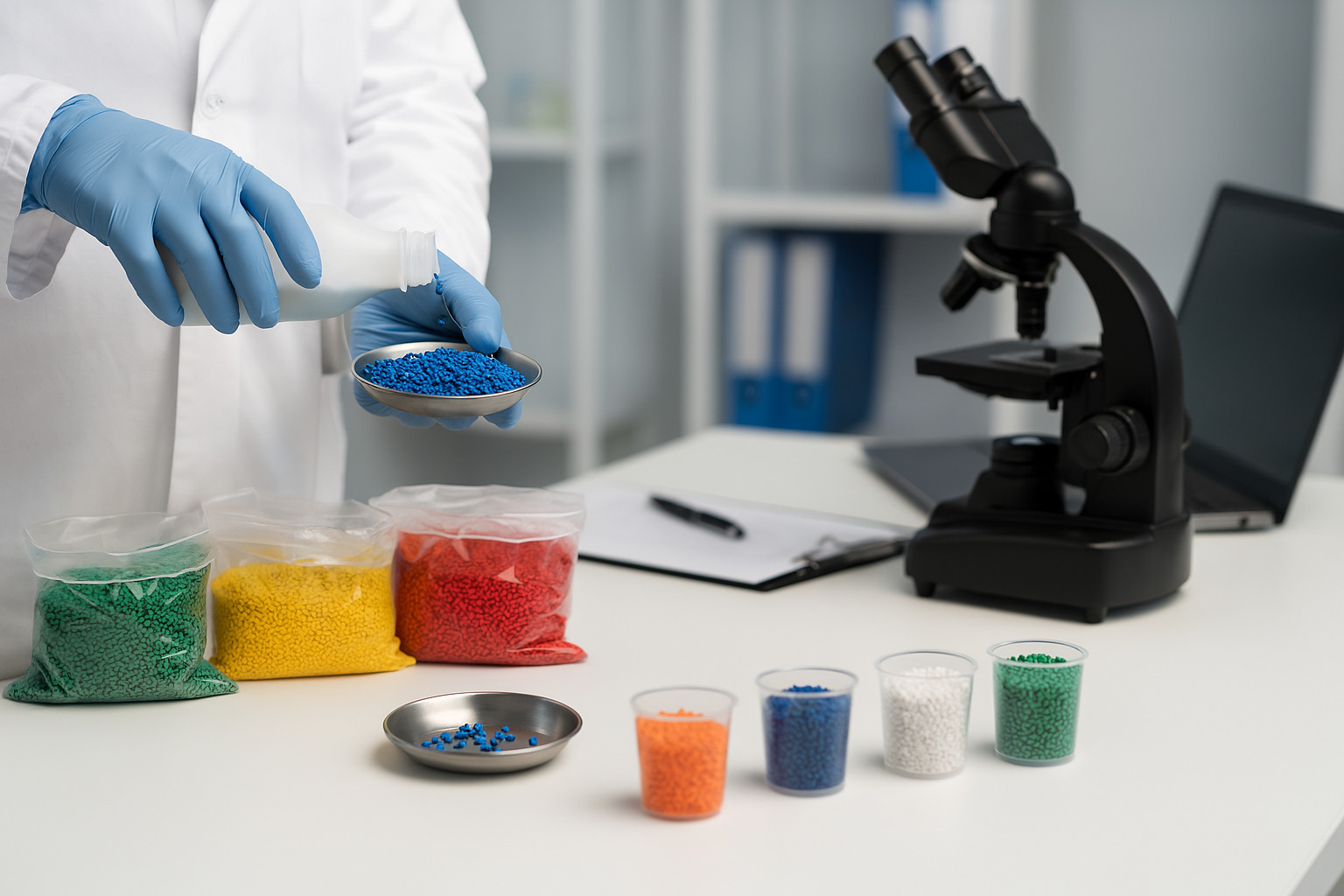
3.4. Heat Stability Testing
Pigments and dyes must resist degradation under heat during processing (usually between 180°C to 300°C).
Method:
- Expose the masterbatch to elevated temperatures
- Measure colour shift (ΔE) post-exposure
3.5. Light Fastness Testing
Exposure to UV or sunlight can cause pigments to fade. Light fastness testing ensures long-term performance in outdoor or exposed environments.
Standard methods:
- Xenon arc testing (ISO 4892-2)
- Blue Wool Scale (1 to 8, with 8 being best)
3.6. Weathering Tests
These simulate outdoor conditions—UV exposure, humidity, and temperature changes—to predict real-world durability.
Standards: ISO 4892-2, ASTM G155
3.7. Migration and Extraction Tests
For food contact or medical applications, pigments must not leach or migrate from the final product.
Tests performed under:
- EU Regulation 10/2011
- FDA 21 CFR compliance
3.8. Physical Property Testing
Sometimes, the masterbatch affects the mechanical properties of the final plastic. Thus, tensile strength, elongation, and impact resistance may be checked.
Testing ensures that the addition of colourant doesn’t compromise structural performance.
4. Typical Quality Control Workflow in Masterbatch Production
- Raw Material Testing: Pigments, additives, and carrier resins are tested before mixing.
- Lab-scale Sample Production: Pilot samples are produced for initial evaluation.
- Masterbatch Production: Full-scale production under controlled conditions.
- Batch Testing: Apply the above-mentioned tests for each production lot.
- Customer Simulation: In some cases, customer-specific tests are performed using their resin or processing method.
5. Who Performs the Testing?
Testing can be done in-house by the masterbatch manufacturer or outsourced to accredited third-party labs. Many leading colour masterbatch manufacturers maintain their own R&D and quality labs equipped with:
- Spectrophotometers
- MFI testers
- Weathering chambers
- Lab extruders and injection molders
6. What Customers Should Ask Their Supplier
Before purchasing colour masterbatch, customers should ensure their supplier provides:
- Certificate of Analysis (COA) with test results
- Colour matching reports (ΔE values)
- Regulatory compliance documents (RoHS, REACH, FDA, etc.)
- Product samples for verification
- Technical support for processing challenges
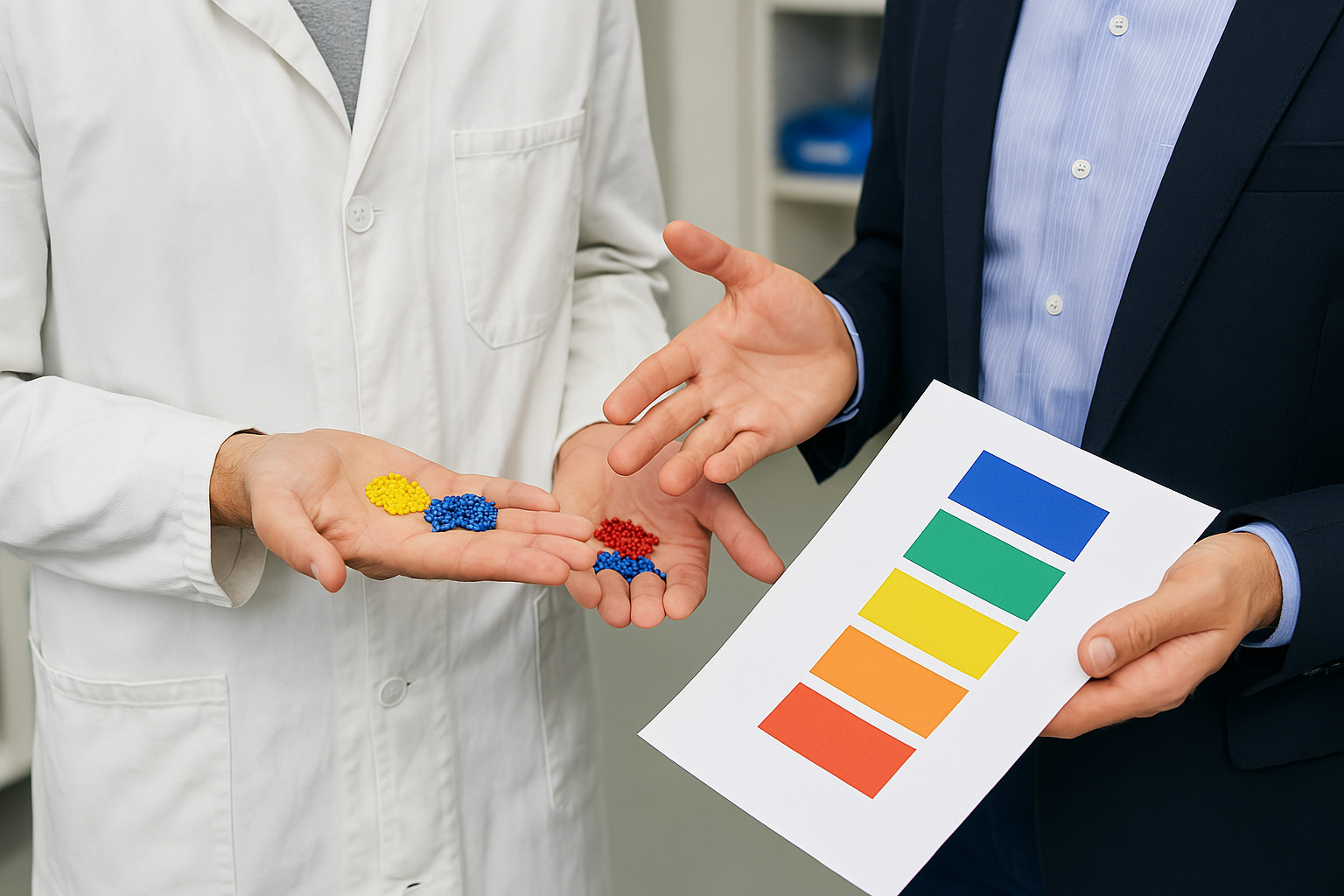
7. Conclusion
The testing of colour masterbatch is a critical step to guarantee colour consistency, product safety, and long-term performance. From spectrophotometry to heat stability and migration testing, each method provides valuable insights into how the masterbatch will perform in your specific application.
Whether you're in packaging, automotive, medical, or consumer goods, understanding how colour masterbatch is tested helps you choose reliable suppliers and produce high-quality plastic products that meet both functional and aesthetic expectations.
8. About EuroPlas
EuroPlas is one of the world’s leading manufacturers of filler and colour masterbatch, with products distributed in over 95 countries. Backed by a strong R&D foundation, EuroPlas delivers tailor-made solutions for plastics manufacturers worldwide.
Its colour masterbatch line is formulated for excellent colour dispersion, thermal stability, and compliance with international standards. Customers benefit from vibrant colour consistency, reduced processing costs, and enhanced product performance.
As a trusted color masterbatch supplier, EuroPlas is providing different color masterbatches such as white, black, red, gray, purple, blue, brown, orange, and yellow. We also provide specialized color masterbatch products with diverse effects according to the requirements of the finished product.
If you wish to learn more about the product, please feel free to click here.