The plastic industry has seen rapid growth in recent years, with the use of plastic products becoming widespread in various industries, from consumer goods to medical equipment. To ensure that plastic products meet the required quality standards, it is essential to implement quality control measures in the production process. This includes following industry-specific standards that provide guidelines for testing and evaluating the performance, quality, and safety of plastic products. In this blog, we will focus on some of the common standards used in the plastic industry for quality control.
Related:
- General arrangements of FCM Food Contact Material
- How will the Vietnamese masterbatch industry change after the EVFTA is signed?
1. Common standards for plastics you should know
ISO
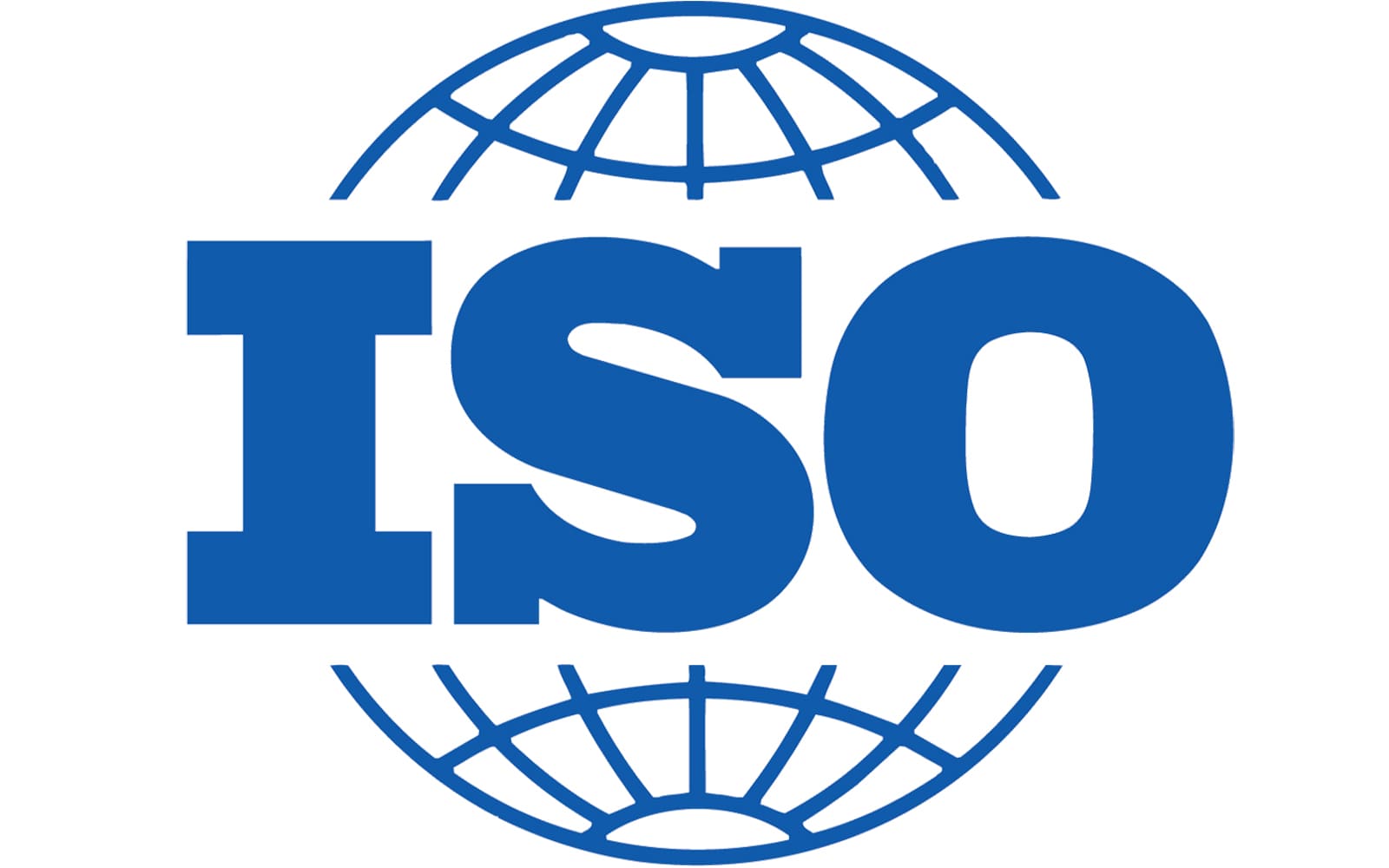
ISO (International Organization for Standardization) is an independent, non-governmental international organization that develops and publishes standards for various industries, including plastics. ISO works to ensure that products are safe, reliable, and of good quality. Some of the most important ISO standards for plastics include:
- ISO 1183-1: Specifies the requirements for determining the basic physical and mechanical properties of plastics, such as density, tensile strength, and impact resistance.
- ISO 12215-1: Specifies the requirements for the design and construction of plastic boats.
- ISO 15223-1: Defines the requirements for the labeling of medical devices made from plastic materials, including information about the device's intended use, manufacturer, and any relevant warnings or precautions.
- ISO 16072: Defines the requirements for measuring the carbon footprint of plastic products, including the calculation of greenhouse gas emissions from the production and disposal of the product.
Among the various ISO standards for plastics, these are only a handful. The industry can guarantee that plastic goods are produced to a high degree of quality, safety, and sustainability, and that they suit the demands of customers and the environment, by following these criteria.
ASTM
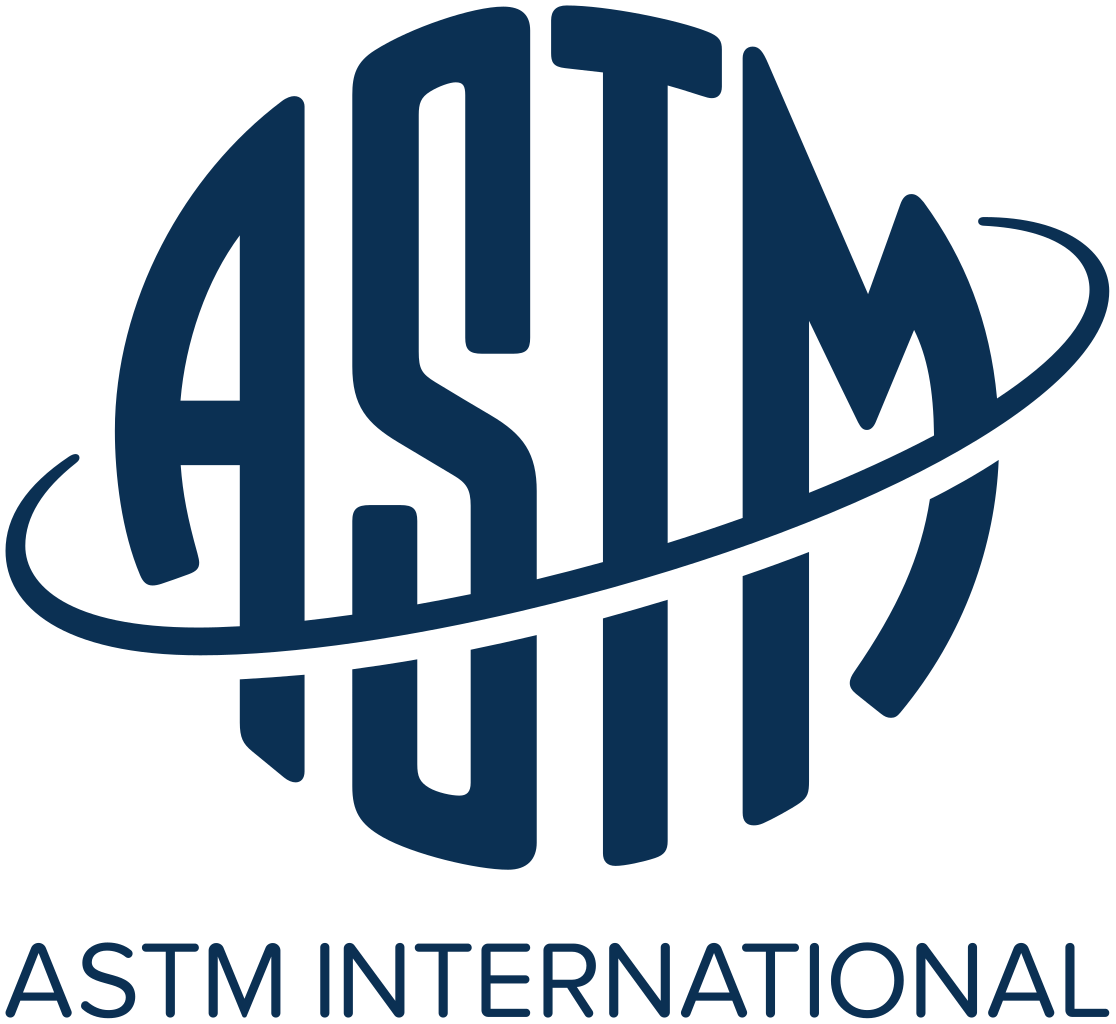
ASTM International, formerly known as American Society for Testing and Materials, is a globally recognized organization that develops and publishes standards for a variety of industries, including plastics. ASTM International works to promote knowledge and improve the quality of products and services in many fields. They establishe and publishes standards for a wide range of industries, including plastics.
In the plastics industry, ASTM has established several critical standards that are frequently used. Some of the most significant ASTM standards for plastics are:
- ASTM D256: Outlines the testing requirements for determining the impact resistance of plastics, including procedures for calculating the energy needed to break a sample of the material.
- ASTM D792: Specifies the methods for measuring the density and specific gravity of plastics.
- ASTM D638: Sets the standards for testing the tensile strength and elongation of plastics, including the procedures for calculating the force required to break a sample of the material.
- ASTM D2240: Defines the testing procedures for measuring the hardness of plastics, including methods for determining the indentation depth of a sample under a specified load.
- ASTM D882: Describes the testing requirements for evaluating the tear strength of plastics, including the procedures for calculating the force needed to initiate and propagate a tear in a sample of the material.
By following these standards, the plastics sector can assure that its products are continuously produced with high quality and safety, satisfying consumers' demands and expectations. Furthermore, ASTM standards serve as a platform for determining regulatory requirements and assessing the performance of plastics in a variety of applications.
JIS
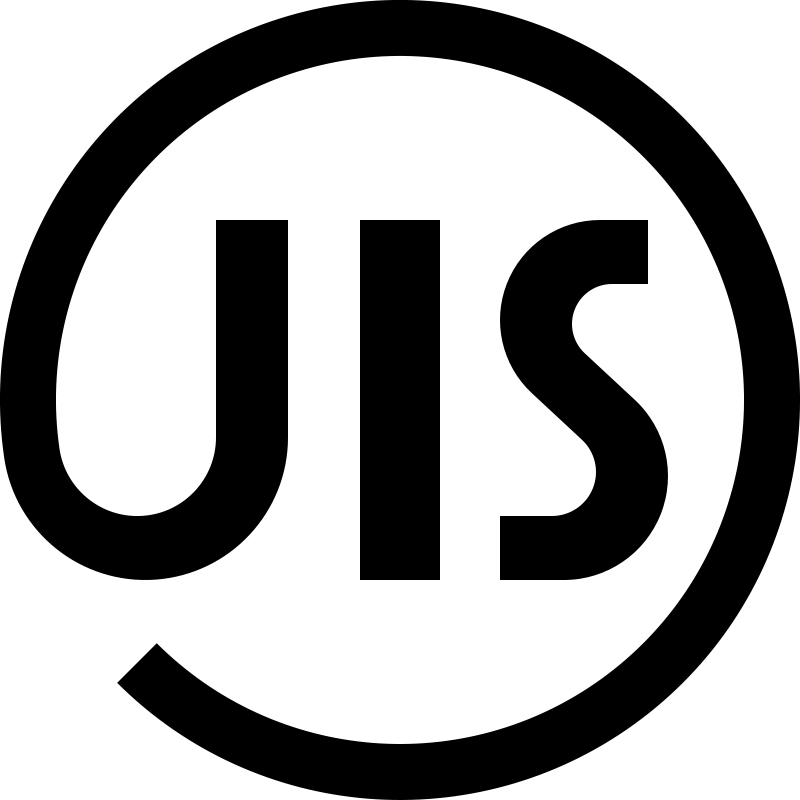
JIS (Japanese Industrial Standards) is a collection of standards that are developed and maintained by the Japanese Industrial Standards Committee (JISC) to ensure the quality and safety of products and services in Japan. JIS covers a wide range of industries, including plastics.
In the field of plastics, JIS has established several critical standards that are widely used in Japan and internationally. Some of the most important JIS standards for plastics include:
- JIS K 7100: Specifies the requirements for the labeling of plastic products, including information about the manufacturer, product type, and any relevant warnings or precautions.
- JIS K 6724: Defines the requirements for the testing of the impact resistance of plastics, including testing procedures for determining the amount of energy required to break a sample of the material.
- JIS K 6741: Specifies the requirements for testing the tensile strength and elongation of plastics, including the procedures for determining the amount of force required to break a sample of the material.
- JIS K 6765: Defines the procedures for measuring the hardness of plastics, including the test methods for determining the indentation depth of a sample under a specified load.
- JIS K 6854: Specifies the requirements for testing the heat resistance of plastics, including the procedures for determining the temperature at which a sample of the material begins to degrade.
The plastics sector can make sure that its products are consistently made to high standards of quality and safety and that they satisfy the needs and expectations of customers in Japan and outside by adhering to these and other JIS standards. JIS standards serve as a foundation for legal specifications as well as for assessing how well polymers function in various applications.
SAE
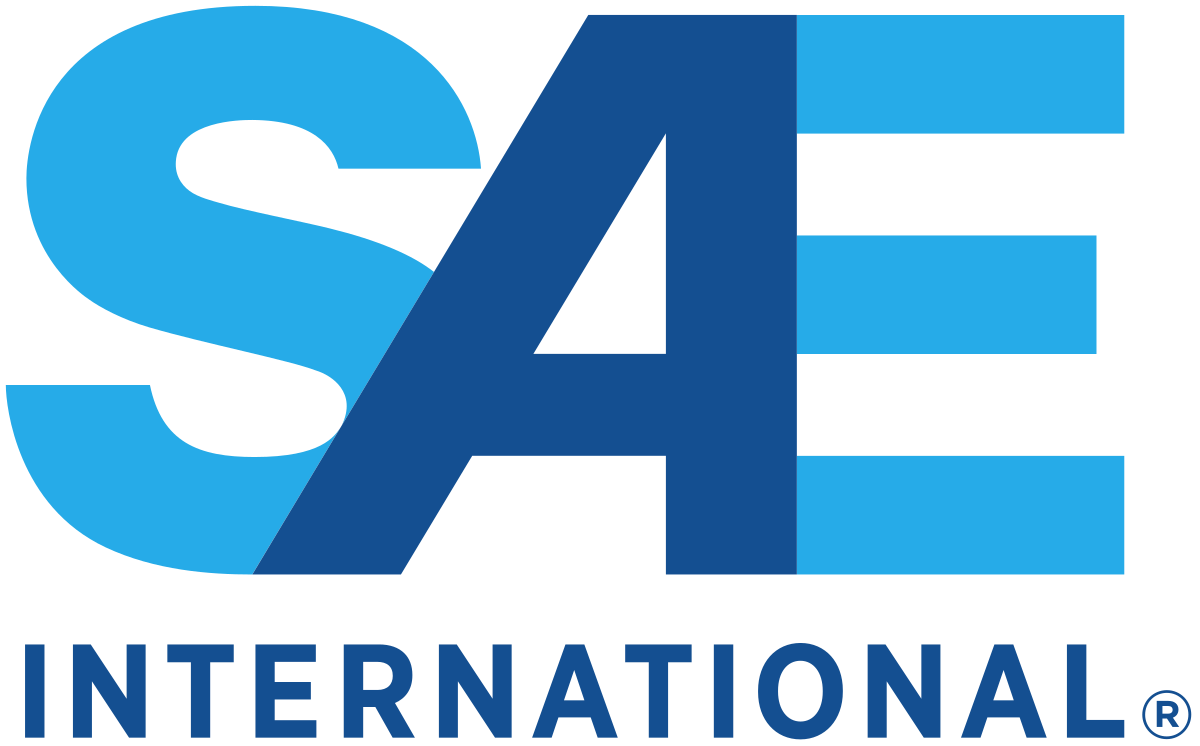
SAE International, formerly known as the Society of Automotive Engineers, is a professional organization that sets industry standards for various engineering fields, including plastics. SAE is dedicated to advancing mobility engineering and promoting the exchange of technical knowledge among its members and the wider engineering community.
In the field of plastics, SAE has established a number of standards that are widely used in the automotive and related industries. Some of the most significant SAE standards for plastics include:
- SAE J1703: Specifies the requirements for testing the impact resistance of plastic fuel tanks, including testing procedures for determining the amount of energy required to break a sample of the material.
- SAE J1704: Defines the procedures for testing the permeability of plastic fuel tanks, including the methods for determining the rate at which fuel vapor can penetrate the material.
- SAE J2412: Specifies the requirements for testing the flammability of plastics, including the procedures for determining the ease with which a sample of the material can be ignited and the rate at which it burns.
- SAE J2530: Defines the requirements for testing the durability of plastic parts in automotive interiors, including the procedures for determining the resistance of the material to wear, fading, and other types of degradation.
By adhering to these and other SAE standards, the automotive and associated industries can make sure that their plastic products fulfill the essential quality and safety criteria in a variety of applications. Legal specifications and assessments of plastic’s performance in certain applications, including gasoline tanks and automobile interiors, are both based on SAE standards.
2. Cosmetic inspection standard for plastics
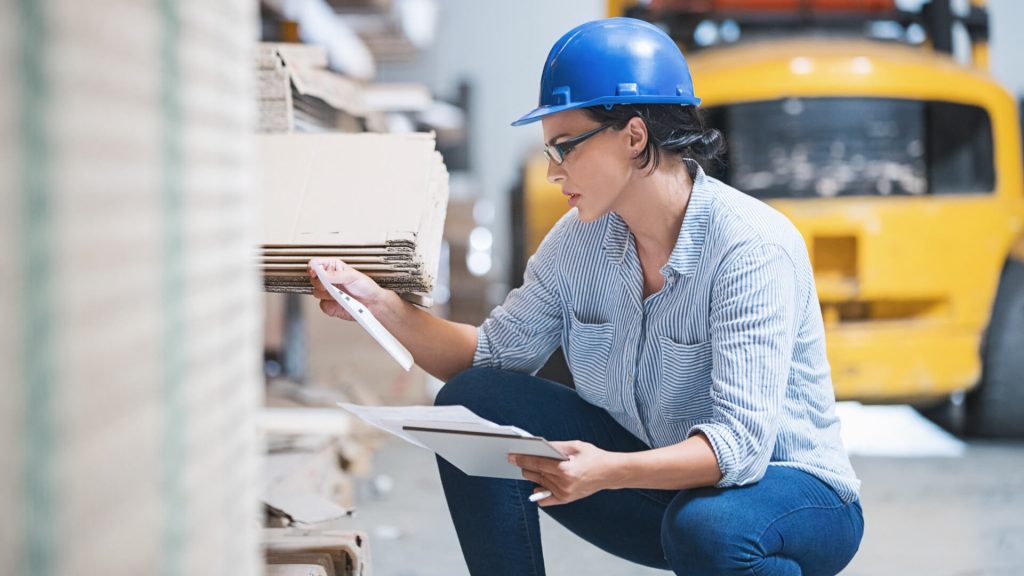
Cosmetic inspection is a critical aspect of the quality control process for plastic products. Itensures that the products meet the desired aesthetic and visual quality requirements. A well-executed cosmetic inspection can help to enhance the reputation and brand image of the manufacturer or supplier, and increase customer satisfaction. Moreover, it can help to reduce the risk of product returns and warranty claims, as well as minimize the cost and time associated with reworking or replacing defective products.
Common cosmetic inspection standards for plastics include:
- ISO 14289-1:2018: Guidelines for the cosmetic inspection of injection-molded plastic parts, including the visual evaluation of surface appearance, surface defects, and the assessment conditions such as lighting and viewing distance.
- ASTM D3359-18: Offers guidelines for measuring the adhesion of coatings to plastic substrates through tape tests.
- JIS B 0202-1:2018: Specifies the visual evaluation of appearance and the testing of surface quality.
When performing cosmetic inspections for plastic, it is important to follow established inspection methods and use appropriate equipment, such as visual aids, microscopes, and specialized inspection software. The inspector should be trained in the use of the inspection methods and equipment, as well as in the interpretation of the cosmetic inspection standards. The inspection should be performed by a qualified and experienced inspector, who can accurately and consistently evaluate the product's appearance and surface quality.
It is also important to consider the impact of the manufacturing process on the product's cosmetic appearance. For example, the surface quality of the product may be influenced by the molding process, the material properties, and the environmental conditions during manufacturing. By understanding these factors and controlling the manufacturing process, manufacturers and suppliers can reduce the risk of defects and improve the overall cosmetic appearance of their products.
3. UV test standard for plastic
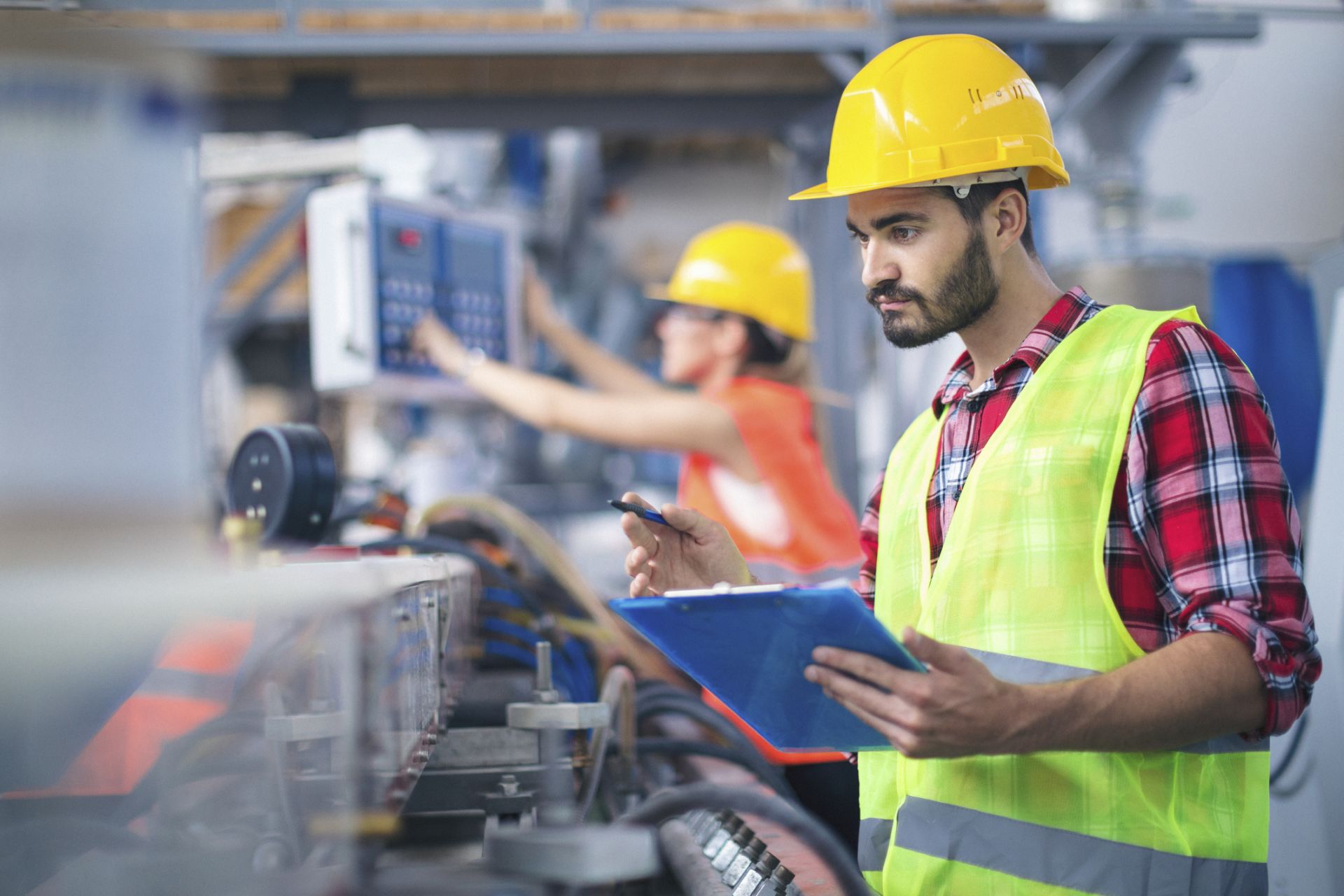
UV exposure can have a significant impact on the performance and durability of plastic products. Over time, UV light can cause degradation of the plastic, leading to changes in its physical and chemical properties, such as discoloration, cracking, and decreased strength. It is important to consider the impact of UV exposure on outdoor products and other UV-exposed applications.
A UV test standard for plastics provides a method for evaluating the impact of UV light on plastic products, allowing manufacturers and suppliers to determine the level of degradation that may occur over time. By following these standards, manufacturers and suppliers can ensure that their products meet the required performance and quality standards.
The most common UV test standards for plastics include ASTM G154, ISO 4892-2, and ISO 11357-3.
- ASTM G154: Specifies the conditions and procedures for exposing plastic materials to UV light, using a standardized light source. The purpose of the test is to determine the effect of UV exposure on the physical and chemical properties of the plastic material.
- ISO 4892-2: Outlines the steps for subjecting plastic materials to UV radiation and artificial weathering, the use of a defined light source, temperature, and humidity levels. It also evaluates the physical and chemical changes of plastics that follow from the exposure.
- ISO 11357-3: Provides guidelines for the determination of the resistance of plastics to UV light and weathering, including the use of a standardized light source and exposure conditions, the assessment of changes in the material's physical and chemical properties.
In addition to UV testing, plastic manufacturers can also take steps to protect their products from UV exposure, such as incorporating UV stabilizers or UV-resistant pigments into the material, and selecting materials with improved resistance to UV degradation. These measures can help to extend the life of the plastic product and maintain its desired properties over time.
4. Visual inspection standard for plastic parts
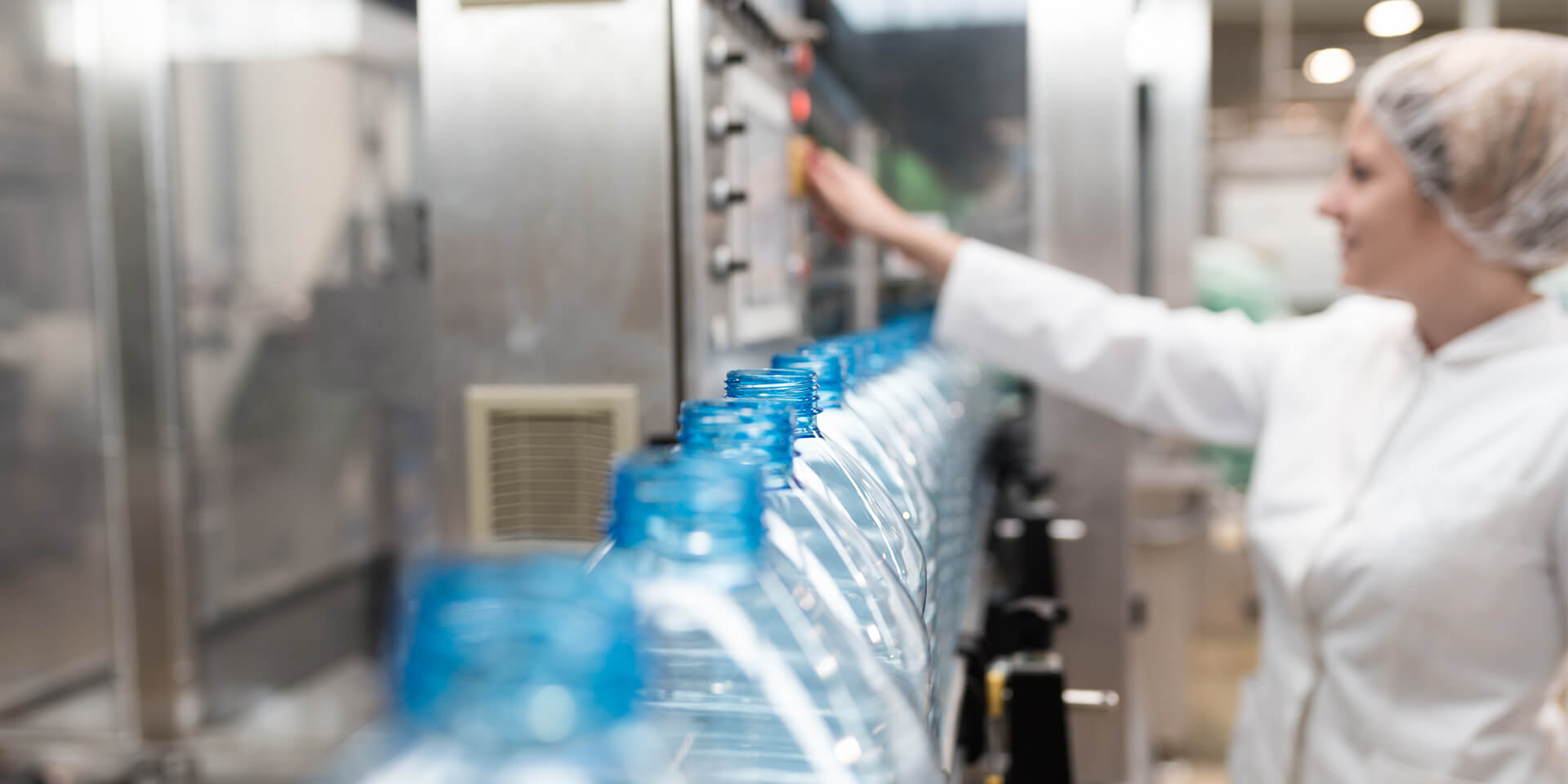
To guarantee the aesthetic and visual quality criteria of plastic products, visual inspection of plastic parts is a crucial part of the quality control process. A well-completed visual inspection assist to improve the manufacturer's or supplier's reputation and brand image, andboost client satisfaction. Additionally, it can lessen the likelihood of product returns and warranty claims, and the expense and time involved in repairing or replacing defective goods.
Common visual inspection standards for plastic parts include:
- ISO 20471: Provides guidelines for the visual evaluation of surface quality, color uniformity, and freedom from defects in plastic products.
- ASTM D3359: Specifies the procedures for performing a cross-cut test to evaluate the adhesion of coatings to plastic substrates. - ASTM D4138: Offers instructions for visually assessing the surface quality, color consistency, and defect-free status of plastic items.
Following established procedures is crucial while doing the visual inspection. The inspector should be trained onutilizing the inspection tools and procedures and interpreting the criteria for visual inspection. A trained and experienced inspector who can properly and consistently do the task should conduct the inspection.
The effect of the production process on the product's aesthetic appeal must also be taken into account. For instance, the molding procedure, the characteristics of the material, and the production environment may have an impact on the product's surface quality. Manufacturers may lower the likelihood of flaws and enhance the overall aesthetic appeal of their products by comprehending these aspects and managing the manufacturing process.
A visual inspection standard for plastic parts may also be used to find problems with manufacturing process uniformity, such as differences in color, gloss, and general look. Early detection of these problems allows producers to take remedial action and increase product uniformity, which increases customer satisfaction and lowers costs.
5. Standards for electroplated plastic
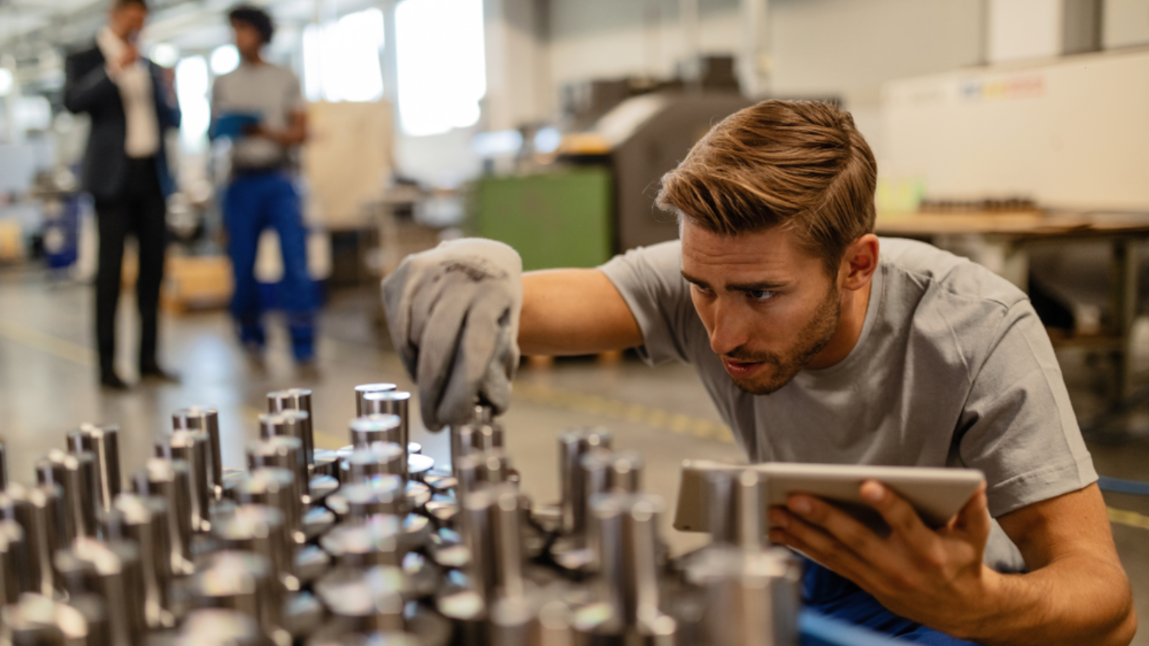
Electroplating of plastic is a process that involves the application of a thin layer of metal onto a plastic surface. The electroplated layer can provide various benefits, such as improved wear resistance, corrosion protection, and aesthetic enhancement. For example, electroplating can be used to give plastic parts a metallic appearance, which is often desired for jewelry or automotive components. The electroplated layer can also improve the electrical conductivity of the plastic, which can be important for electronic components.
The electroplating process involves the use of an electrolyte solution, an electrical current, and a metal salt to deposit the metal onto the plastic surface. The quality of the electroplated layer is influenced by many factors, including the selection of the metal, the composition of the electrolyte solution, the process parameters, and the surface preparation of the plastic. To ensure consistent and high-quality electroplating, it is important to follow established standards and guidelines.
Common standards for electroplated plastic include:
- ISO 4527: Provides guidelines for the electroplating of plastic materials, including the selection of plating solutions, the deposition process, and the evaluation of the metal coating.
- ASTM B456: Specifies the requirements for electrodeposited coatings of nickel, cobalt, and tin on plastic and other non-conductive substrates.
- SAE J2406: Contains instructions for electroplating automobile parts, including guidance on plating solution selection, metal coating deposition techniques, and metal coating assessment.
By following the established standards and guidelines for electroplating, manufacturers of plastic products can ensure that their products will meet the desired quality requirements and provide benefits over time. These standards also help to compare the quality of different electroplating processes to assess the suitability for different applications. In addition, following the standards helps to ensure that the electroplated plastic products are safe and environmentally friendly, and that they will meet the regulatory requirements for different applications.