Filler masterbatch is the main product of EuP. Filler masterbatch is also a vital component in various industries requiring the association of plastic. Plastic, ever since its invention, has become a vital material in the economic and societal development of almost every country in various regions worldwide. Nowadays, myriad of features in daily life of humans are made of plastic. Although it is extremely common in daily life, have you ever be curious on what was plastic and calcium carbonate masterbatch made from? Let’s take a deep look into this advanced material.
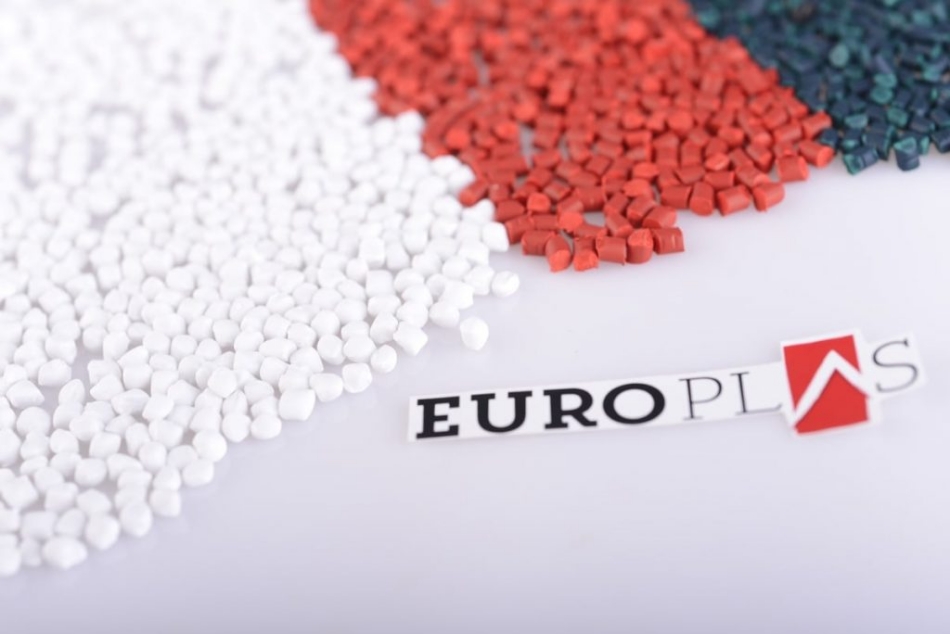
1. The nature of plastic built up filler masterbatch’s properties
The variety of filler masterbatch is countless. Each type of it has distinct features, functions and characteristics. This difference largely comes from the properties of the base resins that compose them. Plastic is synthesized material derived from organic components coal, natural gas, salt, cellulose and especially crude oil. Basics of plastic is polymer chains, which are usually used to name the plastic itself, with its building blocks (monomers) are similar molecules made of hydrogen and carbon atoms, sometimes with the presence of other elements such as oxygen, nitrogen, chlorine, silicon, fluoride, sulfur, phosphorous, etc.
2. How was plastic and filler masterbatch classified?
The nature of the building block determines the chemical properties of plastic and consequently the filler masterbatch. Based on this aspect, plastics are categorized into different types and groups. The categorization of plastics is various. Depending on the properties, functions or constituents, plastic will be classified in several ways. One of the most common ways to divide plastic into groups properly based on its thermal aspect. As following this feature, there are 2 types of plastic: thermosets (assemblage of the constantly hard and rigid plastic despite of the heat) and thermoplastics (which are meltable plastic under heat and will be set back to the rigid form when cooling down).
Besides the thermal aspect, the molecular structure and the constituents in its compositions (How many types of monomers does it include?) are also other fundamentals used to set up the plastic classification.
3. The history from plastic to filler masterbatch – a great invention for human development
Despite of being considered as an artificial material, plastic’s components actually came from nature. The first-ever-found plastic is rubber, which is mainly harvested from latex of the rubber tree. However, these natural materials do not meet the increasing needs of human as the world keeps developing throughout the years. The history of synthetic plastics properly started over 150 years ago. Polyvinyl chloride (PVC) was nearly the earliest synthetic plastic as it was well researched and polymerized in 1838. Following PVC, polystyrene, polyacrylic and polyester was synthesized in 1839, 1843 and 1847, respectively. Celluloid, also called nitrocellulose, a transparent flammable plastic widely used in cinematographic film, was one of the firstly created plastic-product which was invented by Alexander Parkes in 1855 under the name Parkesine. The production of synthetic plastic was massively elevated in another level in 1907 when a Belgian-American chemist named Leo Baekeland created Bakelite. The appearance of bakelite created a revolution in applying plastic into electrical, radio and telephone products.
4. Filler masterbatch – the significant improvement for the plastic industry
Despite of various potentials in prevailing over other traditional materials, the development of plastic was delayed in the early decades of the 20th century due to the world wars and numerous social instabilities which had occurred throughout the world. It was not until the 1950s when the wars, harshness and deprivation were over, that the world's inhabitants entered a more stable period, the superiority of plastic was received its desirable attentions. Ever since, human have focused on researching and inventing more advanced plastics to apply to many other industries and productions. Also in this time, filler masterbatch was upgraded and widely used as an effective tool hugely supporting for the plastic processing and mass production.
5. How does filler masterbatch differ from the plastics?
As mentioned above, plastics are purely polymer chains without any other components. Filler masterbatch, on the other hand, is a mixture consists of multiple ingredients. The plastic is one in the most important components of calcium carbonate masterbatch that serves as the carrier. Other vital element, accounted for the vast majority of plastic filler, approximately 70-80% of the mixture, is calcium carbonate powder. Besides base plastic and CaCO3 powder, filler masterbatch also consist of pigments powder and several additives depending on the customer’s requirements.
6. The production process of plastic – the input material for filler masterbatch
During the procedure of producing the base plastic for filler masterbatch manufacturing, polymerization plays as the key mechanism. In the polymerization process, monomers, which were originally constructed by raw materials, are conjugated together by chemical reactions in the way of forming long polymer chains. Raw materials that were used to generate the plastics’ building blocks can either come from the natural or renewable resources.
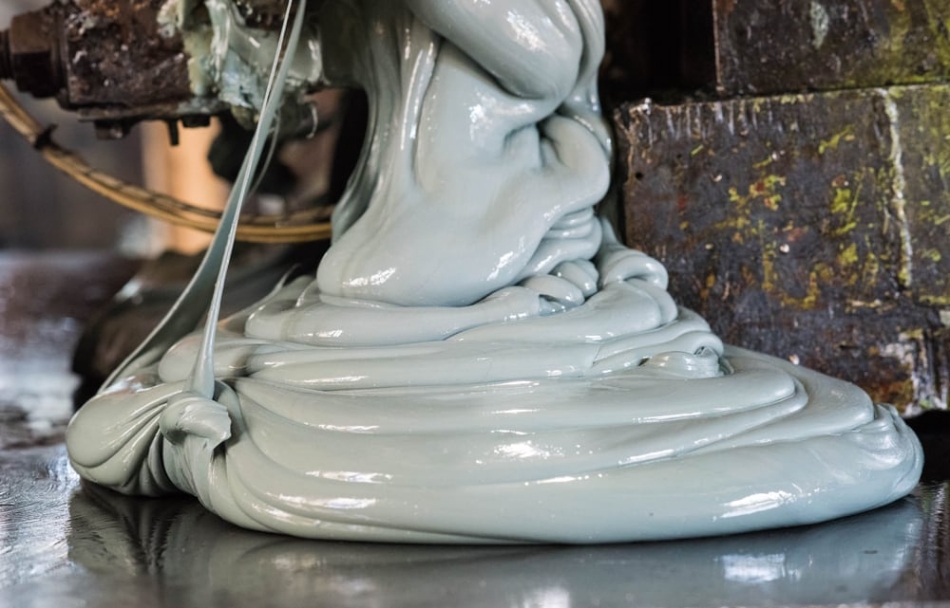
7. 2 ways of producing base plastic:
In plastic calcium carbonate masterbatch manufacturing, there are 2 types of polymerization: the addition polymerization (the chain-reaction) and the poly-condensation (the step-reaction). These 2 types of polymerization differ from each other in the way monomers are linked together. The basis of calcium carbonate masterbatch chain-reaction polymerization is one monomer will link to the monomer next to it thanks to the free radical binding to the initial monomer. This process will continue until another free radical sticks to the final monomer and terminates the polymer chain.
The 2nd method in producing base resin for filler masterbatch, the step-reaction polymerization is commonly used to manufacture plastics with two distinct types of monomer. This process is more complicate than the addition polymerization as it requires higher temperature. As consequent, its products include main product (the polymer) accounted for lower molecular weights and by-products (which is usually small molecule such as water, HCl, etc.).
8. Masterbatch manufacturing process
The production process of calcium carbonate masterbatch takes place according to the following 4 basic stages:
- CaCO3 powder, base resin and additives are mixed by machine at high speed mode
- The mixture is melted into liquid at high temperature
- The liquid is cooled and screwed in a twin screw extruder pushed forward and pressed into the mold
Plastic is inserted into the cutting machine to cut into particles. These particles will be padded into plastic beads to bring new features to the raw plastic.