High density polyethylene is a popular thermoplastic used in various applications, including food containers, milk bottles, shampoo and detergent jugs, etc. HDPE plastic recycling plays an important role in protecting our planet and saving your business money on plastic disposal. Let's delve into the details to see why and how we should recycle it!
1. What Is HDPE?
HDPE, short for High density polyethylene, belongs to the polyethylene family. The plastic is light, tough, and hard-wearing with high tensile strength. It can be translucent or opaque. The material does not absorb liquid readily and is resistant to many chemicals, alcohol and acids, making it suitable for different types of containers, including bottles and containers used for food, healthcare facilities and laboratories.
Read more: HDPE (High density polyethylene) - What is it? Properties & common uses
2. Can HDPE Plastic be Recycled?
Since the material is widely used, the question of recycling starts to come up. So, is HDPE recyclable?
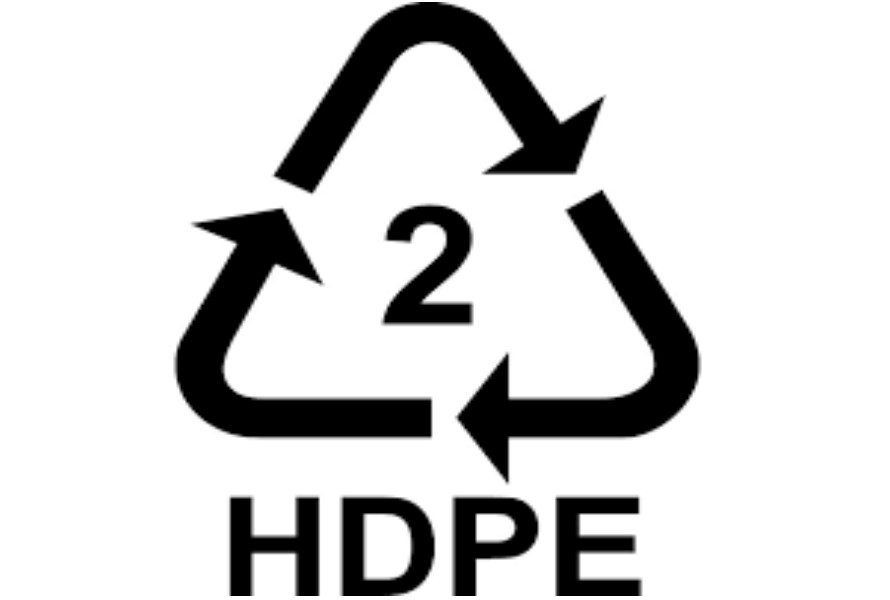
Yes, this plastic is recyclable. It's marked as recycling code 2 and you can recycle it in all forms, including bottles, bags, film, sheets, tanks, and offcuts. It's also known as one of the easiest plastic polymers to recycle.
The material can easily be melted at an industrial scale, but you can also do it at home. Therefore, HDPE can be used several times. It is also easy to work with and can be molded in almost any shape.
HDPE has strong internal structure; thus, after the recycling process, the material can be used in various applications, such as Recycling bins, Plastic lumber, Utility Pipes, Crates, Non-food bottles, Floor tiles, Garden furniture and flower pots, Sheeting and film plastic.
3. What Are The Benefits of Recycled HDPE Plastic?
The plastic is non-biodegradable, meaning it will take hundreds years to decompose. It will be a waste if you just simply discard it after single use. Thus, HDPE plastic recycling brings lots of benefits to businesses and the environment.
Manufacturing a product from recycled HDPE plastic is less expensive than working with virgin plastic. Plus, the process is energy efficient, saving a significant amount of fossil fuels and energy. After recycling, the material is still very durable, so companies can lower the production cost and maintain the same good quality of products.
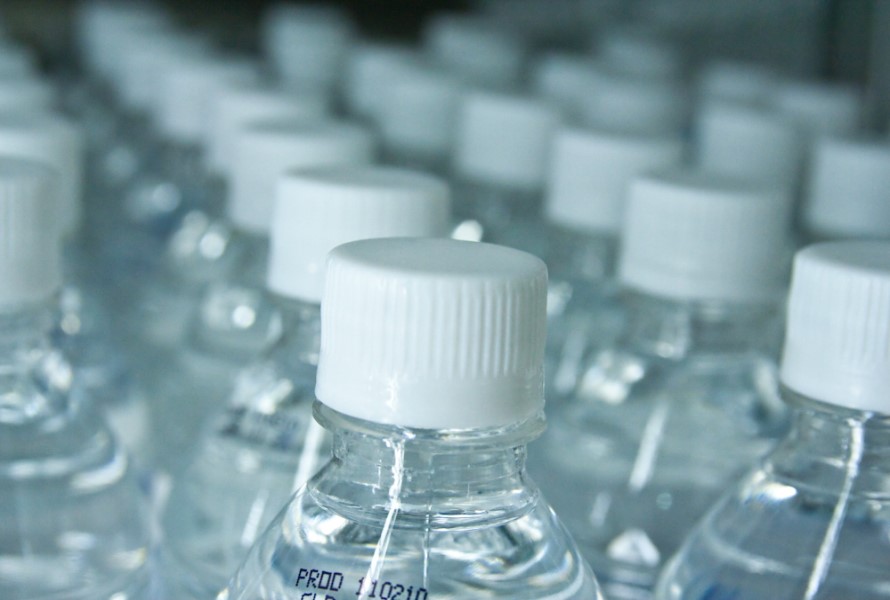
Once you conduct the HDPE plastic recycling process, it also means you send less waste to the landfills, thus having a positive impact on the environment. As for your business, you also can save lots of landfill tax by doing so.
How many times can you recycle HDPE? The great thing about this plastic is that it can be recycled around 10 times. Only after 10 times of shredding, melting and molding does the quality of HDPE begin to compromise, making it a super eco-friendly material. Besides, the process also reduces emissions and helps save our planet. With recycling HDPE, you can protect our environment and run a sustainable business.
4. What Are The Recycling Process?
The source of recycle HDPE include:
- Retailers – plastic carrier bags, containers, and some plastic bottles
- Takeaways – used plastic food containers, bottles, and bags
- Offices – empty plastic milk bottles from the kitchen
- Construction – pipes, pallets, containers, and drums
After collecting the HDPE products from the above sources, the process of HDPE plastic recycling will start with sorting and cleaning. The plastic will be cleaned from unwanted debris and homogenized to ensure only HDPE is selected for the process. If other plastics also present, it may affect the quality of the final products.
Then, Near-Infrared Radiation (NIR) techniques can be used if the plastic is not too dark and does not absorb the infrared waves. Next, it's the shredding and melting process to further refine the polymer. After that, the material is cooled in pallets and ready for manufacturing.
5. EuroPlas - A Reliable Partner For Your Sustainable Business
EuroPlas is the world's No. 1 filler masterbatch manufacturer, providing customers with unique plastic raw material solutions to help their factories optimize production costs and improve their competitiveness in the market. Moreover, we understand the importance of eco-friendly materials to contribute to the green world and encourage sustainable lifestyles. Therefore, we've created a series of biodegradable products used in different industries to help reduce the bad effects of plastics on the environment.
5.1. Bio filler
EuroPlas has more than 16 years of experience in providing sustainable solutions for the plastic industry. Bio filler (including BioMates 01, BioMates 02, and BioMates 03) is another cost-effective material solution for bioplastic end-products. It's a popular choice in the international market, including Europe and the USA. Our biodegradable materials not only save your production cost for bioplastic end-products but also improve their properties such as gloss, stiffness, etc. They can also act as anti-block and slipping agents in blown film, making them ideal for different applications.
- BiOMates 01: It's a mixture of bio-resin, modified CaCO3, and dispersion additives. This biodegradable product can optimize cost for bioplastic end-product processing and play as an anti-blocking and slipping agent for PBAT films.
- BiOMates 02: It's a blend of bio-resin, modified BaSO4, and dispersion additives, helping optimize cost when mixing with several types of bio resins, such as PBAT, PBAT compound, PBAT & PLA blend. It also can increase the film's glossiness.
- BiOMates 03: It combines bio-resin, modified talc, and dispersion additives. It can increase the film glossiness and optimize the cost of bioplastic end-product processing. The product helps produce more transparent film than when using CaCO3. BiOMates 03 also acts as anti-blocking and slipping agents for PBAT films.
5.2. Bioplastic compound
Bioplastic compounds have many advantages. Unlike conventional petrochemical-based plastics, which are made from costly petroleum or natural gas, bioplastic compound is produced from renewable biomass sources, including polylactic acid (PLA) and Polyhydroxyalkanoate (PHA), plants and vegetables (corn, palm oil, potatoes), or fossil fuels like aliphatic-aromatic co-polyester (PBAT).
Using biodegradable and compostable compounds means you'll be less dependent on fossil fuels. Its life cycle assessment shows that it can decrease the carbon footprint in the manufacturing process. Furthermore, the bioplastic compound has better mechanical properties than unprocessed plastics, fewer toxins, and decomposes faster.
The material is widely used in different industrial sectors such as electronics, automotive & transport, household appliances, construction, fibers, and especially food packaging.
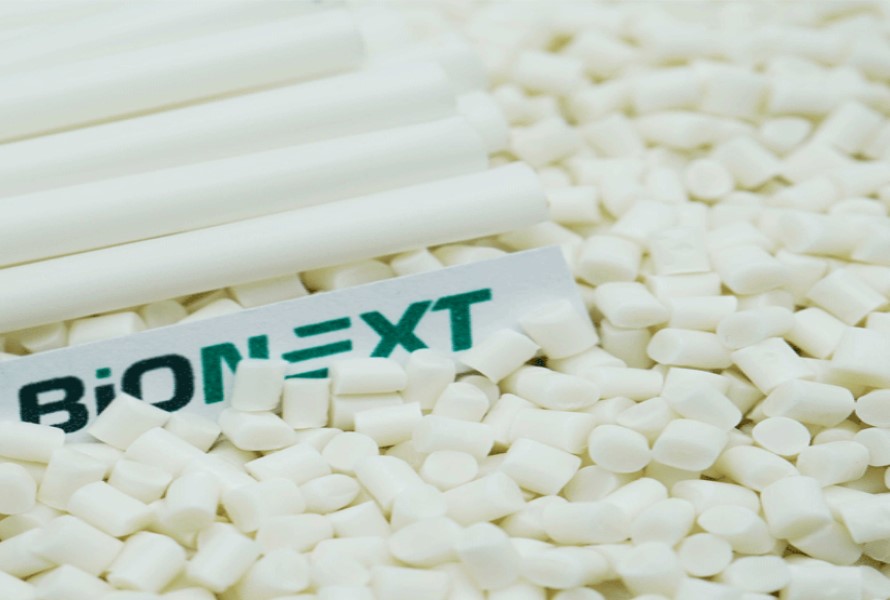
Acknowledging this fact, EuroPlas has introduced the Bioplastic compound, a green material solution with outstanding mechanical properties that enables end-products to be biodegradable within 12 months. We ensure your final products will meet all strict quality control criteria. With our bioplastic compound, you can have a full function in one material, which can be tailor-made based on your end-product requirements.
- BiONext 102 and BiONext 152 - the two bio-compounds made of bioplastic and CaCO3. They have high stiffness, high impact strength, and low melt flow index, making them easy to process.
- BiONext 400 - a bio-compound produced based on bioplastic and modified starch powder. It can keep moisture on the surface, resulting in longer food preservation.
- BiONext 500 - a bio-compound based on bioplastic and reinforced CaCO3 powder. It has high stiffness, good elongation, great dispersion, and is easy to process.
- BiONext 600 - a bio-compound based on bioplastic, talc, and other specific additives. It's anti-UV, oxidation, and moisture.
- BiONext 700 - a bio-compound based on bioplastic and specific plasticizers. It can prevent oxidation, thus resulting in longer food preservation.