HDPE vs. PVC: Which One Should You Choose?
When it comes to choosing plastic materials for various applications, two common options that often come up are HDPE (High-Density Polyethylene) and PVC (Polyvinyl Chloride). Both have their unique properties, advantages, and specific uses, making them suitable for different needs. This article aims to provide a detailed comparison between HDPE vs PVC, covering their characteristics, pros and cons, applications, and guidance on which material might be the best fit for your project.
1. Overview of HDPE and PVC Plastic
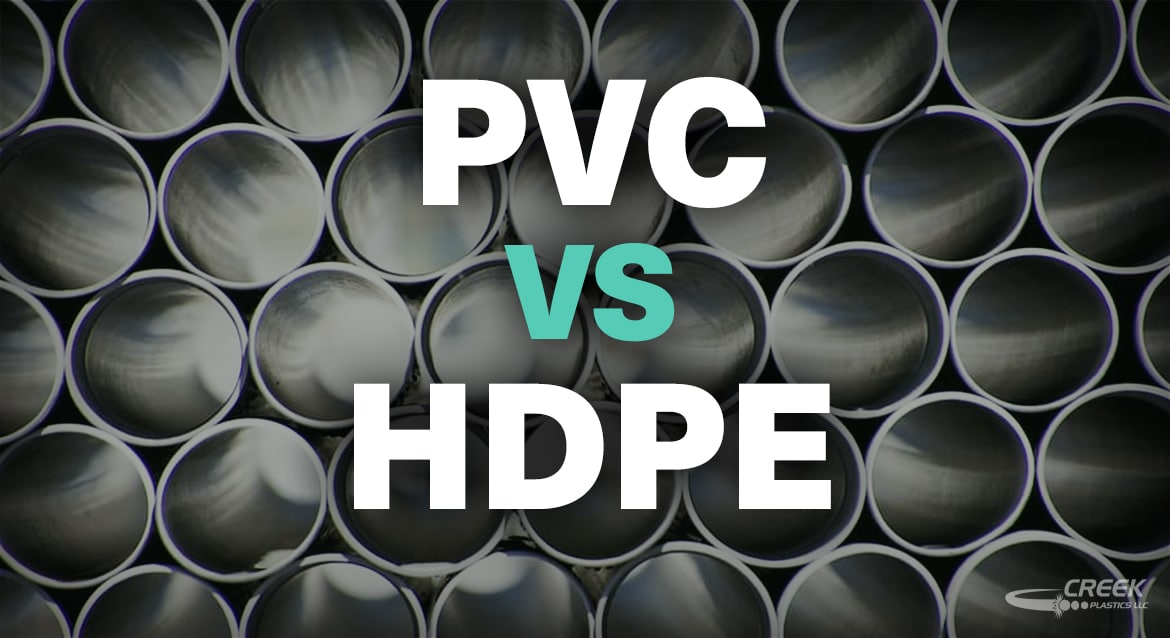
HDPE vs PVC
HDPE and PVC are popular thermoplastic materials known for their durability and versatility. HDPE is a type of polyethylene that is characterized by its high strength-to-density ratio, making it a preferred choice for applications where durability and impact resistance are essential. It is often used in products like pipes, bottles, and containers.
PVC, on the other hand, is a versatile plastic known for its rigidity and chemical resistance. It is widely used in construction materials, pipes, window frames, and insulation. PVC’s composition can be adjusted to make it either rigid or flexible, allowing for a broad range of uses. Understanding the core differences between HDPE and PVC can help in determining which material suits specific needs.
2. HDPE vs. PVC: Comparing Properties
The properties of HDPE vs PVC play a significant role in their suitability for various applications:
- Density and Strength: HDPE is known for its lower density yet high strength, making it lighter while maintaining structural integrity. This property makes it ideal for piping systems and containers. PVC, with its higher density, offers greater rigidity, which is beneficial in applications where a stiffer material is required.
- Flexibility: HDPE is more flexible compared to PVC, which means it can handle bending and pressure changes more effectively, especially in piping applications. PVC's rigidity can be advantageous in situations where the shape of the material needs to remain constant.
- Thermal Resistance: HDPE generally offers better resistance to low temperatures, maintaining its integrity in colder environments. PVC tends to become brittle in extremely cold conditions, which could limit its applications in colder climates.
- Chemical Resistance: Both HDPE and PVC are resistant to various chemicals, but HDPE stands out for its superior resistance to acids and bases, making it ideal for certain industrial applications. PVC’s chemical resistance makes it suitable for plumbing, but it is more prone to degradation under sunlight if not treated.
3. HDPE vs. PVC: Comparing Advantages & Disadvantages
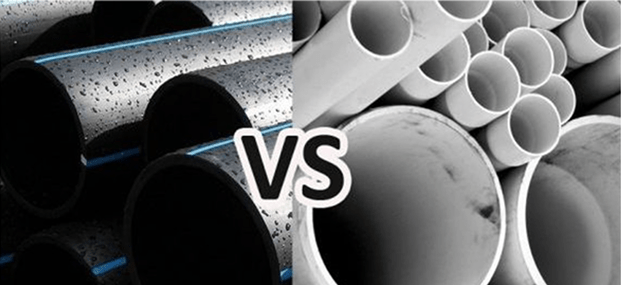
Comparing HDPE vs PVC properties
HDPE vs PVC each have their strengths and limitations, which can significantly influence their suitability for different applications. Here’s a detailed look at the advantages and disadvantages of both materials:
HDPE (High-Density Polyethylene):
Advantages |
Disadvantages |
High Impact Resistance: HDPE is known for its remarkable impact resistance, which means it can withstand heavy loads, drops, and external shocks without cracking or breaking. This makes it ideal for environments where materials may be exposed to rough handling or mechanical stress, such as underground piping. |
Higher Cost: One of the primary drawbacks of HDPE is its higher cost compared to PVC. While it offers better performance in certain conditions, the increased initial investment can be a consideration for budget-conscious projects.
|
Lightweight and Flexible: Despite its strength, HDPE is lightweight, which can significantly reduce transportation and installation costs. Its flexibility is another key advantage, allowing it to be used in applications that require bending or adjusting to shifting ground conditions, such as trenchless piping systems. |
UV Sensitivity: HDPE is susceptible to degradation when exposed to direct sunlight over long periods. Without proper UV stabilizers or protective coatings, HDPE materials can become brittle and lose their structural integrity when used outdoors. |
Moisture and Chemical Resistance: HDPE offers excellent resistance to water and a wide range of chemicals, including acids, bases, and other corrosive substances. This property makes it suitable for containers and piping systems in industrial environments where exposure to chemicals is common.
|
Specialized Installation Requirements: Unlike PVC, which can be joined using simple adhesive techniques, HDPE often requires specialized welding equipment for seamless installation. This can make the installation process more complex and costly, especially in large-scale piping projects. |
Temperature Tolerance: HDPE retains its strength at lower temperatures, maintaining durability in colder environments. This characteristic makes it a better choice for applications in regions that experience harsh winters or fluctuating temperatures. |
|
PVC (Polyvinyl Chloride):
Advantages |
Disadvantages |
Cost-Effective: One of the most appealing aspects of PVC is its affordability. It is generally less expensive than HDPE, making it a preferred choice for projects where cost is a primary consideration without compromising too much on performance. |
Brittleness in Cold Temperatures: While PVC performs well in a wide range of environments, it can become brittle and crack when exposed to extremely cold temperatures. This limits its use in outdoor applications in regions with severe winters. |
Ease of Installation: PVC is known for its easy installation process. It can be connected using solvent cement, which creates a strong bond without requiring specialized equipment. This ease of installation can result in lower labor costs and faster project completion. |
Lower Impact Resistance: Compared to HDPE, PVC is more susceptible to damage from physical impacts. Heavy loads or sudden pressure changes can cause PVC to crack or break, making it less suitable for applications involving dynamic stress. |
Rigidity and Strength: PVC’s high rigidity makes it ideal for applications where maintaining a fixed shape is critical, such as in structural components like window frames and construction pipes. Its rigidity also ensures that PVC pipes can resist external pressures without significant deformation. |
Potential for Chemical Leaching: Over time, PVC can leach certain chemicals into the environment, which is particularly relevant in applications involving potable water. This aspect has led to concerns about its environmental impact and has encouraged the exploration of alternatives for sensitive applications. |
Fire Retardant Properties: Due to the presence of chlorine in its chemical structure, PVC exhibits good fire-resistant properties, making it suitable for use in electrical insulation and building materials where fire safety is a concern. |
Environmental Concerns: PVC is derived from fossil fuels and contains chlorine, which can release harmful substances during production or when improperly disposed of through incineration. This has made it a focus of environmental scrutiny, especially in applications where sustainability is a priority. |
4. Which Plastic Should You Choose?
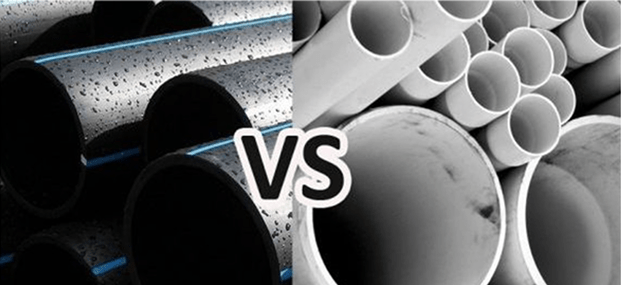
HDPE vs PVC comparison
Choosing between HDPE and PVC largely depends on the specific needs of the project:
- For Durability and Flexibility: If the application requires a material that can endure high impact and varying pressure, HDPE is the better choice. It is suitable for applications such as underground pipes or containers that may experience temperature changes.
- For Structural Rigidity: PVC might be the preferred option when rigidity and dimensional stability are crucial. It is commonly used in construction projects, such as piping in buildings and window frames, where strength and a consistent shape are necessary.
- Budget Considerations: For those with tighter budgets, PVC offers a more affordable option without significantly sacrificing performance in many use cases. HDPE, while slightly more costly, could be justified for its durability and performance in challenging environments.
5. Applications of HDPE and PVC Plastic
The versatility of HDPE and PVC has led to their widespread use across numerous industries, each suited to specific applications based on their unique properties:
HDPE Applications:
- Water and Gas Distribution Piping: HDPE is extensively used in piping systems for water and gas distribution due to its flexibility, durability, and resistance to corrosion. Its ability to withstand pressure changes and shifting soil conditions makes it a preferred choice for underground piping installations. Additionally, HDPE’s resistance to scaling and chemical deposits ensures a long service life in water and gas pipelines.
- Industrial Containers and Tanks: HDPE’s chemical resistance makes it ideal for storing and transporting chemicals, acids, and hazardous liquids. It is used to manufacture industrial containers, tanks, and drums that are resistant to corrosion and impact, ensuring the safe storage of materials over time.
- Geomembranes for Landfills: HDPE is commonly used as a geomembrane lining material in landfills and environmental protection projects. Its impermeability and resistance to chemical degradation prevent the leaching of contaminants into the soil and groundwater, ensuring a safe and environmentally friendly waste management solution.
- Agricultural Uses: In agriculture, HDPE is used for irrigation systems, including pipes and tubing that deliver water efficiently to crops. Its lightweight nature and resistance to chemicals make it suitable for use in harsh outdoor conditions, where exposure to fertilizers and varying weather conditions is common.
PVC Applications:
- Construction and Building Materials: PVC is a staple in the construction industry, used in pipes, window frames, siding, and roofing materials. Its rigidity and weather resistance make it a durable option for building components exposed to the elements. PVC pipes, in particular, are widely used in plumbing systems, delivering water and removing waste in residential and commercial buildings.
- Electrical Cable Insulation: The fire-resistant properties of PVC make it an excellent choice for insulating electrical cables. It is used to cover wires and cables in a variety of electronic and electrical applications, providing both safety and durability in residential, commercial, and industrial settings.
- Medical Applications: Flexible PVC is commonly used in the medical field for products such as tubing, blood bags, and other medical devices. Its flexibility and ability to be sterilized make it a practical choice in applications where hygiene and durability are paramount.
- Signage and Advertising Materials: PVC sheets and foams are used in the creation of signs, banners, and display boards due to their smooth surface and ability to be easily printed on. The lightweight nature of PVC foam boards makes them ideal for both indoor and outdoor advertising, providing a durable and weather-resistant solution.
These varied applications of HDPE and PVC demonstrate how each material brings unique value to different industries. Whether it’s the flexibility and chemical resistance of HDPE or the rigidity and affordability of PVC, understanding their strengths and weaknesses can help in making the right choice for specific needs.
6. Conclusion
HDPE and PVC are two of the most versatile plastics, each with properties that make them suitable for different applications. While HDPE is known for its flexibility and impact resistance, PVC offers rigidity and cost-effectiveness. Understanding their differences and assessing the specific requirements of your project can help you make an informed decision. Whether you need a durable material for industrial use or a cost-effective option for construction, both HDPE and PVC offer valuable solutions tailored to various needs.
7. About EuroPlas
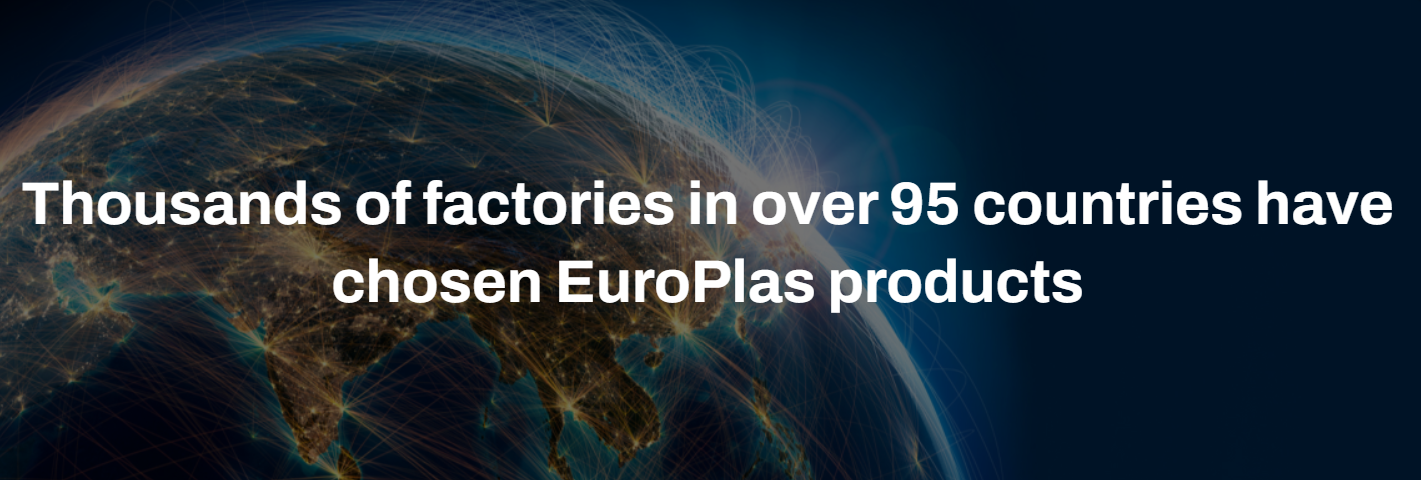
EuroPlas - No. 1 filler masterbatch manufacturer
As the world’s No. 1 filler masterbatch manufacturer, EuroPlas offers tailor-made plastic material solutions that enhance the competitiveness of plastic enterprises. With a global mindset and dedication to innovation, EuP provides materials that meet high-quality standards while ensuring sustainable development practices. EuP operates seven state-of-the-art factories, equipped with advanced technology to produce up to 0.8 million tons annually, serving industries in over 95 countries worldwide. EuP’s commitment to customer satisfaction and optimal material solutions makes it a trusted partner for companies working with plastic materials.
Looking for advanced plastic material solutions? Visit our Contact Us page to learn how EuroPlas can help your business thrive.